Spring testing is an important evaluation that springs undergo to test their properties and to ensure they adhere to certain quality standards. It is common for a spring to undergo a spring compression test, spring rate test, and spring fatigue test before a spring design or production batch is approved.
In this article, we explore what spring testing is, how to test coil springs, the different types of spring testing, the different mechanical properties that are evaluated, and much more.
What Is Spring Testing?
Spring testing is a method of evaluating the properties of springs to ensure they meet quality assurance requirements. Properties such as load capacity, fatigue strength, and spring rate are tested to ensure that springs perform according to their requirements and maintain that performance over their life span.
Why Is Spring Testing Important?
Spring testing is important to verify that springs can perform according to their requirements and avoid spring failure. Springs are common in almost all aspects of our daily lives in products such as machinery, vehicles, and appliances. Spring failures can lead to damaged equipment and safety risks. For example, a spring failure in industrial machinery can halt production, damage equipment, and potentially cause a machine to go out of control in such a way that workers are put at great risk.
Spring testing provides a way to verify that springs can withstand their rated loads, and maintain this performance over their life span. Unexpected spring failures can also be ruled out if springs are tested correctly. This minimizes the risk that a catastrophic spring failure occurs within the product or machinery.
What Are the Different Types of Springs Commonly Tested?
Several different types of springs are commonly tested. These are listed below:
- Compression Springs: Helical compression springs are the type of spring most commonly used, and can be found everywhere—from pens to car shock absorbers. These springs are made to withstand compressive force from opposing ends of the spring. These springs usually undergo spring compression testing.
- Tension Springs: Tension springs, or extension springs are designed to oppose an extending force. They are commonly used in many applications, such as trampoline springs, garage door assemblies, and gates. Tension springs usually undergo tensile testing, to determine the spring’s mechanical properties when subjected to axial tension.
- Torsion Springs: Torsion springs are made to withstand torsion and are commonly used on door hinges and levers. They are usually subjected to torsion testing to measure their resistance to twisting.
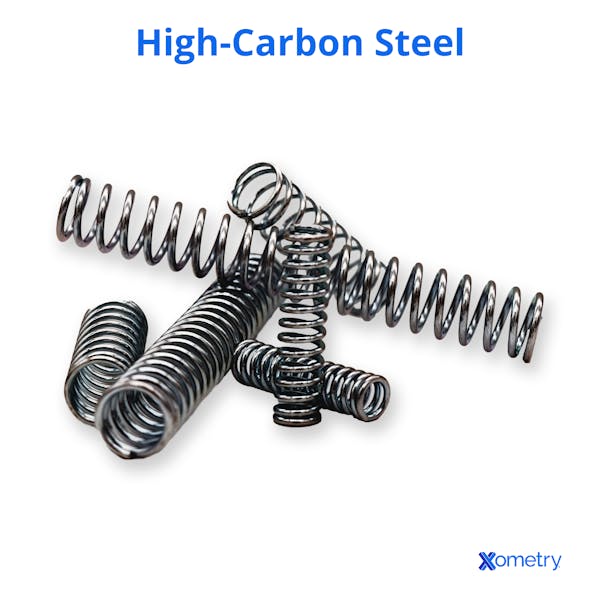
What Equipment Is Utilized for Spring Testing?
Different equipment is used for spring testing, depending on the type of spring being tested and the type of test required. Universal testing machines (UTMs) are a popular choice as they can be used for compression, tensile, and torsion testing. UTMs can be configured to accommodate different spring types and measure several parameters.
More specialized equipment is used to test specific properties, such as fatigue testing machines, torsion testing machines, and specialized spring testing machines that are made to test a specific type of spring. Visual inspection equipment, such as microscopes, is also used to inspect springs and look for signs of wear or other defects.
How Are the Mechanical Properties of Springs Evaluated?
The mechanical properties of springs are evaluated by a series of testing methods. For example, the following list shows how to test coil springs for their most important mechanical properties:
- To measure spring rate, or the stiffness of the spring, a spring is subjected to a compressive or tensile force, and the resulting load and deflection are recorded. The spring rate is then calculated as the change in load divided by the change in deflection.
- The solid height of a spring is the height at which the spring is fully compressed. This is usually determined during the compression test, as the test progresses until the spring reaches its solid height.
- Load capacity is the maximum load a spring can withstand before reaching its solid height. Load capacity is determined by compressing the spring until the solid height is reached. The load at that point is measured and represents the spring’s maximum load capacity.
- Fatigue testing is performed to evaluate a spring’s endurance and resistance to fatigue. This is usually tested by subjecting the spring to repeated cycles of compressive or tensile loading until it fails. The number of cycles a spring can withstand before failure is known as its fatigue life.
How is Test Setup and Method Development Carried Out?
The test setup and method development for spring testing varies, depending on the type of spring being tested, the type of test being carried out, and the specific machine performing the test. One of the most common types of spring testing is a compression test of a coil spring. In one test run, this testing method can test a variety of properties, including load capacity, spring rate, and solid height.
An example of the test setup and methodology for such a test is as follows:
- The test objectives are set out, in this case, to measure the spring rate, load capacity, and solid height of a spring.
- The specific spring testing machine or UTM is chosen to measure the target properties.
- Testing equipment and components are calibrated to ensure accurate measurements.
- The spring is prepared for testing. This involves cleaning the spring and inspecting it to ensure it is free from any visible defects or irregularities. The ends of the spring are also ground or squared to ensure that they can be mounted correctly during testing.
- The spring is mounted to the testing machine using clamps or mounting fixtures.
- The compression testing starts. The spring is gradually compressed at a controlled rate until it reaches its solid height, at which no further compression occurs. All the while the applied force and deflection of the spring are measured.
- Data is collected and exported for analysis. A load-deflection curve is generated using the data collected in the test.
- The spring rate is calculated by finding the slope of the linear portion of the load-deflection curve.
- Load capacity is identified as the load at which deflection stopped occurring.
- Solid height is identified by measuring the displacement at which deflection stopped occurring and the spring was fully compressed. This is the point at which all the coils are touching together.
What Is the Role of Universal Testing Machines in Spring Testing?
Universal testing machines (UTMs) play an important role in spring testing, as they can be used to perform several important tests on a wide variety of springs. A UTM is a test device used to test a material or object’s compression, torsion, and tensile strength. They are versatile machines that are designed to test virtually any material or object.
A UTM can be used to measure the most common mechanical properties of the most commonly used springs, eliminating the need to acquire specialized equipment for testing specific springs or specific properties. UTMs can measure properties, which include tensile strength, compression strength, and torsion strength, as well as perform bending and flexural testing, and load and deflection measurement, all of which are essential parts of spring testing.
What Factors Influence a Spring’s Mechanical Properties?
Several factors influence a spring’s mechanical properties, including:
- Material Selection: Carbon steel, stainless steel, as well as non-metallic materials such as plastics, are all common spring materials. They have vastly different properties, which contribute to the spring’s properties.
- Heat Treatment: Metallic springs generally undergo some sort of heat treatment process, which alters their mechanical properties. The specific heat treatment will affect the mechanical properties of the spring.
- Spring Type: There are numerous different types of springs, the most common of which are compression, extension, and torsion springs. The type of spring and its geometry has a significant impact on its mechanical properties.
- Wire Diameter: The diameter of the wire can have a significant impact on a spring’s stiffness, deflection characteristics, and load-bearing capacity.
- Number of Turns: The number of turns in a spring affects its spring rate or stiffness.
- Spring Pitch: The spring pitch, or distance between adjacent coils, affects the stiffness of the spring.
How Is Hooke’s Law Relevant in Spring Testing?
Hooke’s law states that the force needed to compress or extend a spring by a specific distance is proportional to the specific distance. This is usually expressed by the following equation:
F=kx
Where:
F = force that is applied to the spring
x = distance that the spring deflects
k = spring constant, or spring rate, which defines the stiffness of the spring
Hooke’s law describes the linear region of the load-deflection curve which is commonly measured in spring testing. The slope of this linear region represents the spring rate, which is another commonly measured parameter.
What Are the Standard Measurements Obtained From Spring Testing?
There are a few standard measurements obtained from spring testing. These are listed below:
- Maximum Load Capacity: The maximum load capacity is the maximum load that a spring can withstand before reaching its solid height, at which no further deflection occurs.
- Spring Rate: Spring rate is a measure of the stiffness of a spring. This measures how much force is required to produce a specific amount of deflection in the spring.
- Solid Height: The solid height is the height at which the spring is fully compressed, and all coils are in contact.
- Fatigue Life: Fatigue life is the number of compression cycles a spring can endure before failure.
- Load-Deflection Curve: The load-deflection curve is a graphical representation of how the load applied to the spring changes with its deflection or compression and helps visualize the spring’s behavior under different loads.
How Are the End-of-Test Criteria Established for Different Springs?
End-of-test criteria are dependent on a variety of factors such as the manufacturer of the spring, the material used in the spring, the targeted end use of the spring, and the type of spring. Usually, a predetermined load or deflection is chosen to end the test, but this needs to be adjusted for every spring.
One universal end-of-test measurement is the force rate of a spring. The force rate is calculated as:
Force Rate= k * Test Speed
Where k is the spring constant.
The force rate of a spring is nearly constant until solid height is reached. A universal end-of-test criteria is achieved by measuring the force rate at the beginning of a test, and checking when the force rate is double that of the initial measurement.
How Do International and Local Standards Compare in Spring Testing?
Both the International Organization for Standardization (ISO) and ASTM International have published standards for spring testing, which are accepted internationally. These standards offer guidance in spring design and testing methodologies. Local standards will usually be more specific to the needs and practices of local industry. They may target specific operations or materials that are common to the local country or region.
What Are the Common Standards Followed in Spring Testing?
The following standards are common in spring testing:
- BS 1726: Defines a standard set of tests for testing compression, extension, and torsion springs.
- DIN 2192: Sets out requirements and testing standards for flat springs.
- JIS B 2704: Defines requirements and testing methods for helical compression springs and helical extension springs.
- ASTM A125: Defines a test method for helical heat-treated steel compression springs and is regarded as the best testing procedure for these types of springs. ASTM A125 covers a range of properties that compression springs must adhere to, and there are many spring testing companies and spring testing equipment manufacturers that specifically target this standard.
- ISO 2860: This standard relates to helix-based springs, providing guidelines on the testing and classification of helical springs.
Why Is Dynamic Testing Different From Static Spring Testing?
With static testing, a spring is subjected to a constant force throughout the test, whereas with dynamic testing, the spring is subjected to forces that vary in magnitude and direction throughout the test. Static testing is useful for measuring the mechanical properties of a spring, but in most cases, dynamic testing provides a more accurate picture of what a spring will face during actual use. Therefore, dynamic testing is very important and useful for testing a spring’s real-world performance and measuring resistance to fatigue.
How Do Manufacturers Ensure Consistency and Quality in Spring Production Through Testing?
Manufacturers ensure consistency and quality in spring production by using the data from spring testing to identify potential flaws or inconsistencies in batches of springs, or particular springs themselves. Spring testing can reveal many potential deficiencies, such as inferior material quality, design flaws, and quality-control issues.
Testing in the prototyping stage can ensure that the design of a spring adheres to the relevant requirements and standards. Testing random samples in a production batch can act as quality control for both the production process and the material used in manufacturing.
What Are the Challenges in Spring Testing?
Spring testing presents several challenges, such as:
- There is a large number of spring designs, which makes it difficult to design testing methods and fixtures that can accommodate all types of springs. There are universal testing machines and spring testing standards that go some way toward ensuring different types of springs are tested properly.
- Fatigue testing is a very important test, but can be very time-consuming, as it involves subjecting the spring to a large number of testing cycles to determine its endurance. Automated testing machinery helps with this, as the tests can be run without human intervention or supervision.
- The calibration of testing equipment is incredibly important, as is the quality of the components used in the testing equipment. Any wear in the testing components or incorrect calibration can lead to inconsistent results. Regular maintenance and calibration are required to ensure that testing equipment remains accurate and up to standard.
- Large or heavy springs require specialized equipment and handling to test and are subject to extremely high loads, which may present safety risks. Extra safety precautions need to be undertaken when testing heavy springs, and specialized equipment needs to be used to ensure these springs are tested safely. Outsourcing to a specialized testing company might also be a suitable option if the specialized equipment is not an option.
- The properties of springs can behave non-linearly, which can be very difficult to measure accurately. Specialized software and automated measuring techniques can help capture such non-linear properties more precisely.
How Is Data From Spring Testing Interpreted and Applied?
Data from spring testing provides valuable insights into the performance characteristics of springs. It is very important in all aspects of spring design and manufacture. Mechanical properties such as the spring rate and maximum load capacity are essential parameters to consider when validating the design of a spring.
Usually, after a prototype of a spring is made, it is put through testing to verify its mechanical properties and ensure it meets requirements. The data gained from spring testing helps spring designers iterate on their prototypes to produce a spring that meets performance thresholds. The data gained from this testing will ultimately form part of the specifications of the spring and will be used by anyone choosing a spring to use in the manufacture of a product.
What Future Innovations Are Expected in Spring Testing Techniques?
Spring testing is a growing field, and there are several future innovations expected. Automation has been a part of spring testing for a while, but the demand for automated testing systems is growing. Automated testing systems minimize human error, and make spring testing much more efficient. It is expected that the prevalence and quality of automated testing systems will grow.
There is also a lot of focus on digital spring testing technologies, like advanced sensors and control systems, which improve the accuracy of spring testing. Artificial intelligence (AI) is expected to play a larger role in spring testing, particularly in the analysis of spring testing data.
Is Compression Part of Spring Testing?
Yes, compression is a common part of spring testing. It is very important for determining properties such as the spring rate, maximum load capacity, and solid height of a spring. In spring compression testing, a spring is flattened to a known percentage of its height, and a load reading is taken. This is repeated for several percentages to calculate the spring rate.
Summary
This article presented spring testing, explained it, and discussed its importance. To learn more about spring testing, contact a Xometry representative.
Xometry provides a wide range of manufacturing capabilities and other value-added services for all of your prototyping and production needs. Visit our website to learn more or to request a free, no-obligation quote.
Disclaimer
The content appearing on this webpage is for informational purposes only. Xometry makes no representation or warranty of any kind, be it expressed or implied, as to the accuracy, completeness, or validity of the information. Any performance parameters, geometric tolerances, specific design features, quality and types of materials, or processes should not be inferred to represent what will be delivered by third-party suppliers or manufacturers through Xometry’s network. Buyers seeking quotes for parts are responsible for defining the specific requirements for those parts. Please refer to our terms and conditions for more information.
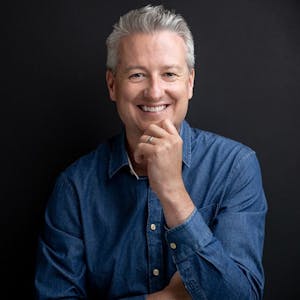