Both of these methods are types of 3D printing. SLS stands for selective laser sintering, and FDM stands for fused deposition modeling. They share a number of similarities. For instance, they’re both used in lower-volume production and rapid prototyping, both use thermoplastic materials, and they’re great for making proofs of concept. But they’re quite different in other areas. In this article, we’ll look at how they differ and when you might want to use either one.
What is SLS?
Developed in the mid-1980s at the University of Texas in Austin and funded by the U.S. Department of Defense, SLS has become one of the most standard methods of 3D printing, with many companies using the same basic technology to manufacture and sell their own machines. These printers usually use a CO₂ laser that selectively sinters and bonds together thermoplastic polymer powder—usually nylon or something similar. When each layer is finished, the print bed will go down, another batch of powder is applied, and the process starts again. When the part is finally complete, it needs to cool down—which could take up to 12 hours—and be cleaned with compressed air or some other form of blasting media.
SLS tends to work out more expensive than FDM, but its parts come out with higher resolutions, amazing mechanical properties, and accurate complex designs. We have an article on SLS which you can check out to find out more. The image below shows one of our SLS 3D printing stations here at Xometry:
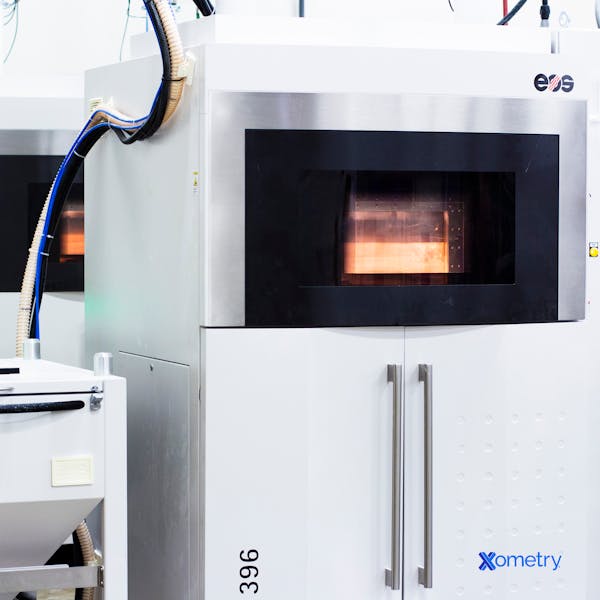
SLS has lots going for it. For instance, aside from being good at making prototypes, it can make parts for end-users too. Also, parts don’t need support structures during printing, the process is quick, and unsintered powder can be reused and recycled. On the downside though, SLS printers are usually only used in industrial settings, so getting hold of one could take a while. What’s more, they have a moderately limited selection of materials (mainly polyamides), and some parts with large, flat surfaces and small holes could warp or be over-sintered.
What is FDM?
The most traditional form of 3D printing today, FDM was developed in the late 1980s, and once its patents expired in 2009, companies jumped at the opportunity to make their own. Since then, it’s become a staple in the 3D printing space and even found in many homes.
Like SLS, FDM uses thermoplastics, but in the form of a filament that’s poured out onto the print bed through a hot nozzle. When each layer is printed and cooled down, the nozzle gets started on the next, until eventually the part is complete. FDM is way cheaper than SLS and is the perfect starting point, even for hobbyists. To learn more, head on over to our article on FDM printing. This is one of our industrial FDM 3D printers here at Xometry:
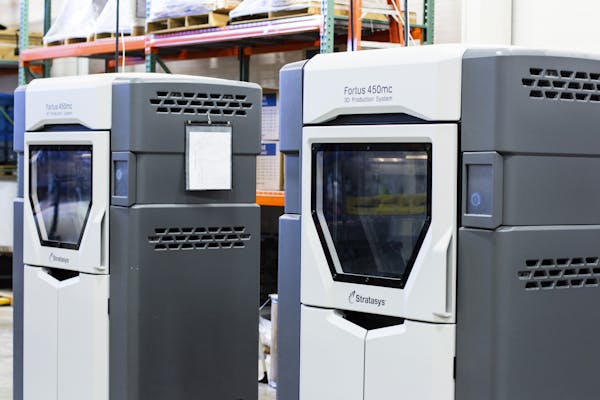
FDM printers are generally easy to use, which is why many hobbyists love using them as a starting point. You can even get hold of rather large FDM machines, which allow you to print parts up to a few feet wide. On the flip side, though, they don’t have as high a print resolution as SLS printers do, so don’t expect perfection on small or detailed parts. They can also be quite slow, and the prints will require support structures during printing. Matthew Schmidt, a Senior Solutions Engineer here at Xometry, says, "SLS and FDM process are common in the respect that they both utilize real thermoplastic feedstock, however, the deposition process is much different. Selective Laser Sintering (SLS) provides a more dense, homogenous and isotropic part due to its laser melting process, but only from a limited number of Nylon derived materials. FDM on the other hand has a less dense, but unique contour and raster extrusion deposition process that can accommodate many different thermoplastics in different colors."
Attribute | SLS | FDM |
---|---|---|
Attribute Technology | SLS More complex | FDM Simple |
Attribute Materials | SLS Mainly nylon, like PA11 and PA12, with some filled variants available | FDM Wide range of thermoplastics, like PLA, ABS, and polycarbonate |
Attribute Prototyping | SLS Good for complex and functional prototypes, as well as mass-production | FDM It’s fine for simple prototypes |
Attribute Print Volume | SLS Up to 13”x13”x20” (Usual) | FDM Up to 24”x36”x36” (Usual) |
Attribute Surface Finish | SLS Generally good, even without post-processing | FDM Slightly rough, like a stair-stepping effect |
Attribute Cost | SLS Typically between $10,000 and $100,000 or more | FDM From a few hundred dollars to over $15,000 for industrial FDM printers |
SLS vs. FDM Attributes
* The suitability of one technology over another can depend highly on your projects unique specifications and needs. Consult with Xometry about your project to determine the best solution.
Frequently Asked Questions on SLS and FDM
Are there any mutual alternatives to both of these?
Of course. Some of the most suitable alternatives are SLA (stereolithography) and DLP (digital light processing). Both of these use photopolymers, which are special resins that are cured using a UV laser in SLA machines, and a light projection in DLP machines. They both work layer-by-layer until the part is built and cured.
What’s the difference between SLS and MJF?
MJF stands for multi-jet fusion, and similar to SLS, it fuses powder to build up each layer. But unlike SLS, it uses an inkjet-style print head to deposit the fusing agent onto the sections of powder it needs to harden. It then projects infrared light onto the entire area to bond the treated powder together, and because of this, MJF is way faster than SLS. You can check out our article on SLS vs. MJF to find out more.
What’s the difference between FDM and FFF?
FDM is often compared to (FFF), which stands for fused filament fabrication. It uses the same process as FDM in that a heated nozzle or extruder will deposit layers of filament onto the print bed. But, unlike FDM, FFF doesn’t have a heated chamber that helps control the temperature. Why not read our article on FDM vs. FFF to learn more about this comparison?
How Xometry Can Help
We’ve covered a lot in this article, but if you still have any questions relating to these methods or general 3D printing, one of our representatives would be happy to help you. Xometry also offers a plethora of manufacturing services in addition to 3D printing, like CNC machining, laser cutting, and powder coating, to name just a few. You can request a free, no-obligation quote today to get started.
Disclaimer
The content appearing on this webpage is for informational purposes only. Xometry makes no representation or warranty of any kind, be it expressed or implied, as to the accuracy, completeness, or validity of the information. Any performance parameters, geometric tolerances, specific design features, quality and types of materials, or processes should not be inferred to represent what will be delivered by third-party suppliers or manufacturers through Xometry’s network. Buyers seeking quotes for parts are responsible for defining the specific requirements for those parts. Please refer to our terms and conditions for more information.
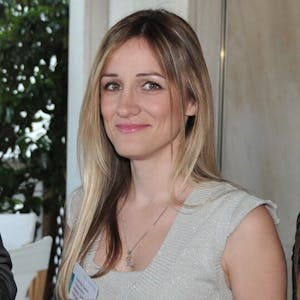