Thermoplastic polyolefin (TPO) grades are proportional blends of high molecular weight polypropylene (HMWPP) or polyethylene (HMWPE) with ethylene-propylene rubber (EPR). The high molecular weight PP or PE means low levels of side branching which makes the materials stronger and more crystalline. This results in a versatile material with excellent properties for various applications, in which the already tough PP/PE are made additionally resilient by the EPR addition. TPO is appreciated for its durability and resilience under distortion, weather resistance, and chemical stability. It's ideal for impact-prone applications and for outdoor use.
This article will discuss what TPO is, including its properties and advantages.
What Is TPO Plastic?
Thermoplastic polyolefin is a compounded polymer blend (rather than a copolymer) made by adding variable proportions of HMWPP or HMWPE and EPR. The material properties are influenced by the relative proportions of the two main constituents. In addition, fillers such as: calcium carbonate, carbon fiber, and talc are used as stiffening/toughening agents.
The manufacturing procedure for TPO involves blending polypropylene and ethylene-propylene rubber (plus powder or fiber additives) under controlled conditions. This is to emphasize the desired properties by adjusting the proportions and additive components.
Properties of TPO Plastic
TPO can be adjusted to emphasize particular properties that make it a flexible, adaptive, and widely selected choice for an increasing range of consumer and industrial applications. Some of its properties are:
- Flexibility: This allows it to conform to required shapes and contours for installation without cracking or tearing and makes it highly tolerant of impact and distortion in use. It resists permanent deformation and returns to its as-molded shape with minimal damage.
- Excellent Resistance to UV, Ozone, and General Weathering: Making parts that are suitable for outdoor use while suffering no detectable degradation or color fade over prolonged use. The materials show good resistance to acids/alkalis, cleaning agents, oils, and solvents, resulting in great durability in prolonged exposure to harsh environments.
- Higher Impact Strength Than Most Other Polymers: This serves to protect components from damage and ensure longevity in demanding conditions. It is widely utilized as buffer components to protect more vulnerable materials, enabling car bumpers to tolerate low-speed impacts and bounce back without substantial damage.
- Lightweight Compared to Many Other Materials: This contributes to fuel efficiency in automotive applications and ease of handling in construction. It is often markedly lower-cost than alternative materials, offering a beneficial performance despite being cost-effective.
When comparing TPO to other materials, TPO typically offers better weather resistance, impact tolerance, and flexibility compared to PVC, while PVC may have superior chemical resistance in some more extreme applications. TPO generally offers better UV resistance and greater dimensional stability than EPDM rubber, although EPDM will typically offer a higher maximum service temperature. TPO provides considerably greater chemical resilience and much-improved impact strength, compared to polyethylene, although polyethylene may have superior long-term moisture resistance.
Advantages of TPO Plastic
Thermoplastic polyolefin (TPO) offers several advantages over alternative materials, such as:
- It is generally available at a lower cost than alternative materials like PVC or EPDM rubber, providing a balance of performance and affordability, as the main constituents are low-commodity polymers manufactured in very large volumes.
- It has low to zero toxicity, unlike the PVC options that it is a potential alternative to.
- TPO is highly flexible, allowing it to conform to various shapes and contours without cracking or tearing and generally with full recovery to the pre-flexed state when forces are removed. This makes it ideal for operations requiring force application and distortion tolerance.
- It exhibits excellent resistance to UV, ozone, and general weathering, offering durability and long service in outdoor applications without property degradation or color fade.
- TPO shows good resistance to moderate acids, alkalis, oils, and solvents. This makes it suitable for applications in which exposure to aggressive chemical environments is demanded.
- Its flexibility results in extremely high impact strength/resilience. This allows it to protect more vulnerable components from damage and ensures TPO component durability in demanding conditions.
- TPO maintains its shape and dimensions even under high-temperature conditions and moderate temperature cycling, with a very low risk of warping or distortion. This is in part due to its thermal resilience but also due to it suffering very low residual stress from molding and forming processes.
- It is lightweight when compared to many alternative materials, contributing to fuel efficiency in automotive and aircraft applications and ease of handling in construction.
- Unlike its primary polyolefin constituents, it can accept adhesive, painting, and surface coating after relatively simple surface preparation. This makes it a great alternative to pure PP or PE in high-cosmetic and bonded applications.
Disadvantages of TPO Plastic
While TPO offers many advantages, it also has some disadvantages, such as:
- High-temperature resistance is good up to its operational limit, but it may not perform well in low-temperature conditions. It can become brittle at low temperatures and rapidly soften as its maximum service temperature is exceeded.
- While TPO generally exhibits good chemical resistance, it can eventually break down and fail under exposure to strong acid or alkali environments. This results in progressive depolymerization and structural collapse.
- TPO typically comes in limited color options compared to materials like PVC, which may limit its aesthetic appeal in certain applications in its as-molded state.
- Susceptibility to stress cracking results from rapid and extreme temperature cycling, extreme and prolonged UV exposure, prolonged chemical exposure at high levels, and long-term cyclic loading that approaches the elastic limit of the material.
- TPO can be challenging to bond using traditional adhesive or solvent processes, requiring specialized techniques for effective bonding.
Applications and Industries That Use TPO Plastic
TPO is utilized in applications across a large range of sectors and industries thanks to its versatility and useful tolerances/properties. These industries include:
- Automotive: TPO is heavily used in automotive applications, such as exterior body panels, interior trim components, bumper fascias, and under-hood parts, due to its excellent impact resistance, weatherability, elevated temperature tolerance, and lightweight nature.
- 3D Printing: TPOs are used in FDM/FFF printers for making elastic and tough prototypes.
- Building and Construction: TPO is used in roofing membranes, wall claddings, window profiles/seals, and piping systems in the construction industry due to its durability, weather resilience, and low-cost processing.
- Consumer Goods: TPO is used in consumer goods, such as: furniture, appliances, and sporting goods, exploiting its impact resistance, chemical durability, and aesthetic qualities.
- Medical: TPO is used in medical devices, hospital equipment, and disposable medical supplies for its chemical stability, biocompatibility, sterilizability, and chemical durability.
- Packaging: TPO is used in packaging applications, such as: films, containers, and closure features, due to its toughness, flexibility, and moisture resistance.
- Agriculture: TPO is used in agricultural applications, like: greenhouse films, irrigation-system components, and protective covers, due to its UV resistance, durability, and chemical resistance.
What Is the Environmental Impact of TPO?
The environmental impact of TPO is relatively low, compared to many other plastics. TPO is recyclable. It can be reprocessed and used in new products, reducing the need for virgin materials and minimizing waste. However, only specialist life-cycle services in the automotive industry have the facility to fully identify the material and grade it precisely for re-use. Normal recycling streams lack the volume or selectivity to exploit this re-usability. TPO manufacturing processes typically require less energy compared to other plastics like PVC as they operate at lower pressures and temperatures, reducing the overall energy footprint associated with virgin material production.
While TPO itself is not biodegradable, some TPO products may be engineered to degrade under certain conditions by the introduction of sensitizing additives. This reduces their environmental impact after use. This is not common in the TPO supply chain. TPO does not contain chlorine or other harmful chemicals. This makes it less hazardous to human health and the environment during its life cycle than PVC and is a potential alternative in many applications. Proper disposal and recycling of TPO products are essential to minimize environmental impact. Improper disposal, such as landfilling or incineration, results in additional pollution and negative health effects.
Is TPO Plastic Safe To Use?
Yes, TPO is generally considered safe to use in various applications. TPO lacks any harmful constituents such as: chlorine, PCBs (polychlorinated biphenyls), plasticizers, and heavy metals. This renders it non-toxic and safe for use in products that come into contact with food, water, or humans. It exhibits high levels of chemical resilience, making it simply unreactive in most environments encountered in industrial or household environments. This stability ensures that TPO does not leach harmful substances into its surroundings. TPO typically emits extremely low levels of VOCs during production and use, so its impact on indoor air quality and resultant reduced health risks for operators and consumers are negligible. TPO materials manufactured into consumer products are subject to broad international and local regulations and standards. These standards ensure their safety and compliance with health and environmental guidelines.
What Are the Differences Between TPO and TPE?
TPO and TPE (thermoplastic elastomer) are both thermoplastics with useful elastomeric properties, but they have some distinct differences that define their application-specific suitability.
TPO is typically a blend of PP or PE and ethylene-propylene rubber (EPR or EPDM). TPEs consist of a thermoplastic matrix, which provides structural integrity and processability, combined with elastomeric segments dispersed throughout the matrix which provide the elasticity that is the principal property sought. TPOs are generally stiffer and more rigid in comparison to TPEs, which are typified by their flexibility, softness, and rubber-like elasticity. TPOs are most commonly processed by: injection molding, extrusion, and thermoforming. TPEs, on the other hand, can be processed using a wider range of methods, including: injection molding, extrusion, blow molding, various rubber molding methods, and very commonly by overmolding onto rigid polymer substrates. TPOs are commonly used in automotive parts, roofing membranes, and construction materials due to their durability, weather resistance, and chemical stability. TPEs find applications in consumer products, medical devices, seals, gaskets, and soft-touch grips, for which flexibility, resilience, and tactile properties are essential. TPOs are highly durable materials that are normal-environment stable. TPEs can suffer from environmental breakdown over time, developing stickiness and loss of structural integrity due to oxidation and moisture.
While both TPOs and TPEs offer elastomeric properties, their chemical compositions, hardness, processing methods, durability, and applications vary significantly.
Summary
This article presented TPO, explained it, and discussed what it is and its various properties. To learn more about TPO, contact a Xometry representative.
Xometry provides a wide range of manufacturing capabilities and other value-added services for all of your prototyping and production needs. Visit our website to learn more or to request a free, no-obligation quote.
Disclaimer
The content appearing on this webpage is for informational purposes only. Xometry makes no representation or warranty of any kind, be it expressed or implied, as to the accuracy, completeness, or validity of the information. Any performance parameters, geometric tolerances, specific design features, quality and types of materials, or processes should not be inferred to represent what will be delivered by third-party suppliers or manufacturers through Xometry’s network. Buyers seeking quotes for parts are responsible for defining the specific requirements for those parts. Please refer to our terms and conditions for more information.
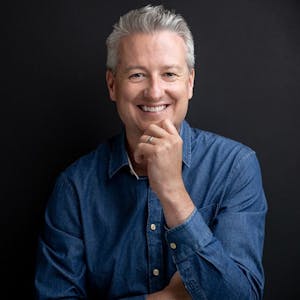