Laser devices create intense beams of light that are focused along tight and extremely precise paths. That gives them unique capabilities, but the ultimate value and employment of a given laser depend upon its power output.
To measure laser power you must not only use the proper methods, but also understand the definition, purpose, and effects of laser power. This article provides an insightful exploration of these key aspects, shedding light on the significance of precise laser power measurement and the diverse techniques for the task.
What Does Measuring Laser Power Mean?
Laser power measurement is the process of quantifying the amount of optical power emitted by a laser beam. It involves determining the power output, typically expressed in watts (W) or milliwatts (mW), which represents the energy delivered per unit time. Accurate power measurements are crucial in numerous applications, including laser research, industrial processes, medical procedures, and telecommunications.
Why Is Measuring Laser Power Necessary?
Measuring laser power is essential for safety, performance, and process control. Accurate readings help prevent hazards like burns or eye damage and ensure devices operate within safe, effective limits. Additionally, in industrial and manufacturing processes, laser power is a critical parameter that directly impacts product quality and helps companies maintain consistent, reliable results.
Calibration of power meters requires reference lasers or light sources with traceable and stable output characteristics, typically certified by standards labs.
What Are the Methods Used To Measure Laser Power?
The methods used to measure laser power are listed below:
1. Power Meter
A laser power meter is made to measure optical power, which represents the amount of energy delivered per unit time, in a light beam. When receiving a pulse train with a high pulse repetition rate, the power meter typically displays only the average power. Standard laser power meters typically use either photodiode sensors for low-power CW lasers or thermal sensors like thermopiles and calorimeters for higher-power or pulsed lasers. Pyroelectric detectors are used specifically for pulsed laser applications.
Calorimeters use timed exposure to determine laser power. The meters display the average power absorbed on a calibrated display scale and are suitable for measuring the average power output of pulsed or continuous lasers. These meters typically have a response time of several seconds.
Pyroelectric meters, on the other hand, respond to changes in incident energy rather than providing a continuous power reading. Pyroelectric meters are best suited for pulsed lasers with repetition rates up to several kilohertz.
2. Photodiode or Photodetector
Semiconductor photodiode-based sensors or optical sensors are utilized in instruments to convert incident photons into measurable currents. These sensors are highly sensitive within their designated spectral range and naturally reject out-of-band noise. They’re ideal for detecting extremely low light levels. However, when operating above the milliwatt level, attenuating filters are necessary to prevent saturation. Their fast response makes them well-suited for real-time laser tuning and detecting rapid power fluctuations. However, their spectral range is more limited compared to other sensor technologies. These sensors are primarily suited to CW laser measurements in the low to moderate power range. Semiconductor/optical sensors are very stable and exhibit significantly higher sensitivity than thermopile sensors.
3. Thermopile Sensors (Thermal Method)
Thermopile sensors are versatile and work with many laser types. They can handle CW lasers, pulsed lasers, and long-pulse energy integration across a wide power range. These sensors absorb the laser radiation and convert it into heat, which is then transferred to a heat sink maintained at ambient temperature through convection cooling or water cooling. The temperature difference between the absorber and the heat sink is converted into an electrical signal using a thermocouple junction.
Thermopiles can handle a wide range of input powers without saturation, unlike photodiode-based sensors. The spectral range depends on the coating applied to absorb the laser power. A broadband thermopile coating typically provides a relatively flat spectral response from the near-UV (~200 nm) through the mid-infrared (~10 µm). The response time of thermopile sensors varies from several seconds for low-power sensors to up to one minute for kilowatt sensors. Some systems use signal processing algorithms to estimate final power readings more quickly, improving perceived response time to just a few seconds.
If you need to measure the power output of a CW laser ranging from tens of milliwatts to kilowatts or in the infrared region beyond 1800 nm (where germanium photodiode sensors have limited sensitivity), a thermopile sensor is likely the most suitable choice.
One unique capability of thermopile sensors is the ability to evaluate the power of a single "long" laser pulse, typically ranging from 1 millisecond to several seconds, over the pulse duration. The meter analyzes the thermopile output and applies an integration algorithm to display a measurement in Joules. This feature is particularly useful for long-pulse medical or industrial lasers.
4. Beam Profiling
There are several methods available to measure the position of the beam focus accurately. One common approach is to utilize standard diagnosis and beam profile measurement systems. These systems scan the beam through a rotating pinhole. The pinhole redirects a minor portion of the radiation to the detector. The scanning traces can be adjusted along the y or z axes, allowing measurement of one plane to be completed within minutes. Repeating the scan at different distances from the focusing head allows a complete beam profile, including focus depth and waist dimensions.
By analyzing the power density distribution at the laser’s focus, the following beam parameters can be accurately measured:
- Positioning of the focal plane in space
- Focus radius
- Beam propagation ratio M2
- Spatial power density distribution
You may also be able to detect highly divergent beams generated by very high-powered diode lasers using different detectors and specialized measuring tips.
For a rough estimation of the beam’s focus position, you can run beam print tests on flat, anodized aluminum sheets at different focus positions. Photography paper also works in place of aluminum sheets. Another method is beam-swiping on tilted anodized aluminum sheets. These tests are easy to perform and do not require a heavy investment. However, these methods lack the precision and repeatability of dedicated beam profiling systems.
What Are the Main Parts of the Thermopile Sensor?
A thermopile sensor is made up of a few parts. Some of the main components are discussed below.
1. Hot Junction
The hot junction is part of the thermocouple network within the thermopile that is exposed to the heated absorber. As the absorber heats up from laser radiation, it causes a temperature rise at the hot junction, which contributes to the generation of a voltage signal.
2. Cold Junction
The cold junction is the reference point or portion of the thermopile that remains at a constant temperature. It serves as a baseline for temperature measurements, allowing accurate calculation of the temperature difference across the thermopile element.
3. Thermocouple Output
The thermocouple output refers to the voltage signal generated by the thermopile element. The temperature difference between the hot and cold junctions induces a thermoelectric voltage across the thermocouples. This voltage is proportional to the laser power being measured.
How to Measure Laser Power?
You can obtain precise and reliable measurements of laser power by combining a sensor and a meter. A sensor is specifically designed to be placed within the laser beam. It generates a signal output that is directly proportional to the laser’s power output. The meter receives the signal from the sensor and processes it using analog and digital adjustments to ensure accurate readings. These adjustments may include compensating for differences in calibration wavelength and laser wavelength. The meter then presents the measurement to the user. Some meters have their own built-in screens for displaying the measurement, while others offer advanced data analysis capabilities but must be connected to a PC for analysis and data processing.
What Are the Considerations for Selecting the Right Method To Measure Laser Power?
There are several key considerations when selecting the right method to measure laser power: the laser type (continuous wave or pulsed), the measurement needed (average power or energy per pulse), the power range, and the wavelength range. For pulsed lasers with repetition rates below 10 kHz and pulse energies in the millijoule range or higher, both thermopile and pyroelectric sensors can be suitable, depending on whether average power or energy-per-pulse measurement is needed. For lasers with higher repetition rates, a thermopile sensor will likely be required to measure the average power accurately. For more information, see our guide on How to Measure Laser Beam Quality.
What Are the Different Applications of Laser Technology?
Laser technology has a wide range of applications across various industries and fields. Here are a few common examples:
- Lasers enable cutting, welding, marking, and engraving of diverse materials, including metals, plastics, ceramics, and textiles.
- Lasers are valuable in advanced medical procedures and treatments. They perform precision cutting, ablation, and coagulation in surgery. Lasers are also employed in ophthalmology for vision correction (LASIK) and as part of non-invasive treatments like photodynamic therapy.
- Fiber-optic communication networks utilize lasers to transmit vast amounts of data over long distances.
- Lasers are invaluable tools in scientific research. They enable atom-level precision in experiments like laser cooling and trapping. Lasers are also used in holography and high-precision interferometry. In some specialized applications, laser-based systems help simulate conditions similar to underwater explosions in laboratory settings.
- Lasers serve as covert illuminators for reconnaissance during nighttime military operations. They can also damage and potentially neutralize missiles.
What Safety Precautions Should Be Followed When Measuring Laser Power?
It is essential to prioritize safety to protect both individuals and equipment from potential hazards when measuring laser power. Here are some important safety precautions to follow:
- Always wear laser safety glasses or goggles that are specifically designed for the laser wavelength being used.
- Understand the laser’s classification and follow the safety guidelines associated with it.
- Maintain a safe distance from the laser beam during power measurement.
- Regularly calibrate and maintain laser power measurement devices to ensure accurate readings.
- Ensure the workspace is well-ventilated to dissipate heat and remove any harmful fumes or particles emitted during laser operation.
- Train personnel involved in laser power measurement on laser safety procedures.
How Can Calibration Be Performed To Ensure Accurate Laser Power Measurements?
The general steps to calibrate a power meter are: select a suitable reference master sensor, ensure a constant power or energy level during calibration, and measure the sensor's sensitivity at different power levels and wavelengths. Additionally, any specific calibration procedures recommended by the power meter’s manufacturer should be followed to ensure accurate calibration.
Some common factors to consider when calibrating a power meter are listed below:
- Calibration Uncertainty: Refers to the level of uncertainty associated with the calibration process itself. It includes factors such as the accuracy of the reference standard used for calibration, measurement uncertainties introduced during the calibration procedure, and the traceability of calibration standards to recognized national or international standards.
- Energy Calibration Uncertainty (for thermal sensors): Thermal sensors require calibration for both power and energy measurements. Their long-pulse integration capability and thermal sensitivity must be accurately verified to ensure consistent performance across a range of applications.
- Wavelength Dependence: Power meters may have different responses to different wavelengths of light. Power meters must be calibrated to account for wavelength sensitivity, especially when used with broadband or tunable lasers across wide spectral ranges.
- Linearity: Refers to the ability of the power meter to provide accurate measurements across a range of power levels. Non-linearities in the response of the sensor can introduce errors, especially at the extremes of the measurement range. To ensure accuracy across different power ranges, calibration should verify linearity by testing at low, medium, and high input levels.
- Uniformity: Refers to the consistency of response across the active area of the power meter's sensor. Non-uniformities can result in measurement errors, particularly in cases where the power distribution is not evenly distributed over the sensor's surface. Calibration should include spatial mapping of the sensor's response to identify and correct any non-uniformity effects.
- Pulse Rate Dependence (for pyroelectric sensors): Pyroelectric sensors are commonly used for pulsed laser measurements. They may exhibit variations in sensitivity with the pulse repetition rate or pulse duration. Calibration should account for pulse rate dependence to ensure accurate measurements in different operating conditions.
- Calibration Uncertainty of the Display Unit: The display unit of the power meter, which provides the readout of power or energy measurements, can introduce its own calibration uncertainty. This uncertainty should be considered when evaluating the overall accuracy of the power meter.
- Environmental Factors: Environmental conditions such as temperature, humidity, and electromagnetic interference can impact the accuracy of a power meter. Calibration should be performed under controlled environmental conditions, or adjustments should be made to compensate for any environmental effects.
For more information, see our guide on Laser Beam Quality.
Are There Any Challenges With Measuring Laser Power?
Yes, measuring laser power can be tricky. Some of the common challenges associated with laser power measurements are listed below:
- Some laser beams have high enough power densities to damage the power measurement equipment.
- The shape and size of the laser beam can vary depending on the application. Using a sensor with a smaller or larger active area than the beam size can lead to inaccurate results.
- Different sensors have different spectral response characteristics. Their sensitivity can vary with the wavelength of the laser beam.
- Laser power measurements require stability to obtain reliable and repeatable results. Factors such as temperature fluctuations, vibrations, and ambient noise can introduce measurement instabilities.
Does Laser Cutting Equipment in Manufacturing Undergo Laser Calibration?
Yes, laser-cutting equipment used in manufacturing undergoes laser calibration. The calibration is an important process to ensure the accuracy and performance of the laser cutting system. Calibration helps to optimize the cutting process, maintain consistent cutting quality, and achieve precise dimensional accuracy in the manufactured parts, resulting in improved productivity and customer satisfaction. Some key aspects of laser calibration in manufacturing include: beam alignment, power calibration, beam quality, cutting parameters, and positioning accuracy.
For more information, see our guide on How Is Laser Cutting Used In Industry.
Common FAQs About Measuring Laser Power
Are There Any Challenges With Measuring Laser Power?
Yes, measuring laser power can be tricky. Some of the common challenges associated with laser power measurements are listed below:
- Some laser beams have high enough power densities to damage the power measurement equipment.
- The shape and size of the laser beam can vary depending on the application. Using a sensor with a smaller or larger active area than the beam size can lead to inaccurate results.
- Different sensors have different spectral response characteristics. Their sensitivity can vary with the wavelength of the laser beam.
- Reliable laser power measurements require a stable environment. External factors like temperature shifts and vibrations can skew readings, particularly in high-sensitivity setups.
Does Laser Cutting Equipment in Manufacturing Undergo Laser Calibration?
Yes, laser-cutting equipment used in manufacturing undergoes laser calibration. The calibration is an important process to ensure the accuracy and performance of the laser cutting system. Calibration ensures consistent quality, dimensional accuracy, and process efficiency, contributing to higher productivity and better product outcomes. Some key aspects of laser calibration in manufacturing include beam alignment, power calibration, beam quality, cutting parameters, and positioning accuracy.
For more information, see our guide on How Is Laser Cutting Used In Industry.
Summary
This article presented measuring laser power, explained what it is, and discussed its necessity and methods. To learn more about measuring laser power, contact a Xometry representative.
Xometry provides a wide range of manufacturing capabilities, including measurement and other value-added services for all of your prototyping and production needs. Visit our website to learn more or to request a free, no-obligation quote.
Disclaimer
The content appearing on this webpage is for informational purposes only. Xometry makes no representation or warranty of any kind, be it expressed or implied, as to the accuracy, completeness, or validity of the information. Any performance parameters, geometric tolerances, specific design features, quality and types of materials, or processes should not be inferred to represent what will be delivered by third-party suppliers or manufacturers through Xometry’s network. Buyers seeking quotes for parts are responsible for defining the specific requirements for those parts. Please refer to our terms and conditions for more information.
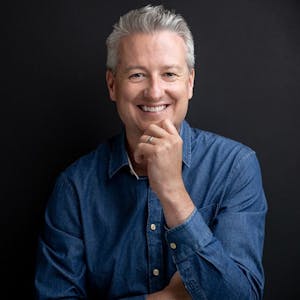