Sure, it’s possible to buy 4140 steel in its plain state, but you’ll find that its pre-hardened version makes a good case for why manufacturers should buy it instead. Mostly, this is because it’s harder and tougher thanks to its pre-treatment. Aside from these characteristics, it also brings a high tensile strength to the table. Here’s why it’s worth considering, and other important info you should know about working with this particular steel alloy.
What Is 4140 Pre-Hardened Steel?
This specific grade is a medium carbon, chromium-molybdenum alloy steel with around 0.4% carbon, and it’s sometimes referred to as “chromoly." The chromium in the alloy adds good hardness penetration, and the molybdenum boosts hardenability and strength. It has trace amounts of other elements, too, but what makes it stand out from its fellow steels is the fact that it’s been pre-treated, meaning it’s delivered to you in a hardened state. Its percentage of carbon is what’s responsible for how easy it is to harden this material.
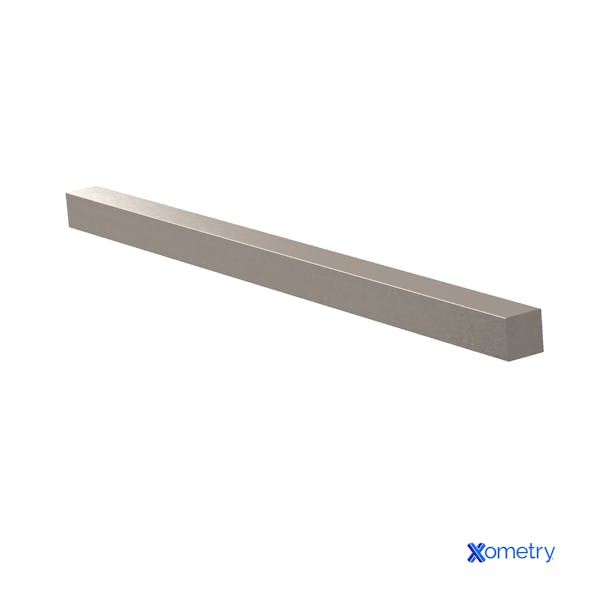
Composition
While it’ll differ ever so slightly from maker to maker, here’s what this kind of steel usually consists of:
- Iron: 96.8–97.7%
- Chromium: 0.8%–1.1%
- Manganese: 0.75–1%
- Carbon: 0.38–0.43%
- Silicon: 0.15–0.3%
- Molybdenum: 0.15–0.25%
- Sulfur: 0.04% max
- Phosphorus: 0.035% max
Properties
These are the key properties you can expect from 4140 pre-hardened steel:
- Superior toughness
- Good wear resistance
- Good ductility
- High tensile strength
- Good machinability
- Good heat resistance
- High fatigue resistance
Treatment Process
As we mentioned, pre-hardened 4140 has to go through processing before it receives this title. This can happen in a handful of different ways and is tailored specifically to create the strength, ductility, and hardness a buyer or manufacturer needs. The most common process is broken down below, but it’s worth knowing this only covers quench-and-temper methods:
- Austenitizing: In this step, you’ll see the steel get preheated then soaked at a temperature that completely changes its microstructure (into the face-centered-cubic austenitic phase). For 4140 specifically, the temperature hovers between 855 and 870°C. The rule of thumb for the required hold time for uniform transformation and dissolution of carbides into the austenite matrix is about 30 minutes per inch of part thickness.
- Quenching: 4140 steel is normally quenched in oil, which isn’t as severe as water quenching but still gives you the desired martensitic microstructure you’re after. Martensite is the hard phase that is produced when austenite is cooled quickly enough to below a critical temperature which depends on the steel’s composition and is fully responsible for getting the right microstructure and hardness. Expect a hardness of about 54 to 59 HRC after this.
- Tempering: Once it turns into a martensite structure, 4140 steel is at its hardest and strongest but also its most brittle. Most applications of this steel require a compromise between hardness and ductility. You can achieve this through reheating the quenched steel to a minimum of 200ºC and a maximum of 650ºC. It can be heated for 30 minutes to two hours, depending on the mechanical properties needed. This cuts down its hardness and turns the microstructure into a mixture of tempered martensite, ferrite, and finely dispersed carbides.
Applications
Some of the most popular sectors and products where you’ll find 4140 pre-hardened steel are:
- Mold and die making, especially for automotive parts
- Gears and shafts in mechanical systems
- Mining equipment for things like crusher components, conveyor rolls, and drill bits
- Aerospace components like landing gear, structural elements, and engine components
- Oil and gas industry parts, such as drilling tools, valve components, and wellhead equipment
- Firearms and defense
- Machine components like shafts, spindles, feed and lead screws, and gears
Welding Considerations
Welding 4140 pre-hardened steel isn’t the easiest endeavor, but with the right considerations, it’s possible. Here’s what to know:
- Heat Treatment Condition: Both pre-hardened and annealed 4140 steel are hard to weld (pre-hardened more so), but it’s possible. Because it's quenched and tempered, the ductility goes down, making it harder for the material to handle the stresses of welding. This is compounded by the risk of hydrogen embrittlement, more pronounced in harder steels, where hydrogen atoms introduced during welding increase brittleness. Welding also impacts the heat-affected zone (HAZ) in this type of steel, more so than with the annealed version. This can lead to cracking and stress that comes from expanding and contracting. If possible, try to anneal your pre-hardened 4140 before welding.
- Filler Metal Choice: You’ll want to match up your filler metal with the tensile strength of 4140, but the chemical compositions don’t have to be identical. It just has to handle multiple cycles and the stresses that can arise from those. A weaker filler can lead to better ductility and fatigue resistance, but a stronger one might lead to cracking. If the weld requires post-weld annealing or normalizing, a 4140 filler metal is usually good enough, as it can regain ductility through these heat treatments. For welds that will undergo quenching and tempering, a 4140 filler metal is necessary, as most low-alloy fillers lack the carbon content needed for these specific treatments.
- Preheating: You’ll want to preheat 4140 to be about 15°C less than the temperature of any previous tempering. This will help cut down on distortion and cracking and slow down its cooling rate.
- Interpass Heating: Once preheating is complete, the preheat temperature must be maintained if multiple weld passes are needed to complete the joint.
- Post-Weld Heat Treatment: The post-weld heat treatment of 4140 steel involves serious oversight of heating and cooling to cut down on hydrogen-induced cracking and lessen residual stresses while also keeping the mechanical properties of the structure once it’s welded. These steps include immediate post-heating (at 575-650°C) after welding to diffuse hydrogen and prevent hydrogen-induced cracking, which is especially important for 4140. Proper preheating and maintaining interpass temperatures are essential in order to keep control over the cooling rate. Following welding, a slow cooling process or “hydrogen bake-out” is recommended. This usually will have you hold the weldment at preheat temperature and then insulate it for gradual cooling. Thicker sheets or formats of 4140 will also need to go through stress-relieving treatments at specific temperatures.
- Heat Treatment: A part welded from annealed 4140 steel can be austenitized, quenched, and tempered after welding to produce the ideally desired microstructure, strength, and ductility for the application. It is not easy to heat treat a weld in situ, which is one of the reasons that welding 4140 that was previously heat treated, for example for a repair, can never match the strength and ductility of the original heat-treated material.
Additional factors should also be considered, such as material thickness, dissimilar metal welding, joint configuration, and welding process.
Annealing and Normalizing—The Impact on 4140 Steel
Both annealing and normalizing are often done to 4140 steel, but they result in very different effects.
Annealing involves heating the steel to a temperature above its Ac3 temperature (which is the temperature at which the microstructure can fully transform to the face-centered cubic phase, austenite) and holding it there before a slow cooling process. There are a few variations of this process, but the main goals of annealing it are to reduce internal stresses and to both soften and toughen the steel. This gives it a more uniform grain structure and reduces warping and cracking tendencies too. Once it’s anneal, you’ll see that its microstructure typically has coarse pearlite and ferrite.
Normalizing, on the other hand, involves heating the steel to a temperature 30-50°C above its Ac3 temperature, then it’s air cooled. Normalizing 4140 also helps give it a more uniform grain structure and extra strength and toughness. However, these two processes are different in their cooling rates. Normalizing cooling rates are quicker than those of annealing, leading to a more refined microstructure. This gives it a great mix of machinability and hardness. In normalized 4140, you’ll find a structure made of fine pearlite and some bainite (a microstructure that forms in steel and other iron-based alloys during certain types of heat treatment, particularly during cooling from a high temperature). One downside of normalizing is a decrease in impact strength due to the thinning of the grain structure.
Advantages and Disadvantages
There are quite a few perks of using 4140 pre-hardened steel, including:
- Corrosion-resistant (especially when compared to plain carbon steel)
- Better-than-average machinability, considering its hardness
- Good ductility
- Good impact and wear resistance
- Great hardness (up to 58 HRC)
- Although it’s hard, it has great toughness too
- Good fatigue strength
- Less distortion when going through processing since it’s already been thermally treated
Pre-hardened 4140 steel also has a few downsides, which we’ve listed out below:
- Hard to weld
- Can cause tool wear
- More expensive than 4140 in an annealed or normalized state
FAQs About 4140 Pre-Hardened Steel
What Is the ASTM Standard for 4140 Steel?
4140 gets its grade from the earlier AISI and SAE International specifications. If you look under the ASTM International system, 4140 steel is included in the ASTM A29/A29M standard, also called the “Standard Specification for General Requirements for Steel Bars, Carbon, and Alloy, Hot-Wrought.”
How Does Machining Work With 4140 Pre-Hardened Steel?
4140 steel has good machinability and is rated 66% of B1112. You’ll be able to saw, drill, broach, hob, or turn this kind of steel as long as you follow best practices and use tools made of high-speed steel or carbide with an average cutting speed of around 110 ft/min.
What Makes 4140 Pre-Hardened Steel Suitable for Industrial Use?
There are a few things that make 4140 pre-hardened steel a great choice for certain uses. It has great hardness and strength because of the preheating treatment it went through. This is very helpful for manufacturing industrial components and machinery since it has boosted wear resistance so that it can handle abrasive or high-wear industrial situations. The heat-treated microstructure also contributes to good toughness and impact resistance. It’s also great for machining and has decent heat resistance.
Is 4140 a High Tensile Steel?
Yes, 4140 steel is considered to be a high-tensile steel. Its high tensile strength is attributed to its carbon level and its chromium-molybdenum alloy composition. Specific heat treatment processes (quenching and tempering, normalizing, and annealing), are needed to fully develop the desired mechanical properties. This steel is usually supplied in the quenched and tempered condition, with a range of tensile strength between 850 and 1000 MPa.
How Xometry Can Help
We have a long list of manufacturing services we can help you with here at Xometry, and you can get free quotes for the likes of steel CNC machining, steel sheet metal fabrication, stainless steel laser cutting, and metal 3D printing.
Disclaimer
The content appearing on this webpage is for informational purposes only. Xometry makes no representation or warranty of any kind, be it expressed or implied, as to the accuracy, completeness, or validity of the information. Any performance parameters, geometric tolerances, specific design features, quality and types of materials, or processes should not be inferred to represent what will be delivered by third-party suppliers or manufacturers through Xometry’s network. Buyers seeking quotes for parts are responsible for defining the specific requirements for those parts. Please refer to our terms and conditions for more information.
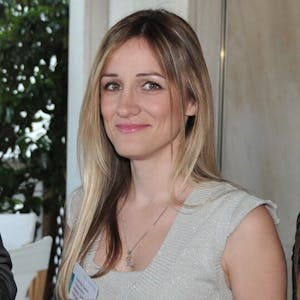