ABS, which stands for acrylonitrile butadiene styrene, is one of the most commonly used 3D printing filaments. It’s used to create plastic parts that have to be strong and hold their own in temperature changes. Let’s go over its composition, uses, and properties, as well as how it fares when compared to other common filaments.
ABS 3D Printing Filament
Most commonly used with fused deposition modeling (FDM) 3D printer models, ABS is a thermoplastic polymer made of the three monomers that make up its name. People saw its usefulness from day one, and it didn’t take very long for this material to gain mass popularity after it was patented (all the way back in 1948). ABS can be found in so many sectors because of how strong, flexible, and moldable it is, making it useful for an array of things from pipes to toys. As far as 3D printing materials go, ABS is machinable, durable, and doesn’t take long to print. It can also withstand hot temperatures, has excellent melt flow, and is resistant to strain and abrasion.
To make ABS, the three main monomers—acrylonitrile, styrene, and butadiene—are polymerized together. Acrylonitrile gives it rigidity, as well as strength and chemical resistance, styrene gives it a smooth and shiny texture, and butadiene is the rubbery element that makes ABS tough. Here’s what the filament looks like:
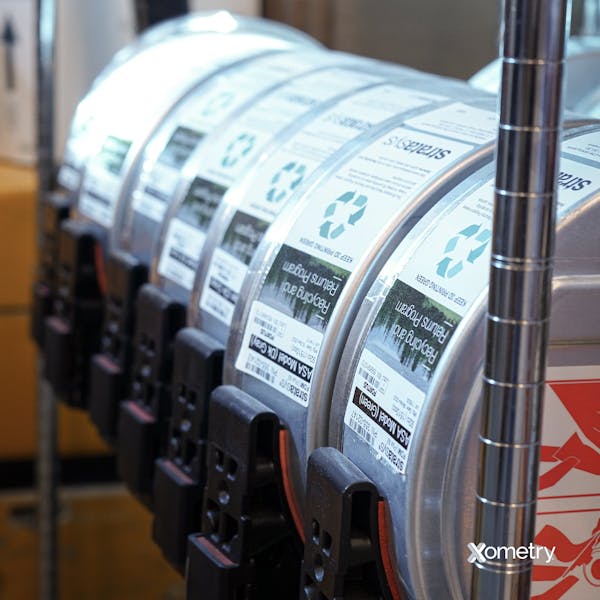
ABS vs. Other Filaments
Other filaments that are similar to ABS include PLA, PLA+, and PETG, but these do have some differences worth knowing about. ABS is a non-biodegradable thermoplastic that’s used for printing end-use parts, as well as functional prototypes and castings. PLA (polylactic acid), on the other hand, is made from biodegradable materials like corn starch and is used for fast projects like showcase models or rapid prototypes. ABS is much stiffer and handles high temperatures much better than PLA, and doesn’t break as easily either.
PLA+ is an enhanced version of PLA. It shares the same basic makeup but has extra additives. It’s made from biodegradable materials and has a narrower printing temperature range (200–230°C) compared to ABS (210–250°C). Also, PLA+ generally produces prints of higher quality compared to ABS. PETG is an adaptation of PET and contains glycol for better strength and durability. One of the main differences between ABS and PETG is that the latter can be used outside because it’s resistant to UV rays—something that ABS isn’t. However, ABS wins in the heat resistance department.
We’ve listed out the properties of ABS, PLA, and PETG in the table below.
Properties | ABS | PLA | PETG |
---|---|---|---|
Properties Impact strength | ABS 200-215 J/m | PLA 26 J/m | PETG 101 J/m |
Properties UV resistance | ABS Average | PLA Average | PETG Better than average |
Properties Density | ABS 1.03-1.14 g/mL | PLA 1.24 g/mL | PETG 1.27 g/mL |
Properties Thermal conductivity | ABS 0.17- 0.23 W/mK | PLA 0.111 W/mK | PETG 0.21 W/mK |
Properties Elongation at break | ABS 10-50% | PLA 7% | PETG 130% |
Properties Yield strength | ABS 2.96-48 MPa | PLA 70 MPa | PETG 50 MPa |
Properties Flexural strength | ABS 2400 MPa | PLA 106 MPa | PETG 70 MPa |
Properties Hardness shore D | ABS 100 | PLA 88 | PETG 106 |
Properties Tensile strength | ABS 2.96-43 MPa | PLA 59 MPa | PETG 53 MPa |
Properties Specific heat capacity | ABS 1.60-2.13 kJ/(kg·K) | PLA 1.590 kJ/(kg·K) | PETG 1.30 kJ/(kg·K) |
Properties Young modulus | ABS 1.79-3.2 GPa | PLA 3.5 GPa | PETG 2.1 GPa |
Comparison of ABS vs PLA vs PETG
The image below is an example of some ABS parts that were 3D printed by the Xometry team:
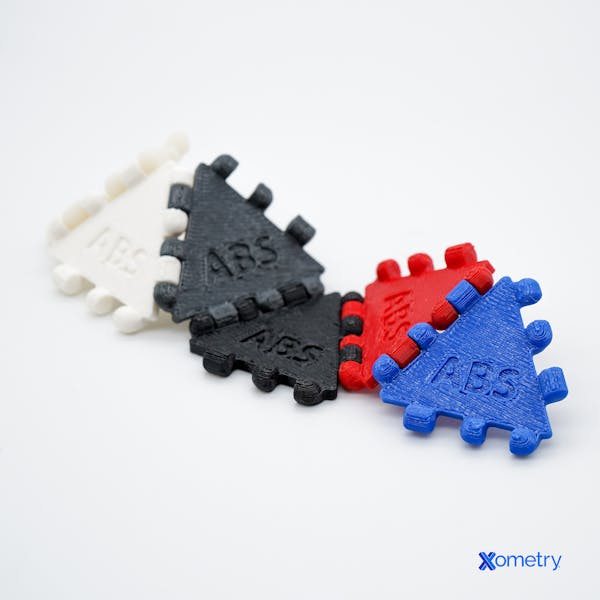
Pros | Cons |
---|---|
Pros Its mechanical properties are great, making it strong and durable | Cons While printing, it releases toxic, and frankly, quite smelly volatile organic compounds (VOCs) |
Pros You can use acetone to easily remove any interface lines between printed layers | Cons When printing with ABS, some layers cool faster before binding with the next layer. Because of this uneven temperature distribution, ABS parts are prone to warping. |
Pros It’s very affordable compared to other materials in its class | Cons If exposed to UV radiation for too long, ABS can become discolored and brittle, so it’s best not to use it outside |
Pros Compared to most inexpensive thermoplastics, it can withstand relatively high temperatures | Cons - |
ABS Pros and Cons
Printer Settings | Value |
---|---|
Printer Settings Extruder temperature | Value 230-250°C |
Printer Settings Bed temperature | Value 95-110°C |
Printer Settings Nozzle Temperature | Value 210-250°C |
Printer Settings Print speed | Value 30-60 mm/sec |
Printer Settings Extruder fan speed | Value Leave the fan off for the first layer. Set it no higher than 30% of maximum speed thereafter. |
Printer Settings Retraction speed | Value 25 mm/sec |
Printer Settings Retraction distance | Value 3-6 mm |
Printer Settings Layer height | Value 0.1-0.2 mm |
Printer Settings Print temperature | Value 220-245°C |
Printer Settings Bed material | Value Glass with glue |
ABS Printer Settings
Tips and Tricks for 3D Printing with ABS
There are certain things you can try to make your experience with using ABS a little easier and safer. Here’s our pick:
- The printer should be located somewhere with a fairly stable temperature. Then, either turn the fan off or all the way down as it can mess up the temperature distribution and end up ruining your print. Also, don’t try to make the cooling process happen quicker—it’ll happen when it happens!
- Before you start the print, put some glue on the printing bed (for printers with heated beds, around 90–100°C is the perfect temperature). The heat and glue will work together to make sure the material doesn’t warp, separate, or any of the other annoying issues you might normally get during printing.
- Keep the printing speed low. That way each layer has some time to cool before the next layer is printed. Corners sometimes tend to lift and separate, so keeping your speed to around 30 mm/s at first and not exceeding 50–60 mm/s can help prevent this.
- Always store ABS in an airtight container because, as a hygroscopic material, it can absorb moisture from the air.
- Keeping your walls thin is a great way to economize your material usage and speed up the printing process, but we don’t recommend making your walls thinner than 1.5mm, even if your part requires flexibility.
How Xometry Can Help
Xometry provides a wide range of manufacturing capabilities, including 3D printing, laser cutting, CNC machining, and much more. ABS 3D printing filament is extremely popular among Xometry customers. If you’d like to learn more about it, or request a free no-obligation quote, reach out to a Xometry representative today.
Disclaimer
The content appearing on this webpage is for informational purposes only. Xometry makes no representation or warranty of any kind, be it expressed or implied, as to the accuracy, completeness, or validity of the information. Any performance parameters, geometric tolerances, specific design features, quality and types of materials, or processes should not be inferred to represent what will be delivered by third-party suppliers or manufacturers through Xometry’s network. Buyers seeking quotes for parts are responsible for defining the specific requirements for those parts. Please refer to our terms and conditions for more information.
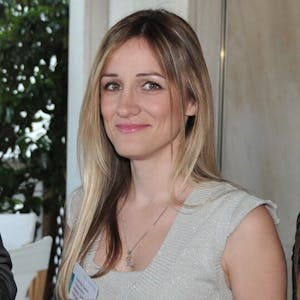