Casting is one of the oldest manufacturing methods known to man, going back around 7,000 years — give or take. The reason it’s still popular today is that it’s simple, efficient, and cost-effective, and it can be used with many different materials. Read on to learn about all things casting.
What is Casting?
Casting is an age-old manufacturing process in which different materials are melted down and poured into molds to set. Engineers and manufacturers use casting to make complex and detailed parts. It reduces production times and costs and simplifies assembly processes because extensive welding or joining isn’t needed—the parts basically come out of the molds ready to go.
Although better suited to small quantities, casting is also successfully used for bulk production and can even make extra-large castings that weigh several tons. In the case of certain metals, like some cast irons, complex alloys, and ceramics, casting is the only processing method available as these materials can’t be mechanically processed.
Casting is often confused with injection molding, but this is a very different process. Both methods use molds but injection molding (as the name suggests) injects the melted material into a mold and uses high pressure to set it. Casting, on the other hand, just uses good old gravity.
There are various casting techniques, and different materials can be used with each one. The process can take anywhere from a few hours to a few days, depending on the material, the casting type, the size of the part, and the number of pieces you want to make.
Types of Casting
There are around 14 different types of casting, but below we look at five of the most popular ones.
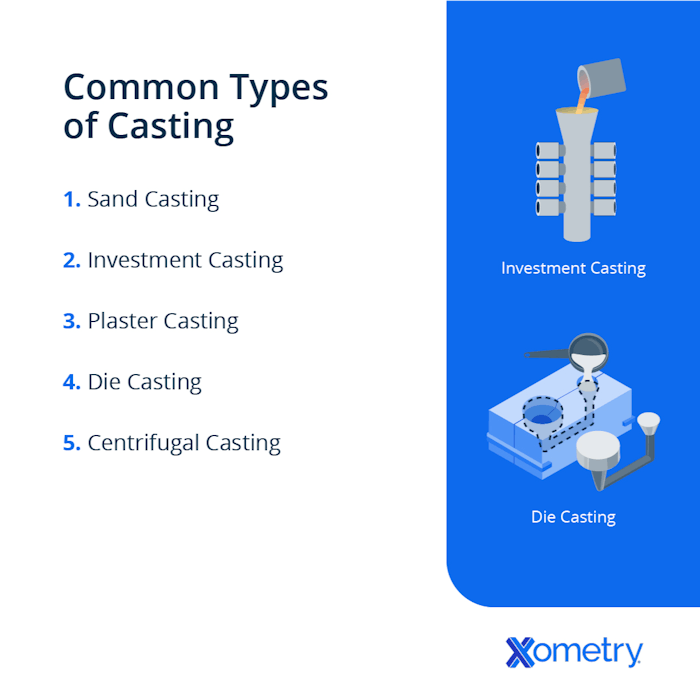
- Sand Casting: Sand casting is one of the oldest types known and has its roots in metal casting. It creates molds with different types of sand (dry/resin) and can even make large parts from ferrous and non-ferrous metals.
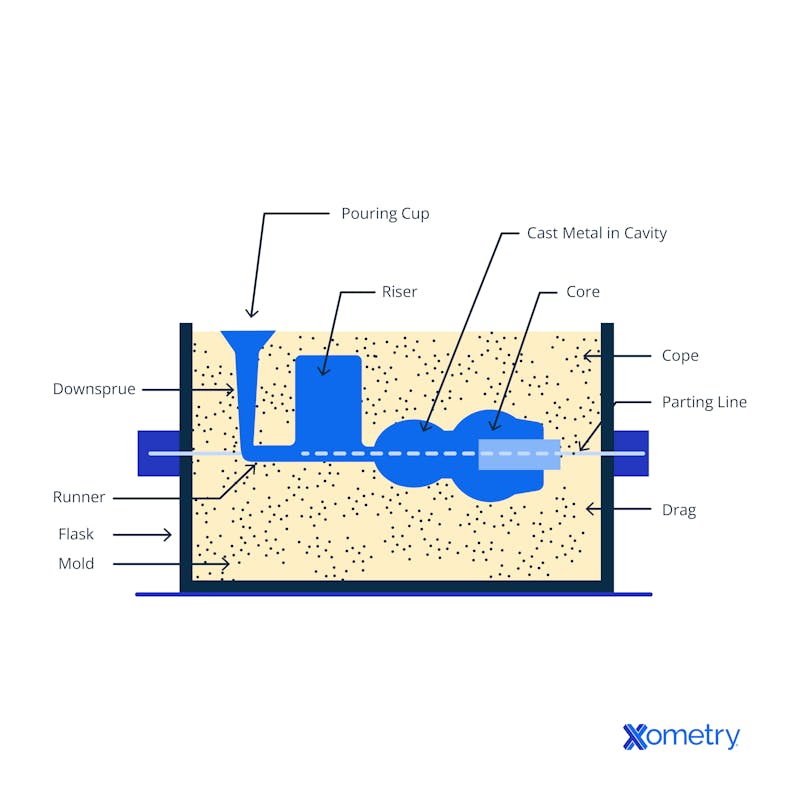
- Investment Casting: This is another super old method that uses wax patterns coated with a heat-resistant material to make the mold. It can make smooth and complex designs with thin walls.
- Plaster Casting: This process uses gypsum (think: drywall), water, and a strengthening material like lime or cement, and is able to make complex shapes with smooth finishes. It’s one of the more expensive types and isn’t compatible with a wide range of materials.
- Die Casting: This casting method involves feeding the liquid metal at high speed and under high pressure into a reusable mold. Methods include gravity die casting, high- and low-pressure die casting, and squeeze die casting. It’s one of the more accurate methods, making it a hit with Xometry die-casting customers.
- Centrifugal Casting: Used to make long, cylindrical parts, centrifugal casting uses molten metal slowly put into a spinning mold. It can be done with water-cooled molds or pressure casting for irregularly shaped parts.
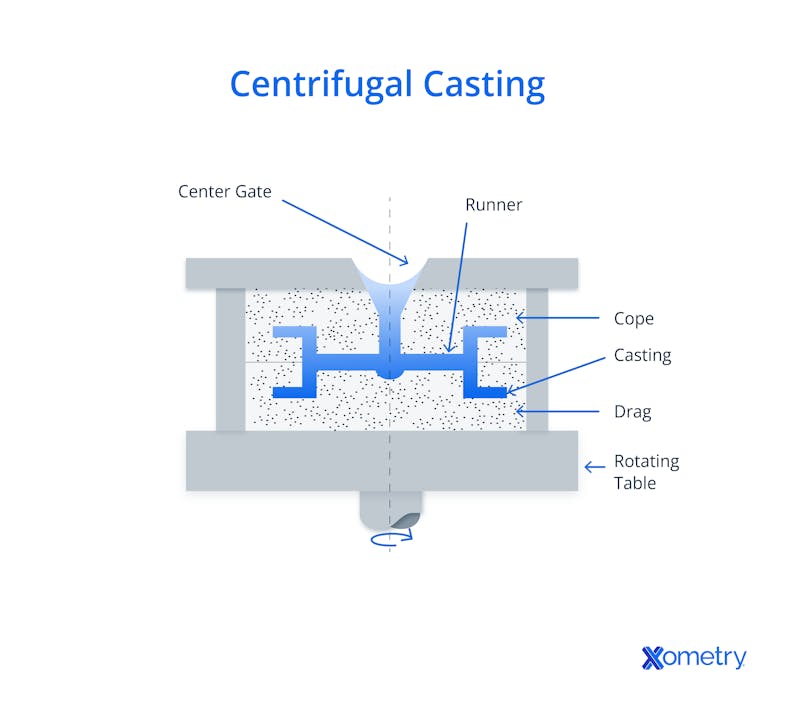
Casting Process
The general premise of casting is putting a melted material into a mold, waiting for it to set, and then taking it out when it’s ready. There are, of course, a few extra steps to the process, which can be different for each casting type. In sand casting, the mold pattern is put in the sand mixture until it hardens to make the mold. When the sand has taken shape, the mold pattern is removed and the mold is ready for use. You’ll then have to melt the metal and pour it into the mold cavity via a gating system.
Metal, like steel or iron, is heated until molten before being poured into the mold cavity through the gating system. It’s then left to cool in the mold, with cooling times differing depending on the metal used. When solidified, the mold is removed, and the newly formed metal casting is revealed. The piece will then undergo processing, cleaning, and any other necessary treatments. Sand cast mold patterns are typically reusable, but the sand molds will need to be remade for each casting.
Casting Materials
Below are some common materials used in casting manufacturing:
Magnesium: This material is lightweight with a good strength-to-weight ratio and is used to make lightweight and durable parts for aerospace and automotive.
Aluminum: Thanks to aluminum’s high thermal conductivity, mechanical properties, and corrosion resistance, parts can be made with many different casting methods. It’s used everywhere from automotive and aerospace to consumer goods.
Iron: This tough metal also has high thermal conductivity and is commonly used metal for engine blocks, pipes, automotive parts, and other load-bearing components.
Zinc: Zinc has a low melting point and offers excellent flow and stability. It is used to make complex or delicate parts in automotive, electronics, consumer products, and many other industries.
Steel: Known for its strength and durability, steel is ideal for making heavy-duty parts, i.e. machinery parts, tools and construction equipment, that need to survive harsh conditions.
Copper alloys: These offer electrical and thermal conductivity and corrosion resistance, making them ideal for use in electrical and plumbing parts, and even music instruments.
Lead alloys: Lead alloys have a low melting point and are malleable. The use of lead is carefully regulated due to its potential environmental and health hazards, but it’s still used in areas like radiation shielding, and battery manufacturing.
Casting Applications
Because it’s versatile, easy, and one of the more cost-effective manufacturing methods, casting is understandably popular in many industries. Products made with the casting method are all around us — tools, accessories, cell phones, appliances, brackets, gears, housings … all cast. In automotive, it’s used to make engine blocks, cylinder heads, transmission cases, and other essential parts. It’s also used for more specialized applications like chemical process equipment (reactors, heat exchangers, pumps), or plant machinery (impellers, casings, and valves).
Casting Limitations
Despite being one of the most reliable manufacturing processes, there are a couple of things to keep in mind when it comes to casting. The equipment and tools needed for many casting processes need to be powerful and durable, meaning they’ll likely need a high initial investment. Also, casting is mainly for metals with lower melting points, so you don’t get such a variety of materials that you can use.
Other issues are casting defects (like porosity), potential shrinkage during the solidification step, which could lead to dimensional inaccuracy, and the surface finish, which may need some additional finishing work. Despite these drawbacks, casting is still a very reliable and efficient manufacturing method for many industrial applications.
How Xometry Can Help
Xometry offers a wide range of manufacturing services. We focus on on-demand precise manufacturing with methods such as die casting, urethane and silicone casting, injection molding, CNC machining, milling, turning, 3D printing, and sheet metal fabrication. To learn more, or get your free quote, please reach out to a Xometry representative.
Disclaimer
The content appearing on this webpage is for informational purposes only. Xometry makes no representation or warranty of any kind, be it expressed or implied, as to the accuracy, completeness, or validity of the information. Any performance parameters, geometric tolerances, specific design features, quality and types of materials, or processes should not be inferred to represent what will be delivered by third-party suppliers or manufacturers through Xometry’s network. Buyers seeking quotes for parts are responsible for defining the specific requirements for those parts. Please refer to our terms and conditions for more information.
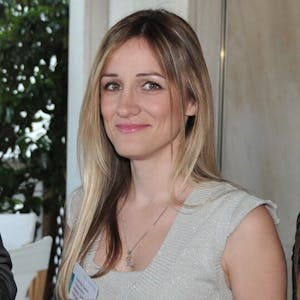