4130 steel is a low-carbon alloy steel. It stands out from other steels as it has a high chromium and molybdenum content which reinforces the steel making it stronger whilst also improving its corrosion resistance. 4130 steel is used, as many sheets of steel are, for structural applications as well as cutting and milling tools, fasteners, aircraft landing gear, and in resistance welding.
What Is 4130 Carbon Steel?
4130 carbon steel is a low-carbon steel with a carbon content of around 0.3%. 4130 is also an alloying steel that uses chromium and molybdenum as strengthening agents. This steel is easy to weld and responds better than other lower low-carbon steels for heat treatment. The presence of a high level of chromium increases the resistance to corrosion, wear, and abrasion. The hardenability is also increased due to the chromium content. The molybdenum in 4130 steel improves the steel’s resistance to creep. For more information, see our guide on Carbon Steel Properties.
What Is 4130 Carbon Steel Used For?
4130 steel is most prominently used for structural applications. However, with heat treatment, the steel becomes exceptionally tough and exhibits great workability and machinability. These characteristics mean that 4130 steel is also used in applications such as: mills and cutters, drill bits and taps, bearings, landing gear for aircraft, and mounts for aircraft engines. 4130 steel is known as steel with high corrosion resistance, a high strength-to-weight ratio, and good machinability and weldability. Due to these properties, 4130 is used in aircraft and automotive construction, structural frames, and fasteners for ships, bridges, and buildings.
How Is 4130 Carbon Steel Made?
4130 carbon steel is made by mixing the molten metals together and then hot rolling them. This process is similar to most carbon steels, and the only real difference is the chemical composition.
Initially, pig iron is melted in an electric furnace at above 2,600 °F with coke. It remains molten while the impurities burn off. Oxygen is pumped through the melted iron which oxidizes the iron, removing the carbon. The correct levels of alloying elements can then be added to the iron. After they are added, the steel can be solidified into steel ingots ready for hot rolling or cold drawing.
What Is the Chemical Composition of 4130 Carbon Steel?
The main element of 4130 steel, as with any steel, is iron at approximately 98%. Two other major alloying elements in 4130 steel are chromium at around 1% and manganese at 0.6% Table 1 shows the full chemical composition of 4130 steel:
Element | Percentage |
---|---|
Element Iron | Percentage 97.03%–98.22% |
Element Chromium | Percentage 0.8%–1.1% |
Element Manganese | Percentage 0.4%–0.6% |
Element Carbon | Percentage 0.28%–0.33% |
Element Silicon | Percentage 0.15%–0.35% |
Element Molybdenum | Percentage 0.15%–0.25% |
Element Sulfur | Percentage < 0.04% |
Element Phosphorus | Percentage < 0.035% |
What Is the Carbon Content of 4130 Carbon Steel?
The carbon content of 4130 steel is between 0.28% and 0.33%. Steels less than 0.3% carbon are considered low-carbon steels. Low-carbon steels are renowned for their ductility, malleability, and weldability. However, they have a lower strength-to-weight ratio and less corrosion resistance than high-carbon steels.
What Are the Properties of 4130 Carbon Steel?
Listed in Table 2 below are the properties of 4130 carbon steel:
Property | Value |
---|---|
Property Density | Value 0.284 lb/in^3 |
Property Yield Strength | Value 63,100 psi |
Property Hardness | Value 92 Rockwell |
Property Magnetism | Value Ferrous magnetic |
Machinability Rating of 4130 Carbon Steel
The machinability rating of 4130 steel is 70% when annealed. This means that 4130 is easy to machine and won't wear out tools excessively fast. It is suggested that generic carbide tooling is used to cut this steel. For milling, the advised cutting rate is 520–710 SFM (Surface Feet per Minute), and for turning 840–1,150 SFM.
What Are the Thermal Properties of 4130 Carbon Steel?
The melting point of 4130 steel is 2,610 °F. The thermal conductivity of 4130 steel is 296 BTU-in/hr-ft2-F. The specific heat capacity of 4130 steel is 0.114 VTU/lb-°F and it has a rate of thermal expansion of 6.2 * 10-6 in/i(in/°F).
What Are the Common Forms of 4130 Carbon Steel Material?
Some of the common forms of 4130 carbon steel are listed below:
Sheet
The sheet metal form of 4130 steel will have a thickness of between 0.018–0.250”. 4130 steel in sheet form is generally used for bodywork panels or to create walls/bulkheads or tanks.
Bar
The bar form of 4130 steel is used to produce parts under high stress, including: pumps, valve bodies, fittings, and chassis.
Plate
A plate of 4130 steel will be of a thickness greater than 0.250”. The plate form of 4130 steel has uses in the automotive, aerospace, construction, cycling, and firearms industry.
Hot Rolled
Hot rolling of 4130 steel should take place at temperatures between 1,500–2,000 °F. The hot rolling of 4130 steel will strain the steel's microstructure and create dislocations. The resultant increase in dislocation density strain hardens the steel, creating a harder and stronger steel.
Annealed
Annealing of 4130 steel should be done at 1,500 °F. The process of annealing, which involves heating the steel to a set temperature and then cooling slowly, will recrystallize the grain structure and remove internal stresses from the steel. By heating the steel to below its melting point, new crystals will start to form. The growth of these new crystals is controlled by controlling the rate of cooling. Annealing the steel will remove impurities, and reduce the brittleness and hardness of the steel.
Cold-Drawn
The cold drawing of steel should happen at ambient temperatures. Cold drawing of steel is much more dimensionally accurate because there is no change in size due to thermal expansion. The process of cold drawing is used to create bars, tubes, wires, and spindles. The cold-drawn form of 4130 steel will be much stronger and harder than the hot-rolled version. However, the cold rolling process is more labor intensive, so the end product is also more expensive.
What Are Equivalents of 4130 Carbon Steel?
Table 3 below lists the 4130 equivalent standards of steel for other countries, it should be noted that not all standards will be exactly equal and will likely differ slightly in chemical composition and therefore properties:
Country standard | Equivalent grade |
---|---|
Country standard European (EN) | Equivalent grade 25CrMo4 |
Country standard Germany (DIN) | Equivalent grade 25CrMo4 |
Country standard Japan (JIS) | Equivalent grade SCM430
Or
SCM420 |
Country standard France (AFNOR) | Equivalent grade 25CD4 |
Country standard England (BS) | Equivalent grade 708A25
Or
708M25 |
Country standard Italy (UNI) | Equivalent grade 25CrMo4 |
Country standard Russia (GOST) | Equivalent grade 20KHM
Or
30KMH |
What Are the Advantages of Using 4130 Carbon Steel?
One big advantage 4130 has over other steels is that it is more corrosion-resistant. This is due to its high chromium content. Additional advantages of using 4130 steel over other steels are:
- It is dimensionally stable at high temperatures
- Has a high strength-to-weight ratio
- Has a high elastic modulus
- Has low carbon content which makes it easy to weld
What Are the Disadvantages of Using 4130 Carbon Steel?
Listed below are some disadvantages of using 4130 carbon steel:
- It can not be aged
- Due to the range of alloying elements, it is more expensive
- It can be difficult to form
What Is the Difference Between 4130 Carbon Steel and A514 Steel?
Comparing 4130 steel to A514 steel, A514 has the addition of boron and vanadium and 4130 does not. The addition of boron increased the hardenability of steel. While vanadium increases the hardenability of steel it also improves corrosion resistance and creep resistance. A514 is much stronger and harder than 4130 steel. However, 4130 steel is much more machinable with a 70% rating when compared to 1212 carbon steel as a baseline. A514 however, has a machinability rating of 40%.
Summary
This article presented 4130 carbon steel, explained it, and discussed its various applications and properties. To learn more about 4130 carbon steel, contact a Xometry representative.
Xometry provides a wide range of manufacturing capabilities and other value-added services for all of your prototyping and production needs. Visit our website to learn more or to request a free, no-obligation quote.
Disclaimer
The content appearing on this webpage is for informational purposes only. Xometry makes no representation or warranty of any kind, be it expressed or implied, as to the accuracy, completeness, or validity of the information. Any performance parameters, geometric tolerances, specific design features, quality and types of materials, or processes should not be inferred to represent what will be delivered by third-party suppliers or manufacturers through Xometry’s network. Buyers seeking quotes for parts are responsible for defining the specific requirements for those parts. Please refer to our terms and conditions for more information.
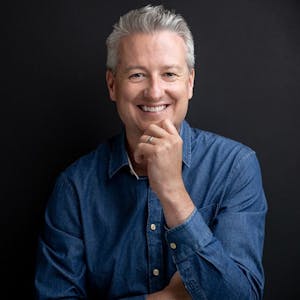