Tin bronzes are important alloys that are mainly composed of 87% copper and 8–12.5% tin, along with other elements including phosphorus and zinc. Phosphorus improves wear resistance, hardness, and fatigue resistance. MTEK Navy G 1% Lead (C92300) and MTEK Tin Bronze (C90500) are two notable varieties.
The extraordinary qualities of this alloy family make them highly desirable for a variety of uses. The fact that they are widely used in gears, bushings, and bearings demonstrates their versatility.
This article will dig deeper into the composition, characteristics, and uses of tin bronzes.
What Is Tin Bronze?
Tin bronzes are copper alloys primarily composed of copper and tin, with other alloying elements such as phosphorus and zinc for enhanced properties. Tin bronzes are known for their improved hardness compared to pure copper, fatigue resistance, and wear resistance. The "tin" in "tin bronze" refers to the major alloying element in traditional bronze. When combined with copper, tin imparts desirable mechanical and physical characteristics to the alloy, making it valuable in various applications.
What Is the History of Tin Bronze?
The earliest known usage of tin as an alloying element in copper to make a new metal, bronze, was in the Mesopotamian city of Ur, which is located in modern-day Iraq. Tin bronze has a long history reaching back to 3500 BC. The Sumerians were the first to combine copper and tin to make objects (principally weapons) from what we now call “bronze.” These early uses signaled the start of tin bronze's historical significance, even though the identities of the specific discoverers are unknown.
What Is the Other Term for Tin Bronze?
Tin bronze is alternatively known as "phosphor bronze." This designation stems from the alloy's incorporation of a small amount (0.01–0.45%) of phosphorus, which serves as a deoxidizer during casting and increases the corrosion resistance, strength, and wear resistance.
What Is Tin Bronze Made Of?
The main constituents of tin bronze are 87% copper and 8–12.5% tin. Hardness, strength, corrosion resistance, fatigue resistance, and wear resistance are all improved by adding small amounts of phosphorus (0.01% to 0.45%). Chemistries are changed, such as by adding lead, to enhance machinability and pressure tightness. Owing to its resilience to wear and corrosion in harsh conditions, it finds extensive use in maritime applications, bearings, bushings, and other machinery parts.
How Are Tin Bronzes Made?
Tin bronzes, alloys of copper and tin, are produced by incorporating cassiterite (an ore-rich tin oxide, SnO2) into molten metallic copper. In a controlled process, this recipe would yield approximately 55 grams of metallic copper, melted at 1090 °C. Subsequently, 5 grams of cassiterite, along with charcoal, are introduced into the crucible. This addition facilitates the extraction of tin from the ore and its amalgamation with copper. The resulting alloy exhibits enhanced strength, corrosion resistance, and a distinctive bronze hue.
Melted bronze is continuously cast by putting it into a crucible fitted with a water-cooled die and measuring the diameter of the finished result by gradually withdrawing it using a roller mechanism. Once a particular block or billet is started, wrought bronze is usually formed using rolling, extrusion, or forging mills. Melting bronze into hollow molds is the method used in bronze casting processes (lost wax, ceramic shell, sand casting) to manufacture a variety of artifacts, including: instruments, medals, and sculptures.
Can Tin Be Turned Into Bronze?
No, tin cannot be turned into bronze. However, tin can be added to copper to make the alloy known as bronze.
What Are the Characteristics of Tin Bronze?
The characteristics of the tin bronzes include:
- Good Wear Resistance: The alloy resists wear effectively, ensuring longevity and reliability in applications subjected to friction and abrasion.
- High Load-Carrying Capacity: Tin bronze has a relatively high yield and tensile strength, making it suitable for applications in which materials must endure significant levels of stress or pressure. The cored dendritic microstructure of cast tin bronzes, featuring a composition gradient with increasing tin content in growing dendrites, contributes to enhanced mechanical properties.
- High Ductility: The alloy can withstand substantial plastic deformation before breaking because of its high ductility. Its formability and malleability are facilitated by this attribute.
- Corrosion Resistance in Seawater and Brines: Tin bronze is useful in corrosive and marine conditions because of its good resistance to corrosion in saltwater and brines.
- Good Impact Resistance: Tin bronze can endure impact forces, making it suitable for applications in which impact resistance is important.
How Does Tin Bronze Differ From Other Types of Bronze?
Tin bronze differs from other types of bronzes because it has a large proportion of tin in its composition. On the other hand, silicon bronze has 2.8–4% silicon, while aluminum bronze contains 9–14% aluminum and 4% iron. Tin bronze performs exceptionally well against corrosion, while aluminum bronze outperforms it in terms of strength and wear resistance.
To learn more, see our full guide on the 9 Different Types of Bronze.
What Is the Color of Tin Bronze?
Tin bronze exhibits a metallic brown color. The exact shade is a result of the ratio of copper to tin. This distinctive hue enhances its aesthetic appeal and makes it recognizable in various applications. Bronzes with greater levels of tin have lighter shades. Aluminum, manganese, and nickel additives influence the final product's color when mixed with the original alloy in metal manufacturing.
What Does Tin Bronze Look Like?
Tin bronze has a warm, reddish-brown appearance, with the exact hue depending on the proportions of copper and tin in the alloy, and how much of a patina (tightly adherent oxide layer) it has developed.
What Are the Physical Properties of Tin Bronzes?
Table 1 highlights the physical properties of two typical tin bronzes:
Property | C90200 Tin Bronze | C90300 Tin Bronze |
---|---|---|
Property Density | C90200 Tin Bronze 0.318 lb/cu in. at 20 °C | C90300 Tin Bronze 0.318 lb/cu in. at 20 °C |
Property Hardness, Brinell | C90200 Tin Bronze Brinell Hardness of 70 with a 500 kg | C90300 Tin Bronze Brinell Hardness of 70 with a 500 kg |
Property Tensile strength | C90200 Tin Bronze 262 MPa | C90300 Tin Bronze 310 MPa |
Property Electrical conductivity | C90200 Tin Bronze 13% IACS at 20 °C | C90300 Tin Bronze 12% IACS at 20 °C |
Property Melting point solidus | C90200 Tin Bronze 876 °C | C90300 Tin Bronze 854 °C |
Property Melting point liquidus | C90200 Tin Bronze 1046 °C | C90300 Tin Bronze 1000 °C |
Property Specific Heat Capacity | C90200 Tin Bronze 0.09 Btu/lb/°F at 20 °C | C90300 Tin Bronze 0.09 Btu/lb/°F at 20 °C |
Property Thermal Conductivity | C90200 Tin Bronze 36 Btu/sq ft/ft hr/°F at 20 °C | C90300 Tin Bronze 43.2 Btu/sq ft/ft hr/°F at 20 °C |
Is Tin Bronze Harder Than Brass?
Yes, generally, tin bronze is harder than brass. The hardness of an alloy depends on its composition. Tin bronze, consisting of copper and tin, tends to have a higher hardness due to the addition of tin. Brass, composed of copper and zinc, is generally softer. The difference in strength between the two alloy types is a result of how their atoms interact, creating the hardness/strength disparity and, therefore, distinct mechanical properties. Hardness is an outcome, not a cause.
To learn more, see our full guide on Brass Alloys.
Is Tin Bronze Brittle?
Yes, tin bronze can become brittle with a higher tin composition (~15%). Elevating tin content in sand-cast tin bronze alters mechanical properties. Up to 15%, bronze remains a single-phase alloy. At higher tin contents, other, brittle phases can also form, particularly in the interdendritic spaces in cast microstructures. These brittle phases then lower the overall ductility.
What Are the Chemical Properties of Tin Bronze?
Table 2 below highlights the chemical properties of tin bronze:
Property | Description |
---|---|
Property Oxidation | Description Upon exposure to air, tin bronze forms an outer layer of copper oxide, which eventually becomes copper carbonate. This protective patina prevents further corrosion. |
Property Seawater Corrosion | Description Tin bronze exhibits strong resistance to seawater corrosion, similar to copper and brass, but can succumb to "bronze disease" if chlorides are present. |
Property Atmospheric Pollutants | Description Reacts with sulfur compounds in the atmosphere, leading to the formation of light green patches, especially in urban and industrial areas. These patches are often identified as patina, a layer formed on the metal surface due to oxidation and environmental exposure. |
Property Animal Droppings | Description Bird or animal droppings, being acidic, can accelerate localized corrosion on bronze surfaces. |
What Are the Applications of Tin Bronze?
Some of the applications of tin bronzes include:
1. Piston Rings
Tin bronze is often used in the manufacturing of industrial hardware, including piston rings. It is valued for its combination of strength, corrosion resistance, and wear resistance, making it suitable for applications where durability and performance under mechanical stress are crucial, such as in the functioning of piston rings within engines.
2. Impellers
Impellers, the rotating components in pumps or turbines, demand materials with high corrosion resistance. Tin bronze's resistance to corrosive environments makes it useful for fluid-handling system impellers.
3. Steam Fittings
Steam fittings, crucial components connecting steam pipes, require materials that can withstand high temperatures and resist steam-induced corrosion. Tin bronze is employed in steam fittings for its resistance to steam and heat. This application ensures the longevity and reliability of steam systems, as tin bronze maintains its structural integrity even under elevated temperatures. For example, the operating temperature range of a C90300 tin bronze steam fitting is -268–659 °C (-450–1200 °F).
4. Valve Components
Tin bronze's resistance to corrosion is advantageous for valve components, which manage fluid flow in different kinds of systems. Tin bronze is the material of choice for valves in machinery or systems used in manufacturing plants, refineries, power plants, or any other industrial facility where the control of fluid flow is essential because of its long-term corrosion resistance. By extending the life and reliability of valves, this application reduces maintenance requirements and provides reliable operation.
5. Seal Rings
Seal rings, crucial for effective sealing in a variety of applications, benefit from the unique properties of tin bronze. Its self-lubricating characteristics and resistance to wear make tin bronze an ideal material for sealing rings for certain applications. This application not only reduces friction but also extends the lifespan of seal components, contributing to a reliable seal.
6. Bushings
Good lubricity and load-bearing capability are necessary for materials used in bushings, which are cylindrical parts that support rotating shafts. Tin bronze, which has the qualities needed to reduce friction and improve wear resistance, is often used for bushings. This application of tin bronze helps mechanical assemblies last longer by assuring smooth and reliable performance over extended periods.
What Are the Advantages of Tin Bronze?
Some of the advantages of using tin bronzes include:
- Exhibits excellent corrosion resistance, making them suitable for applications in harsh environments, including marine settings.
- Have good machinability, allowing them to be economically shaped into a variety of components and parts.
- Have anti-friction characteristics, reducing wear and tear in components like bearings, making them ideal for use in machinery.
- Offers a balance of strength and ductility to obtain desired durability, ensuring longevity in structural applications.
- Is well-suited for casting due to its favorable combination of properties, including: high fluidity when molten, good castability, and excellent detail reproduction.
What Are the Disadvantages of Tin Bronze?
Tin bronzes have several disadvantages such as:
- Bronze cores cannot be used when casting in bronze because the high casting temperatures would cause them to melt. Thus, to survive the casting process and preserve the integrity of the finished product, all core materials must be non-bronze substances.
- Are costlier than brass and steel, primarily due to their high copper content.
- The presence of chlorides can lead to bronze disease, causing green spots and eventual deterioration.
- Is susceptible to corrosion by ammonia, ferric compounds, and cyanides.
- Over time, bronze naturally loses its luster due to reactions with air and water.
Is Tin Bronze Expensive?
Yes, tin bronze is relatively expensive compared to brass. This is primarily attributed to its high copper concentration. Copper is a costly material, and its significant presence in the alloy contributes to the overall expense of tin bronze.
Does Tin Bronze Rust?
No, tin bronze doesn't rust. Unlike ferrous metals, bronze, including tin bronze, doesn't contain iron. However, while this mix enhances corrosion resistance and strength compared to copper, it isn't impervious to deterioration over time. Instead of disintegrating, bronze tarnishes to protect its surface. Tarnish can be perceived as having either a positive or negative effect, depending on the product’s intended use — preserving luster or embracing the rustic beauty of tarnished bronze.
Does Tin Bronze Turn Green?
Yes, tin bronze can develop a green patina, often due to bronze disease triggered by oxygen and chloride in a moist setting, leading to hydrochloric acid formation. This acid creates copper and tin chlorides, causing green spots. Distinguishing between a healthy and unhealthy patina involves assessing uniformity, and color variations, and ensuring it doesn't compromise structural integrity. Reducing exposure to moisture can mitigate this problem.
Is Tin Bronze a Strong Metal?
Yes, tin bronze is a strong metal compared to pure copper and brass though not as ductile as brass. The tin added to copper (along with minor elements that may also be added) provides tin bronze with its strength. Its strength combined with its corrosion resistance and other desirable properties have contributed to its historical and continuing contemporary use in sculptures, tools, and industrial applications such as fittings and bearing surfaces.
What Is the Difference Between Tin Bronze and Arsenical Bronze?
The primary distinction between arsenical and tin bronze is the latter's higher rate of work hardening. This means that arsenical bronze could be reduced to thinner cross sections because it strengthened and became harder to shape more slowly than tin bronze. Arsenical bronze is an attractive option for producing thin metal sheets because of its improved ductility. Arsenic contamination in copper ore occurs naturally. Specifically, alloys containing more than 1% arsenic by weight are referred to as "arsenical bronze" in archaeology. This differentiation serves to separate possible unintentional inclusions of arsenic from purposeful use of arsenic.
What Is the Difference Between Tin Bronze and Tin Metal?
Tin bronze is an alloy that combines the qualities of tin and copper. Tin metal, on the other hand, only refers to pure tin. The melting point of pure tin is 231.9 °C which is quite low compared to tin bronze.
To learn more, see our full guide on Tin Metal.
Summary
This article presented tin bronze, explained it, and discussed its properties and various applications. To learn more about tin bronze, contact a Xometry representative.
Xometry provides a wide range of manufacturing capabilities and other value-added services for all of your prototyping and production needs. Visit our website to learn more or to request a free, no-obligation quote.
Disclaimer
The content appearing on this webpage is for informational purposes only. Xometry makes no representation or warranty of any kind, be it expressed or implied, as to the accuracy, completeness, or validity of the information. Any performance parameters, geometric tolerances, specific design features, quality and types of materials, or processes should not be inferred to represent what will be delivered by third-party suppliers or manufacturers through Xometry’s network. Buyers seeking quotes for parts are responsible for defining the specific requirements for those parts. Please refer to our terms and conditions for more information.
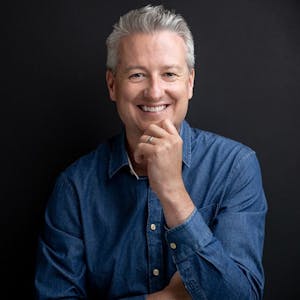