As we see new and innovative technologies disrupt the manufacturing industry, it’s a good time for us to explore how older methods compare—and when both should be used. Two manufacturing processes that usually get weighed up against one another are injection molding and 3D printing, especially since each brings specific advantages, downsides, and budget considerations to the table.
While additive manufacturing has given many engineers and manufacturers pause, it’s not necessarily a solution for all companies’ needs. Here’s how these two compare financially and how they stack up in terms of what they can offer.
What Is Injection Molding?
Injection molding is one type of manufacturing process that works by funneling molten plastic into molds of certain shapes and designs. They cool and you’re left with different parts — which can be pretty complex. This technique gels well with plastics and it’s cost-effective compared to a lot of other methods.
FREE Injection Molding Design Guide
How It Works
- First, the mold is shut and tonnage is applied to both halves or however many sections your mold is split into.
- Then, the plastic (or other material mixture) is heated into a molten hot state and injected into the mold.
- Once the right amount is in, the machine will apply pressure for a set time limit to the mold to make sure the plastic has reached every nook and cranny.
- Then the mold will go through a cooling phase where the plastic shape will harden.
- After it’s hardened and cooled down, the molds will be opened and the object will be ejected and continue on to get processed or finished.
In the diagram below, you can see a drawing of what some injection molding machines look like and how each component fits together.
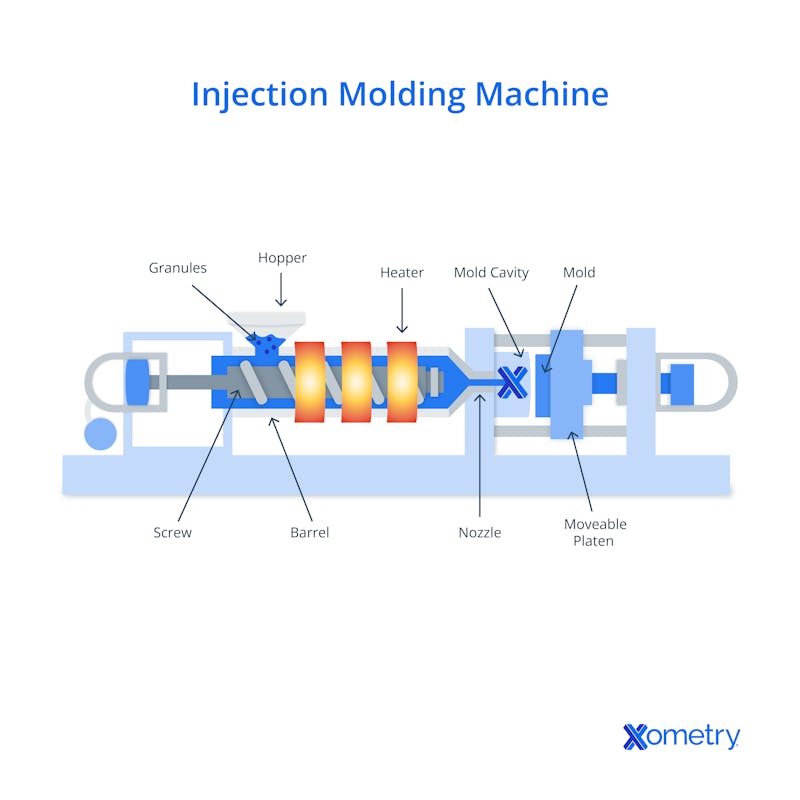
What Is 3D Printing?
This is a large family of technologies that use printers for additive manufacturing—and it’s forever advancing, becoming quicker, easier, and more affordable. It’s possible to make very complex parts and customized components through this layer-by-layer methodology. You can 3D print with almost any material, from plastics and polymers to glass and metal. It’s a popular choice for prototyping as the costs are pretty low once the machinery is taken care of.
How It Works
There isn’t a step-by-step guide that covers all types of 3D printing, as each machine operates differently and has its own way of creating parts. In general, these machines will lay down one layer of material at a time, cure it, and continue layering until the part is fully built.
Pros and Cons | Injection Molding | 3D Printing |
---|---|---|
Pros and Cons Production quantities | Injection Molding Fit for mass production and large-scale orders still made at a high quality. | 3D Printing Not quite to the point where it’s ready for mass production. |
Pros and Cons Design requirements | Injection Molding Stricter guidelines and requirements than 3D printing. Tough to create small quantities with injection molding. | 3D Printing Not as strict guidelines. Easy to iterate and test different designs. Doesn’t require large quantities for production. |
Pros and Cons The process | Injection Molding Makes strong parts, but is an expensive process, and any mistakes are costly and take a long time to fix. | 3D Printing Longer production times but more affordable and capable of creating complex parts. |
Pros and Cons Waste | Injection Molding Minimal | 3D Printing Minimal |
Pros and Cons Aesthetics | Injection Molding Clean, sleek parts | 3D Printing Often rough surfaces that need to be post-processed |
Pros and Cons Applications | Injection Molding Bumpers, dashboards, cup holders, mirror housings, medical devices, pill bottles, X-ray machinery, turbine blades, chassis components, food storage containers, caps, straws, custom construction parts, hand tools, and fasteners. | 3D Printing Aerospace components, robotic parts, dental implants and appliances, prosthetics, prototypes, art, replacement parts, and automotive parts. |
3D Printing vs. Injection Molding Comparisons
Cost Comparison Breakdown
The break-even point hovers between 250 and 2,000 parts when it comes to finding the point at which injection molding and 3D printing are most cost-effective. To give you a better picture, we’ve analyzed a few case studies below. But before jumping into those, you’ll want to heavily consider the following factors when you’re deciding between these two types of manufacturing, as these tend to be the most important:
- Surface design: The bigger the surface area the more you’ll have to pay and the longer it’ll take to create your part when it comes to 3D printing. This isn’t as much of an issue for injection molding.
- Volume order: Like with any manufacturing process, the more volume you have, the less you usually have to pay per part. 3D printed parts tend to be more affordable (around 10% to 20% less) than injection molded parts when you have an order of 20,000 or less. The price seems to be on par when you hit 40,000 to 50,000 parts.
- Tooling costs: When you’re looking at the costs of iterating products, 3D printing comes out on top as far as affordability goes. It’s much more expensive to change the designs (and thus the molds) of injection molded parts.
Now, we’ll take a look at a couple of product production examples we’ve priced out using our Instant Quoting Engine at Xometry. This looks at the cost of creating a drone leg, potentiometer knob, and junction housing and how their prices compare depending on quantity when you 3D print them or create them through injection molding.
Example 1: Drone Leg Pricing
- The bounding box is 146.69 mm x 139.57 mm x 33.00 mm (5.775 in x 5.495 in x 1.299 in).
- The drone’s leg geometry means it'll cost around $32 for one part or $24 per part for 250 parts through selective laser sintering (SLS). HP Multi Jet Fusion is a little less expensive per part after 250 units.
- The price per unit with injection molding hits break-even pretty fast, so scaling is doable and cost-effective. Think $3 per part at quantities over 8,000 — far cheaper than 3D printing.
- After 250 units, it’s better to look at injection molding for speed and cost-effectiveness.
See the graph below to see how different 3D printing methods and injection molding prices compare:
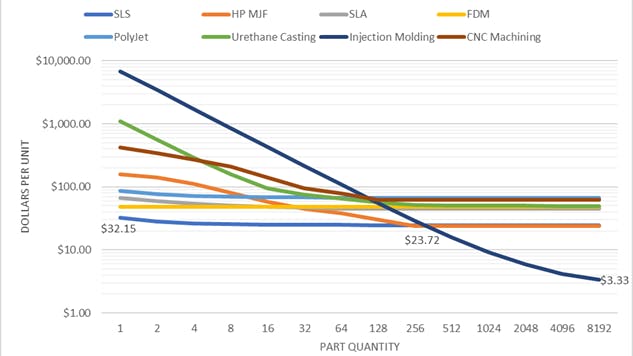
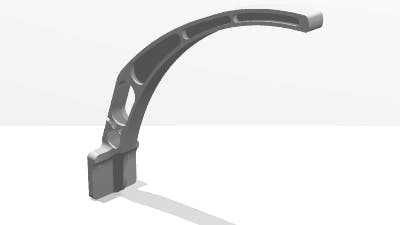
Data results for the per-unit price of the drone leg over doubling quantities from 1 to 8,192 pieces.
Example 2: Potentiometer Knob Pricing
- We’re looking at a potentiometer knob with a bounding box of 16.81 mm x 15.20 mm x 15.20 mm (0.662 in x 0.598 in x 0.598 in)—it’s around the size of a thimble for reference.
- Because it’s so tiny, the cost of 3D printing remains competitive with injection molding until you hit 2,000 units.
- At around 30 units, you’ll want to consider HP MJF printing over SLS. This would equal out to about $3.45 per unit and is great if you’re looking to stick with lower quantities.
- When you need more than 2,000 units, injection molding will save you thousands of dollars, as it costs around $0.80 per unit (without tooling).
Take a look at the graph below, which compares methodologies for making a potentiometer:
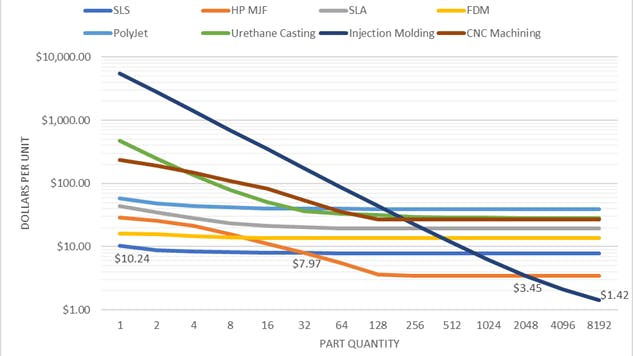
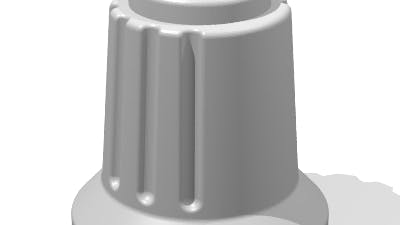
Data results for the per-unit price of the potentiometer knob over doubling quantities from 1 to 8,192 pieces.
Example 3: Junction Housing Pricing
- This example looks at junction housing with a bounding box of 215.84 mm x 172.44 mm x 68.18 mm (8.498 in x 6.789 in x 2.684 in).
- Because junction housing has a pretty large surface area, you’ll get higher costs from the get-go, even with 3D printing. You can expect a little over $200 per part made from nylon with SLS. Then at 30 units, you’ll get a better cost with CNC machining.
- Urethane casting and HP MJF offer better prices between 30 and 250 units, but injection molding ends up being the cheapest if you have a large quantity.
- It can cost around $10,000 in tooling but after 250 units, it’s still cheaper to use injection molding.
Take a look at the graph below for the price breakdown between methods and costs:
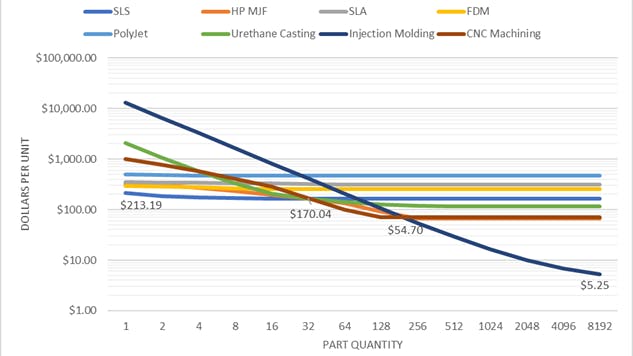
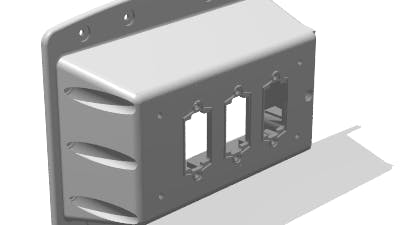
Data results for the per-unit price of the junction housing over doubling quantities from 1 to 8,192 pieces.
How do the costs of injection molding and 3D printing compare?
It will all depend on the quantity of units you’re after and tooling costs, but in many cases, 3D printing is usually cheaper for lower numbers, whereas injection molding cuts the price down significantly at higher quantities. However, if you have a part with a large surface area, 3D printing may not be cost-effective at all, even with fewer units.
Is injection molding additive manufacturing?
Nope—additive manufacturing involves creating a part layer by layer, whereas injection molding involves pushing molten plastic into molds. 3D printing is an example of additive manufacturing.
Disclaimer
The content appearing on this webpage is for informational purposes only. Xometry makes no representation or warranty of any kind, be it expressed or implied, as to the accuracy, completeness, or validity of the information. Any performance parameters, geometric tolerances, specific design features, quality and types of materials, or processes should not be inferred to represent what will be delivered by third-party suppliers or manufacturers through Xometry's network. Buyers seeking quotes for parts are responsible for defining the specific requirements for those parts. Please refer to our terms and conditions for more information.
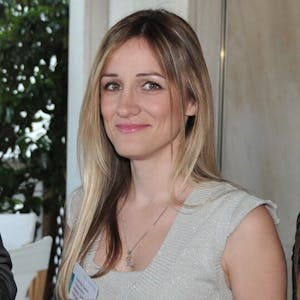