Monel® 400 is a nickel-copper alloy renowned for its exceptional capabilities across many applications. With its unique combination of corrosion resistance, high strength, and excellent mechanical characteristics, Monel 400 has found its place in numerous industries across the globe. From marine and chemical processing to aerospace and electrical equipment, this alloy has proven its mettle in challenging environments.
This article will discuss Monel 400, its diverse uses, detailed composition, and key properties.
What Is Monel 400?
Monel 400 (also known as Phyweld 400 and Nicorros LC), is a nickel-copper alloy that is known for its excellent corrosion resistance in a wide range of environments. It is composed of approximately 63-70% nickel and 28-34% copper, along with small amounts of iron, manganese, carbon, and silicon. It possesses a single-phase structure, forming a solid solution of nickel and copper. The material exhibits significant strength, corrosion resistance, ductility, and thermal conductivity.
Such properties make Monel 400 valuable to many industries. Some typical uses of Monel 400 include chemical processing equipment, hydrocarbon processing facilities, marine engineering components, and heat exchangers. Its corrosion resistance makes it suitable for environments where it’s exposed to seawater, alkaline solutions, and organic, sulfuric, hydrofluoric, or phosphoric acids. Additionally, its excellent thermal conductivity makes it an attractive choice for heat-transfer applications. For more information, see our guide on Monel.
What Is Monel 400 Used For?
Monel 400, with its excellent corrosion resistance and mechanical properties, finds numerous applications, including as:
- Feed-water and steam-generator tubing.
- Brine heaters and seawater scrubbers.
- Sulfuric acid and hydrofluoric acid alkylation plants.
- Pickling bath heating coils.
- Transfer piping from oil refinery crude columns.
- Uranium refining and nuclear fuel production.
- Manufacturing of perchloroethylene and chlorinated plastics.
- Monoethanolamine (MEA) reboiling tube.
- Propeller and pump shafts.
How Is Monel 400 Made?
Monel 400 is typically produced through a process known as alloying. It's important to note that specific manufacturing processes and techniques may vary among different manufacturers, but it always follows a few general steps:
- Melting: The primary raw materials (nickel and copper) are melted in a furnace at high temperatures.
- Alloying: Once the materials are molten, they are thoroughly mixed to ensure a homogeneous blend of nickel and copper. Alloying elements such as iron, manganese, carbon, and silicon are added in precise amounts at this point to achieve the required composition of Monel 400.
- Casting: The molten alloy is then cast into forms such as ingots or billets. This step allows the alloy to solidify and take on a specific shape which will later be processed into the desired final product.
- Forming: The cast alloy is then subjected to various forming processes, such as hot or cold rolling, forging, or extrusion. These processes shape the alloy into the desired forms, such as sheets, bars, plates, rods, or wires.
- Heat Treatment: After forming, the Monel 400 alloy may need to be annealed or tempered. These heat treatments optimize the material's mechanical properties, including its strength, hardness, and ductility.
- Finishing: The final step involves surface finishing. That may require cutting, machining, surface treatment, and quality inspections to ensure that the Monel 400 products meet the desired specifications and quality standards.
What Is the Chemical Composition of Monel 400?
Monel 400 is a primarily nickel-copper alloy. At a minimum, it will contain 63% Ni and 28-34% Cu. The remainder is made up of iron, manganese, and other compounds. The rough chemical composition of Monel 400 is given in Table 1 below:
Ni | Cu | Fe | Mn | Si | C | S |
---|---|---|---|---|---|---|
Ni Remainder (min 63%) | Cu 28-34% | Fe <=2.5% | Mn <=2.0% | Si <=0.5% | C <=0.3% | S <=0.024% |
Property | Metric | Imperial |
---|---|---|
Property Density | Metric 8.8 g/cm3 | Imperial 0.319 lbs/in3 |
Property Yield Strength | Metric 172-345 MPa | Imperial 25-50 ksi |
Property Tensile strength (annealed) | Metric 517-620 MPa | Imperial 75-90 ksi |
Property Hardness | Metric 115-240 BHN | Imperial 115-240 BHN |
Property Magnetic Permeability | Metric Annealed moderately | Imperial Annealed moderately |
Table Credit: https://www.azom.com/article.aspx?ArticleID=9338
Machinability Rating of Monel 400
Monel 400 has a machinability rating of 44%, indicating that the material is relatively difficult to machine compared to standard reference material. This rating suggests that it poses challenges during machining operations and may require special tools or techniques to achieve desired results.
What Are the Thermal Properties of Monel 400?
The thermal properties of Monel 400 can be found in Tables 3 and 4 below:
Property | Value |
---|---|
Property Melting point | Value 1300 -1350°C |
Property Curie temperature | Value 35°C |
Temperature (°C) | Mean Linear Expansionb (m/m°C) | Thermal Conductivitya (W/m°C) | Specific Heata (J/kg°C) | Electrical Resistivity^a,c (m) |
---|---|---|---|---|
Temperature (°C) -200 | Mean Linear Expansionb (m/m°C) - | Thermal Conductivitya (W/m°C) - | Specific Heata (J/kg°C) - | Electrical Resistivity^a,c (m) 0.36 |
Temperature (°C) -180 | Mean Linear Expansionb (m/m°C) 11.1 | Thermal Conductivitya (W/m°C) 16.5 | Specific Heata (J/kg°C) 223 | Electrical Resistivity^a,c (m) - |
Temperature (°C) -130 | Mean Linear Expansionb (m/m°C) 11.4 | Thermal Conductivitya (W/m°C) 18.2 | Specific Heata (J/kg°C) 320 | Electrical Resistivity^a,c (m) - |
Temperature (°C) -70 | Mean Linear Expansionb (m/m°C) 12.1 | Thermal Conductivitya (W/m°C) 19.8 | Specific Heata (J/kg°C) 378 | Electrical Resistivity^a,c (m) - |
Temperature (°C) 21 | Mean Linear Expansionb (m/m°C) - | Thermal Conductivitya (W/m°C) 22 | Specific Heata (J/kg°C) 427 | Electrical Resistivity^a,c (m) 0.511 |
Temperature (°C) 100 | Mean Linear Expansionb (m/m°C) 14.2 | Thermal Conductivitya (W/m°C) 24 | Specific Heata (J/kg°C) 445 | Electrical Resistivity^a,c (m) 0.537 |
Temperature (°C) 200 | Mean Linear Expansionb (m/m°C) 15.2 | Thermal Conductivitya (W/m°C) 26.9 | Specific Heata (J/kg°C) 459 | Electrical Resistivity^a,c (m) 0.559 |
Temperature (°C) 300 | Mean Linear Expansionb (m/m°C) 15.7 | Thermal Conductivitya (W/m°C) 30.1 | Specific Heata (J/kg°C) 470 | Electrical Resistivity^a,c (m) 0.574 |
Temperature (°C) 400 | Mean Linear Expansionb (m/m°C) 16.1 | Thermal Conductivitya (W/m°C) 33.4 | Specific Heata (J/kg°C) - | Electrical Resistivity^a,c (m) 0.587 |
Temperature (°C) 500 | Mean Linear Expansionb (m/m°C) 16.3 | Thermal Conductivitya (W/m°C) 36.5 | Specific Heata (J/kg°C) - | Electrical Resistivity^a,c (m) 0.603 |
Temperature (°C) 600 | Mean Linear Expansionb (m/m°C) 16.6 | Thermal Conductivitya (W/m°C) 39.4 | Specific Heata (J/kg°C) - | Electrical Resistivity^a,c (m) 0.62 |
Temperature (°C) 700 | Mean Linear Expansionb (m/m°C) 17 | Thermal Conductivitya (W/m°C) 42.4 | Specific Heata (J/kg°C) - | Electrical Resistivity^a,c (m) 0.639 |
Temperature (°C) 800 | Mean Linear Expansionb (m/m°C) 17.4 | Thermal Conductivitya (W/m°C) 45.5d | Specific Heata (J/kg°C) - | Electrical Resistivity^a,c (m) 0.658 |
Temperature (°C) 900 | Mean Linear Expansionb (m/m°C) 17.7 | Thermal Conductivitya (W/m°C) 48.8d | Specific Heata (J/kg°C) - | Electrical Resistivity^a,c (m) 0.675 |
Temperature (°C) 1000 | Mean Linear Expansionb (m/m°C) 18.1^d | Thermal Conductivitya (W/m°C) - | Specific Heata (J/kg°C) - | Electrical Resistivity^a,c (m) 0.692 |
Table Credit: https://www.specialmetals.com/documents/technical-bulletins/monel-alloy-400.pdf
a This also applies to Monel 405 (or R-405), the free-machining version of Monel 400
b Annealed material. Between 21°C and temperature indicated
c Annealed material
d Extrapolated data
What Are the Common Forms of Monel 400 Material?
Monel 400 is available in different forms to suit different manufacturing and fabrication requirements. The most common forms are listed below:
Sheet
Monel 400 sheet stock is flat, thin, and flexible. It is strong, resists corrosion, and is easy to weld. This makes it suitable for sheet metal fabrication, cladding, roofing, chemical processing equipment, and marine applications.
Bar
Monel 400 bars are solid cylindrical shapes with varying diameters and lengths. They exhibit high strength, good corrosion resistance, and are highly machinable. These bars are commonly used in shafts, fasteners, bolts, fittings, pump components, valve stems, and machine parts.
Plate
Plates of Monel 400 are flat, rectangular, and available in different thicknesses and dimensions. They are strong, resist corrosion, and are formable into other shapes. Plates find use in structural components, pressure vessels, tanks, heat exchangers, and marine environments.
Hot Rolled
Hot rolled Monel 400 is formed by the process of hot rolling at high temperatures. This treatment improves its strength and toughness, making it suitable for structural components, heat exchangers, piping systems, and marine applications.
Annealed
Some Monel 400 undergoes an annealing process to relieve internal stresses and enhance ductility. That makes it more formable so it’s easier to fabricate or machine. This form is commonly used in sheet metal fabrication, welded components, machined parts, and electrical connectors.
Cold Drawn
Cold drawn Monel 400 is formed through cold drawing or cold working processes. It is stronger than the basic material and better maintains accurate dimensions. It is used for precision components, fasteners, springs, wire mesh, and electrical applications.
What Are the Advantages of Using Monel 400?
Here are some key advantages of Monel 400:
- It exhibits exceptional resistance to corrosion in a wide range of environments, including seawater, acids (sulfuric acid, hydrochloric acid, etc.), alkaline solutions, and various corrosive gasses. This corrosion resistance makes it suitable for chemical processing, marine, and offshore applications.
- Monel 400 is strong and tough and retains its properties even at elevated temperatures. This combination of properties allows it to withstand demanding conditions, such as high-pressure and high-stress environments, making it suitable for applications in aerospace, oil and gas, and power-generation industries.
- The metal exhibits resistance to erosion and cavitation damage, making it suitable for applications involving high-velocity fluid flow, such as pumps, impellers, and propeller shafts.
- Monel 400 metal accepts various welding techniques, such as gas tungsten arc welding (GTAW) and shielded metal arc welding (SMAW). This gives manufacturers flexibility in their fabrication techniques.
- It displays little magnetic permeability. Monel 400 is thus great where nonmagnetic or minimally magnetic behavior is critical.
- It is resistant to pitting, crevice corrosion, and stress corrosion cracking, which helps ensure the long-term reliability of equipment and components made from Monel 400.
What Are the Disadvantages of Using Monel 400?
While Monel 400 offers many advantages, it is important to consider its potential disadvantages as well. Listed below are some of those disadvantages:
- It is generally more expensive than other common alloys such as stainless steel or carbon steel. The higher cost of Monel 400 can be a limiting factor, especially in cost-sensitive applications.
- It can be susceptible to chloride stress corrosion cracking in certain conditions, particularly in the presence of chlorides at elevated temperatures.
- Monel 400’s performance may be limited in extremely high-temperature applications compared to specialized high-temperature alloys.
- This metal can be more challenging to machine compared to some other alloys due to its tendency to work-harden. Proper machining techniques, tools, and cooling methods must be employed to achieve good results.
What Is the Difference Between Monel 400 and Monel 500?
Monel 400 and Monel K-500 are two distinct alloys that differ in their strengthening mechanisms and properties. Monel 400 achieves its strength through solid solution strengthening, where a solid solution of nickel and copper enhances its mechanical properties. In contrast, Monel K-500 gains its strength through precipitation hardening which involves the formation of precipitates within the alloy matrix. Furthermore, the addition of titanium and aluminum in Monel K-500 enables age hardening, a heat treatment process that further enhances its strength and hardness. This attribute makes Monel K-500 advantageous for specific applications that demand increased performance.
When it comes to overall performance, Monel K-500 tends to outperform Monel 400. The precipitation hardening mechanism in Monel K-500 makes it harder and stronger, so it’s better for applications requiring high strength. Both alloys, however, exhibit excellent corrosion resistance, displaying resilience in the face of corrosive environments such as seawater, acids, alkalis, and salts.
Despite their similarities in corrosion resistance, Monel K-500 is more susceptible to stress corrosion cracking in certain environments due to its increased strength. This factor should be carefully considered when selecting between the two alloys.
Another significant difference between the two alloys is their magnetic properties. Monel 400 can be affected by magnetism in certain cases, while Monel K-500 remains non-magnetic in all circumstances.
What Is the Difference Between Monel 400 and Monel 405?
Monel 405, or R-405 (UNS N04405), is a specialized form of Monel 400 that prioritizes machinability. Referred to as the free-machining grade of alloy 400, R-405 contains more sulfur to make it more machinable.
Despite this, alloy R-405 maintains similar physical properties and corrosion resistance to alloy 400. However, there may be slight differences in strength, hardness, and other mechanical attributes. For more information, see our guide on Monel 405.
Summary
This article presented Monel 400, explained it, and discussed its composition and properties. To learn more about Monel 400, contact a Xometry representative.
Xometry provides a wide range of manufacturing capabilities and other value-added services for all of your prototyping and production needs. Visit our website to learn more or to request a free, no-obligation quote.
Copyright and Trademark Notice
- Monel®: Monel 400 is a registered trademark of Special Metals Corporation.
Disclaimer
The content appearing on this webpage is for informational purposes only. Xometry makes no representation or warranty of any kind, be it expressed or implied, as to the accuracy, completeness, or validity of the information. Any performance parameters, geometric tolerances, specific design features, quality and types of materials, or processes should not be inferred to represent what will be delivered by third-party suppliers or manufacturers through Xometry’s network. Buyers seeking quotes for parts are responsible for defining the specific requirements for those parts. Please refer to our terms and conditions for more information.
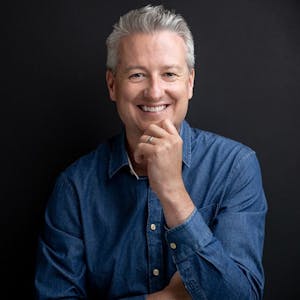