Solder is used for bonding metal pipes and electrical components. It has a low melting temperature, making it easy to handle while also having a low viscosity when melted, allowing it to fill very small spaces between parts. Solder is often supplied in a wire form and is melted using either a handheld soldering iron or a flame torch for higher melting temperature soldering, but when the temperature exceeds 450°C, the process is referred to as brazing rather than soldering.
This article will discuss what solder is, where it is used, advantages, disadvantages, and various properties of solder.
What Is Solder?
Solder is a metal alloy with a relatively low melting point. Typically, it is made from lead and tin, both of which have relatively low melting points. There are many different types of solder, and they can be purchased in rolls of soldering wire. Some solder also has a core of soldering flux that helps remove oxides from the metals being bonded to create an effective bond.
What Is Soldering?
Soldering is the process of electrically joining electronic components or metallurgically bonding metal parts. However, it does not provide significant mechanical strength compared to brazing or welding. The solder is typically melted using an external heat source like a soldering iron.
Soldering is most commonly used for electrical connections and less commonly for mechanical connections. Once melted, the solder has a low viscosity that allows it to fill the smallest gaps, creating a solid connection.
What Is the History of Solder?
Basic forms of soldering can be traced back to as early as 5,000 years ago when it was used to mechanically bond metal parts, such as different weapon components, as well as decorative metalwork, coin-making, and even early forms of plumbing. In terms of modern electrically related applications, the first soldering iron was patented in the 1890s by the American Electrical Heater Company. In 1928, the first soldering workstation was patented by William Alfernik. The effectiveness of the soldering iron was significantly improved with the advent of the instant heat soldering gun which was patented by Carl E. Weller. In terms of the solder itself, lead used to be the primary constituent of solder but has since been largely phased out, with mixtures of tin, silver, antimony, and nickel replacing lead-based solder.
What Is the Other Term for Solder?
When it comes to mechanically joining components, brazing is sometimes used instead of solder. However, brazing is a distinct process that requires a higher temperature and different filler materials. It must also be noted that the American pronunciation of solder is often “sodder” despite being spelled the same way.
What Is Solder Made Of?
The most common solder is a tin-lead alloy that has a relatively low melting point. However, lead has been phased out in some parts of the world due to its toxicity, with lead-free solder now being more commonly used. Lead-free solders typically have higher melting points and are often made from alloys of tin, silver, antimony, copper, and nickel. The exact composition can vary between different suppliers and applications. Some soldering wires also have flux cores to improve the bond during soldering.
How Are Solders Made?
Regardless of the type of solder, the first step involves mixing the various alloying elements and melting them in a furnace. The solder is cast into a usable shape, and it is drawn through various dies with decreasing diameters to create a wire of the desired diameter. With flux core solder, the flux is added into a large diameter billet with a hole drilled down the center. The billet diameter is reduced through various dies, and the flux gets drawn out along with the solder until the solder has reached its required diameter. A thin tube of flux remains in the center of the solder.
What Are the Characteristics of Solder?
Solder typically has a melting point ranging from 90°C to over 300°C, depending on its composition. Solder can be easily manipulated in its wire form and does not exhibit significant mechanical strength. It is also especially good at transmitting electrical current. Solder typically has a silver appearance. Lead-based alloys exhibit a degree of toxicity and should be used with care.
What Does a Solder Look Like?
Solder is often supplied as a thin wire wrapped around a plastic spool. However, different wire thicknesses are available. Figure 1 below shows a typical roll of soldering wire:
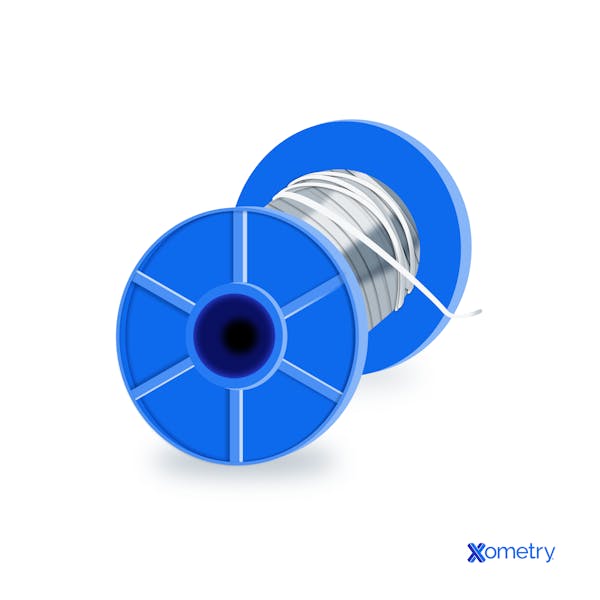
What Are the Different Types of Solder?
In general, solder can be divided into two different categories: lead-containing and lead-free. Each of these categories can be further differentiated by their exact composition and whether or not they are flux core types as described below:
- Lead-Based: Lead-containing solders are typically made of lead (40%) and tin (60%). However, some lead alloys contain as much as 95% lead. Lead-based alloys are represented by two numbers separated by a forward slash. The first number represents the tin content, and the second number is the lead content. The exact amount of each alloy can vary slightly for slightly different melting temperatures.
- Lead-Free: Lead-free refers to a family of solder that does not contain any lead. Certain regions like the EU have banned lead-based solders for specific use cases and, therefore, require lead-free alternatives. Most lead-free solder contains alloys of silver (Ag), tin (Sn), copper (Cu), and antimony (Sb).
- Flux Core: Flux core is a type of solder that contains both the solder alloy and the flux in the soldering wire. There are many different types of flux, the two most common being acid core and rosin core. Acid core provides excellent removal of oxidation but is generally used for higher temperature solders for bonding metals. Rosin core is more common for electrical applications as the rosin is non-corrosive. Both lead-based and lead-free solders are available with flux cores.
What Is Solder Used For?
Solder is used either for bonding metal parts together like plumbing pipes or for creating solid connections for electrical wiring or PCBs (printed circuit boards). For bonding metal parts, the process is often referred to as brazing and often requires a higher temperature than electrical soldering.
What Are the Properties of Solder?
A wide range of different solder compositions exist for both lead-based and lead-free solder alloys. For comparative purposes, lead-based and lead-free solder alloys have been listed in Table 1 below:
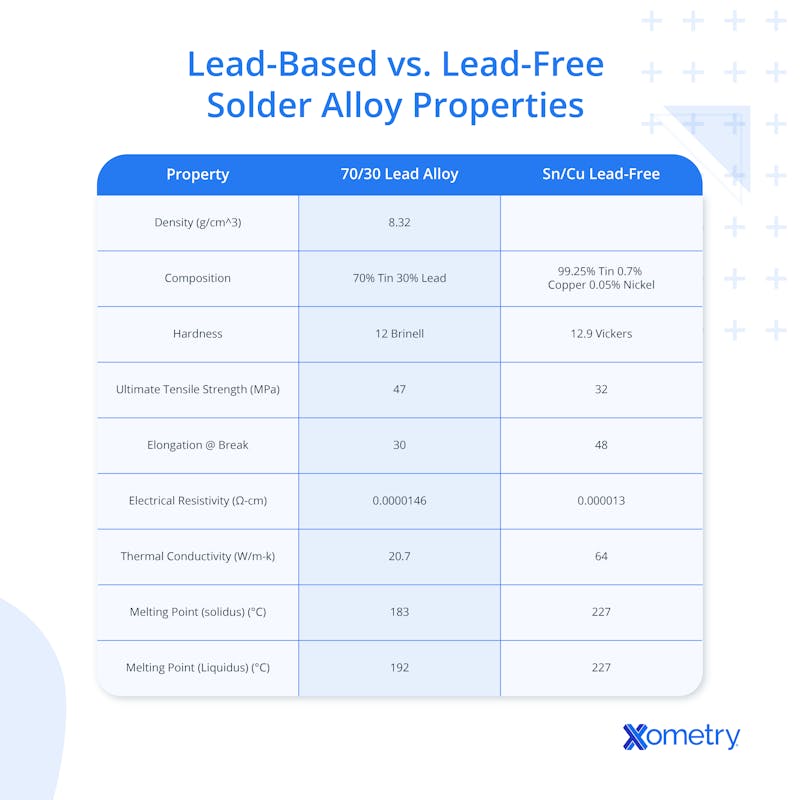
At What Temperature Does Solder Melt?
There are many different types of solder with different melting points. The melting point depends on the composition of the solder. For brazing, a temperature of at least 450°C is common whereas for electrical soldering, the melting temperatures can be anywhere from 90°C to 300°C. According to AWS (American Welding Society), soldering typically occurs below 450°C.
What Are the Advantages of Solder?
Listed below are some common advantages of solder:
- Flowability: Solder has a low viscosity when melted, and coupled with the capillary effect, enables the solder to flow into tiny spaces, creating a sealed joint.
- Low Melting Point: Solder has a relatively low melting point when compared to other joining methods like welding and can be melted with low-heat soldering irons or gas flames. The low melting point prevents the warping of metal parts or damaging sensitive electrical components.
- Ease of Use: Soldering does require some skill but is an accessible method for joining metal and making electrical connections as the tools are relatively cheap, and the process can be quickly learned.
What Are the Disadvantages of Solder?
Listed below are some common disadvantages of solder:
- Harmful Fumes: Both lead-containing solder and flux produce potentially hazardous fumes, which can be dangerous in the case of long-term exposure. Lead-containing solder is banned for commercial products within the EU (European Union).
- Hot Tools: While soldering temperatures are generally lower than other thermal joining methods, the tools are still hot enough to cause serious burns if improperly used.
- Low-Strength Joints: As soldering does not melt the base metals as welding does, the joints made are not as strong and may not be suited for high-stress applications.
Common FAQs About Solder
Does Solder Rust?
No, only iron-based alloys can rust, and solder does not contain any iron. Solder is also highly resistant to general atmospheric oxidation, but like most metals, it can corrode over time. When soldering, the parts to be soldered will often have a layer of oxide on the surface, preventing a good connection. This is overcome by using soldering flux, which removes oxides from the surface and prevents new oxides from forming during soldering.
Is Solder as Strong as Aluminum?
No, solder is made from low-melting-point metals like tin, silver, copper, etc. Aluminum is stronger than all of these metals. An aluminum weld is significantly stronger than a soldered joint.
Is Solder Expensive?
No, solder is not particularly expensive, especially in electrical applications in which very little is required to make a sound electrical connection. However, lead-free solder can be more costly due to the inclusion of silver.
Summary
This article presented solder, explained it, and discussed its composition and properties. To learn more about solder, contact a Xometry representative.
Xometry provides a wide range of manufacturing capabilities and other value-added services for all of your prototyping and production needs. Visit our website to learn more or to request a free, no-obligation quote.
Disclaimer
The content appearing on this webpage is for informational purposes only. Xometry makes no representation or warranty of any kind, be it expressed or implied, as to the accuracy, completeness, or validity of the information. Any performance parameters, geometric tolerances, specific design features, quality and types of materials, or processes should not be inferred to represent what will be delivered by third-party suppliers or manufacturers through Xometry’s network. Buyers seeking quotes for parts are responsible for defining the specific requirements for those parts. Please refer to our terms and conditions for more information.
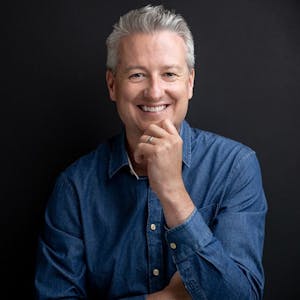