The metal known as AISI 9310 steel is a versatile alloy renowned for its exceptional strength, durability, and wear resistance. With a wide range of applications across various industries, this steel alloy has become a go-to choice for critical components that operate in demanding environments. This article will discuss the uses, composition, and properties of 9310 steel, shedding light on its significance and why it’s held in such high regard across so many industries.
What Is 9310 Steel?
9310 steel is a type of alloy steel widely used in the manufacturing industry due to its high strength and durability. It falls into the category of nickel-chromium-molybdenum (Ni-Cr-Mo) steels. This steel contains carbon, manganese, silicon, chromium, nickel, molybdenum, and small amounts of phosphorus and sulfur. 9310 has a fine-grained microstructure and undergoes a heat treatment process called carburizing, followed by oil quenching and tempering. This treatment enhances its hardness, strength, and toughness. For more information, see our guide on How is Carbon Steel Made.
What Is 9310 Steel Used For?
9310 steel is valued for its strength, toughness, and wear resistance, making it suitable for a variety of applications in the manufacturing industry. Here are some common uses of 9310 steel:
- Critical aerospace components such as gears, shafts, and bearings benefit from 9310’s resilience.
- It is commonly used in the automotive industry for gears, transmission parts, crankshafts, and camshafts. The steel's hardness and durability contribute to improved performance and longevity.
- It is employed in gears, shafts, and other portions of industrial machinery and equipment
- Cutting tools, punches, dies, and molds made of 9310 steel are strong and durable.
- It sees use in the oil and gas sector in the form of drilling equipment, pumps, and valves that require high strength and resistance to corrosion and wear.
How Is 9310 Steel Made?
The production of 9310 steel is a multi-step process. First, the raw materials are melted in an electric arc furnace or an induction furnace. The raw materials typically include iron, nickel, chromium, molybdenum, and other alloying elements such as manganese and silicon. Once the molten metal reaches the desired temperature, these alloying elements are added in precise amounts to achieve the desired composition. After the alloying process, the molten steel is cast into ingots or billets. This solidification step preps the material for subsequent processing. The cast ingots or billets are heated and subjected to hot working processes, such as forging or rolling. The steel is first carburized by exposing it to a carbon-rich atmosphere or a carburizing compound. After carburizing, the steel is rapidly quenched in oil or water. This rapid cooling "freezes" the carbon-rich microstructure into a very hard configuration. The quenched steel is then tempered by reheating it to a specific temperature and holding it there for a predetermined time. The final step involves machining the 9310 steel to give it the proper dimensions and surface finish. Machining processes such as milling, drilling, and grinding work well with 9310 steel.
What Is the Chemical Composition of 9310 Steel?
The chemical composition of 9310 steel is outlined in Table 1 below:
Fe | C | Mn | Si | Cr | Ni | Mo | P | S |
---|---|---|---|---|---|---|---|---|
Fe 93.77-95.19% | C 0.08-0.13% | Mn 0.45-0.65% | Si 0.20-0.35% | Cr 1.0-1.4% | Ni 3.0-3.5% | Mo 0.08-0.15% | P <= 0.025% | S <= 0.025% |
Table Credit: https://www.azom.com/article.aspx?ArticleID=6733
What Is the Carbon Content of 9310 Steel?
The carbon content of 9310 steel typically ranges from 0.08% to 0.13%. It is a relatively low carbon content compared to some other types of steel. The presence of carbon contributes to the overall strength and hardness of the steel, but it is balanced with other alloying elements to achieve 9310 steel’s unique properties.
What Are the Properties of 9310 Steel?
Table 2 below outlines the properties of 9310 steel:
Property | Imperial | Metric |
---|---|---|
Property Bulk modulus | Imperial 20300 ksi | Metric 140 GPa |
Property Density | Imperial 0.284 lb/in³ | Metric 7.85 g/cm3 |
Property Elastic modulus | Imperial 27557-30458 ksi | Metric 190-210 GPa |
Property Shear modulus | Imperial 11600 ksi | Metric 80 GPa |
Property Tensile strength | Imperial 119000 psi | Metric 820 MPa |
Property Yield strength | Imperial 65300 psi | Metric 450 MPa |
Property Elongation at break (in 50 mm) | Imperial 17.30% | Metric 17.30% |
Property Hardness, Brinell | Imperial 241 | Metric 241 |
Property Poisson's ratio | Imperial 0.27-0.30 | Metric 0.27-0.30 |
Table Credit: https://www.azom.com/article.aspx?ArticleID=6733
Machinability Rating of 9310 Steel
The machinability rating for 9310 steel ranges between 24% and 56% with a hardness range of 125-425 BHN. Machinability ratings are used to compare different materials and indicate their suitability for machining operations such as drilling, milling, turning, or threading.
A rating of 56% suggests that the material is moderately machinable. Compared to other materials, it may require more effort, time, or specialized tooling to achieve the desired machining results. As the rating decreases to 24%, the material becomes more difficult to machine, likely requiring specialized tools, techniques, or machining processes.
What Are The Thermal Properties Of 9310 Steel?
The thermal properties of 9310 steel can be found in Table 3 below:
Property | Metric | Imperial |
---|---|---|
Property Thermal expansion coefficient (@ 20°C/68°F, estimated) | Metric 11.5 µm/m°C | Imperial 6.39 µin/in°F |
Property Thermal conductivity (typical steel) | Metric 51.9 W/mK | Imperial 360 BTU in/hr.ft.°F |
Table Credit: https://www.azom.com/article.aspx?ArticleID=6733
What Are the Equivalents of 9310 Steel?
There are no other steel grades that are equivalent to 9310. Some comparable materials, however, include: AMS 6260G, AMS 6265C, and AMS 6267A. These materials share similar properties and characteristics with AISI 9310 and can be used as alternatives in certain applications.
What Are the Common Forms of 9310 Steel Material?
Common forms of 9310 steel material include:
Sheet
9310 steel is available in flat, thin sheets of consistent thickness. Sheets are best for manufacturing techniques that demand flexibility in the raw material,
Bar
9310 steel is commonly available in long, solid bar form with round or square cross-sections. Bars are frequently used in applications that require strength and stability, such as in shafts, fasteners, or precision-machined components.
Plate
9310 steel can also be found in plate form. These plates are flat, rectangular pieces of steel of substantial thickness. Plates typically go into items that require load-bearing capacity or structural strength such as heavy machinery or structural components.
Hot Rolled
9310 steel can be obtained in a hot-rolled condition, indicating that the steel has been heated and then passed through rolling mills to achieve the desired shape and dimensions.
Annealed
Annealed 9310 steel has undergone an annealing process, which involves heating the steel to a specific temperature and then gradually cooling it. Annealing helps to relieve internal stresses and improve the metal’s machinability. Annealed 9310 steel is commonly used for subsequent machining or fabrication processes.
Cold Drawn
9310 steel is also available in a cold-drawn form. Cold drawing is the manufacturing process of pulling the material through a die to simultaneously reduce its cross-sectional area and increase its length. This process is performed at room temperature, resulting in improved dimensional accuracy, surface finish, and mechanical properties.
What Are the Advantages of Using 9310 Steel?
Here are some advantages of using 9310 steel:
- It exhibits high tensile and yield strength. 9310 is suitable for applications that require strong and durable components. It has a typical tensile strength of 150,000 to 170,000 pounds per square inch (psi).
- The toughness of 9310 steel allows it to accept heavy loads, impacts, and dynamic stresses without fracturing. This property makes it ideal for applications where it’s subjected to harsh operating conditions or sudden shocks.
- 9310 has excellent fatigue resistance. It can withstand repeated loading and unloading cycles without failure. This characteristic is particularly valuable in applications involving rotating or oscillating parts such as gears and shafts.
- This metal can be case-hardened to enhance its wear resistance and extend its service life. The steel can be subjected to processes like carburizing or nitriding to create a hard outer layer while maintaining a tough core.
- 9310 steel can be welded using conventional welding methods, which allows for easy fabrication and repair of components.
What Are the Disadvantages of Using 9310 Steel?
While 9310 steel is a very useful metal, it also has certain disadvantages that should be considered. Here are some of the potential drawbacks of using 9310 steel:
- 9310 steel is generally more expensive than standard carbon steel due to its alloying elements and specific heat treatment requirements. The cost may impact overall production expenses, making it less economical for some applications.
- 9310 steel is not as common as some other steel grades. The restricted availability can lead to longer lead times, increased costs, or sourcing challenges, particularly for smaller-scale or specialized manufacturing operations.
- Optimal mechanical properties in 9310 steel depend upon careful heat treatment processes. The steel must be heated to specific temperatures and subjected to precise cooling rates to reach its ideal hardness, strength, and toughness. Improper heat treatment can result in suboptimal performance and properties.
- 9310 steel tends to undergo dimensional changes during heat treatment, particularly during quenching. This can lead to distortion or warping of the finished components, which may require additional machining or corrective measures to ensure proper fit and functionality.
- While 9310 steel has good mechanical properties, it is not inherently corrosion-resistant. It can be susceptible to rust and other forms of corrosion when exposed to moisture or corrosive environments. Proper coating, plating, or other corrosion protection measures may be necessary to mitigate this issue.
- Like many high-strength steels, 9310 steel can become more brittle at low temperatures. This reduced toughness can impact its performance in extremely cold conditions or cryogenic environments.
- The alloying elements in 9310 steel make its material composition and behavior more complex. This can affect material selection, processing, and quality control, requiring specialized knowledge and expertise to ensure consistent and reliable performance.
What Is the Difference Between 9310 Steel and Carpenter 158 Steel?
9310 steel and Carpenter 158 steel differ in their composition and intended applications. 9310 steel is a nickel-chromium-molybdenum alloy steel containing carbon, manganese, silicon, chromium, nickel, and molybdenum. It is known for its strength, toughness, and wear resistance, making it suitable for heavy-duty gears, clutch parts, machined components, and aircraft parts.
On the other hand, Carpenter 158 steel is chosen for its toughness, shock resistance, and fatigue strength. As such, it sees use in firearm components, gears, shafts, and general machinery.
What Is the Difference Between 9310 Steel and 8620 Steel?
9310 steel and 8620 steel are low-alloy steels with some key differences between them. In terms of chemical composition, 9310 steel is a nickel-chromium-molybdenum alloy with more nickel, chromium, and molybdenum compared to 8620 steel.
These variances in composition result in distinct properties and applications. 9310 steel has better hardenability, strength, and toughness due to its higher nickel content. It has excellent core strength, making it suitable for load-bearing tasks. Aerospace manufacturers commonly employ 9310 steel for gears, crankshafts, and bearings due to their strength and fatigue resistance.
In contrast, 8620 steel exhibits good toughness and wear resistance. It’s a perfect candidate for case hardening, creating a hard outer layer while maintaining a tough core. This makes it suitable for gears, camshafts, and driveshafts. Automotive and machinery industries often utilize 8620 steel in components like gearboxes, axles, and crankshafts thanks to its combination of strength, toughness, and case hardening capability.
What Is the Difference Between 9310 Steel and 4140 Steel?
9310 steel and 4140 steel are both formed into sheets but have distinct properties and applications. 9310 steel is a nickel-chromium-molybdenum alloy with more nickel and chromium than 4140 steel. This composition makes 9310 steel stronger, tougher, and more hardenable. It is particularly well-suited, for example, to the load-bearing needs of aircraft gears, crankshafts, and bearings. Additionally, 9310 steel can be heat treated to improve its hardness, further expanding its suitability for heavy-load applications.
By contrast, 4140 steel is a chromium-molybdenum alloy with more carbon content than 9310 steel. Its proportion of carbon makes 4140 steel hard and wear-resistant. It also exhibits good toughness, making it strong in the face of impacts. This versatility makes 4140 steel very valuable in the automotive, machinery, and oil and gas sectors. Components such as shafts, axles, gears, and tooling are often made of 4140 steel.
Summary
This article presented 9310 steel, explained what it is, and discussed its composition and properties. To learn more about 9310 steel, contact a Xometry representative.
Xometry provides a wide range of manufacturing capabilities and other value-added services for all of your prototyping and production needs. Visit our website to learn more or to request a free, no-obligation quote.
Disclaimer
The content appearing on this webpage is for informational purposes only. Xometry makes no representation or warranty of any kind, be it expressed or implied, as to the accuracy, completeness, or validity of the information. Any performance parameters, geometric tolerances, specific design features, quality and types of materials, or processes should not be inferred to represent what will be delivered by third-party suppliers or manufacturers through Xometry’s network. Buyers seeking quotes for parts are responsible for defining the specific requirements for those parts. Please refer to our terms and conditions for more information.
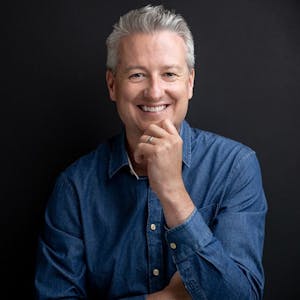