Bulk modulus is a measure of a material’s decrease in volume with an increase in pressure. This measurement can assess gases, liquids, and solids. Any volume of material can be squeezed while preventing it from bulging out, off the axis of compression. This results in equal pressure being applied in all directions, resulting in compression. Gases are highly compressible, liquids and solids are thought of as incompressible, whereas in reality, they're just really hard to compress. This article will further define bulk modulus, how it works, and its formula, provide some examples, and list the benefits of having this value on hand.
What Exactly Is Bulk Modulus?
Bulk modulus measures the change in volume of a material sample, either by compression or extension, as a function of the applied load. For gases, the “tensile” loading is easily applied by using force to increase the volume of the gas in a sealed chamber. For solids and liquids, this is less practical, so the modulus is validated using compressive loading only. The harder-to-perform “tensile” or elastic expansion test has been used to confirm that the bulk modulus in tension is identical to the bulk modulus in compression.
This tension/compression equivalency only breaks down when the elastic limit is exceeded and a yield point is reached. In general, compressive yield (in a volume-constrained part) is considerably higher than the tensile equivalent. Where the part is not effectively volume constrained (i.e., the sample is allowed to bulge perpendicularly to the applied force), the failure mode and yield point are encountered at considerably lower loads, as perpendicular strains are much greater in this squash-necking distortion mode.
How Does Bulk Modulus Work?
Bulk modulus works when the entire load is converted into a pure volume change. A load is applied to a fixed volume of material that is constrained from shape changes other than by compression. In general, the bulk modulus is derived from the single-axis loading of a shape-constrained cylindrical sample in a load cell. Measuring the axial motion of the load application easily converts to a volumetric change which results solely from the compression.
The applied load is measured in the load cell. The system hysteresis (“taking up of the slack”) is dismissed and a plot of force against plunger travel distance is produced. In general, the relationship between machine travel (strain) and applied load (stress) is a linear one to the limits of elastic compressibility, after which yield becomes partially permanent deformation.
What Is the Importance of Bulk Modulus?
Bulk modulus is a critically important measure of the elasticity of materials. For solids such as metals, polymers, and 3D prints, it is extremely valuable in helping to design components and systems that both function as required and survive the expected conditions they will experience in real-world applications. It is useful in predicting the elastic behavior of materials and potential density changes under load, and potentially in surmising the atomic structure of a material sample.
What Are the Uses of Bulk Modulus?
Bulk modulus is used for the following:
- Specify material selection for particular applications.
- Ensure the elastic performance of stressed components is sufficient for the purpose.
- Aid in the design of parts to increase shape constraint of loaded components to better use their volumetric elasticity, reducing the “burst” or “neck” risk.
- Identify aspects of the crystalline structure of materials.
How Important Is Bulk Modulus in 3D Printing?
The “bulk” behaviors of 3D printed parts are highly dependent on construction methods, in some cases much more than on native material properties. For example, the overwhelming majority of 3D prints are produced by FDM. This approach results in systematically open and porous structures, with porosity present even at the highest density build patterns. This renders the materials epitaxially structured and the behaviors much more complex than for a shape-constrained solid. Internal distortion ability changes the properties from essentially material (in a constrained solid) to essentially structural, as air spaces reduce all constraints.
Bulk modulus can be calculated/tested for some 3D printed parts, where porosity is low and general properties are isotropic (same in all directions). Examples that are closer to this nature are listed below:
- Material jetting, where most “grain” from build orientation is subsumed in the wet build—and porosity is very low.
- Many powder-sintered metal prototypes such as MetalX, in which the sintering removes most porosity, alleviates the construction structures, and increases isotropic characteristics.
- SLS plastic systems that offer intrinsically low porosity and highly isotropic mechanical properties.
For more information, see our guide on 3D Printing.
What Is the Formula of Bulk Modulus?
The formula of bulk modulus expresses the relationship between pressure increase and the resultant decrease in volume, which is elastic compression of the material sample. It is stated in the equation below:
K = P / ε (Pascals)
Where:
- P = Pressure applied (Pascals)
- ε = Volume strain (dimensionless)
- K = Bulk modulus (can also be denoted as B)
Volume change denoted as:
Vo (original volume) - Vc (compressed volume) (l or ml)
Volume strain:
ε = (Vo - Vc) / Vo
Other approaches to calculating bulk modulus are also used.
What Is the Bulk Modulus K?
Bulk modulus is widely denoted as K in scientific notation. which has other (related and unrelated) meanings. It is also denoted as B, which is equally open to misinterpretation as other measured and constant scientific properties.
What is the Bulk Modulus B?
Bulk modulus is also denoted as B, commonly but less so than K.
How to Calculate Bulk Modulus?
For a typical polyurethane sample, to illustrate the calculation:
- Pressure applied P = 12 MPa
- Volume strain ε = 0.75
K = P / ε = (12 x 106) / 0.75 = 16 MPa
What Is the Unit of a Bulk Modulus?
Bulk modulus has units of pascals, Pa, MPa, or GPa.
What Is an Example of the Bulk Modulus of a Material?
The bulk modulus of steel is around 140 GPa or 2.03 x 107 psi.
What Are the Benefits of Bulk Modulus?
The primary benefit of understanding the relative bulk moduli of materials is that it helps in product design, materials selection, and in design for load tolerance and factor of safety issues.
What Are the Limitations of Bulk Modulus?
The limitation of the bulk modulus is that it is not a tangible or real-world meaningful measure, so it is most useful for comparisons of materials. Variations in real behavior are significant, compared with rigorous laboratory testing of the bulk modulus. This is because real-world parts are rarely as perfectly shape constrained as in bulk modulus testing. Bulging and shear can often distort the apparent bulk elastic behavior, as parts change shape under load.
What Is the Bulk Modulus of Water?
The bulk modulus of water is 2.1 GPa or 3.0 x 105 psi.
What Is the Bulk Modulus of Steel?
The bulk modulus of typical steel is around 140 GPa or 2.03 x 107 psi.
What Is the Bulk Modulus of Polymer?
Polymers range widely in bulk modulus, both within a classification and between polymer families. Note that butadiene rubber has among the highest bulk modulus of all polymers, despite being easy to distort and highly elastic. For more information, see our guide on Polymer.
Table 1 below shows some examples of bulk modulus of common polymers:
Polymer | Bulk modulus (GPa) |
---|---|
Polymer PVC (polyvinyl chloride) | Bulk modulus (GPa) 2.41–4.14 |
Polymer Nylon 66 | Bulk modulus (GPa) 1.59–3.79 |
Polymer PC (polycarbonate) | Bulk modulus (GPa) 2.38 |
Polymer PS (Polystyrene) | Bulk modulus (GPa) 2.28–3.28 |
Polymer LDPE (low-density polyethylene) | Bulk modulus (GPa) 1.08 |
Polymer PET (polyethylene terephthalate) | Bulk modulus (GPa) 2.76–4.14 |
Polymer PP (polypropylene) | Bulk modulus (GPa) 1.14–1.55 |
Polymer Butadiene rubber | Bulk modulus (GPa) 5.5 |
Table Credit: https://www.sonelastic.com/
What Is the Reciprocal of Bulk Modulus?
Bulk modulus for a material defines its resistance to compression. Therefore the reciprocal of bulk modulus defines the compressibility of the material.
What Is the Relationship Between Bulk Modulus and Compressibility?
Bulk modulus and compressibility are the inverses of each other. Bulk modulus is described as the reciprocal of compressibility. A material that is easily compressed has high compressibility but a low bulk modulus. On the other hand, a material that is difficult to compress has a large bulk modulus but a small compressibility.
Are Bulk Modulus and Volume Elasticity the Same?
Yes, bulk modulus and volume elasticity are the same. Volume elasticity is simply another term for bulk modulus.
What Is the Difference Between Bulk Modulus and Young's Modulus?
Bulk modulus describes the behavior of a material in three dimensions, i.e., the resilience or resistance to volumetric change under load. Young's modulus, on the other hand, is a much narrower and more specific characteristic, in that it defines the tensile elasticity of a material when loaded on a single axis.
Summary
This article presented bulk modulus, explained what it is, and discussed how to calculate it and its importance. To learn more about bulk modulus, contact a Xometry representative.
Xometry provides a wide range of manufacturing capabilities, including 3D printing and other value-added services for all of your prototyping and production needs. Visit our website to learn more or to request a free, no-obligation quote.
Disclaimer
The content appearing on this webpage is for informational purposes only. Xometry makes no representation or warranty of any kind, be it expressed or implied, as to the accuracy, completeness, or validity of the information. Any performance parameters, geometric tolerances, specific design features, quality and types of materials, or processes should not be inferred to represent what will be delivered by third-party suppliers or manufacturers through Xometry’s network. Buyers seeking quotes for parts are responsible for defining the specific requirements for those parts. Please refer to our terms and conditions for more information.
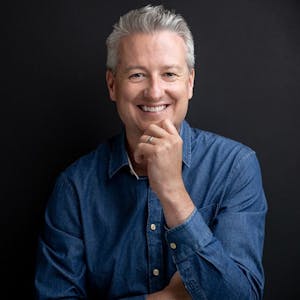