3D printing, also known as additive manufacturing, is highly valued in the aerospace industry. In an industry where reductions in weight or drag can lead to huge cost savings, 3D printing has enabled aerospace manufacturers to create lighter and more fuel-efficient aircraft in a more cost-effective manner. The aerospace industry was one of the first industries to widely adopt 3D printing in the manufacture of key components, and the process has redefined the boundaries of design and manufacturing. Aerospace engineers have been instrumental in the development of certain 3D printing processes, and the industry continues to reap the benefits today as 3D printing matures as a manufacturing process.
From jigs and prototype tooling to end-use parts like nozzles and even rocket bodies, 3D printing in aerospace can be used to both aid the manufacturing process and satisfy particular applications within an aircraft. This article will discuss 3D printing in aerospace, the materials and processes used, and its different applications.
What Is 3D Printing?
3D printing, also known as additive manufacturing, is a manufacturing process that creates parts layer by layer until the entire three-dimensional part is complete. It is the opposite of subtractive manufacturing processes like CNC (computer numerical control) machining, where the material is removed from a workpiece to create parts. 3D printing can be used to manufacture trinkets, simple tools, and advanced components used in several industries, such as aerospace, automotive, medical, machinery, and more. While 3D printing technology has existed since the 1980s, its use has exploded since the start of the 21st century as additive manufacturing has become a sound alternative to produce parts that require several processes to manufacture.
When Did the Aerospace Industry Start Using 3D Printing?
The aerospace industry was one of the first industries to implement 3D printing in the 1990s. Since the inception of 3D printing technology in the 1980s, the aerospace industry has been one of the largest contributors to the development of 3D printing processes and technology. Today, the industry remains one of the largest beneficiaries of the process and accounts for nearly 15%-20% of the total revenue generated by the additive manufacturing industry (depending on the source and market fluctuations).
How Did 3D Printing Start in the Aerospace Industry?
The origin of 3D printing in the aerospace industry dates back to the late 1980s. At the time, the largest benefactors of 3D printing were the US military and the defense industry. These sectors widely used plastics as a cheaper alternative to metals to conduct testing and simulation of various aircraft systems and components.
3D printing was mainly used for prototyping and testing in the aerospace industry until the mid-2000s when it became possible to 3D print flame-retardant plastics through processes like selective laser sintering (SLS) and fused deposition modeling (FDM). As advancements in 3D printing continued throughout the first two decades of the 21st century, its use in aerospace applications expanded. Now, it is used for applications throughout the aerospace component lifecycle, including prototyping and validating designs, tools, jigs for aircraft maintenance, end-use parts in jet engines, and aircraft interiors.
What Kinds of Materials Are Used in 3D Printing for Aerospace Applications?
A number of different materials are used in aerospace industry applications. Common materials used are listed and described below:
1. Ceramics
Ceramics are inorganic, non-metallic materials. They are great for aerospace applications due to their corrosion resistance, lightweight, high-temperature resistance, and wear resistance. However, ceramics are exceptionally hard and brittle, making them difficult to fabricate into parts. Kaolin and porcelain clay are two examples of ceramics that can be 3D printed to make parts. Ceramic 3D printing can be used to make satellite mirror components made from silicon carbide, with the goal of reducing weight and improving the stiffness-to-strength ratio.
2. Carbon Fiber
Carbon fibers are long, exceptionally thin, but strong strands of carbon atoms. Carbon fiber composites are ideal for aerospace applications since they are as strong as steel but lighter than aluminum. This allows manufacturers to improve aircraft performance by integrating 3D-printed carbon fiber parts into aircraft frames and structures. However, carbon fiber is expensive and difficult to produce, which limits the potential applications it can have in the aerospace industry.
3. Metal
Metals are naturally occurring or alloyed materials that are excellent conductors of heat and electricity compared to other materials. Common aerospace metals like aluminum, titanium, and nickel-based superalloys are widely used due to their corrosion resistance and high strength-to-weight ratios. 3D-printed metals are used in engine components, frames, structures, and electronics equipment. A major downside of metals is that they are relatively dense, and excessive use of metal in an aircraft can adversely affect aircraft performance and fuel efficiency.
5. Polymers
Polymers are materials composed of repeating chains of molecules. Common examples of polymers in aerospace include synthetic thermoplastics like Nylon, PEEK, and ULTEM 9085 (a form of polyetherimide). These materials can be used to 3D-print interior components like seatbacks, wall panels, and air ducts. Generally, polymers are great for aerospace applications since they are lightweight and durable. However, polymers are weak compared to metals and cannot be used for high load-bearing applications where metal is often preferred. For more information, see our guide on What Are Polymers.
6. Inconel®
Inconel® is a nickel-chromium-based superalloy valued for its strength at high temperatures and excellent creep and corrosion resistance. In 3D-printing aerospace applications, Inconel® is often used in jet turbine engines to make fuel nozzles. Inconel’s primary disadvantage is that it is an expensive material. For more information, see our guide on What is Inconel Metal.
7. Composites
Composite materials are composed of two or more constituent materials whose properties complement each other. Composite materials have structural benefits such as high strength and low weight, as well as increased wear resistance. Composite materials for 3D printing in aircraft lead to lighter and more structurally resilient aircraft since the desirable properties of different materials synergize. A downside of 3D-printed composite materials is that they can be expensive.
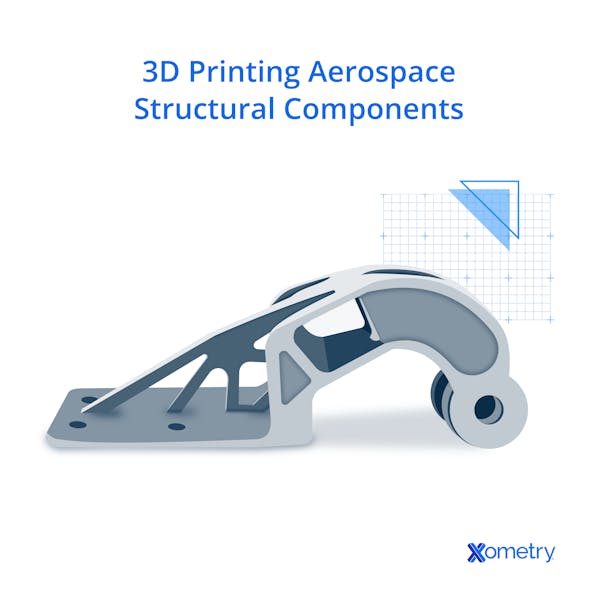
What Are the Steps in the 3D Printing Process in the Aerospace Industry?
3D printing can help validate part design and function and can be used for small-to-medium production volumes. The parts of the 3D printing process as it is used in the aerospace industry are listed and described below:
1. Design
Aerospace designs commonly begin as concept models that showcase a particular aircraft component. Models are created in CAD software and then exported to a 3D-printer-friendly file format like .stl.
2. Preparation
Before a design can be fabricated by a 3D printer, certain preparation work must be completed to ensure optimal print quality. The preparation methods will differ depending on part geometry, the type of 3D printing, and the printer being used. Part models must be configured and oriented in printers in a manner that ensures optimal quality. Additionally, some printers, like FDM (fused deposition modeling) and SLS (selective laser sintering) printers, require the print bed or build platform to be heated before use.
3. Printing
After 3D models are configured as desired and 3D printing systems are properly prepared according to the type of 3D printing and printing machine used, parts can be fabricated. Print times vary from a few minutes to several days, depending on the size of the part and the type of printing used.
4. Post-Processing
When 3D printing is completed, parts can be removed from the build tray. Most 3D printed parts require some post-processing. However, parts printed by one method may require more post-processing than those produced by another method. For example, FDM printed parts often only require support material to be removed while DED (direct energy deposition) printed parts require additional machining processes to obtain desired dimensions.
5. Testing
Once post-processing is completed, the 3D printed part is tested and evaluated. If design modifications are needed, 3D printing enables designers to quickly create and test new designs. When a 3D-printed part’s intended function is satisfied, the part can be 3D printed for small-to-medium batch production or manufactured by more traditional methods.
6. Part Certification
Part certification is a vital step in the aerospace industry to ensure that 3D printed components meet stringent safety, performance, and regulatory requirements. Certification processes can include material testing, mechanical testing, and adherence to aerospace standards such as those from the Federal Aviation Administration (FAA) or the European Union Aviation Safety Agency (EASA). Parts may need to undergo extensive validation procedures to prove their reliability, durability, and performance in real-world aerospace conditions.
Once a part is certified, it can be approved for use in production aircraft and aerospace applications, ensuring compliance with industry regulations and safety standards.
What Are the Different Types of 3D Printing Used in the Aerospace Industry?
There are several different types of 3D printing that can be used in the aerospace industry. These are listed below:
1. Fused Deposition Modeling (FDM)
Fused deposition modeling (FDM) is a type of 3D printing that utilizes an extruded thermoplastic filament to make parts layer by layer. Molten plastic is extruded out of a nozzle onto a build tray. When the first layer cools, the following layer is deposited. This process repeats, layer by layer, until the entire part is complete. FDM printing in aerospace was originally used for prototyping and design verification purposes, but in recent times, it has been used to produce functional aircraft parts.
2. Stereolithography (SLA)
Stereolithography (SLA) is a 3D printing process that utilizes precisely placed photosensitive polymer resin that is cured by UV light to make parts layer by layer. SLA offers very high resolution and is often used to make models for wind tunnel testing.
3. Selective Laser Sintering (SLS)
Selective laser sintering (SLS) is a 3D printing process that precisely sinters and fuses thermoplastic powders to form parts layer by layer. When a layer is completed, more powder is deposited, the build tray descends, and the process repeats. SLS is great for producing parts with complex geometries at high resolutions. SLS 3D printing in aerospace is commonly used for small-batch production of flexible airflow components like air ducts and heat-resistant parts like nozzle bezels.
4. Electron Beam Melting (EBM)
Electron beam melting (EBM) is a 3D printing process that uses electrically conductive metal powder and electron beams to manufacture parts layer by layer. The printing process must occur in a vacuum to prevent gas molecules from interfering with the energy emitted by the electron beam. The electron beam heats the metal powder to extremely high temperatures to melt and fuse it together to form parts. EBM can be used to make metal parts such as engine components.
5. Direct Energy Deposition (DED)
Directed Energy Deposition (DED) is a 3D printing process that uses an energy source such as an electron beam, laser, or plasma arc to melt powder or filament as it is deposited from a nozzle. The process is similar to EBM but does not require a vacuum to be completed. DED printing is commonly used to make metal parts in jet turbine engines and can be used to repair metal parts that have been traditionally manufactured
What Are the Different Types of 3D Printing Machines Used in the Aerospace Industry?
The different types of 3D printing machines used in the aerospace industry are described below:
1. Powder Bed Fusion (PBF) Machines
Powder bed fusion (PBF) machines are 3D printing machines that deposit powders and fuse them together through processes like SLS or EBM. The advantages of PBF machines include the ability to recycle unused powder for future printing processes, a wide selection of plastic and metal materials to choose from, and minimal support needed to produce parts. The disadvantages of PBF machines include the high power requirements to print parts, parts susceptible to thermal distortion, and slow printing time.
2. Fused Deposition Modeling (FDM) Machines
FDM machines are 3D printing machines that create parts by extruding plastic filaments layer by layer. FDM machines have several advantages including low cost, small footprint, and a wide variety of materials available for printing. However, FDM machines also have disadvantages. Parts printed by FDM are prone to warping and are weak in directions perpendicular to the print layers. Additionally, FDM machines are prone to nozzle clogging and frequently require bed calibration.
3. Stereolithography (SLA) Machines
SLA machines are 3D printing machines that manufacture parts by curing photosensitive polymers with a UV-emitting LCD screen or laser. The advantages of SLA machines include the ability to print highly accurate and precise parts, the ability to save unused resin for future print jobs, and the ability to print complex and intricate patterns. However, the disadvantages of SLA machines include high upfront and maintenance costs and resins are not environmentally friendly.
4. Direct Energy Deposition (DED) Machines
Direct energy deposition (DED) machines are 3D printers that produce parts by using a focused heat source such as a laser, plasma arc, or electron beam that melts the powder or filament. The primary advantages of a DED printer are that it allows the grain structure of printed parts to be controlled and enables large parts to be made with little tooling. Disadvantages of DED machines include parts made with poor precision and the need for post-processing to obtain desired dimensions. Additionally, DED machines are expensive and can cost over $500,000, which can be a barrier for many organizations.
5. Continuous Fiber 3D Printing
While FDM can print composite polymers, they tend to use chopped fibers, which diminish the inherent strength found in longer carbon fibers. With continuous fiber 3D printing systems (such as Markforged), the continuous length of carbon fiber is deposited onto the print bed, allowing the final part to retain the strength of bulk carbon fiber. The carbon fiber filament is often coated in a thermoplastic, which is heated as it passes through a nozzle, allowing the carbon fiber filament to bond to the layer before it.
What Types of Applications Are 3D-Printed Parts Used for in the Aircraft Industry?
Listed below are some examples of parts that can be manufactured by 3D printing for the aircraft industry:
1. Engine Components
The materials used for engine components must withstand high mechanical and thermal stresses. Parts like fuel nozzles can be made by 3D printing processes like EBM (electron beam melting) and DED (direct energy deposition). Not only is the production of nozzles using these processes more efficient, but the nozzles themselves are lighter than those made by traditional manufacturing methods. This offers significant positive benefits related to aircraft performance and environmental impact.
2. Structural Components
Structural components are interior and exterior components that help form and support the rigid body of an aircraft. Structural components like brackets and wishbones can be made by 3D printing processes like EBM and DED using titanium, titanium alloys, copper, and nickel alloys.
3. Maintenance and Repair
Maintenance and repair are routinely conducted on aircraft to ensure their safe use and long life. 3D printing methods like EBM and DED can be used to fabricate jigs, fixtures, and tools needed to conduct maintenance and repair on aircraft out of titanium, stainless steel, and copper, among other metals.
4. Interior Components
Interior components in aircraft include everything from avionics equipment to cabin accessories like door latches and light fixtures. FDM (fused deposition modeling) and SLS (selective laser sintering) are two popular methods of 3D printing commonly used to fabricate plastic interior components for aircraft.
5. Prototyping and Tooling
Prototyping and tooling refer to the processes related to designing and testing new design concepts and developing the related tooling. 3D printing is great for creating prototypes and tooling for the aerospace industry due to its ability to make complex parts on demand with little setup work required. This allows for rapid development and testing of new products.
What Are 3D Printed Aerospace Parts?
The following are mechanical aerospace parts that can all be made by 3D printing:
- Fuel nozzles
- Turbine blades
- Housings
- Aerofoils
- Door latches
- Duct work
- Seatback
- Panels
- Trim pieces
- Engine components
- Rocket bodies
- Fuel tanks
- Spacecraft parts
What Are the Advantages of 3D Printing Technology in the Aircraft Industry?
There are several advantages of 3D printing applications in the aircraft industry. They are described below:
- Reduced Weight: 3D printing can be used to replace metal parts with lighter plastic parts. Components produced by 3D printing will reduce the aircraft’s overall weight, which consequently reduces fuel consumption and improves the aircraft’s performance.
- Cost-Effectiveness: 3D-printed parts can be made in far fewer process steps than parts produced by traditional manufacturing processes. This helps reduce overall production costs and waste.
What Are the Disadvantages of 3D Printing Technology in the Aircraft Industry?
There are also several disadvantages of 3D printing in the aircraft industry. Some disadvantages are described below:
- Limited Materials Available: While many widely used plastics and metals are compatible with 3D printing, thousands of alloys and compounds are still incompatible. This fact limits the potential applications of 3D printing in the aerospace industry.
- Weak Part Structure: Some 3D printing methods, like FDM (fused deposition modeling) and SLS (selective laser sintering), produce parts with anisotropic properties (characteristics that differ depending on the direction of an applied load). This can be undesirable for certain load-bearing parts and limits the potential of various 3D printing applications for the aerospace industry.
3. Time-consuming certification process: Aerospace is a safety-driven industry, and new materials and processes must undergo certification and qualification before they can be used on aircraft. This can be both time-consuming and costly.
Who Uses 3D Printing in the Aircraft Industry?
3D printing is used by R&D firms, aircraft manufacturers, and maintenance companies. 3D printing can be used for rapid prototyping of aerospace parts, and small-to-medium batch production of end-use aerospace components, jigs, fixtures, and tools for aircraft maintenance.
What Applications for 3D Printing Technology in the Aviation Sector Might There Be in the Future?
3D printing is a process that continues to impact the aerospace industry positively. It is poised to reduce the negative environmental impact of the aerospace industry, bolster innovation within the industry, and improve both aircraft performance and manufacturing efficiency for years to come. 3D-printed wings and green aviation are just two examples of future 3D printing applications in aerospace.
How Xometry Can Help
Xometry provides a wide range of manufacturing capabilities including CNC machining, 3D printing, injection molding, laser cutting, and sheet metal fabrication. Get your instant quote today.
Copyright and Trademark Notices
- Inconel® is a registered trademark of Special Metals Corporation.
Disclaimer
The content appearing on this webpage is for informational purposes only. Xometry makes no representation or warranty of any kind, be it expressed or implied, as to the accuracy, completeness, or validity of the information. Any performance parameters, geometric tolerances, specific design features, quality and types of materials, or processes should not be inferred to represent what will be delivered by third-party suppliers or manufacturers through Xometry’s network. Buyers seeking quotes for parts are responsible for defining the specific requirements for those parts. Please refer to our terms and conditions for more information.
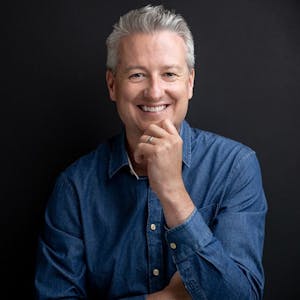