Additive manufacturing / 3D printing are central and accessible capabilities that have transformed the process of creating and evaluating prototypes across all product sectors and markets. These capabilities saw their inception in the later 1980s as a burgeoning range of highly specialized and low-availability processes. The rapid development and extraordinary diversification of this family of techniques have normalized a steady stream of capability and material developments that show no sign of decelerating. But they're not right for every project. Here are 6 alternatives to 3D printing that you could consider.
1. Casting
Several methods of casting can be defined, with varied levels of complexity and tooling. All casting methods use the same basic approach. For metal casting, a cavity of refractory or temperature-tolerant metal is formed by a variety of means. For plastic casting, the cavity material restrictions are less/different, as the temperatures are considerably lower. The chosen material is prepared at a viscosity that is suitable for the process. For a metal charge, the material is melted and cleaned of oxide and detritus (the slag) and degassed to prevent excessive cavity formation. For a plastic charge, either the thermoplastic is melted to an appropriate temperature OR the two-part thermoset material is appropriately mixed and vacuum degassed. The cavity is charged (filled) with the required material. The cooled or cured part is removed from the cavity material, either by cavity opening or by cavity destruction.
The available processes for casting are: sand casting, gravity die casting, pressure die casting, investment casting, plaster casting, centrifugal casting, vacuum casting, squeeze casting, continuous casting, and shell molding.
While all of these can be applied to prototype work, the lowest process costs are associated with single-use cavities and methodologies that require little or no specialist tooling. This generally (but not universally) excludes die casting, centrifugal casting, squeeze casting, and continuous casting from this type of application.
To learn more, see our full guide on What is Casting.
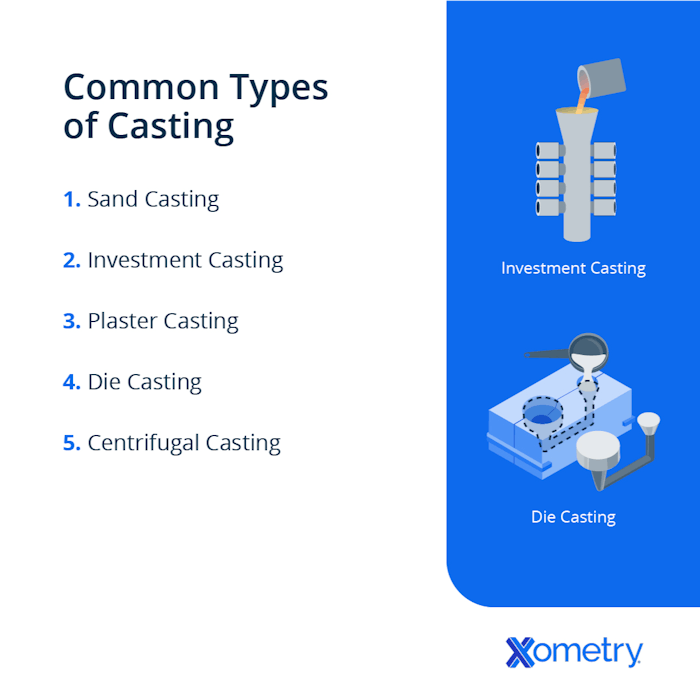
2. Injection Molding
Injection molding is the commonly applied manufacturing process for the production of the majority of plastic products. This includes small and simple components like plastic washers and large and complex parts such as entire car dashboards and bumpers.
Once a part design is finalized, an openable steel (occasionally aluminum) cavity is manufactured. It consists of two halves, referred to as the cavity and the core, which are close to forming the shape of the component. Thermoplastic material is heated to a molten state and then injected into the mold cavity under high pressure. The molten material fills the cavity and cools in place to solidify. The cavity tool is opened, and the finished part is ejected.
Injection molding is best suited to high-volume production, as the cost of tooling is very high relative to the typical value of a one-off plastic part. However, some applications demand prototypes that are closer to real production. Consequently, there is an active market in supply of very low volume injection-molded tools/parts, using a simplified process with typically low cost and very limited service prototype tools. Injection molding is very different from 3D printing, and it is unusual to see true early-stage prototype parts made in that way, as the cost is very high.
To learn more, see our full guide on Injection Molding Plastic.
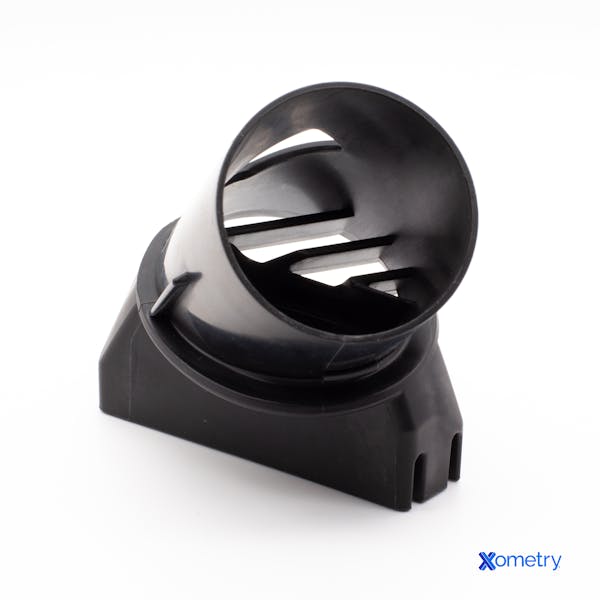
3. Thermoforming
Thermoforming is used to shape thermoplastic sheets into specific forms. It works by softening the material through radiant heat and then using a mixture of pressure and vacuum to pull the material into shape in conformity with a pattern. The source material sheet is heated until it reaches a pliable state, above its glass transition temperature but below its liquefaction temperature. The heated sheet is placed over the male or female mold and vacuum and/or pressure is applied to force the sheet to conform to the shape of the mold. In some cases, an “opposite side” mold is used to assist in close conformity for more extreme shapes. This established forming is held in place as the material cools. Once cooled, the part is removed from the process equipment and the “waste” material of the sheet edge is trimmed off the required part.
Thermoforming is a versatile process used in various industries to produce items such as: packaging, trays, automotive interior trim components, and some medical-device components. It involves low tooling costs in simple and hard-wearing patterns, fast production times, and the ability to create relatively complex shapes with high-quality outcomes.
This process does not relate in any way to 3D printing, being somewhat analogous to casting processes. However, it does offer a rapid and low-cost method for producing relatively precise prototype components in approximately “real” mass-production materials from a large range of available thermoplastic sheet materials. It is one of the few plastic manufacturing processes that allows continuity from one-off prototyping to true mass production without any significant change in tooling or materials.
4. CNC Machining
Computer numerical control (CNC) machining is a subtractive manufacturing process used to produce high-quality, precision parts with tight tolerances and complex geometries. A wide variety of metal, plastic, and natural materials are typically used.
CAD models are translated into machine-readable instructions using computer-aided manufacturing (CAM) software. This process creates a tool path and specifies cutter diameters and operational parameters for feed rate, cut depth, and spindle speed. The most basic CNC machines operate by moving the workpiece in three axes relative to a rotating cutter. More-complex machines also integrate cutter-alignment movements such as tilting the rotational axis. The more sophisticated end of the market can move the cutter and the workpiece in multiple axes to a maximum of 12 distinct motion classes (so far embodied in available machines).
CNC machining of various complexity and adaptability is widely available as a prototype, low-volume, and mass-production process for making simple and complex parts ranging from a custom washer to a gas-turbine combustion chamber. Virtually all product areas can and do exploit CNC machining.
Virtually any material available for mass production can be worked by CNC machining, so plastic parts can represent mass-production components more closely than most 3D printing processes can deliver. Throughput can be considerably faster than 3D printing for relatively simple parts, though production times can approach the same level for both options as part complexity rises. CNC machines of very large format are widely available, whereas 3D printing processes are generally quite limited in build envelope dimensions. “Height” in 3D printing requires a considerable increase in process times, whereas CNC machines can rapidly traverse the Z-axis to deliver taller parts faster. While metal 3D printing processes are rapidly evolving, CNC machining of metal parts retains some distinct advantages in precision and surface finish. Z resolutions in metal 3D printing are generally 0.2 mm at best, whereas CNC can operate at a better tolerance than 0.05 mm if slower processing and shallower cuts can be accepted.
To learn more, see our full guide on the CNC Process.

5. 4D Printing
4D printing is a novel and rapidly evolving process that builds on 3D printing technology by introducing the element of time. It allows printed objects to transform or self-assemble in response to external stimuli such as temperature, humidity, light, or water. While both 4D printing and traditional 3D printing are additive manufacturing techniques, 4D printing differs by offering the extension capability of smart materials to create dynamic and adaptive objects.
The key function of 4D printing is to create dynamic objects that can undergo controlled transformations after being printed, enhancing functionality and adaptability in previously impossible or unimagined ways. 4D printing relies on the use of smart materials, such as shape-memory polymers, hydrogels, electroactive and electrostrictive polymers, and a sector that is becoming known as programmable composites. These materials are precisely programmed during the printing process to achieve specific and planned transformations (such as bending, folding, expanding, or contracting of structures) in response to expected stimuli. Common (and generally experimental) applications of 4D printing include: self-assembling furniture, adaptive infrastructure, medical implants, deployable structures, and soft robotics.
6. Rapid Liquid Printing
Rapid liquid printing (RLP) is a recent innovation in additive manufacturing that enables the rapid production of large-scale, moderate to high-resolution objects by selectively curing liquid material that is precisely dispensed. RLP serves to create large-scale objects with appropriate precision and high speed. It utilizes a variety of liquid materials that are rapidly cured as they are dispensed to form a faithful reproduction of a digital design.
Typically, a multi-axis-capable robotic arm carrying a nozzle dispenses a liquid material, such as photopolymer resin or silicone, onto a build platform. The material is then selectively cured using UV light or a curing method. This process is repeated layer by layer until the object is fully formed. Because of the nature of the applicator process, this type of additive manufacturing is not necessarily lithographic (based on slices) but can be performed regionally across a build.
RLP can work with a variety of liquid materials, including: photopolymers, silicones, and other resin-type materials. It is applied in architecture, automotive, consumer products, and furniture design for producing large-scale prototypes.
While both RLP and more established 3D printing methods are fundamentally similar, RLP offers distinct advantages in terms of speed and scalability. RLP is a complementary technology for the other forms of 3D printing. Unlike traditional 3D printing methods that deposit material layer by layer, RLP enables the rapid fabrication of large objects with smooth surfaces and fine details and less grain bias as the nozzle can dispense in any build direction, increasing anisotropy in the resultant parts.
Considerations When Deciding Whether to Use 3D Printing or Another Technology
Considerations in selecting non-additive-manufacturing processes are typically:
- Whenever 3D metal parts are preferred, CNC machining is the only tooling-free approach with fast lead times. Sand casting, die casting, and forging are good alternatives, but they carry higher establishment and lead-time burdens.
- Whenever plastic components are required and the correct material choice is critical, CNC machining is once again the more rapid and low-cost-setup option, whenever 3D printing cannot serve.
- Whenever plastic parts are required but the stress or temperature issues they’ll face are low, vacuum forming offers a good option with relatively low setup costs and potentially high-quality parts.
- If parts are flat or essentially 2D, laser or abrasive waterjet cutting is effective in processing most materials and carries no setup or tooling costs.
- Whenever a part can be made from 2D components that are fabricated together to produce a 3D part, various construction methods can serve in attaching flat-cut sub-components in metals, plastics, etc.
- If the cosmetic finish of parts is critical, the selection of the initial manufacturing process is usually less critical than the ability to hand or machine finish the required surfaces to a high standard. This can involve grit blasting, sanding, polishing, electroplating, painting, and more, and is generally quite high-cost.
Summary
Xometry provides a wide range of manufacturing capabilities including CNC machining, 3D printing, injection molding, laser cutting, and sheet metal fabrication. Get your instant quote today.
Disclaimer
The content appearing on this webpage is for informational purposes only. Xometry makes no representation or warranty of any kind, be it expressed or implied, as to the accuracy, completeness, or validity of the information. Any performance parameters, geometric tolerances, specific design features, quality and types of materials, or processes should not be inferred to represent what will be delivered by third-party suppliers or manufacturers through Xometry’s network. Buyers seeking quotes for parts are responsible for defining the specific requirements for those parts. Please refer to our terms and conditions for more information.
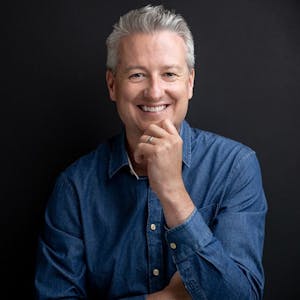