O1 tool steel is a high-carbon and high-chromium alloy used extensively in tool manufacturing. It is crafted into tools because of its optimal combination of hardness, wear resistance, and machinability.
This article will discuss O1 steel, delving into its use, processing intricacies, resistance factors, and the boundaries it navigates within the realm of tool steel.
What Exactly Is O1 Tool Steel?
O1 tool steel, classified as an oil-hardening steel, is a high-carbon and high-chromium alloy used extensively in tool manufacturing. It is designed for tool and die applications. O1 tool steel stands out in part due to the oil quenching that it undergoes during heat treatment, distinguishing it from its air-hardening counterparts.
Its composition includes approximately 0.95-1.1% carbon, 0.5% chromium, 1.0% manganese, 0.6% tungsten, and traces of vanadium. All of this provides a balanced mix of hardness, wear resistance, and machinability. This makes O1 a preferred choice for applications that demand precision and reliability, such as: woodworking tools, punches, and tool and die making.
O1 tool steel's defining characteristics stem from the oil quenching process during heat treatment. Quenching improves the metal’s hardness and dimensional stability.
Is O1 Tool Steel the Same as Carbon Steel?
No, O1 tool steel is not the same as generic carbon steel. While O1 tool steel contains a significant amount of carbon, it is a specific alloy designed for tools and dies. Its composition includes elements such as chromium, tungsten, and vanadium, which are carefully balanced to provide enhanced hardness, wear resistance, and machinability. The inclusion of chromium in O1 tool steel contributes to its exceptional hardenability and corrosion resistance, characteristics not typically associated with basic carbon steels.
In essence, O1 tool steel is a distinct alloy with tailored properties, making it well-suited for specialized tool manufacturing, whereas carbon steel is a broader category encompassing many steel types with varying compositions and properties.
Why Is O1 Tool Steel Preferred in Tool Making?
O1 tool steel is preferred in tool making because it strikes an excellent balance of hardness, wear resistance, and machinability. It is well suited for demanding applications that require precision and reliability.
Its high carbon content (0.95 -1.1%) contributes to its excellent hardness, allowing tools made from O1 to maintain sharp edges and resist deformation during use. The inclusion of chromium in the alloy enhances hardenability. It’s what makes the oil quenching process so effective at hardening the surface. This feature is crucial in tool making as it ensures the tools can withstand mechanical stresses and abrasive conditions. The tungsten content in O1 steel further improves wear resistance, making tools more durable and capable of withstanding repeated use over time without significant loss of performance.
Machinability is another key factor in O1 tool steel's appeal among tool makers. Its composition allows for relatively easy machining and shaping, facilitating the production of intricate tool designs with precision.
How Does O1 Tool Steel Offer Superior Durability Compared to 4140 Pre Hardened Steel?
O1 tool steel is more durable than 4140 pre-hardened steel primarily because of the hardening process and the alloy’s inherent wear resistance. O1 tool steel is hardened by its carbon and chromium content as well as the heat treatment and oil quenching stage. The superior hardness allows tools to maintain sharp edges, resist deformation, and endure significant abrasion.
In contrast, while 4140 pre-hardened steel is strong, it may not exhibit the same level of hardness as O1 tool steel. This difference in hardness directly impacts the metal’s capacity to withstand wear and maintain cutting edges.
Tool steel hardness tests, such as Rockwell hardness testing, reveal that O1 tool steel ordinarily achieves higher hardness values than 4140 pre-hardened steel. The superior hardness of O1 makes it a durable and preferable choice for tools that experience significant wear and abrasion.
Who Typically Uses O1 Tool Steel?
Metalworkers, machinists, and toolmakers prefer O1 tool steel because its properties cater to the demands of precision machining and tool manufacturing. Metalworkers engaged in tasks like forging and shaping metal also favor O1 tool steel for its excellent machinability. Its composition is simple to machine, enabling metalworkers to create intricate designs and precise components. Machinists like O1 for its combination of hardness and machinability. This steel can be readily shaped and machined but still maintains the dimensions and sharpness required for cutting tools and dies.
Are Knife Makers the Main Users of O1 Tool Steel?
No, though knife makers do often use O1 tool steel, they’re far from the only ones. The metal is also extremely valuable in other sectors. It’s often found in molds and cutting dies, among other tools.
When Should O1 Tool Steel Be Chosen Over Other Types?
O1 tool steel should be chosen when a combination of high hardness, excellent wear resistance, and machinability is critical for the intended application.
The biggest reason to choose O1 tool steel is if your part must maintain a sharp cutting edge, as is the case in: tools and dies, woodworking tools, and precision machining applications. The high carbon content and chromium composition in O1 steel contribute to its exceptional hardness, ensuring tools can withstand heavy use without significant dulling.
Where Does O1 Tool Steel Stand in Terms of Global Production?
It’s hard to rank O1 tool steel in terms of global production since worldwide data on production is limited and inconsistent. However, here are a few relevant sources to examine:
- Market Share: Reports estimate the global tool steel market size at around 5 million metric tons in 2023, with a projected CAGR (compound annual growth rate) of 4.5% until 2030. The share of O1 steel within the overall tool steel market is unknown, but it is likely to be a smaller percentage than more common tool steels like A2, D2, and H13.
- Leading Producers: Major producers of O1 tool steel include: Voestalpine, SCHMOLZ+BICKENBACH, Sandvik, Fushun Special Steel, and BaoSteel. However, their production volumes are not publicly disclosed, making it difficult to assess O1's global ranking.
- Application-Specific Importance: O1 tool steel holds significant importance in items like: knives, chisels, punches, and dies. Its combination of good wear resistance, toughness, and hardenability makes it a popular choice for these applications.
- Regional Variations: Production and consumption of O1 tool steel can vary significantly across different regions. For instance, it might be more prominent in countries with strong knifemaking cultures, where the demand for high-quality steel in cutlery production influences its prevalence. Additionally, specific manufacturing industries, such as precision tools and die making, may heavily rely on O1 tool steel due to its favorable properties.
Is O1 Tool Steel the Best Choice for High-Precision Tools?
It depends on the task’s specific requirements. O1 tool steel is an excellent choice for high-precision tools in many situations due to its combination of hardness, wear resistance, and machinability. Its ability to maintain a sharp cutting edge and withstand heavy use makes it suitable for precision machining, tool and die making, and other applications where accuracy is crucial.
However, the "best" choice depends on factors such as: the type of tool, the specific demands of the application, and the working conditions. In some cases, you may be better off with other tool steels or alloys with different properties. It's essential to consider the specific needs of the tool and its employment to determine the most suitable material for high-precision tools.
Is O1 Tool Steel Ductile?
Yes, O1 tool steel is considered to be relatively ductile. While O1 tool steel is not as ductile as some lower carbon steels, its composition, which includes a balance of carbon, chromium, and tungsten, confers reasonable ductility. This allows O1 tool steel to withstand certain levels of deformation without fracturing, making it suitable for various tool and die applications that need some degree of toughness along with high hardness and wear resistance. The specific heat treatment process can also influence the balance between hardness and ductility in O1 tool steel.
To learn more, see our guide on Ductile Materials.
How Is O1 Tool Steel Manufactured and Processed?
O1 tool steel is manufactured and processed by melting and casting the proper mixture of iron, carbon, chromium, manganese, tungsten, and other alloying elements. The precise composition is crucial to achieving the right balance of hardness, wear resistance, and machinability. The molten steel is then hot-worked into a usable shape, such as bars or sheets. This process helps refine the steel's structure and ensures uniformity.
Initial heat treatment starts with annealing, a process in which the steel is heated to a specific temperature and then slowly cooled to relieve internal stresses and refine the grain structure. This step sets the foundation for subsequent hardening processes which harden the O1 tool steel to its final level.
The steel is next heated to a critical temperature, typically above 800 °C (1,475 °F), and then quenched in oil. This rapid quenching "freezes" the steel's structure, enhancing its hardness.
The hardened steel is then tempered, a process where it is reheated to a lower temperature (usually between 177-316 °C) to reduce brittleness and achieve the desired balance of hardness and toughness. This step is crucial to striking the right middle ground.
The precise parameters of each step, including temperatures and cooling rates, are critical to controlling the final properties of O1 tool steel. The careful manipulation of these processes allows manufacturers to tailor the steel for specific applications, making it suitable for use in a variety of cutting tools, dies, and precision instruments.
Can O1 Tool Steel Be Recycled or Repurposed?
Yes, O1 tool steel can be recycled or repurposed. Steel, including tool steels like O1, is highly recyclable. The recycling process involves melting the metal and reforming it into new products. Since steel maintains its properties and durability even after multiple cycles of recycling, it can be considered a sustainable material.
The recycling of O1 tool steel can be part of a broader steel recycling system that conserves resources and energy. Repurposing may also involve reshaping or reheat treating the steel for different applications, extending its lifecycle, and reducing the need for new raw materials.
What Are the Limitations of Working With O1 Tool Steel?
Working with O1 tool steel, while advantageous in many respects, comes with certain limitations such as:
- Without proper care and maintenance, exposure to moisture and corrosive environments can lead to rusting and degradation.
- It may not be the best choice for tools that are subjected to high temperatures for extended periods.
- While the heat treatment process imparts desirable properties on O1 tool steel, achieving the optimal balance of hardness and toughness requires precise control of temperatures and cooling rates.
- O1 is more expensive than some other tool steels. This cost factor may influence your decision-making process when selecting materials.
- While it excels in applications requiring high hardness and wear resistance, it may be unsuitable for tasks involving heavy impacts or sudden loads.
- Machining processes need to be carefully managed to avoid excessive tool wear and achieve precise results.
Is O1 Tool Steel Difficult To Maintain?
No, O1 tool steel is not inherently difficult to maintain, but proper care is essential to prevent corrosion. The surfaces must be regularly cleaned to remove dirt, debris, and any substances that may contribute to corrosion. Dry the tools thoroughly after use and before storage. Moisture can accelerate corrosion, so keeping tools dry is crucial. A thin layer of oil or other protective coating can act as a barrier against moisture to prevent rust. Limit O1 tool steel’s exposure to corrosive environments whenever possible. If tools will be used in corrosive conditions, take extra precautions and consider applying additional protective coatings.
Why Does O1 Tool Steel Differ in Corrosion Resistance?
The specifics of O1 tool steel’s corrosion resistance are primarily attributed to its composition and the specific heat treatment processes employed during its manufacture. O1 tool steel contains a significant amount of carbon, which enhances its hardness and wear resistance. However, higher carbon content can make the steel more susceptible to corrosion. The inclusion of chromium helps to offset this problem, but O1 steel is nowhere near as resilient as stainless steel, which has far more chromium.
The heat treatment process — particularly the quenching step — can influence the steel's corrosion resistance. O1 tool steel is oil-hardened, which contributes to its high hardness but may leave the surface more vulnerable to corrosion than steels that undergo different quenching processes.
The surface finish of O1 tool steel can affect its corrosion resistance as well. A polished or coated surface provides better protection against corrosive elements compared to a rough or untreated surface.
Corrosion rates are also influenced by the environment in which the O1 tool steel is used. Exposure to moisture, chemicals, and other corrosive agents will accelerate corrosion. Proper storage and maintenance practices can mitigate these effects.
How Does O1 Tool Steel Compare with Other Tool Steels?
O1 tool steel compares favorably with other tool steels, offering a unique balance of hardness, wear resistance, and machinability. Its hardness is comparable to other popular tool steels like D2 and A2. O1 tool steel exhibits good wear resistance, allowing tools made from this steel to withstand abrasion and maintain their cutting performance over time. While it may not match the wear resistance of some high-speed steels like M2, it provides a well-rounded balance.
O1 tool steel’s composition makes it relatively easy to shape, form, and machine. This machinability is a notable advantage over some other high-alloy tool steels that can be challenging to machine. O1 tool steel is susceptible to corrosion, however, so it may not perform as well in corrosive conditions as stainless tool steels like 440C. However, proper maintenance practices can mitigate corrosion risks.
O1 tool steel has limitations in red hardness, or its ability to retain the same hardness at elevated temperatures. In contrast, high-speed steels like M2 exhibit better red hardness, making them suitable for particularly hot applications.
Does O1 Tool Steel Require Special Handling To Prevent Rust?
Yes, O1 tool steel requires special handling to prevent rust. It must be cleaned regularly to remove any contaminants, dirt, or residues that can contribute to corrosion. Dry your tools thoroughly after use. Moisture accelerates corrosion, so keeping the tools dry is essential. This also includes storing tools made from O1 tool steel in a dry environment and away from harsh conditions. Consider using moisture-absorbing materials in storage areas. Apply a thin layer of oil or other protective coatings after cleaning and drying to create a barrier against moisture and prevent rust formation. Implement a regular maintenance schedule, especially for tools that you don’t frequently use. Periodic inspections and reapplication of protective coatings can help prevent rust and give the tools long useful lifespans.
Is O1 Tool Steel More Affordable Than Other Tool Steels?
No, O1 tool steel is not always more affordable than other tool steels. O1 tool steel is a high-quality alloy with desirable properties, and its pricing is influenced by: its alloying components, precision manufacturing processes, and the overall demand for such steel in the market. In some cases, O1 tool steel may be more cost-effective than certain high-speed or premium tool steels, but it’s typically more expensive than basic carbon steels.
Your specific application and requirements will dictate your choice of tool steel. Consider factors like: hardness, wear resistance, and machinability. While O1 tool steel offers a good balance of these properties, its cost competitiveness depends on the context and the specific needs of the application.
Which Standard Measures the Hardness of O1 Tool Steel?
The Rockwell Hardness Scale (also called the Rockwell scale or HRC), is commonly used to measure the hardness of O1 tool steel. The Rockwell Hardness Test involves applying a specific load to the material's surface and measuring the depth of penetration.
Higher HRC values represent greater hardness. This standard measurement is widely employed in the tool-making industry to ensure that products have reached the proper hardness levels during heat treatment.
To learn more, see our guide on ASTM International Standards.
Summary
This article presented O1 tool steel, explained it, and discussed its various uses and limitations. To learn more about O1 tool steel, contact a Xometry representative.
Xometry provides a wide range of manufacturing capabilities and other value-added services for all of your prototyping and production needs. Visit our website to learn more or to request a free, no-obligation quote.
Disclaimer
The content appearing on this webpage is for informational purposes only. Xometry makes no representation or warranty of any kind, be it expressed or implied, as to the accuracy, completeness, or validity of the information. Any performance parameters, geometric tolerances, specific design features, quality and types of materials, or processes should not be inferred to represent what will be delivered by third-party suppliers or manufacturers through Xometry’s network. Buyers seeking quotes for parts are responsible for defining the specific requirements for those parts. Please refer to our terms and conditions for more information.
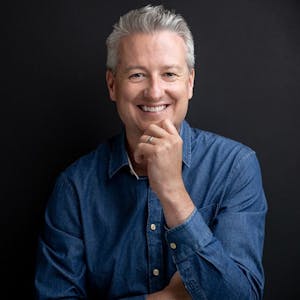