If you’ve ever stepped on a garage floor, held a paintbrush, or used an electronic device, you’ve likely come into contact with epoxy. These thermoset polymers are popular materials for 3D printing and manufacturing for a wide range of industries, like the dental, automotive, and electronic sectors. Aside from serving as a coating or a finish, epoxies are also go-to glues when you need to combine difficult-to-bond materials. At Xometry, we use epoxies to bond large 3D prints together to make huge models or in our shop when working with assemblies.
Learn more about this versatile and important polymer below, and get a better understanding of its applications and all the types of epoxies there are to choose from.
What is Epoxy?
Epoxies are thermoset polymers that are really like chameleons in their ability to change and adapt depending on what they’re needed for. They can be used to coat and seal a floor or structure, painted between two components to serve as an adhesive, and found among the bottles of glue in craft kits. This adaptability hints at their top-notch characteristics and why people often reach for epoxy in many situations. They’re great adhesives and have a higher tensile and compressive strength — not to mention they remain chemically and thermally stable in a variety of environments.
How it Works
The science behind epoxy is fascinating. In plain sight, you’ll see that it can turn from a liquid or paste into a solid. Under the microscope, you’ll notice that this occurs through a series of cross-linking that happens between groups of epoxides and hydroxyl that are already within the pre-polymerization resin.
To get this reaction to take place, you’ll either use two chemical agents that’ll cause the coupling and free radicals to appear or you’ll use a catalytic hardener that’ll trigger this response. Either way, once this reaction happens, it’ll result in a strong, hardened surface.
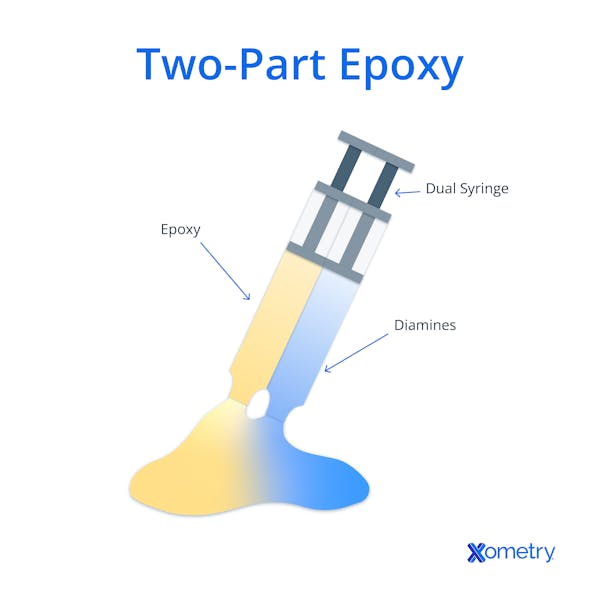
Epoxy in 3D Printing
Epoxy has been around for a while, but more recently it has played a large part in 3D printing, including in our own 3D printing services here at Xometry. It has more than one purpose, too, and below we’ve broken down all the ways in which this material can be used:
- Coupling agent: To improve the adhesion between the printing table and the printed object, epoxies are sometimes used to enhance the surface of build plates, allowing the surface to grip the printed part better. This is particularly helpful with desktop FDM machines.
- Penetrative coating: Printed objects made out of porous materials can be coated in epoxy, which will fill in holes and create a stronger and more durable exterior.
- Coloring and smoothing coating: Aside from penetrating porous materials, you can simply use epoxy to give a 3D model color or a smoother finish.
- Epoxy casting: For extra copies of a model, you can create a silicone mold from the original print, using it as a master pattern, then pour epoxy resin into the mold to create additional parts. For other materials, you may be able to make the mold out of epoxy as well!
- Printing material: Photosensitive epoxy resins are incorporated into materials used for some printing processes, such as our PolyJet or SLA printing processes. Resin-based materials can exhibit great mechanical properties and other useful characteristics.
A Quick History of Epoxy
Swiss chemist Pierre Castan can be thanked for creating epoxy resin after experimenting with reactions between several different chemicals. This happened in the 1930s and he was eventually granted a patent in 1940. Around the same time, a German chemist named Paul Schlack was also toying with different materials, leading to the ability we now have to synthesize and manufacture epoxies.
In the 1940s and 1950s, the dental industry started using epoxy and gradually it began gaining traction in other industries, like the aerospace, marine, and automotive sectors. Twenty years later, they entered the consumer market and have since remained an important material for large manufacturers and companies as well as individual hobbyists.
Properties and Characteristics
Looks-wise, epoxy morphs from a paste, liquid, or gel into a hardened solid. It’s usually clear or slightly opaque and you can tint it in numerous different colors. Outside of its appearance, it has many mechanical and physical properties that make it a favorite adhesive and coating.
- Epoxy has high tensile, compressive, and impact strength, so it’s ideal for structural uses.
- They have great chemical resistance to a range of acids, bases, solvents, and oils. That means it’s possible to use epoxies to coat the insides of tanks and reaction chambers as they can handle these rough environments.
- They’re also impressively heat resistant, so they’re capable of serving aerospace and electronic needs. Additionally, they work as great electrical insulators, too.
- Epoxy isn’t prone to serious shrinkage after it cures, so you can use it for surfaces and structures that require good dimensional stability and as little distortion and cracking as possible.
- There are several ways you can cure and cause the polymerization reaction, such as UV curing devices, thermal-triggered catalysts, or through moisture curing.
- As an adhesive, they’re capable of sticking a variety of materials together with ease, including wood, metal, plastic, ceramic, stone, and composite. We use epoxies to join together large 3D-printed models that would not be printable as a single piece.
- Aside from their durability in chemical-laden environments, epoxies can handle exposure to UV radiation, moisture, and saltwater too.
Types of Epoxy
Epoxy not only has many useful properties, but it comes in a long list of different types, which is useful for customizing the epoxy for your intended application.
1. Standard
This is the closest formula to the original epoxy that appeared back in the 1930s. However, they’ve been tweaked and reformulated to have even higher strength and resilience as well as faster curing times. This is a great cost-effective option for a wide range of purposes, such as for repairs and furniture making.
2. Water-Dispersed (or Water-Based)
This type of epoxy isn’t truly water-based as it’s often called, but it has a water-dispersed composition that will evaporate when it’s cured. It’s a smart formulation to use when you’re sealing tanks or in need of a waterproof sealing agent. They also have low to no volatile organic compounds, which makes them a safe choice when you’re applying them in enclosed environments around people.
3. UV-Cured
As the name implies, this type of epoxy is cured through a UV light and is a two-part process. The epoxy and the chemical that will initiate the reaction are both applied and then hardened through UV. You’ll commonly see this in casting, artwork, and even dental work. Because the epoxy can be irritating or relatively toxic, it takes a well-trained professional to apply it. UV-sensitive epoxy resins are also common in the material used for certain additive manufacturing processes that we offer.
4. Structural
Structural epoxies are perfect for applications that require bonding difficult materials or items or structures that will need to be machined after. This type of epoxy doesn’t slump and it’s pretty viscous, so it’s well suited for filling in gaps and serving as an electrical insulator. They’re also resistant to abrasion, water, and impact, making them an all-out great choice.
5. High-Temperature
For applications where you’ll be subjecting surfaces, structures, or objects to extremely high temperatures, this is the best-suited epoxy for the job. They have very similar properties to other epoxy resins but can withstand temperatures up to 300° C and have good chemical resistance too. They’re typically made with a bisphenol F diglycidyl ether copolymer that gets cured through a fatty acid or tetraethylenepentamine polyamide.
6. Flexible
Within the makeup of flexible epoxies are rubber or elastomer beads that give extra shock tolerance, toughness, and flexibility to the final hardened product. There have been important breakthroughs recently with this type, thanks to the silane and siloxane components within the epoxy. Mixed into the formula, they provide a cross-linked material that’s tough when cured but still ranks as a 20D on the Shore Hardness scale, which is softer than a rubber heel of a shoe.
7. Conductive
A conductive epoxy helps support electrically conductive environments (though they aren’t intrinsically conductive), while also offering surfaces or sections of parts an anti-static, flexible, and durable coating or composite. You’ll find them in repair pastes for etched copper tracks, wristbands on fitness tracking equipment, and circuit boards.
Classes of Epoxy Resin
On top of epoxy types, there are also specific classes that speak to the chemical groups that make up each type, which we break down below.
1. Glycidyl
This class of epoxies has a functional glycidyl group within their chemical structure, and the resins form through the reaction between epichlorohydrin and a reactive hydrogen compound, like bisphenol A (BPA). From it, you get an epoxy with a linear and branched makeup that has great thermal and chemical resistance and top-notch adhesion. Manufacturers and companies looking for quality adhesives and coatings or an epoxy that works on electronics products or composite materials will likely opt for one of these epoxies.
2. Novolac
This epoxy involves the chemical reaction between phenolic novolac and epichlorohydrin. In comparison to a glycidyl epoxy, or one with BPA in its structure, it offers more chemical resistance and thermal stability thanks to its highly cross-linked structure. This epoxy is usually cured with amines and often has toxic substances in its makeup (like formaldehyde and phenol), so they should be used carefully and in the right environments.
3. Cycloaliphatic
The chemical structure of these epoxies features a ring-like structure as their backbone, making them more rigid and compact. They’re often found in the manufacturing of composites, coatings, and adhesives and usually contain hazardous substances, so it’s best to take care when you’re working with this type. They’re reliable for instances where chemical resistance, mechanical strength, and electrical insulation are important.
4. Aliphatic
Similar sounding to cycloaliphatic epoxies, these differ in that they don’t have a circular structure within their makeup, but a straight or branched set of carbon chains instead. This makes them less rigid than their cyclo-counterparts, lending themselves to situations where flexibility is key. These epoxies are also very useful if you’re after UV resistance, color stability, and low toxicity. That’s why they’re often found in marine, automotive, outdoor, and food applications.
5. Aromatic
An aromatic epoxy also features a “ring” within its chemical structure and is a product of BPA and epichlorohydrin reacting together. They’re great epoxies for lining containers and tanks as they have high levels of chemical resistance and are strong and stiff. They’re relatively glossy as a finish but they’re not ideal for applications that need to retain their color. It’s another class of epoxies that should be used with caution as they contain hazardous substances, too.
6. Hybrid
This class includes epoxies that mix two or more types. As an example, this could be a blend of a cycloaliphatic epoxy with a novolac epoxy. Hybrid epoxies are created and used when you need specific benefits that only occur when you combine several together, and it leads to a material that can be used as a coating, adhesive, or composite in industries that require a higher level of performance, like the aerospace, construction, or automotive sectors.
Applications
Read on to get a small snippet of the long list of applications there are for epoxy:
- Floor and surface coatings, whether for protection or repair
- Protection for electronic parts like circuit boards
- Bonding mechanical and automotive parts
- Sealing and potting aerospace components
- Coating automotive parts to protect or repair
- Waterproofing for buildings, structures, and tanks
- Sealing and coating boats and marine vessels
- Jewelry-making and woodworking adhesive
- Materials for resin-based 3D printing
Choosing an Epoxy
There are a few important considerations to keep in mind when you’re selecting an epoxy. The most important priority is choosing a type or class that’s fit for the application you have in mind. It should be formulated for adhesion, coating, or creating a composite material. Epoxies are also made for specific materials, which ensures that it’ll create a secure and durable bond for that specific surface. There are also a range of cure times, which may be important to note depending on the timeframe or outlying factors that can affect a successful epoxy coating.
In harsh environments or those exposed to high temperatures, choose an epoxy that’s built to handle these factors for the best results. Epoxies can also lead to health problems and hazards (like fires), so check warning labels, find the right environment conditions, and wear the right safety equipment.
Epoxies for Specific Materials
Some epoxies are better for specific materials, too. For instance, when working with metal, clear, toughened, high-temperature, and conductive epoxies are best. With plastic, you’ll want epoxies with plastic-bonding agents included, fast-setting epoxies, flexible epoxies, or structural epoxies. Lastly, for cement, there are specific concrete epoxies available that work best. Outside of this, structural, moisture-tolerant, and high-temperature epoxies are best.
Tips for Use
- Make sure you properly clean and dry any surface that you’re applying epoxy so contaminants, dust, and grime aren’t trapped within it, and so the surface dries evenly.
- Closely follow the mixing ratio when you’re working with an epoxy that requires two different components.
- Apply epoxy evenly and quickly after readying it to avoid problems like uneven surfaces, air pockets, or poor coverage.
- Give the epoxy plenty of time to cure and ensure you stick to the recommended drying times and environment conditions (like specific temperatures). Sometimes it’s a good idea to “overcure” UV cured epoxy to ensure all parts of it have properly set.
Advantages and Disadvantages of Using Epoxy
When working with epoxy, it’s good to have an idea of the pros and cons that come with this material. Some of the advantages include that epoxy:
- Is great at filling bonds and offers good surface conformity
- Attaches easily and strongly to a long list of materials, like wood, plastic, and metal
- Has high strength and tolerance to shock and varying temperatures
- Has good hardness
- Is easy to use and low cost
There are also a few disadvantages to note. Epoxy can:
- Have a long cure time, specifically for high-strength versions
- Be weaker if you use a fast-cure version
- Have toxic and hazardous chemicals and ingredients in its formula
- Be brittle, depending on the type or class you use
- Have a hard time sticking to and coupling with low-energy surfaces
How Xometry Can Help
Working with epoxy often provides users with strong and durable surfaces and coatings, whether it’s used to create a 3D printed mold, properly seal a structure on an aerospace vessel, or provide a consistent and even coating on a warehouse floor. If you’re interested in services that involve epoxy, reach out to our team for more information or get an instant quote for our 3D printing services.
Disclaimer
The content appearing on this webpage is for informational purposes only. Xometry makes no representation or warranty of any kind, be it expressed or implied, as to the accuracy, completeness, or validity of the information. Any performance parameters, geometric tolerances, specific design features, quality and types of materials, or processes should not be inferred to represent what will be delivered by third-party suppliers or manufacturers through Xometry’s network. Buyers seeking quotes for parts are responsible for defining the specific requirements for those parts. Please refer to our terms and conditions for more information.
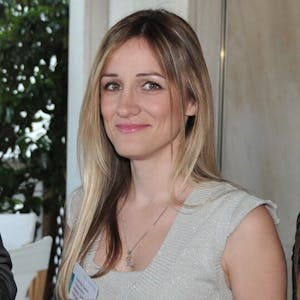