Shielded metal arc welding (SMAW), commonly known as arc welding or stick welding, is a popular welding process widely used in various industries. It is a manual welding technique that uses a disposable electrode covered in flux. The flux coating melts and decomposes to form a protective layer over the molten weld metal. By creating an electric arc between the electrode and the workpiece, SMAW produces a powerful amount of heat that melts both the electrode and the base metal. The molten metal cools, solidifies, and creates a solid, long-lasting weld joint.
SMAW has several benefits, including portability, simplicity, and versatility. It is appropriate for both indoor and outdoor applications, and it can be used to weld a variety of materials. A wide range of users can use SMAW equipment because it is also relatively inexpensive and simple to set up. SMAW remains a popular option for both welding experts and hobbyists. In the sections that follow, we will delve into the operating concepts, major benefits, and other aspects of this adaptable welding process.
What Is Shielded Metal Arc Welding (SMAW)?
SMAW, also known as stick welding or manual metal arc welding, is a process that utilizes a consumable electrode covered with a flux coating. The electrode is manually held at the correct distance from the joint to maintain a stable electric arc while heating the electrode at a rate fast enough to melt it, providing filler metal to create the finished weld joint.
What Is the Other Term for Shielded Metal Arc Welding (SMAW)?
Another name for shielded metal arc welding (SMAW) is “stick welding.” This commonly used name comes from the welding process's use of electrodes consisting of discrete lengths of flux-covered metal rods that call to mind sticks of wood.
Who Invented Shielded Metal Arc Welding (SMAW)?
In 1888, Nikolay Gavrilovich Slavyanov, a Russian engineer, introduced the use of metal electrodes (replacing the previous carbon electrodes) for melting and casting precision parts, such as gun barrels. American Charles L. Coffin took this innovation a step further in 1890, developing consumable metal electrodes for arc welding. This invention represented a significant development in welding technology.
What Is the Importance of Shielded Metal Arc Welding (SMAW)?
The importance of SMAW lies in its versatility and simplicity. SMAW is a widely used welding process that can be performed in various positions and environments. It provides a reliable and cost-effective method for construction, repairs, and maintenance in industries such as automotive, construction, and manufacturing.
How Does Shielded Metal Arc Welding (SMAW) Work?
Shielded metal arc welding (SMAW), also known as stick welding or manual metal arc welding (MMA), utilizes a welding arc, which is a sustained electrical discharge through a high-conducting plasma. This arc generates sufficient thermal energy to join metals by fusion. The welding arc is maintained between the consumable electrode and the workpiece, with current ranging from 5 to 2,000 amperes and voltage ranging from 10 volts to higher levels. The arc has a point-to-plane geometric configuration, where the electrode's end is the point and the workpiece is the plane. The length of the arc is proportional to the voltage applied. The electrode's flux coating shields the arc and molten metal, preventing oxidation and contamination, and forms a slag layer for post-weld cleaning.
How to Use Shielded Metal Arc Welding (SMAW)
To do SMAW, follow these steps:
- Clean the metal surfaces to be welded. Eliminate rust, dirt, and oil residue from the surface to ensure a strong weld..
- Choose the electrode type based on the metal being welded and the desired weld characteristics. Consult welding manuals, industry standards, welding textbooks, or experienced welders and welding instructors for information on how to select the proper electrode for SMAW.
- Connect the welding machine's power cable to a suitable power source. Connect the electrode holder to the positive terminal and the ground clamp to the negative terminal of the welding machine.
- Hold the electrode at a slight angle and strike it gently against the workpiece to initiate the arc. Ensure proper alignment, and hold the welding electrode in a vertical position relative to the area where the materials will be joined. Subsequently, tilt the electrode slightly at an angle ranging from around 5 to 15 degrees.
- Move the electrode in a steady and controlled manner along the joint, maintaining the correct arc length and angle.
- Allow the molten metal from the electrode to fill the joint, which will ensure proper penetration and fusion.
- Ensure even heat distribution and proper fusion by carefully monitoring and adjusting the welding speed. Additionally, adjusting the technique can help control the weld puddle and produce the desired bead size and appearance. Examples of these adjustments include maintaining a constant arc length and using the appropriate weaving or oscillation motion.
- Continue welding until the joint is fully traveled along the entire length of the intended weld, then extinguish the arc by carefully removing the electrode from the workpiece while still in control of the welding machine.
- Remove the slag created by the flux from the weld bead surface and inspect the weld for any defects, such as: cracks, blow holes, areas of obvious lack of penetration, etc.
What Basic Equipment Is Required for SMAW?
The basic equipment required for SMAW includes:
- Welding Machine or Power Source: Provides the electric current for welding.
- Electrode Holder: Holds the SMAW electrode and connects it to the welding machine.
- Ground Clamp: Completes the electrical circuit between the welding machine and the workpiece.
- SMAW Electrodes: Consumable electrodes with flux coatings, selected based on the type of metal being welded.
- Personal Protective Equipment (PPE): Includes welding helmet, gloves, protective clothing, and safety glasses for operator safety.
What Is the Right Speed for Shielded Metal Arc Welding?
The recommended range of travel speed for shielded metal arc welding (SMAW) is generally between 3 and 6 inches per minute (75-150 mm/min). This speed range ensures that enough heat is generated to provide adequate fusion.
What Is the Recommended Power to Shielded Metal Arc Welding?
For most welding purposes, the welding voltage typically ranges from 20 to 80 volts (V), while the current ranges from 30 to 1500 Amperes (A). The recommended power for SMAW depends on the specific welding application and the characteristics of the power source. Power sources for arc welding are designed to transform the power from the grid to controlled values of voltage and current suitable for welding. Different welding processes use different current types, such as direct current (DC), alternating current (AC), or pulsed current. Waveform control/pulse welding, constant current welding, and constant voltage welding are the three types of power sources for welding.
In What Positions Can SMAW Be Performed?
The five welding positions for shielded metal arc welding (SMAW) are flat, horizontal, overhead, vertical-up, and vertical-down. Each position requires speed and technique adjustments to achieve the desired weld quality. The difficulty of defying gravity necessitates a slower travel speed for vertical-up welding in particular. This is so that each subsequent layer of filler metal has enough time to solidify and provide support for the adhesion of the following layer. When working with materials thicker than sheet metal, slowing down the travel speed enhances penetration and fusion. This promotes a stronger and more credible weld joint in vertical-up positions by ensuring that the molten metal has enough time to cool and solidify.
Is SMAW Recommended for Beginners?
Yes, SMAW is often recommended for beginners in welding. It is a relatively simple and versatile process that can be used on a wide range of materials and in various positions. SMAW equipment is also affordable and portable, making it accessible for beginners to practice and gain experience.
Which Metals Can Be Welded With SMAW?
The following metals can be welded with shielded metal arc welding (SMAW):
1. Copper
While SMAW delivers excellent results for steel and iron, welders often avoid this method for aluminum and copper. Welding copper can pose challenges due to its high thermal conductivity and lower melting point compared to steel. However, oxygen-free and phosphorus-deoxidized copper are more easily welded variants. It can be applied to many different things, including heat exchangers, plumbing, and electrical wiring. For more information, see our guide on the Properties of Copper.
2. Stainless Steel
Stainless steel is known for its non-hardenable nature upon cooling, along with its excellent toughness, which usually eliminates the necessity for pre- or post-weld heat treatment. The welding process enables accurate regulation of heat input, ensuring effective fusion and preserving the desired properties of stainless steel. Chromium carbide precipitation may occur during stainless steel welding, potentially impacting its corrosion resistance. However, using filler electrodes with low carbon content and regulating heat input prevent the precipitation of chromium carbide while welding stainless steel. Applying the proper passivation and post-weld cleaning procedures helps to keep stainless steel's corrosion resistance. These steps guarantee successful fusion while preserving the desired characteristics of stainless steel.
3. Tool Steel
SMAW can be utilized to weld tool steel, keeping its elevated hardness, resistance to wear, and toughness if you select the right filler metal and perform the necessary preheat and post-weld treatments. This welding method allows for the repair or alteration of tools, dies, and molds made from tool steel. Nevertheless, certain tool steels incorporate alloying elements such as chromium that can impact their weldability, necessitating preheating and post-weld heat treatment to reduce cracking and preserve the desired hardness.
4. Nickel
Nickel is weldable using SMAW and offers excellent corrosion resistance, high-temperature strength, and thermal expansion properties. Proper joint preparation and heat input control are essential to prevent cracking and produce solid welds. Nickel welding is commonly used in industries such as chemical processing, aerospace, and power generation.
5. Cast Iron
SMAW offers the opportunity to weld cast iron, enabling the mending of cast iron parts or the fusion of cast iron with other metals. While SMAW does involve localized heating, it is important to note that cast iron welding requires specific considerations. These include meticulous preheating, careful electrode selection for compatibility, and post-weld heat treatment to reduce stress, prevent cracking, and achieve optimal results.
6. Carbon Steel
Carbon steel is commonly joined using SMAW due to its simplicity of welding — greatly influenced by its carbon content. Higher carbon content can make welding more difficult due to the increased risk of cracking, while low-carbon steels are typically easier to weld. Additionally, pre-weld and post-weld heat treatments might be required depending on the amount of carbon and the desired weld properties. Proper electrode selection and welding techniques are crucial to guarantee effective welds free of flaws like porosity, cracking, or excessive distortion. For more information, see our guide on What's Carbon Steel?
What Material Thicknesses Can Be Welded With SMAW?
SMAW, or stick welding, is commonly used to weld metal with a thickness of 1/8 inch (3.2 mm) or thicker. While it can be used for thinner materials, it is better suited for thicker sections due to its high heat input and deep penetration capabilities.
Are Shielded Metal Arc (SMAW) Welds Durable?
Yes, the shielded metal arc welding process can produce durable welds. Every weld must be properly designed, taking into consideration the materials to be joined, their thickness, and the kind of loading and corrosion environment that the weld will experience in service. When these factors are considered, the stick welding process can produce robust and reliable joints. This makes it a popular choice in applications where strength and durability are essential, such as construction, infrastructure, and heavy machinery.
What Industries Use Shielded Metal Arc Welding (SMAW)?
The industries that commonly use SMAW include:
- Construction
- Infrastructure
- Shipbuilding
- Automotive manufacturing and repair
- Oil and gas
- Pipeline construction and maintenance
- Structural steel fabrication
- Heavy equipment manufacturing and repair
What Are the Advantages of Shielded Metal Arc Welding (SMAW)?
The advantages of SMAW include:
- Portability and versatility
- Suitability for outdoor and remote work environments
- Cost-effectiveness compared to other welding methods
- Ability to weld a wide range of metals and alloys
- Deep penetration capability
- Ability to weld thick materials
- Minimal equipment requirements
What Are the Disadvantages of Shielded Metal Arc Welding (SMAW)?
The disadvantages of SMAW include:
- Slower welding process compared to some other methods such as gas tungsten arc welding (GTAW) and gas metal arc welding (GMAW)
- Limited efficiency due to high heat loss
- SMAW generates higher levels of welding fumes compared to welding processes such as GMAW and GTAW. SMAW also results in the formation of slag during the welding process.
- Requires frequent electrode changes
- Limited suitability for thin materials due to potential distortion
Is Shielded Metal Arc Welding (SMAW) Costly?
No, SMAW is not generally considered to be costly. The equipment required for SMAW is relatively simple and inexpensive compared to that for other welding methods, such as tungsten inert gas (TIG) welding. Additionally, SMAW electrodes are affordable and widely available, making them a cost-effective choice for many welding applications.
Is It Safe To Use SMAW?
Yes, it is safe to use SMAW when proper safety precautions are followed. In addition to the risks of burns and exposure to harmful fumes, there is also a significant danger to the eyes. SMAW can result in severe eye injuries, including flash burns and long-term damage, due to the intense brightness and ultraviolet (UV) radiation it emits. It is essential to wear the proper eye protection, such as welding helmets or goggles with tinted lenses, to protect against these risks.
What Is the Difference Between SMAW and FCAW?
SMAW (shielded metal arc welding) and FCAW (flux-cored arc welding) are both arc welding processes with some key distinctions. While FCAW uses a tubular electrode filled with flux, SMAW employs a solid electrode coated with flux. This difference allows FCAW to achieve higher deposition rates compared to SMAW. Additionally, a significant disparity is that FCAW can be automated since it can utilize a continuous-feed wire, making it suitable for mechanized and robotic welding applications.
What Is the Difference Between SMAW and GMAW?
Both SMAW (shielded metal arc welding) and GMAW (gas metal arc welding) are arc welding processes. However, the electrode and shielding techniques used in each process vary. While GMAW uses a continuous wire electrode and relies on a shielding gas, SMAW uses a flux-coated electrode and generates liquid slag to protect the molten weld pool.
Summary
This article presented shielded metal arc welding, explained what it is, and discussed its various applications. To learn more about shielded metal arc welding, contact a Xometry representative.
Xometry provides a wide range of manufacturing capabilities, including sheet cutting and other value-added services for all of your prototyping and production needs. Visit our website to learn more or to request a free, no-obligation quote.
Disclaimer
The content appearing on this webpage is for informational purposes only. Xometry makes no representation or warranty of any kind, be it expressed or implied, as to the accuracy, completeness, or validity of the information. Any performance parameters, geometric tolerances, specific design features, quality and types of materials, or processes should not be inferred to represent what will be delivered by third-party suppliers or manufacturers through Xometry’s network. Buyers seeking quotes for parts are responsible for defining the specific requirements for those parts. Please refer to our terms and conditions for more information.
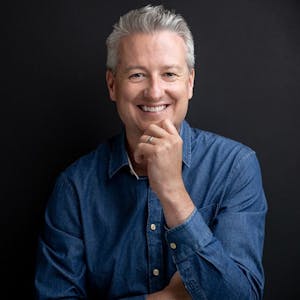