A compression set measures a material’s ability to recover to its original shape and dimensions. The advantages (and disadvantages) of higher or lower compression sets are highly application specific. One advantage of a high compression set is a material’s formability into fine and precise detail, for example, in coining and cold forging. Compressible and non-recovering materials as spacers create precise closures/fits that are retained at disassembly. The disadvantage of a high compression set is that materials distort under compressive and impact forces and are then no longer fit for purpose. On the other hand, the advantages of a low compression set are its formability into constrained recesses and conformance to surfaces while retaining high forces on the recess. They can also recover from force and impact, such as buffers and vibration dampers. This article will further expand on the advantages and disadvantages of high and low compression sets.
What Is a Compression Set?
The compression set is the measure of the ability of a material sample to recover its original shape and dimensions after being compressed. There are two methods of measuring the compression set. The first of these is used to measure deflection and usually involves displacing a sample by 25% of its thickness for a specified length of time. The partial or complete recovery within a specified time limit is then observed.
The other method is more commonly used, and it involves standardized compression and recovery. It is this method on which we will concentrate in this article. This type of compression set is defined as the percentage of the original thickness or volume that is not recovered after the material is subjected to a specific amount of compression for a given time and then allowed to recover for a certain time. The time-related component is critical, as many materials show some degree of viscoelastic behavior with long time constants, making net recovery a slower process than the initial compression. The compression set is the measure of the permanent deformation that remains in a material after it has been subjected to a compressive force and then released. It is typically (and somewhat loosely) expressed as a percentage of the original thickness or volume of the material.
Why Is Compression Set Important in Material Design?
Compression set is an important property in component design because it indicates how well a material can maintain its shape and properties under compressive loads over time. A material with a high compression set will not be able to recover its original shape and dimensions after being subjected to a compressive load, while a material with a low compression set will be able to recover its original shape and dimensions more effectively, albeit potentially slowly.
This behavior is especially important in applications for which maintaining pressure on a compressive element is critical, such as in seals, gaskets, and O-rings. This enables the material to maintain a seal against liquids or gases. High compression set materials will not maintain this condition. Compression set is also an important consideration in the design of products that must maintain their shape and properties over time, such as the socket component of a hip prosthesis. Materials with a low compression set are necessary for these applications to ensure long-term performance and reliability.
How Is Compression Set Determined?
The compression set is determined by applying a specific compressive load to a specified sample section and thickness for a predetermined period. The percentage of the material's original thickness (or volume in the case of a more compressible material) that is not recovered after the load is removed is then measured.
Test methods used to determine this value vary significantly depending on the type of material being tested and the application for which it is intended. A steel sample requires much higher loads and more sensitive measurements than a rubber, for example. A generic test procedure is listed below:
- The sample is cut or molded into a specific shape and size as per a standardized test protocol. Tests are performed under preset environmental conditions, to ensure consistency.
- The sample is compressed to a specified load (or deformation distance) for a predetermined time. This will usually be performed using a compression testing machine, but valid results can be achieved with more ad-hoc equipment if measurements of applied load and sample compression are appropriately precise.
- After the specified compression period, the load is removed and the sample is allowed to recover its shape and dimensions (to whatever degree it can) for a set period.
- The sample's thickness or volume is then measured, and the unrecovered percentage of the original thickness or volume is calculated, giving the compression set for THAT sample, under THOSE test conditions.
How Does Compression Set Affect the Durability of Materials?
The compression set can affect the durability of materials in that it helps a part recover to its original shape and dimension after a compressive load is applied to it. Material with a high compression set will not be able to recover while a material with a low compression set can.
What Are the Advantages of Using a High Compression Set?
The advantages of using a high compression set are listed below:
- In permanent electrical connections, the high compression set of copper wires crimped between brass couplings leads to a larger contact area. This results in reduced contact resistance and risk of arcing.
- In automotive (lead acid) battery connections, a lead contact post has a lead plate or cap applied to it. The parts are advantageously able to distort and conform to one another to make a lower resistance coupling.
- In pipe seals on copper pipe, it is common to use brass compression set washers (called olives) to compress and distort to make a permanent metal-to-metal pressure seal. Olive systems are also used in stainless steel pipework, in which temperatures are too high for elastomeric seals to be considered reliable in the long term.
What Are the Disadvantages of Using a High Compression Set?
High compression set materials are generally considered disadvantageous as they suggest materials that will relatively easily permanently deform when force is applied to them. Most mechanical systems rely on precision and the fixed nature of the parts that make them, so a high compression set disturbs this.
What Are the Factors That Contribute to High Compression Set?
Some factors that contribute to the high compression set are listed below:
- Certain chemical compositions are more prone to compression, due to their inherent properties. For example, metals with a low glass transition temperature will constantly recrystallize and distort rather than spring.
- Temperature can also influence this property. Many materials experience significantly increased compression set at higher temperatures, often as the glass transition temperature is approached and exceeded. This is particularly true with polymers.
- Many materials will reach a yield behavior when loaded, contributing to the compression set.
- The amount of time that the material is subjected to compression can also contribute to the compression set. Longer periods of compression can lead to increased deformation and a higher compression set due to creep or internal structural relaxation.
- Aging and exposure to environmental factors such as UV light and moisture can lead to compression.
For more information, see our guide on What is Compressive Stress?
Is High Compression Set Better?
It depends. High compression set materials are highly desirable in a limited range of circumstances, where this property is successfully exploited. In general, high compression set materials are rejected for engineering applications, consumer products, and medical devices, other than as failure “fuses” and as gaskets for some applications.
What Properties of Materials Result in Low Compression Set?
Compression set is a direct result of material properties. Some material properties that result in low compression sets are listed below:
- Materials that are strong, with a high yield point (or elastic limit) which prevents them from easy, compression-related distortion.
- Materials that possess highly crystalline structures, in which loads are applied to strong atomic bonds result in higher elasticity.
- Materials that have high levels of cross-linking or pseudo crystalline properties, in the case of low compression set polymers.
- Materials with high yield strengths are more likely to be elastic and therefore have low compression set properties.
What Are Some Real-World Applications of Materials With Lower Compression Sets?
Some real-world applications of materials with lower compression sets are listed below:
- Main linkages in an aircraft landing gear must transmit forces from the hub to the stanchion without undergoing compression set at bearing mounts.
- Vibration dampers in a bridge or building foundation are designed to allow movement in a damped fashion while remaining elastic under heavy, steady loads.
- Train buffers are precise systems that are intended to reduce the impulse in low-speed impacts, to reduce the potential for damage. This is achieved using a stiff oil damper (shock absorber) between the train chassis and the buffer pad.
- Car tires are an element of the system that enforces compliance between the vehicle and the variable road surface. Rubber tires are vulcanized, to impose a rigid, cross-linked structure that prevents compression set in short loading periods.
What Are the Advantages of Using Low Compression Set?
The advantages of using a low compression set material are listed below:
- Low compression set materials can maintain their original shape and properties over an extended period and within expected loading limits. This means they can withstand cyclic and heavy compressive forces without permanent deformation.
- Softer, low compression set materials have a better ability to maintain seal pressure over time, preventing leaks, product failure, and hazards. Ideal seal materials are selected to maintain their properties under all expected pressure or temperature conditions.
- Softer, low compression set materials can help absorb and damp out vibrations. This reduces the likelihood of equipment failure or damage in high-speed and potentially overloaded systems.
- Low compression set materials are often used in applications for which comfort and safety are paramount, such as in medical devices or automotive components. These materials can help provide a cushioning effect, reducing the likelihood of injury or discomfort.
- While very low compression set materials are more expensive at the start, long-term durability will result in a lower probability of product failure.
What Are the Disadvantages of Using Low Compression Set?
The disadvantages of using a low compression set are listed below:
- In metals, shock loading of aluminum parts is more likely to result in permanent compression/deflection than for an otherwise identical steel part. The steel part will result in product survivability being generally improved. Like many such material pairings (but by no means all), the low compression set option will likely weigh more, even when optimized in design.
- Low compression set materials cost more.
- Lower compression set materials often require more post-processing to deliver the improved property. For example, a medium carbon steel component will require several further stages after shaping, if it is to be hardened and tempered to further improve its compression set behavior.
- In elastomers, lower compression set materials are generally thermoset types, which benefit from cross-linking to achieve this beneficial property. This results in higher material costs and lower production capacity than the near equivalent thermoplastic part that lacks the compression set resilience.
What Are the Factors That Determine Low Compression Set?
Some of the factors that determine low compression sets are listed below:
- Metals with fine crystalline structures have lower compression set behavior than those with larger matrices.
- Polymers with plentiful cross-linking are more structurally resilient, i.e., have a lower compression set tendency than polymers that rely on the weak atomic forces between polymer chains. This is exemplified by natural rubber, which has a relatively high compression set, albeit a fairly slow process. Once vulcanized, using sulfur to induce aggressive cross-linking in the structure, the compression set behavior improves considerably.
- Polymers that creep have a higher compression set than those which do not. For example, a high-density polyethylene component will slowly distort under load—i.e., it shows a moderately high compression set which is relatively slow to set. Acetal, on the other hand, shows more crystallinity and therefore undergoes much less compression set creep, all other factors being equal.
Is Lower Compression Set Material More Durable?
Yes, low compression set materials are generally more durable. Generally, higher compression set materials are failure-prone when dimensional accuracy and manufactured shape are necessary for a component function. On this basis, it is best practice to select the lowest compression set material available/commercially practical for tasks in which equipment dimensions and device repeatability are factors.
What Testing Standards and Methods Are Used To Evaluate Compression Set in Materials?
Various testing standards and methods exist to evaluate the compression set of materials and are listed below:
- ASTM D395: Used to determine the compression set of rubber and rubber-like materials. The test involves compressing a specimen to a specific percentage of its original thickness and holding it at that compression for a specified period. The thickness of the specimen is measured after it has been released from the compression and allowed time to recover. The rate of recovery is also a factor to consider in determining the full properties.
- ISO 815: This is similar to ASTM D395 and is also used to determine the compression set of elastomers.
- ASTM D575: Used to determine the compression set of flexible cellular materials. The test involves compressing a specimen to a specific percentage of its original thickness. The materials are held at that compression for a specified period. They are then released from the compression, allowed time to recover, and measured for any reduction in thickness.
- ISO 1856: Used to determine the compression set of rigid cellular plastics.
- ASTM D3950: This test method is used to determine the compression set of thermoplastic elastomers (TPEs), and it is similar in principle to the other polymer tests.
What Materials Are Best for High Compression Set Gaskets?
The best material for high compression set gaskets are:
- Crushable metal framed asbestos.
- PVC and neoprene blend.
- Silicone and EPDM (Ethylene Propylene Diene Monomer) foams.
What Materials Are Best for Low Compression Set Gaskets?
The most commonly used materials for low compression set gaskets are listed below:
- Viton fluoroelastomer.
- Silicone rubbers.
- Nitrile synthetic rubber.
- EPDM (Ethylene Propylene Diene Monomer).
- PTFE (Polytetrafluoroethylene).
Is Low Compression Set Good?
It depends. Low compression set gaskets are resilient and recover when uncompressed. They maintain contact pressure at the junction and can be reused when the parts are disassembled and reassembled.
Does High Compression Set Produce Durable Material?
It depends. High compression set materials can be thought of as durable when they’re used in ways that exploit their properties well. The durability of materials is highly related to the type of applications they are normally and correctly used for. High compression set materials tend to permanently distort when overloaded. For example, a car engine cylinder head gasket is designed to crush to precisely set the gap from block to cylinder head and seal the cylinders off from the waterways. So the gasket intentionally crushes but will serve for as long as the cylinder head is not removed, which is commonly several years and thousands of hours of operation under demanding conditions.
Summary
This article presented high vs. low compression sets, explained what each is, and discussed each of their advantages and disadvantages. To learn more about compression sets, contact a Xometry representative.
Xometry provides a wide range of manufacturing capabilities and other value-added services for all of your prototyping and production needs. Visit our website to learn more or to request a free, no-obligation quote.
Disclaimer
The content appearing on this webpage is for informational purposes only. Xometry makes no representation or warranty of any kind, be it expressed or implied, as to the accuracy, completeness, or validity of the information. Any performance parameters, geometric tolerances, specific design features, quality and types of materials, or processes should not be inferred to represent what will be delivered by third-party suppliers or manufacturers through Xometry’s network. Buyers seeking quotes for parts are responsible for defining the specific requirements for those parts. Please refer to our terms and conditions for more information.
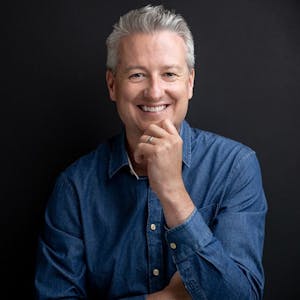