Thermoplastic Elastomers or TPEs combine the look and feel of a thermosetting elastomer with the processing power of thermoplastics. While elastomers are employed when flexibility is a primary concern, thermoplastic uses are broader and place more emphasis on the specific material’s properties. However, with the right process of injection molding or extrusion, manufacturers can create flexible materials that also take on important thermoplastic-type properties. This is a major advantage of TPE materials.
Uses of thermoplastic elastomers vary between industries. It’s important to pick a TPE material that is compatible with the application where it will be used.
This article will review 7 uses of thermoplastic elastomers, review their advantages, and examine how they’re processed. The table below shows some of the common uses of TPE:
Uses of Thermoplastic Elastomer | Description |
---|---|
Uses of Thermoplastic Elastomer Automotive | Description TPE is used for automotive applications due to its flexibility, excellent wear, chemical, and electrical resistance, and UV stability. |
Uses of Thermoplastic Elastomer Construction | Description TPE’s durability and flexibility make it the perfect choice for extruded weather seals. |
Uses of Thermoplastic Elastomer Industrial | Description TPE has excellent damping ability for applications such as anti-vibration mounts and springs. |
Uses of Thermoplastic Elastomer Consumer Products | Description TPE’s durability, flexibility, ease of molding, and chemical resistance are desirable for remote control covers and mobile phone cases. |
Uses of Thermoplastic Elastomer Medical | Description TPE is flexible, biocompatible, lightweight, and chemically resilient. This makes it useful for breathing tubes, syringe seals, masks, and other airtight seals. |
Uses of Thermoplastic Elastomer Electronics | Description TPE is used for mobile phone components, cables, plugs, and sockets due to its electrical resistance and ability to be molded. |
Uses of Thermoplastic Elastomer Sporting Goods | Description TPE is used for shoe soles, scuba flippers, and ski pole handles due to its flexibility, wear resistance, and UV stability. |
Table: Common Applications and Uses of TPE Material
1. Thermoplastic Elastomers is Used For Automotive Parts
Many automotive parts are made of thermoplastic elastomers. They find their way into seats and interiors, weather seals, and floor mats, among other things. TPEs are ideal for automobiles due to their excellent wear, chemical, and electrical resistance characteristics. Additionally, environmental resilience and UV stability make TPE highly desirable for use in cars since it won’t degrade in direct sunlight.
2. Thermoplastic Elastomers is Used in Construction Materials
In construction, TPEs are used in the form of extruded weather seals for doors and windows as well as other seals such as glazing and pipe seals. TPEs are great for these applications due to their chemical and environmental resilience and their durability and flexibility.
3. Thermoplastic Elastomers is Used in Industrial Applications
TPEs are used in industrial applications, especially to create seals and reduce vibration. Uses include: vibration isolators, springs and shock absorbers, drum suspension bushes, and seals and O-rings. TPEs are ideal for these applications due to their excellent damping ability.
4. Thermoplastic Elastomers is Used in Consumer Products
In consumer products, TPEs are often co-injected with a separate plastic material or over-molded onto a substrate. They’re found in power tool grips, remote controls, mobile phone covers, magnetic seals in refrigerators, and shock-absorbing components for vacuum cleaners. TPEs can be used in various consumer products due to their durability, flexibility, ease of molding, and chemical resistance.
5. Thermoplastic Elastomers is Used in Medical Supplies
Supplies such as breathing tubes, syringe tips, catheters, and masks often contain TPEs. These materials see wide use in medical settings because of their excellent chemical resistance, biocompatibility, flexibility, and lightweight.
6. Thermoplastic Elastomers is Used in Electronic Devices
TPE materials often show up in condensers, casings for plugs and sockets, cables, and smartphone components. They are ideal for such applications because they’re not conductive and are easy to mold.
7. Thermoplastic Elastomers is Used in Footwear and Sporting Goods
TPEs are used in shoe soles and various sporting goods including: ski equipment (pole handles, boots) and diving equipment (flippers, masks, and snorkels). The low density, flexibility, and abrasion resistance of TPEs make them great options for footwear and sporting goods.
When Do You Use Thermoplastic Elastomers?
TPEs are used in applications where flexibility is desirable. Many thermoplastics are far more rigid than TPEs and simply don’t fit the bill for soft or flexible components. This is where TPEs shine. Additionally, TPEs are used in applications where chemical, environmental, and abrasion resistance are important.
For more information, see our guide on thermoplastic elastomer.
Where Can Thermoplastic Elastomers Be Used as an Alternative?
TPEs can be substituted in place of materials like silicone, latex, and PVC compounds. Comparatively, TPEs are cheaper to manufacture but exhibit similar characteristics - specifically flexibility and durometer rating. Silicone, latex, and PVC compounds are tedious to turn into products. These materials often require additives along with extra time to allow the material to cure in a mold. Additionally, since TPEs can be formed through automated processes such as injection molding or extrusion, they are easier to mass-produce.
What Is the Most Common Thermoplastic Elastomer Production Method?
Injection molding and extrusion are the most popular methods for processing TPEs. However, blow molding, thermoforming, and 3D printing are also viable options. Unlike silicone, latex, and PVC compounds, TPE doesn’t require additional stabilizers, reinforcing agents, or cure systems. Therefore, TPEs function well for large-volume injection molding or extrusion runs.
For more information see our guide on the Types of Thermoplastic Elastomers (TPEs).
How Is Thermoplastic Elastomer Processed Before Being Used?
Unlike silicone, latex, and PVC compounds, TPE processing doesn’t require additives to help it set and cure. However, some TPE materials must be sufficiently dried before processing. Drying TPE ensures that excess moisture doesn’t hinder manufacturing or affect the final material’s properties. Refer to the material data sheet for each individual resin to determine drying temperatures and times.
What Are the Advantages of Using Thermoplastic Elastomers?
Perhaps the greatest advantage of TPE is that it exhibits characteristics of thermosetting rubber but can be formed using the same processes used for thermoplastics. TPE is lightweight and exhibits excellent material properties that make it ideal for certain applications. It is also cheaper to process than the materials it typically replaces such as silicone, latex, and PVC compounds. TPE is easy to color or dye, making it attractive for customer-facing parts.
For more information see our guide on the Advantages of Using Thermoplastic Elastomers.
What Are the Disadvantages of Using Thermoplastic Elastomers?
Disadvantages of thermoplastic elastomers include sensitivity to shear forces, low resistance to odors, and, in some cases, price. TPEs can be more expensive than thermoset rubbers. Additionally, their low melting temperature makes TPE materials unusable in high-heat applications.
Common FAQs About Thermoplastic Elastomers
Is Thermoplastic Elastomer Uses Less Energy to Manufacture?
Compared to other thermoplastics, TPEs use less energy during processing. They owe this benefit to short cycle times in injection or extrusion machines.
Is Thermoplastic Elastomer a Rubber Substitute?
TPEs function as rubber substitutes and, in many cases, are more desirable. This is due to lower processing costs, consistency in production, and desirable material properties.
Summary
This article discussed 7 uses of Thermoplastic Elastomers (TPEs) plus the advantages and limitations of the material.
Xometry offers on-demand manufacturing for all of your prototyping and production needs. Visit our website to learn more and to request a free, no-obligation quote using our Instant Quote Engine.
Disclaimer
The content appearing on this webpage is for informational purposes only. Xometry makes no representation or warranty of any kind, be it expressed or implied, as to the accuracy, completeness, or validity of the information. Any performance parameters, geometric tolerances, specific design features, quality and types of materials, or processes should not be inferred to represent what will be delivered by third-party suppliers or manufacturers through Xometry’s network. Buyers seeking quotes for parts are responsible for defining the specific requirements for those parts. Please refer to our terms and conditions for more information.
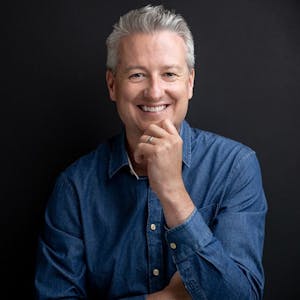