Monel® K500 is a nickel-copper alloy that is sought after for its high mechanical and corrosion-resistant properties as well as its ability to work at high temperatures. It is often found in marine, and oil & gas applications for its corrosion resistance and high-strength properties, it is also used in aircraft engines for its temperature resistance. While being made out of roughly two-thirds nickel and one-third copper, Monel K500 also has small amounts of aluminum, iron, manganese, and even smaller amounts of other elements. It is the specific combination of these elements which gives Monel K500 its properties.
What Is Monel K500?
Monel K500 is a corrosion-resistant nickel-copper alloy. Monel K500 is categorized as a superalloy, which means that it has excellent corrosion resistance and mechanical properties. It performs well at high temperatures close to its melting point. Monel K500 is non-magnetic which means it can be used in electrical applications. The broad composition of Monel K500 is as follows:
- 63% Nickel
- 0.25% Carbon
- 1.5% Manganese
- 2% Iron
- 27%–33% Copper
- 2.3%–3.15% Aluminum
- 0.35%–0.85% Titanium
For more information, see our guide on Monel Material.
What Is Monel K500 Used For?
Monel K500 can be used for a variety of applications but is currently found mostly in the following:
- Chemical industry (for valve and pump components).
- Blades and scrapers used in paper production.
- Centrifugal pumps in the marine industry.
- Pump shafts, instruments, and impellers in the oil & gas industry.
- Oil well drill collars.
- Electronic components and sensors.
How Is Monel K500 Made?
Monel K500 is manufactured by adding aluminum to a basic nickel-copper alloy. The aluminum is added through precipitation hardening (also known as age hardening). Precipitation hardening takes two stages. In the first step, the base alloy is heated to a high temperature and then quenched to lock the current grain structure. In the second step extremely small particles of the precipitant material, in this case, aluminum, are uniformly spread across the original material. The alloy is then heated again to a lower temperature and quenched. This allows for proper dispersal of the precipitant throughout the metal.
What Is the Chemical Composition of Monel K500?
Monel K500 is mostly made up of nickel (at a minimum of 63%) and also includes 27–33% copper and 2.3–3.15% aluminum. The composition of this alloy is designed for high strength and corrosion resistance. Other elements used to create Monel K500 are listed in Table 1 below:
Element | Min Percentage | Max Percentage |
---|---|---|
Element Nickel | Min Percentage 63 | |
Element Copper | Min Percentage 27 | Max Percentage 33 |
Element Aluminum | Min Percentage 2.3 | Max Percentage 3.15 |
Element Cobalt | Min Percentage - | Max Percentage 2 |
Element Iron | Min Percentage - | Max Percentage 2 |
Element Carbon | Min Percentage - | Max Percentage 0.25 |
Element Manganese | Min Percentage - | Max Percentage 1.5 |
Element Silicon | Min Percentage - | Max Percentage 1 |
Element Titanium | Min Percentage 0.35 | Max Percentage 0.85 |
Element Sulfur | Min Percentage - | Max Percentage 0.01 |
What Are the Properties of Monel K500?
The properties of Monel K500 will differ depending on how it is made, and its final form. For example, if it is in sheet, strip, tube, or bar form and whether it has been hot-finished or cold-drawn plus annealed or aged. Table 2 below lists the property values of Monel K500:
Property | Value |
---|---|
Property Density | Value 8.44 g/cm^3 |
Property Yield Strength | Value 690 MPa |
Property Hardness | Value 29 |
Property Magnetism | Value Non-magnetic for temperature as low as -150 °F |
Machinability Rating of Monel K500
Monel K500 has a machinability difficulty rating of 75%. This means it is moderate/difficult to machine. This is because it is specifically a wear-resistant alloy. Although this alloy is not easy to machine it can still be machined with regular machining tools to a good standard. Monel K500 has a high shear strength which results in a lot of heat generation during machining. This heating can lead to tooling welding itself to the workpiece.
What Are the Thermal Properties of Monel K500?
At 200 °F, Monel K500 has a thermal expansion of 7.6 in/in/F, a thermal conductivity of 19.4 Btu-in/h/ft2/F, and a specific heat capacity of 0.107 Btu/lb/F. At 1,600 °F Monel K500 has a thermal expansion of 9.6 in/in/F, a thermal conductivity of 282 Btu-in/h/ft2/F, and a specific heat capacity of 0.157 Btu/lb/F.
What Are the Common Forms of Monel K500 Material?
Monel K500 can be procured in many forms including: pipe, tube, sheet, strip, plate, round bar, flat bar, and hexagonal wire. Each of these forms may be created using different post processes such as age hardening, cold working, and hot working. Each of these processes will affect the microstructure and properties and therefore the supplier should be consulted to understand the specific properties of each form.
What Are the Advantages of Using Monel K500?
The advantages of using Monel K500 over other materials stem from the properties it possesses. These properties include:
- Corrosion Resistance: Monel K500 is highly corrosion-resistant, however, it may be susceptible to corrosion in slow-moving or stagnant salt water. It is also at risk of stress corrosion cracking.
- High Strength: Monel K500 has very high strength, and it retains its strength even at high temperatures.
- Temperature Resistance: Monel K500’s temperature resistance allows it to be used in the most demanding environments such as aircraft engines.
What Are the Disadvantages of Using Monel K500?
Although Monel K500 has outstanding mechanical and chemical properties there are some drawbacks to using it, which are as follows:
- High Cost: The high cost of Monel K500 means that it should only be used in situations for which there are no other materials with sufficient properties. This limits its use to advanced applications.
- Work Hardening: Monel K500 will work harden as it is machined. This will result in each layer becoming progressively harder to machine. This causes tools to wear more quickly and risks tools welding themselves to the metal.
- Stress Corrosion Cracking: Monel K500 is at risk of stress corrosion cracking.
- Pitting Corrosion: Monel K500 is at risk of pitting corrosion when submersed in slow-moving or stagnant salt water. However, it is well suited to fast-moving salt water, which is why it is used in maritime pumps.
What Is the Difference Between Monel K500 and Monel 400?
Both Monel 400 and Monel K500 are part of a family of nickel-copper alloys. Both materials share a lot of similarities but are also distinctly different. Monel K500 is a nickel-copper alloy with the addition of aluminum and titanium which gives it corrosion resistance and strength properties. Whereas Monel 400 is a nickel-copper alloy without the addition of these two elements, which gives it corrosion resistance and workability characteristics. K500 is more corrosion-resistant than Monel 400 due to the presence of aluminum; K500 is also stronger due to the presence of titanium.
What Is the Difference Between Monel K500 and Monel R405?
Monel R405 is the same composition as Monel 400, with the addition of more sulfur. The addition of more sulfur to Monel R405 gives the alloy better machinability. This is because the sulfur creates nickel-sulfur inclusions which act as breaking points in the composition. Therefore the differences between Monel K500 and Monel R405 are the same as the differences between Monel K500 and Monel 400, but with the additional fact that Monel R405 has increased machinability. The difference between Monel K500 and Monel 400 is that Monel K500 has increased strength characteristics and Monel 400 has increased workability characteristics. Monel K500 is also more corrosion-resistant than Monel 400.
Summary
This article presented Monel K500, explained it, and discussed its composition and uses. To learn more about Monel K500, contact a Xometry representative.
Xometry provides a wide range of manufacturing capabilities and other value-added services for all of your prototyping and production needs. Visit our website to learn more or to request a free, no-obligation quote.
Copyright and Trademark Notices
- Monel® is a registered trademark of Special Metals Corporation.
Disclaimer
The content appearing on this webpage is for informational purposes only. Xometry makes no representation or warranty of any kind, be it expressed or implied, as to the accuracy, completeness, or validity of the information. Any performance parameters, geometric tolerances, specific design features, quality and types of materials, or processes should not be inferred to represent what will be delivered by third-party suppliers or manufacturers through Xometry’s network. Buyers seeking quotes for parts are responsible for defining the specific requirements for those parts. Please refer to our terms and conditions for more information.
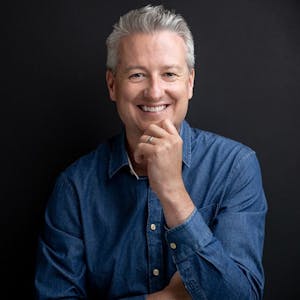