Despite its funky name, polyethylene (PE) might sound like a mystery material, but it’s much more familiar than you might think. Polyethylene is actually the most widely used commodity plastic—meaning it’s mass-produced and used for all sorts of applications. Our customers at Xometry use it to create some of the most popular products we interact with all the time, such as water bottles and plastic bags. It’s a durable material that can handle abrasion and constant use without fail. That’s what has led to polyethylene becoming such a popular material in manufacturing and a common choice for Xometry’s injection molding customers.
Below, we break down exactly what polyethylene is, other ways it’s used across industries, and the types that are available.
What Is Polyethylene (PE)?
Polyethylene is a type of thermoplastic. More specifically, it’s a homopolymer that contains ethene molecular chains. This structure is chemically what makes up the plastic we know and use so often, whether it’s for a container that holds your favorite takeout or more serious matters, like part of a knee replacement. There are four common types you’ll likely come across, which we break down later in this article.
Who Discovered Polyethylene?
We have Reginald Gibson and Eric Fawcett to thank for the invention of polyethylene. In the early 1930s, they experimented with ethylene and benzaldehyde. The reaction that came from this is what we now know as polyethylene. While the original methodology was pretty rudimental, today we have outlined processes, the right equipment, and safety guidelines to guide manufacturers in the creation of polyethylene.
A few years later in 1936, Imperial Chemical Industries filed a patent for polyethylene. Its adaptability made it a popular plastic to work with and more uses and processes for creating it emerged. Another chemist by the name of Karl Ziegler came along and figured out a way to specifically combine high-density polyethylene (HDPE), which is still an important process used nowadays. Even a portion of the process is named after him, the Ziegler-Natta catalyst or Ziegler-Natta polymerization—Natta being another chemist who played a part in the development.
What is the Chemical Formula for Polyethylene?
Time to think back to chemistry class. Polyethylene’s chemical formula is (C2H4)n. This means it has two carbon atoms that are linked to four hydrogen atoms. The “n” at the endpoints to the chain structure that polyethylene takes on. The image below shows the structure of polyethylene and how the chains are presented and repeated.
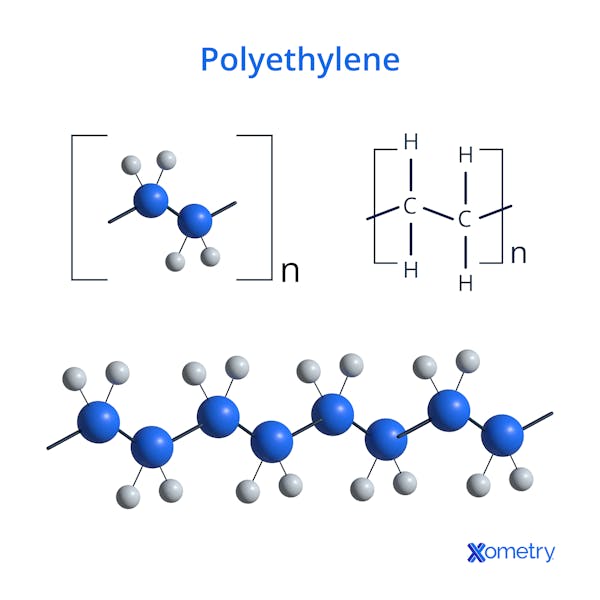
How is Polyethylene Produced?
As its name suggests, polyethylene is made out of ethylene, which results from both crude oil and natural gas. Ethylene needs a catalyst in order to transform into polyethylene, whereas different types of polymerization create other well-known plastics, like nylon.
One of the most common polymerization processes is called addition polymerization. Also known as chain reaction polymerization, there are several forms or subtypes that fall under this category, including coordination. What happens is that a catalyst (such as the famous Ziegler-Natta catalyst) is introduced and monomers will react and link up to create chains. This reaction creates the plastic.
Free radical polymerization, on the other hand, uses a radical to break the double bond between the two carbon atoms. This reaction leaves one side open on the molecule for bonding, and another molecule will slide right in and link up—creating the polymer chain. After these processes take place, you can shape polymer into long threads or filaments. These will be chopped into pellets and then passed along for processing into objects we’re familiar with.
What are the Properties of Polyethylene?
The properties of polyethylene are listed in Table 1 below:
What are the Common Applications of Polyethylene?
There are many different ways that we use polyethylene, from day-to-day products to more niche items. Some of the most common products include:
- Fishing nets
- Bottles
- Water tanks
- Bags and food containers
- Pipes and pipe fittings
- Flexible films
- Medical implants
- Ropes
- Wear-resistant liners for objects like chutes
Planning to Use Polyethylene For Your Parts?
What are the Types of Polyethylene?
There are so many things that can be crafted and produced with polyethylene, and no shortage of types either. Some are built better for more specific purposes whereas other types are great for just about anything in the world of plastics. Here are the four most common types of polyethylene and a few of their qualities and uses:
Ultra-High Molecular Weight Polyethylene (UHMWPE)
When you’re looking for a tough material, call on ultra-high molecular weight polyethylene (UHMWPE) for the job. This type can withstand heavy-duty wear and tear and has a low coefficient of friction, so it’s a worthy candidate for industrial purposes. UHMWPE has much longer chain structures, which gives it its name. We offer UHMWPE in our CNC machining process, which allows engineers to create parts like custom bushings, bearings, gears, rollers, and other components where a tough, low-friction plastic is desirable.
High-Density Polyethylene (HDPE)
The most popular format of this thermoplastic is high-density polyethylene (HDPE). It’s flexible in what it can be used for and a go-to choice for things like plastic bottles and sturdy pipes. The chemical composition of HDPE opens up a lot of possibilities, whether you need a strong, rigid material for surfaces and structures or something that can be crushed down and recycled after a one-time use. Xometry can CNC machine or injection mold HDPE.
Low-Density Polyethylene (LDPE)
If transparency is a selling point for you, low-density polyethylene will likely be a top choice. It’s clear in comparison to its opaque counterparts like HDPE, and it’s also softer. This is because it has lower crystallinity. Although it may not be as rigid or hard, this softness gives it more flexibility. Xometry can injection mold LDPE into products like bottles, food containers, fittings, and more.
Linear Low-Density Polyethylene (LLDPE)
Very similar to low-density polyethylene, linear low-density polyethylene (LLDPE) is bendable and softer. This is thanks to the open branches in its molecular structure. If you’re in need of a material with superb tensile strength and the ability to stretch and stay put (also known as elongation), LLDPE is the one. This plastic is popular for stretch films across different industries.
What are the Benefits of Using Polyethylene?
Polyethylene has many benefits. For starters, it’s strong, durable, and is resistant to wear and tear, which means it will last a long time. It’s relatively affordable, and easy to create and source. It’s a good insulator, making it ideal for insulating electrical components. Polyethylene is also resistant to chemicals and can hold up against certain solvents, and dilute acids. It is adaptable and easy to process, especially helpful for injection molding. Finally, it offers a lot of choice; polyethylene can be cut into filaments, pellets, films, and threads, and although some grades are transparent, you can also dye it.
Frequently Asked Questions About Polyethylene
Is Polyethylene Suitable for Plastic Injection Molding?
Yes, polyethylene is widely used for plastic injection molding. It is one of the easiest materials to work with. Its processing ease makes it popular in other applications as well, such as blow molding and film extrusion.
Why is Polyethylene Used in Plastic?
Polyethylene is a thermoplastic and as such is not used in plastic but is rather a plastic itself.
Is Polyethylene Environmentally Friendly?
No, polyethylene is not environmentally friendly. Like most thermoplastics, polyethylene is produced as a crude oil processing by-product and is not biodegradable. In fact, a large percentage of plastic pollution is due to discarded polyethylene films and bags.
What is the Difference Between Polyethylene and Polypropylene?
The difference between polypropylene (PP) and polyethylene (PE) is in the makeup of their polymeric chains. Polypropylene molecular chains are made from repeating propylene (C3H6)n monomers, whereas polyethylene chains are made from repeating ethylene (C2H4)n monomers.
What is the Difference Between Polyethylene Terephthalate and Polyethylene?
Polyethylene (PE) and polyethylene terephthalate (PET) are entirely different polymers, manufactured differently, and used for different applications. PET, with the chemical formula (C10H8O4)n, is produced from the polymerization of ethylene glycol and terephthalic acid, while PE ((C2H4)n) is produced from the polymerization of ethylene. Polyethylene is often used for making plastic films or containers, whereas PET is more typically used in fibers. It is more commonly known as polyester.
How Xometry Can Help
As you can see, polyethylene is a versatile material with multiple useful variants. At Xometry we offer instant quoting of machined or sheet-cut polyethylene parts, specifically UHMWPE and HDPE. If you’re looking for high-volume production capabilities, we’ve got you covered with our injection molding services. Choose from polyethylene or from dozens of other materials through the Xometry Instant Quoting Engine® today!
Disclaimer
The content appearing on this webpage is for informational purposes only. Xometry makes no representation or warranty of any kind, be it expressed or implied, as to the accuracy, completeness, or validity of the information. Any performance parameters, geometric tolerances, specific design features, quality and types of materials, or processes should not be inferred to represent what will be delivered by third-party suppliers or manufacturers through Xometry’s network. Buyers seeking quotes for parts are responsible for defining the specific requirements for those parts. Please refer to our terms and conditions for more information.
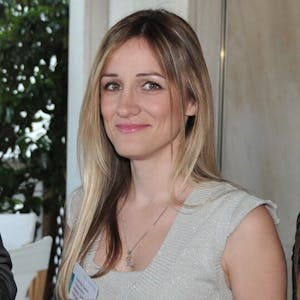