Manufacturing materials put up with a lot of different stresses—the engineering kind, that is. From tensile to compressive to shear stress and many more in between, they show the strength of materials and their point of deformity. But it’s how they react to these forces that matters to designers, manufacturers, and engineers who are aiming to create products and structures that can handle these forces in real-life scenarios. Two such examples of stresses that are important for determining what materials to use are tensile stress and compressive stress, which we’ll explore the differences between.
What Is Tensile Stress?
Tensile stress is all about elongation, and it describes when an applied force stretches the length of a material along the axis of the force. If you’re working with a formula, you can represent tensile stress through this:
stress = F/A
Measurements for this type of stress, and most other kinds, are usually expressed through Pascals (Pa) or through pounds per square inch (psi). While tensile elongates, it’s helpful to see how it compares to compressive and shear forces, too, which you can see in the diagrams below.
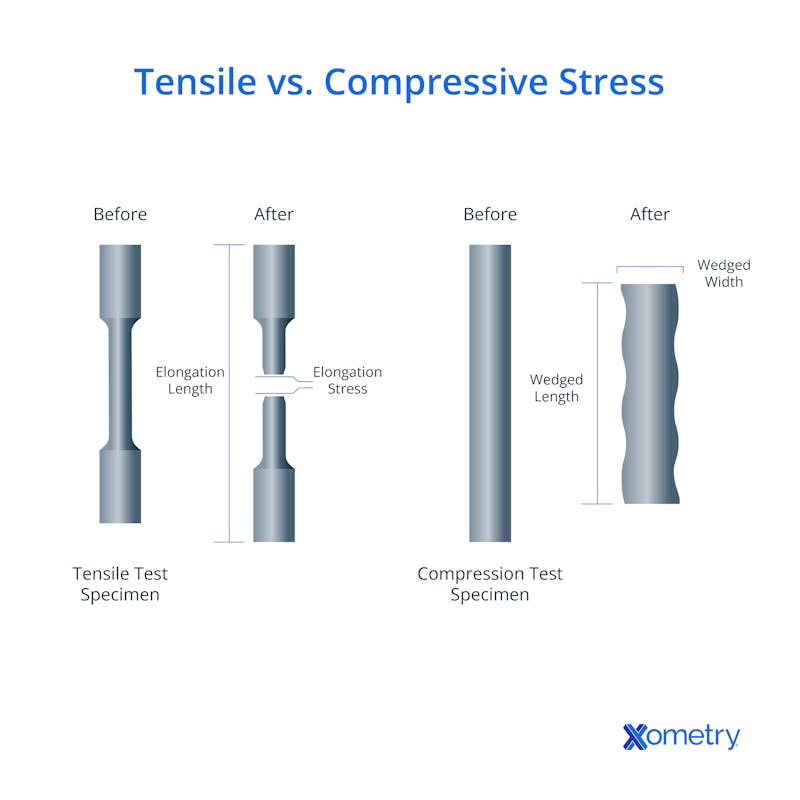
Examples of Tensile Stress
There are tons of examples that exist in the real world of tensile stress and how it looks. We’ve listed a few to give you a good idea of how it appears:
- Pulling a rubber band apart
- Two people pulling opposite ends a rope away from each other
- A crane cable that’s holding something suspended in the air
- Cables on a suspension bridge while vehicles pass over it
What Is Compressive Stress?
This type of stress could be viewed as the reverse of tensile stress. Rather than elongating a material, compressive stress makes it become more compact, exactly as its name states. It’s also expressed in Pascals or pounds per square inch and it, too, deforms and dislocates the material as force is applied.
Examples of Compressive Stress
There are plenty of examples of this type of stress, too, many of which you’ll come across in everyday life:
- Concrete slabs as flooring in buildings or as sidewalks that deform as people, animals, and machines walk and roll over them.
- Structural columns in buildings that support the weight of every floor
- Furniture items like chairs and couches which compress under the weight of people on top
The image below shows a visual comparison of before and after testing and how tensile stress impacts a material versus how compressive stress affects it.
[IMAGE]
Comparing These Stress Types
The main difference between tensile stress and compressive stress is the type of force applied and how the material deforms as a response. With tensile stress, the force stretches and elongates the material, whereas compressive stress presses it together and makes the material more compact.
Although they’re different and basically opposite in nature, they can still happen at the same time. It may sound impossible, but it’s a common occurrence in materials and objects that bend. For example, if you bend a pencil until it breaks, you can see both of these stresses in action. As the pencil bends into a U-shape, you can witness compressive stress in the upper portion of the U and tensile stress in the bottom area.
How Xometry Can Help
Whether you’re working with objects made of materials that are frequently exposed to compressive stress or tensile stress, our instant service quotes can help you find the right process, from 3D printing to CNC machining.
Disclaimer
The content appearing on this webpage is for informational purposes only. Xometry makes no representation or warranty of any kind, be it expressed or implied, as to the accuracy, completeness, or validity of the information. Any performance parameters, geometric tolerances, specific design features, quality and types of materials, or processes should not be inferred to represent what will be delivered by third-party suppliers or manufacturers through Xometry’s network. Buyers seeking quotes for parts are responsible for defining the specific requirements for those parts. Please refer to our terms and conditions for more information.
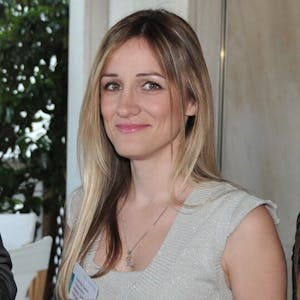