Steel microstructure refers to the arrangement of atomic and crystalline features within steel. It is crucial because it directly influences steel's mechanical properties, such as strength, hardness, and ductility. Understanding steel microstructure is essential for designing materials with specific performance attributes and ensuring the safety and reliability of applications ranging from buildings and bridges to machinery and vehicles.
This article will discuss the definition, properties, and factors involved in determining the microstructure and phases of steel.
What Is Steel Microstructure?
The microstructure of steel refers to the arrangement and distribution of phases composed of iron and alloying elements. These phases vary in structure and properties based on composition, heat treatment, and processing methods. This microstructure governs the steel's chemical and physical behavior and reflects its processing history.
Are Steel Microstructure and Cast Steel the Same?
No, steel microstructure and cast steel are not the same. Steel microstructure, previously defined, refers to the microscopic arrangement of phases in steel. This arrangement influences properties like strength and hardness. By adjusting the microstructure through heat treatment, steel can be tailored for specific applications.
Cast steel, on the other hand, is a type of steel made by casting. The process involves melting steel and pouring it into molds to create shapes. These shapes can have different microstructures depending on how they are made. Cast steel is used to create various things, from car parts to machinery.
What Is the Importance of Steel Microstructure?
Steel microstructure is one of the primary factors determining mechanical properties like strength, hardness, ductility, and toughness. This means that the material’s performance depends on the distribution, shape, and size of the phases within the microstructure. The microstructure of steel can have different appearances, which are influenced by parameters like rolling setup, alloying elements, cooling rates, heat treatments, and post-treatments of the steel.
Engineers can tailor steel for specific applications by understanding and controlling its microstructure. Heat treatment processes are employed to modify the microstructure, enhancing properties like hardness and toughness. Additionally, microstructure affects weldability, corrosion resistance, formability, and durability of steel components. It plays an important role in quality control, ensuring that steel products meet performance standards.
What Determines Steel Microstructure?
Steel microstructure is influenced by alloying elements, cooling rate, mechanical processing (e.g., rolling, forging, extrusion), heat treatments, and post-processing steps. Alloying elements, such as carbon, manganese, and chromium, significantly influence microstructure by dictating the types and proportions of phases that form within the steel. The cooling rate during fabrication and heat treatment also plays an important role; rapid cooling can transform austenite into the hard martensite phase, while slower cooling permits the development of phases like pearlite and bainite. Mechanical processes like rolling, forging, and extrusion deform the steel, affecting grain size and uniformity, which in turn impact strength and ductility. Heat treatments, like annealing and tempering, offer precise control over the microstructure to enhance desired properties. Subsequent post-processing treatments, including cold working and precipitation hardening, further refine the microstructure.
What Are the Properties of Steel Microstructure?
Steel’s atomic arrangement determines key properties and behavior, depending on which phases are present and how they’re distributed. This microstructure can be visualized as a lattice of iron atoms, much like stacked billiard balls. When carbon is added to iron, it forms various phases within the microstructure, each with distinct properties. For example, ferrite, which has a body-centered cubic (BCC) crystal structure, is soft and ductile. Austenite, with a face-centered cubic (FCC) structure, can hold more carbon and is stable at high temperatures. However, when steel cools, austenite can transform into harder phases like martensite, which has a body-centered tetragonal (BCT) structure. Heat treatments can further modify the microstructure, impacting steel's hardness and toughness.
What Is the ASTM Standard for Steel Microstructure?
There is no single ASTM standard that defines all aspects of steel microstructure, but several ASTM standards provide detailed methods for microstructural evaluation and analysis. Instead, ASTM provides various standards related to the testing and characterization of steel microstructures. These standards cover techniques and procedures for examining and analyzing steel microstructures. Some relevant ASTM standards include:
- ASTM E3: Covers the preparation of metallographic specimens, including steel, for microscopic examination. It outlines techniques for sectioning, mounting, grinding, polishing, and etching of specimens to reveal their microstructures.
- ASTM E112: Defines standard test methods for determining average grain size in metals, including steel, using comparison and planimetric methods under a microscope.
- ASTM A923: Provides procedures for examining the microstructure of steel and alloy samples to detect the presence of harmful intermetallic phases, such as the sigma phase, which can affect material properties.
- ASTM A1084: Provides a standard test method for detecting detrimental intermetallic phases in lean duplex stainless steels through metallographic examination and impact testing.
- ASTM A892-09: Outlines the process for defining and rating the microstructure of carbide structures found in annealed high-carbon bearing steels. It includes specifications for the optical metallography equipment and specimen preparation, which encompasses procedures like polishing and etching. This standard is crucial for ensuring the quality and performance of high-carbon-bearing steels used in various applications.
What Does the Steel Phase Diagram Look Like?
The iron-carbon phase diagram shows the relationship between temperature (Y-axis) and carbon content (X-axis), illustrating how different microstructures form in iron-carbon alloys at various compositions and temperatures. Each region or phase field within the phase diagram signifies the phases present for a specific alloy composition and temperature.
In this diagram, carbon acts as an interstitial element within the iron lattice, which can adopt either a body-centered cubic (BCC) or face-centered cubic (FCC) structure depending on temperature, leading to the formation of different phases. The main phases represented in the diagram include α-ferrite (BCC), γ-austenite (FCC), δ-ferrite (high-temperature BCC), and Fe₃C (cementite), a hard, brittle iron carbide.
What Are the Main Phases in Steel Microstructure?
The behavior of steel, from its soft and ductile form to its hardest phases, is influenced by the interplay between carbon content, temperature, and cooling rates. Listed below are the different phase structures of steel microstructure:
1. Ferrite
When a minute fraction of interstices houses carbon atoms, the resulting microstructure is ferrite. Ferrite has a body-centered cubic (BCC) structure, making it soft and ductile, similar to pure iron. The maximum carbon solubility in ferrite is approximately 0.02% at 912°C and about 0.008% at room temperature.
2. Martensite
Rapid cooling, typically faster than 20–30°C per second, traps carbon atoms within the distorted body-centered tetragonal (BCT) lattice of martensite. Higher carbon levels result in harder martensite. When heated, martensite allows carbon to diffuse out, reducing hardness and increasing toughness.
Heating martensite leads to tempered martensite, which combines ferrite and iron carbide (Fe3C). This microstructure disperses Fe3C more evenly than pearlite, reducing compression stresses.
3. Austenite
Austenite has larger gaps than ferrite, with a face-centered cubic (FCC) crystal structure. At temperatures above 1,000°C, austenite can dissolve up to approximately 2.1% carbon. However, it's unstable at temperatures below the eutectic point (727°C) unless rapidly cooled. Austenite is non-magnetic.
Some austenite doesn't transform into martensite during quenching, creating retained austenite. Its presence depends on factors like carbon content and alloying. For example, austenitic stainless steels like 304 and 316 maintain their austenitic structure at room temperature.
4. Cementite
Cementite, also known as iron carbide (Fe3C), is a hard and brittle compound that forms in steel when excess carbon is present. It has a fixed composition and is often used to strengthen steel. Cementite typically appears as small, hard particles in the microstructure.
5. Bainite
Bainite, formed at intermediate cooling rates (between those for pearlite and martensite), consists of ferrite and fine carbide particles. In some cases, especially in lower bainite, retained austenite may also be present. The rounded hard components in bainite make it more resistant to crack initiation and propagation than flat, elongated structures like pearlite. This balance of strength and ductility makes bainitic steels suitable for applications like automotive wheels and suspension arms.
6. Pearlite
Pearlite forms during slow cooling of austenite and consists of alternating lamellae of ferrite and cementite (Fe₃C). The amount of cementite depends on the carbon content. Unlike ferrite, cementite is hard, brittle, and less resistant to cracks. It forms a lamellar structure, resembling mother-of-pearl (nacre) under a microscope.
What Is the Strongest Steel Microstructure?
Martensite is the hardest and strongest common steel microstructure, but is also brittle in its untempered state. It derives its strength from its unique crystal structure and the way it forms. Martensite has a body-centered tetragonal (BCT) crystal structure, which results from the rapid cooling or quenching of austenite, another steel microstructure. During this rapid cooling, carbon atoms are trapped in the crystal structure, creating internal stresses that make martensite exceptionally hard and brittle.
What Is the Weakest Steel Microstructure?
Ferrite is considered the softest common steel microstructure due to its low carbon solubility and simple BCC structure, making it highly ductile but low in strength. Ferrite has a body-centered cubic (BCC) crystal structure, which gives it lower hardness and strength compared to microstructures like martensite, which have a more complex crystal structure and higher hardness. This lower hardness and strength make ferrite less suitable for applications in which high strength and hardness are required. However, ferrite's softness and ductility can be advantageous in applications in which toughness and formability are more important than hardness and strength.
How Do Atomic Mechanisms of Transformation Affect Steel Microstructure?
The atomic mechanisms of solid-state phase transformations in steel are critical in determining the resulting microstructure, morphology, and chemical composition. These mechanisms define how atoms move and rearrange during phase transformations, ultimately shaping the material's properties. Two fundamental atomic mechanisms of transformation in steel are displacive (also called diffusionless) and reconstructive (diffusional) mechanisms. In the displacive mechanism, the crystal structure changes via a coordinated shift of atoms without long-range diffusion. This leads to significant strain energy and rapid transformation, typical of martensitic transformations.
Conversely, the reconstructive mechanism involves atomic diffusion, where atoms move over longer distances, breaking and reforming bonds to form new crystal structures (e.g., transformation of austenite into ferrite or pearlite). This mechanism requires atoms to diffuse over distances comparable to the size of the transformation product.
Displacive transformations typically result in plate-shaped products, while reconstructive transformations are characterized by changes in chemical composition and a range of product shapes.
What Are the Heat Treatments for Steel Microstructure?
The heat treatments for steel microstructure are:
1. Annealing
With annealing, the steel is heated to a specific temperature (typically below the eutectoid point for hypoeutectoid steels) and held there before slow cooling, usually in a furnace. This method alleviates internal stresses, refines the grain structure, and improves the steel’s softness and ductility. It is fre
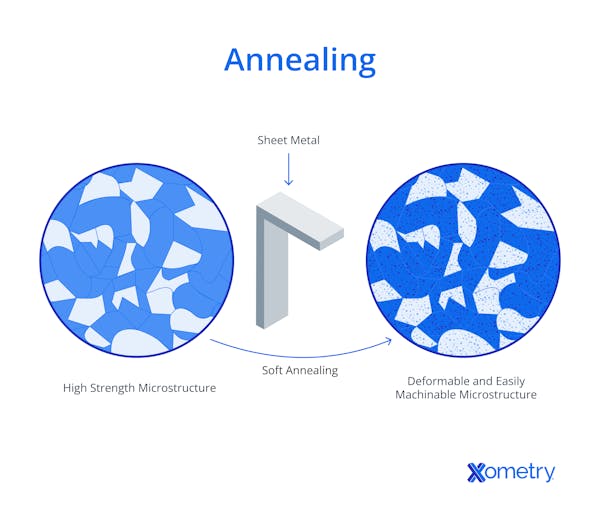
2. Tempering
Performed after quenching, tempering reheats the steel to a temperature below its critical point to reduce brittleness, improve toughness, and relieve internal stresses. The precise temperature and duration for tempering can be customized to attain the preferred balance between toughness and hardness.
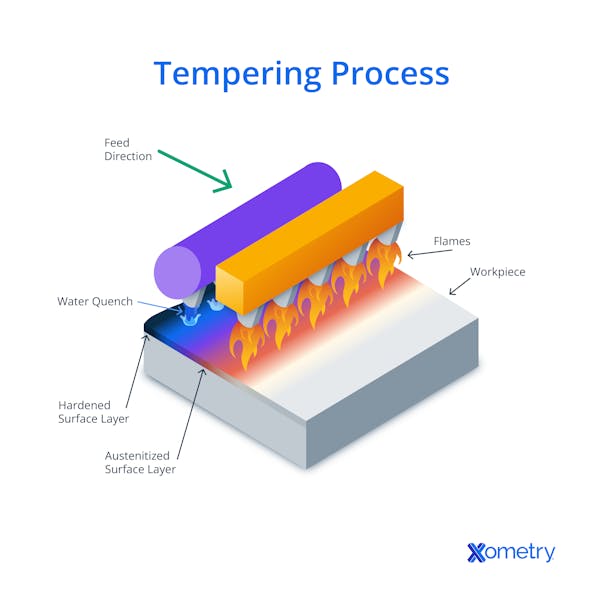
3. Hardening
Hardening involves heating the steel to its austenitizing temperature (above the critical point) and then rapidly cooling it in a quenching medium such as oil, water, or polymer solutions. This rapid cooling locks the steel's microstructure in a hardened state, increasing both hardness and strength. However, it also makes the steel more brittle, so tempering is often performed afterward to restore some toughness.
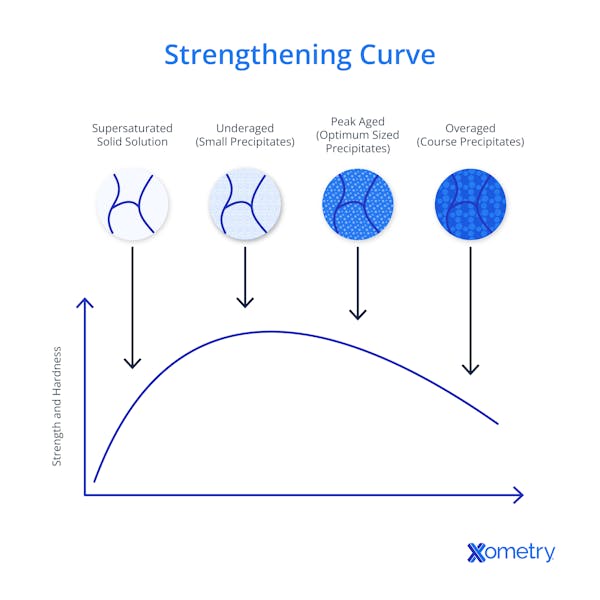
4. Normalizing
Normalizing is a heat treatment used to refine the grain structure of the steel and improve its mechanical properties. It involves heating the steel to a temperature slightly above its critical point and then allowing it to cool in still air. Normalizing eliminates internal stresses, improves machinability, and enhances the steel's uniformity and strength.
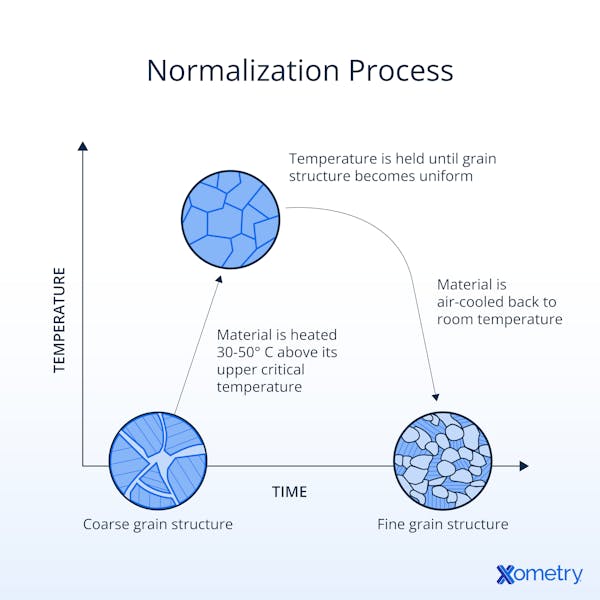
What Is the Advantage of Steel Microstructure?
Steel microstructures offer a wide range of advantages, including exceptional strength, durability, and versatility. Steel can be tailored to meet specific requirements through precise control of its microstructure. This results in steel grades that can be made suitable for everything from structural applications to cutting tools. Certain steel microstructures, especially those with high alloy content, offer good heat and fire resistance, making them suitable for high-temperature environments. Additionally, steel is readily available and cost-effective, making it a preferred choice for many engineering and construction projects.
What Is the Disadvantage of Steel Microstructure?
Some steel microstructures present disadvantages that must be considered. One significant drawback is susceptibility to corrosion in certain environments, which can compromise steel’s structural integrity over time. Some steel microstructures, especially untempered martensite with high carbon content, can be brittle, limiting their use in applications requiring toughness. In general, the relatively high density of steel can be a disadvantage in weight-sensitive industries like aerospace, where lighter alternatives like aluminum or titanium are often preferred. Additionally, the production of steel can have a significant environmental impact due to energy consumption and greenhouse gas emissions. Complex heat treatment processes may be required to achieve desired properties, adding to production costs. Despite these disadvantages, the adaptability and extensive range of steel microstructures continue to make it a material of choice across numerous applications.
What Is the Difference Between Cast Iron and Steel Microstructure?
The main difference between the microstructures of cast iron and cast steel lies in their carbon content. Cast iron typically contains more than 2% carbon, while cast steel typically contains between 0.1–0.6% carbon, depending on the grade. This carbon content significantly affects their properties and characteristics.
Cast iron is known for its relatively high carbon content, which makes it easier to cast due to its better flowability and lower shrinkage during cooling. It has excellent vibration-damping properties, making it ideal for applications like engine blocks, in which reducing vibration is crucial. It also exhibits good compressive strength, making it suitable for parts subjected to high compressive forces. However, cast iron lacks impact resistance and can be brittle, limiting its range of applications.
On the other hand, cast steel contains lower carbon content, which makes it more challenging to cast compared to cast iron. Steel has excellent impact resistance, allowing it to withstand sudden impacts without deforming or breaking. This makes steel ideal for applications in which toughness is essential. While steel may be more challenging to machine, it offers a good balance of strength and ductility, making it widely used in various mechanical and structural applications.
Summary
This article defined steel microstructure and discussed its phases, properties, and influencing factors. To learn more about steel microstructure, contact an Xometry representative.
Xometry provides a wide range of manufacturing capabilities and other value-added services for all of your prototyping and production needs. Visit our website to learn more or to request a free, no-obligation quote.
Disclaimer
The content appearing on this webpage is for informational purposes only. Xometry makes no representation or warranty of any kind, be it expressed or implied, as to the accuracy, completeness, or validity of the information. Any performance parameters, geometric tolerances, specific design features, quality and types of materials, or processes should not be inferred to represent what will be delivered by third-party suppliers or manufacturers through Xometry’s network. Buyers seeking quotes for parts are responsible for defining the specific requirements for those parts. Please refer to our terms and conditions for more information.
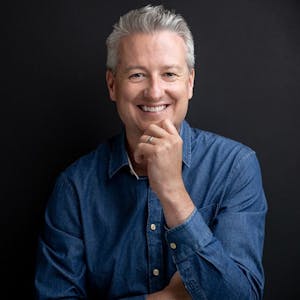