Shear test is used to measure the shear strength of materials in various industries such as construction, aerospace, automotive, and manufacturing. Torsion, lap, and shear vane tests are specific types of shear tests to determine the strength of certain elements, items and materials based on distinct working principles. However, shear tests are typically conducted by applying a specific force to a material tangentially, which can result in a sliding failure along the plane parallel to the force.
This article discusses the importance of shear testing in material engineering applications along with the required equipment, its advantages and disadvantages, and the applications where the shear test is needed.
What Is a Shear Test?
As a strength test, the shear test is conducted on a test sample to determine the reaction of a material to shear stress, modulus, and strain. The test sample material can be metal, wood, polymer, film, plastic, ceramic, adhesive, and fasteners in the applications of rheology, quality control, material development, adhesives, and structural engineering.
What Is the Importance of the Shear Test?
The shear test is primarily conducted to discover the behavior of materials such as metals and plastics under the influence of shear stress. On the other hand, shear tests are widely used by researchers to analyze the flow characteristics of fluids and gels, such as lotions, emulsions, resins, polymer melts, slurries, and oils. In this context, rheometers are widely used in rheology to identify the properties of a liquid. The results obtained from shear tests and rheometers enable the researchers to make critical decisions for cosmetic and pharmaceutical applications.
Manufacturers conduct shear tests to ensure that the products meet industry standards regarding durability and strength in various industries. Shear testing is also used by scientists to determine the properties of the material during the development stage. The results are evaluated to identify material features for a specific application. Shear testing can also show the strength of an adhesive that bonds different parts together and provides structural engineers with valuable insight to assess the strength and safety of structures.
Is Shear Testing the Same as Lap Shear Testing?
No, lap shear testing and shear testing are not the same, and each serves a distinct purpose, even though lap shear testing is a specific type of shear testing. While shear testing determines the resistance of a material to stress or force, lap shear testing evaluates the durability of an adhesive.
What Is the Shear Test Used For?
A shear test is performed to measure the resistance of a material to deformation or shear stress, which occurs when the interfaces of two parts slide over each other under the influence of load or force. In other words, the test is used to determine the shear strength of a material.
What is the Equipment Used for Shear Testing?
The equipment used in the shear test is given below:
- Single/Double-Column Universal Testing Machine: A single/double-column universal testing machine measures the strength of several materials by conducting shear, hardness, tensile, and compression tests in a single environment.
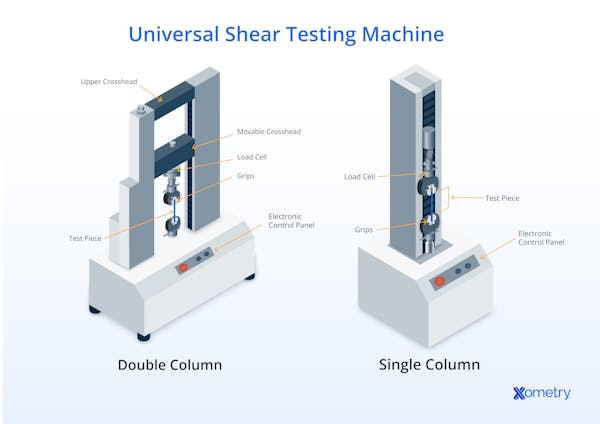
- Soil Shear Strength Tester: The soil shear strength tester is a portable device that measures the shear strength of soil in kPa precisely.
- Shear Blade: The shear blade can be used to cut metals with varying levels of sharpness and hardness formed by heat-treating, material selection, and processing.
- Direct/Residual Shear Data Acquisition Software: The direct/residual shear data acquisition software collects the data, calculates the friction angle, and records collected and calculated data simultaneously during the direct and residual shear testing.
- Tension Tester: A tension tester measures the shear strength of a material in the industries of metal wire, paper, and plastic film.
- Shear Sensor: A shear sensor measures the friction and shear force of materials by converting the mechanical strength into the electical signals precisely. The shear sensors can measure the reaction of a material under dynamic loading scenarios such as crash and fatigue testing in the automotive industry.
What Are the Different Types of Shear Testing?
Different types of shear testing are available to precisely measure the strength of material for specific applications and loading scenarios.
- Torsion Testing: Torsion testing is generally conducted to determine the reaction of a material to an excessive turning force through movement, loosening, and markup checks.
- Cutting: The cutting shear test is mainly used in the food industry to test food texture and measure the net force required to bite it. In this test, the food item is placed on a flat surface and cut using a shear blade to determine the toughness of the food.
- Direct Shear Test: This shear test is widely used in geotechnical engineering applications to test the strength of rocks and soils. The sample is placed in a shear box with a specific weight on the top, which results in deformation with the influence of a force applied in the horizontal direction
- Lap Shear Test: The lap shear test is conducted to determine the strength and durability of an adhesive by applying it between two flat surfaces. Once the surfaces are fully bonded after a certain time duration, a shear force is applied to move the surfaces in opposite directions until the bond is released by the shear stress, which is measured as the shear strength of the adhesive.
- Iosipescu Shear Test: The Iosipescu shear test is widely used to measure shear stress, shear modulus, and shear strain in construction and composite materials. Initially, a V-shaped notch is created at two opposite sides of a rectangular sample. Then, the sample is placed in a fixture, and opposing forces are applied perpendicular to the long axis of the sample to create a shear stress along the plane between two notches. Finally, the shear strain is measured using a strain gauge.
Is the Shear Test Used To Measure Shear Modulus?
Yes, the shear test can be used not only to measure the shear modulus but also to evaluate the shear strain, which represents the ability of the material to resist deformations induced by shearing or twisting.
The shear modulus test is typically conducted using the static torsion and standard tests. While the first is performed using a torsional pendulum or a material rod, the latter is conducted using various materials such as ASTM A938 for metallic wire and ASTM E143 for structural materials.
Can Shear Tests Determine the Shear Stress?
Yes, shear tests can determine the shear stress, focusing on the shear strain and shear modulus as well.
To learn more, see our full guide on the Shear Stress Formula.
How Does Shear Testing Work?
Shear testing is carried out by using a shear testing tool to determine the resistance of a material to shear stress or deformation during various loading scenarios. Shear testing is widely used to determine features such as ductility, toughness, yield strength, strain hardening exponent, and rigidity modulus of materials (e.g., polymeric, composite, metallic, and ceramic) through specific tests such as in-plane, punch, single, double, direct and torsion.
A shear test is typically conducted using a universal testing device following fundamental steps such as sample preparation, test setup, machine calibration, setting of parameters, test running, data collection/analysis, and reporting. The sequence of these steps is briefly explained below:
- The test sample is prepared according to the guidelines outlined by the test standard and type of the test.
- The test sample is carefully placed in the universal testing machine to prevent unintended stresses or shears prior to the test.
- The test machine and equipment are calibrated to ensure accurate measurements.
- Parameters of the test machine (loading rate, maximum rate, etc.) are set according to the test standards. The universal testing machine applies a load to the test sample at a set rate until the material starts deforming.
- Variation of the deformation with the load is recorded and analyzed by plotting stress-strain curves to calculate shear strength and modulus of the material.
- Features of the test sample, test conditions and results are reported in a document in detail. Yield shear stress, shear modulus, stress-strain curves and deformation data are the major results that can be obtained from a universal testing machine.
How To Read a Shear Test Result
A systematic analysis is required to understand and interpret the recorded data, which is generally represented in a graph or tabular format. The critical parameters of a material, such as shear strength, shear modulus, or shear strain, can be determined from a comprehensive data anaylsis to assess the performance of the material according to the industry standards.
What Is the Standard Measure for Concrete in a Shear Test?
Dimensions of a concrete test sample is standardized as 230 mm x 150 mm x 150 mm for a shear test. The concrete grades or strength classes of M20 and M30 should be 2.8 MPa and 3.5 MPa, respecively, according to the standards. The main factors influencing the shear strength of the concrete are corrosion, stirrup size and spacing, and concrete grade.
How Does the Shear Test Differ From Other Material Testings?
Shear tests should be considered apart from other widely used test types, such as compression and tensile tests. Compression tests measure the force normal to the test section required to compress (or deform) the material under the effect of compression loads, including modulus of elasticity, ultimate compressive strength, and compressive yield strength. A compression test is typically conducted by placing the test sample in a compression testing machine and applying a constant force perpendicular to the sample until a preset deformation occurs. On the other hand, the tensile test measures the tension stress that can result in the cracking of the material, focusing on the yield strength, modulus of elasticity, and tensile strength. However, the shear test measures the resistance of the material to a specific force prior to the deformation or cracking of the test sample.
When To Do a Shear Test?
Shear testing should be conducted to assess the shear strength of a material before deciding the material type to be used in the application considering loading conditions. This will also help to determine the resistance of the material to stress or strain, which plays an important role in assessing the performance of the material.
How Long Does a Shear Test Take?
The duration of a shear test depends on the test type. For example, direct shear testing can take up to 24 hours for granular materials or three weeks for clay materials.
What Are the Materials Used in a Shear Test?
Materials used in a shear test fall into three major categories: layered composites, adhesives, and rigid substrates.
What Are the Advantages of the Shear Test?
The advantages of the shear test are given as:
- Researchers can determine the maximum load that a material can resist before cracking.
- It can be determined whether the material can meet the standards outlined by the regulations.
- The safety of a structure can be assessed reliably.
- The properties of a material can be determined by considering loading conditions.
- The joint strength of bonded surfaces and the durability of the applied adhesive can be thoroughly evaluated.
- The safety of the material can be assessed according to its features.
- The excessive stress level of a material can be measured before it fails.
- The material's response to the stress can be observed.
- Various types of shear tests are available for different materials and industries.
What Are the Disadvantages of the Shear Test?
The disadvantages of shear tests can be outlined as:
- Excessive shear stresses can cause damage to the material.
- Dimensions of the the test material must exactly match the dimensions indicated by the standards depending on the material type. For example, plastics should be 2-inch-square plates with a thickness of from 0.05 to 0.5 in. according to the ASTM D-732.
- Sample preparation requires strict compliance with industry standards for sample orientation, size, and shape.
- Standardized steps are followed independent of the test type.
- A one-size-fits-all approach is not available for shear testing since different materials require different tests.
- Failing to take safety precautions prior to the test may cause issues.
- Some tests may be expensive due to the equipment costs and test duration, which depend on the material and test conditions.
What Are the Types of Failures in Shear Tests?
The types of shear test failures include:
- Cohesive Failure: A cohesive failure occurs when the adhesive remains on the surface due to a fracture.
- Adhesive Failure: Adhesive failure occurs when surfaces can not bond properly due to dirt or roughness.
- Interfacial Failure: Interfacial failures may occur due to the presence of an element or hydrolysis at the interface.
- Mixed Mode Failure: Mixed mode failure is generally caused by interlaminar tension or shear stresses resulting from remote loadings applied to composite components.
- Ductile Failure: Ductile failure results from the plastic deformation of a material when the loading exceeds the yield strength of the material.
- Brittle Failure: Brittle failure occurs when a material experiences little to no plastic deformation.
- Localized Shear Failure: This failure can be seen in soft soils due to the lack of a well-defined loading.
Is It Hard To Conduct a Shear Test?
No, a shear test such as direct test or shear vane test can be conducted in a simple and straightforward way.
Is the Shear Test Dangerous?
No, shear tests are not dangerous. Yet, necessary precautions need to be taken prior to the testing such as maintaining a constant strain rate throughout a test and avoiding bubble formation during adhesive application to surfaces.
What Is the Difference Between the Shear Test and the Tensile Test?
The shear test focuses on the resistance of the material to the force. On the contrary, the tensile strength measures the force that is required to pull material to the point where it breaks. In both mechanical tests, the strength of a material can be determined.
How Xometry Can Help
This article presented shear tests, explained them, and discussed their importance and how they work. To learn more about shear testing, contact a Xometry representative.
Xometry provides a wide range of manufacturing capabilities and other value-added services for all of your prototyping and production needs. Visit our website to learn more or to request a free, no-obligation quote.
Disclaimer
The content appearing on this webpage is for informational purposes only. Xometry makes no representation or warranty of any kind, be it expressed or implied, as to the accuracy, completeness, or validity of the information. Any performance parameters, geometric tolerances, specific design features, quality and types of materials, or processes should not be inferred to represent what will be delivered by third-party suppliers or manufacturers through Xometry’s network. Buyers seeking quotes for parts are responsible for defining the specific requirements for those parts. Please refer to our terms and conditions for more information.
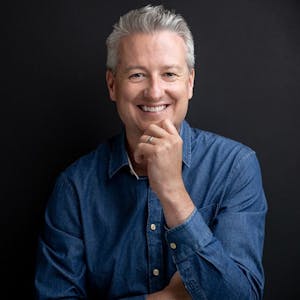