Acetal is a synthetic plastic that is often used when injection molding or extruding. Acetal resins have well-balanced properties, including a hard self-lubricated surface and excellent chemical resistance, strength, stiffness, and toughness over a broad temperature range. Acetal homopolymer is one type of acetal.
This article will look at the properties of acetal homopolymers, the formation of the acetal resin, and its uses.
What is an Acetal Homopolymer?
Acetal, also called polyoxymethylene (POM), polyacetal, and polyformaldehyde, is an engineering thermoplastic used in precision parts that require low friction, high stiffness, and excellent dimensional stability. Like many other synthetic polymers, it is manufactured by different chemical firms with slightly different formulas.
Acetal is categorized by its high strength, hardness, and rigidity to −40 °C. Acetal is intrinsically opaque white because of its high crystalline composition but can be produced in various colors. It has a density of 1.410–1.420 g/cm3.
Homopolymer and Copolymer are two different variations of acetal that have different properties and applications.
How is Acetal Homopolymer Made?
To make an acetal homopolymer, anhydrous formaldehyde must be generated. The primary method for doing so is by reacting aqueous formaldehyde with alcohol to create a hemiformal, dehydration of the hemiformal and water mixture either by extraction or vacuum distillation, and release of the formaldehyde by heating the hemiformal. Next, the formaldehyde is polymerized by anionic catalysis, and a reaction with acetic anhydride stabilizes the resulting polymer. Because of the manufacturing process, large-diameter cross-sections may have pronounced centerline porosity.
What Are the Properties of Acetal Homopolymer?
The mechanical properties of acetal include high strength and stiffness plus enhanced dimensional stability and ease of machining. As a semi-crystalline material, acetal is also characterized by a low coefficient of friction and good wear properties, especially in wet environments. Because acetal absorbs minimal moisture, its physical properties remain constant in various settings. The polymer's low moisture absorption yields excellent dimensional stability for close-tolerance machined parts.
Acetal materials are well suited for close tolerance mechanical parts and electrical insulators, which require strength and stiffness. It is also very chemically resistant, including resistant to many solvents. Other mechanical properties include a tensile strength at break of 7,000 to 9,800 psi at 73°F and compressive strength of 4,400 to 16,000 psi.
Acetal homopolymer is easily machined with conventional metalworking equipment into custom components having very close tolerances. Both sheet and rod are available in many thicknesses and diameters. Also, it has a low-density centerline/core porosity, especially in thicker sheet sections.
What Are the Uses of Acetal Homopolymer?
Acetal homopolymer is used for high load mechanical applications and in plumbing and irrigation applications because of its excellent thread strength and ability to resist scale build-up. In addition, because of its machinability, it is used to prototype in vivo medical devices. Some applications include bearings and bushings, gears, jigs & fixtures, conveyor belts, safety restraints, housings, automotive ventilation, automotive cooling system parts, electrical components, wear pads, and fuel system components.
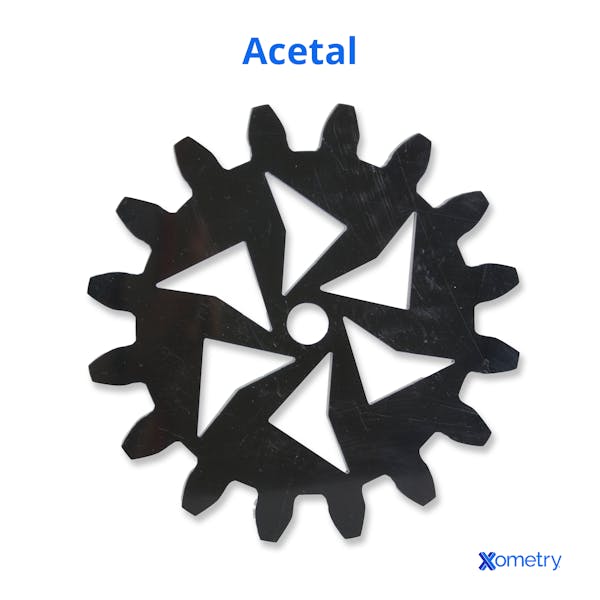
What Are the Grades of Acetal Homopolymer?
There are many different grades of acetal homopolymer, including:
- General Purpose Grades: These low to medium viscosity resins include 100, 111P, 500, 511P, 900, 911, and 1700. These resins are designed for injection-molding processing. The “P” designation used after certain acetal resin numbers denotes that the resin contains additives to enhance processability during injection molding.
- Toughened Grades: These super tough high viscosity grades are developed for injection molding processing, including 100 ST, 500ST, and 500T.
- Low Friction and Wear Grades: These grades contain lubricants that reduce surface friction. These grades are generally designed for injection molding processing and include 500 AL, 500CL, 100AF, 500AF, 520MP, 510MP,500TL, 900SP, and 100KM. Only 100AF is designed for extrusion. A blend of AF 100 with 100, resulting in lower PTFE and lower cost, is also produced for extrusion.
- High Stiffness Grades: These grades are glass-reinforced for added mechanical strength. The grades that are primarily designed for injection molding include 570 NC, 577BK, 510GR, and 525GR.
- UV Stabilized Grades: These grades are designed for outdoor use and feature UV degradation resistance. They contain a chemical UV stabilizer. The grades are 127UV, 527UV, 927UV, and 1727UV. The 127UV is most suitable for extrusion. The other grades are primarily for injection molding processing.
- Extrusion Grades: These grades are designated as extrusion grades for the stock shapes market.
What Are the Advantages of Using Acetal Homopolymers?
Some advantages of homopolymer acetal over copolymer acetal are the greater stiffness, with higher flexural modulus at room and elevated temperature applications, and the slightly higher tensile and impact strength at room temperatures. Homopolymer acetal is slightly harder, therefore providing for a lower coefficient of friction.
Compared to acetal copolymer resin, a homopolymer offers higher tensile strength, impact resistance, and creep resistance. These characteristics mean that it can be used for thinner and lighter part designs, shorter molding cycles, and thus affords the potential for cost reduction.
What Are the Disadvantages of Using Acetal Homopolymers?
The disadvantages of acetal homopolymer resin include longer molding cycle times, sinks, and a relatively high cost. The disadvantage to acetal is that it does not bond well, and so is not ideal for prototyping. The reason acetal doesn’t glue well is that it is so chemically resistant. This, of course, can be an advantage as well for other applications. However, it is also quick burning without flame retardants because of the high presence of oxygen, has poor resistance towards strong acids and bases, and may suffer color degradation and loss of strength with prolonged exposure to UV radiation.
What is the Difference Between Copolymer and Homopolymer Acetal Plastic?
The main difference between copolymer acetal plastic and homopolymer acetal plastic is that two monomers make the polymer in copolymers whereas, in homopolymers, only one monomer repeats and forms the whole polymer. Because acetals are highly crystalline, they must be heated above their melting point to be processed. Homopolymers possess a greater degree of regularity than copolymers in their structure; therefore, they are more crystalline. In addition, the other monomer used to make the acetal copolymers has a longer hydrocarbon linkage that creates more space between the oxygen atoms in the polymer chain. These oxygen atoms are the most significant when considering susceptibility to thermal and oxidative degradation, so the fewer of these present, the more resistant the material will be to degradation.
However, creating that reduced level of regularity also reduces the crystallinity. This is good for the processor because it results in a melting point for acetal copolymer of about 10 degrees Celsius lower than the homopolymer. Thus, an acetal copolymer can potentially be processed at a lower melt temperature. Also, the vulnerable oxygen atoms' spacing increases the material's tolerance for higher melt temperatures. So copolymers have a wider processing window because of advantages on both ends of the thermal spectrum.
How Does Acetal Homopolymer Affect Human Health?
There are no known effects from exposure to the Acetal homopolymer itself. If overheated, the polymer may release formaldehyde, which may cause skin, eye, and respiratory irritation and allergic reactions. However, significant skin permeation and systemic toxicity after contact are unlikely. There are inconclusive or unverified reports of human sensitization.
Is Acetal Homopolymer Toxic?
Acetal homopolymer is not known to contain toxic chemicals under Section 313 of Title III of the Superfund Amendments and Reauthorization Act of 1986 and 40 CFR Part 372. Additives in this product do not present a respiration hazard unless the product is ground to a powder of respirable size and is then inhaled.
However, all dust can cause potential injury to the respiratory tract if respirable particles are generated and inhaled in sufficiently high concentrations. As with all dust, good industrial hygiene practices should include precautions to prevent the inhalation of respirable particles, such as using appropriate personal protection equipment (PPE) and installing suitable filtration equipment to minimize operator exposure.
Summary
This article provided a review of Acetal Homopolymers, including what they are, their uses, material properties, and toxicity.
Xometry offers a full range of injection molding capabilities to help with your production needs. Visit our website to explore the full range of our capabilities or to request a free, no-obligation quote.
Disclaimer
The content appearing on this webpage is for informational purposes only. Xometry makes no representation or warranty of any kind, be it expressed or implied, as to the accuracy, completeness, or validity of the information. Any performance parameters, geometric tolerances, specific design features, quality and types of materials, or processes should not be inferred to represent what will be delivered by third-party suppliers or manufacturers through Xometry’s network. Buyers seeking quotes for parts are responsible for defining the specific requirements for those parts. Please refer to our terms and conditions for more information.
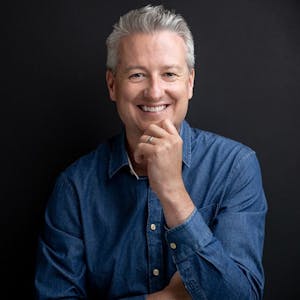