Copolymer acetal (more commonly known just by “acetal”) and homopolymer POM (“Delrin®”) are both polyoxymethylene (POM) polymers with great properties, like strength and durability, that make them appealing to manufacturers. We’ll talk about both of these materials in this article, and we’ve even got a side-by-side comparison table so you can decide which one is best for your needs.

What is Acetal?
Acetal is a semi-crystalline engineering thermoplastic that comes in two forms: homopolymer and copolymer. The terms “POM” and “acetal” are often used interchangeably, but in practical terms, “acetal” generally refers to the copolymer version. This copolymer is a chain of CH2O molecules with extra comonomers added in after every 70–100 units of CH2O. These disrupt the regular ordering of the molecular chains, ultimately making the material less crystalline.
Acetal copolymers readily accept reinforcing materials like glass fiber, and their molecules can be chemically bonded to the glass via coupling, which increases its strength and stiffness. Acetal has a low friction coefficient, meaning that it’s got good wear- and abrasion-resistance. It can also handle exposure to organic and inorganic solvents and acids, and prolonged exposure to hot water and high temperatures. This copolymer’s low porosity means that centerline porosity (where voids form in the center of an extruded part/sheet) will be highly unlikely. It’s also, most times, more affordable than homopolymer POMs, too.
What are the Characteristics of Acetal?
Acetal polymers have good thermal and chemical resistance. Some typical acetal plastic properties are listed below:
- Reinforcing: Acetal copolymers readily accept reinforcing materials like glass fiber. A chemical process known as coupling allows the polymer molecules to chemically bond to the glass fiber. This results in significant increases in strength and stiffness.
- Low Coefficient of Friction: A low friction coefficient means that acetal has good wear- and abrasion-resistant properties.
- Chemical Resistance: Acetal copolymer is resistant to both organic and inorganic solvents and acids.
- Lower Relative Cost: Acetal copolymer tends to be cheaper than homopolymer POMs like Delrin.
- Low Porosity: Acetal has low porosity characteristics, meaning that centreline porosity is unlikely. Centreline porosity is the phenomenon wherein voids form in the center of an extruded profile or sheet.
- Resistance to Hot Water: Acetal resists degradation caused by prolonged exposure to hot water, helping it maintain dimensional stability.
- High Continuous Service Temperature: Acetal copolymers can withstand prolonged exposure to high temperatures without serious reductions in mechanical properties.
- Custom Colors: Acetal copolymer is available in many different colors.
What are the Uses of Acetal?
Acetal polymers are used in almost every industry from automotive to consumer electronics. Some typical applications are listed below:
- Insulin pens
- Dry powder inhalers
- Electric toothbrushes
- Electrical connectors
- Kitchenware
- Gears
- Valves
- Pumps
- Fuel sender units
- Door locks
- Vehicle fuel tanks
What is Delrin?
Delrin is a semicrystalline homopolymer POM that’s one of the strongest and stiffest unreinforced polymers around. It was developed by DuPont (which patented the “Derlin” trade name). Homopolymers have a uniform backbone made with repeating CH2O units, which makes it possible to create larger crystalline blocks than other POMs. Delrin’s high crystallinity gives it excellent mechanical properties, including the aforementioned strength and stiffness, as well as spring back. There are different types of Delrin, some of which have fillers like glass fiber and PTFE.
Delrin’s toughness doesn’t vary in temperatures of -40–90॰C, and it’s able to withstand high intermittent temperatures of up to 120॰C. It won’t be able to sustain that temperature for a longer time, however. As a resin, it flows well and can fill injection molds much better than similar materials with short cycle times. Its ability to flex without deforming makes it ideal for snap-fit connectors. It can resist fatigue very well, making it a common option for parts that are put under continuous cyclic loading. Unlike acetal, Delrin is prone to becoming porous at the center of extruded profiles due to its outer surfaces cooling first, reducing the center’s density.
What are the Characteristics of Delrin?
Delrin polymer is a tough and high-strength engineering polymer. Some of the key Delrin material properties are listed below:
- Easy to Mold: Delrin acetal resin flows well in liquid form. It fills injection molds better than similar materials and also enables short cycle times.
- Crystalline: Delrin has a high degree of crystallinity. That gives it excellent mechanical properties such as strength, stiffness, and springback.
- High Yield Strain: Delrin can flex with very little permanent deformation. This is an ideal characteristic for snap-fit connectors.
- High Toughness: Delrin has excellent toughness, a helpful property that does not vary over a temperature range of -40॰C to 90॰C.
- Temperature Resistance: Delrin is able to withstand high intermittent temperatures of up to 120॰C. It cannot sustain that temperature for extended periods, however.
- Fatigue Strength: Delrin is well suited to applications that undergo continuous cyclic loading because it resists fatigue very well.
What are the Uses of Delrin?
Delrin is popular for its excellent mechanical properties, especially fatigue resistance and toughness. Some typical applications are listed below:
- Conveyor system parts
- Bearings
- Bushes
- Implants & prosthetics
- Rollers
- Safety restraints
- Door system parts
- Zip fasteners
- Linear guide rails
What is the Difference Between Acetal and Delrin?
As we’ve seen, both acetal and Delrin have some great properties, but let’s see a side-by-side comparison to really understand their differences.
Property | Acetal | Delrin |
---|---|---|
Property Chemical resistance | Acetal Resistant to organic/inorganic solvents and acids | Delrin Not resistant to acids, bases, or oxidizing agents |
Property Temperature resistance | Acetal Better long-exposure temperature resistance, doesn’t oxidize or degrade in high temperatures for long periods | Delrin Higher instantaneous temperature resistance, but degrades with prolonged exposure, poor flame resistance (UL94 rating of HB) |
Property Processing difficulty | Acetal Wider processing window as it’s not sensitive to temperature variations | Delrin Needs to be processed in a very narrow temperature band to prevent degradation. Due to its high crystallinity, it has a very precise melting temperature |
Property Effect of reinforcing additives | Acetal Glass-filled acetal has better mechanical properties due to the way the copolymer bonds chemically to the glass | Delrin Additives like glass fiber do not bond chemically to the polymer chains, so they behave as fillers and only increase the stiffness of the material |
Property Mechanical properties | Acetal Not as good as Delrin, but can keep its mechanical properties at high temperatures for long periods | Delrin High fatigue resistance for cyclic loading applications, better creep resistance when exposed to long-term loading |
Property Advantages | Acetal Reinforcing, low coefficient of friction, chemical resistance, low cost, low porosity, hot water resistant, high continuous service temperature | Delrin Easy to mold, high crystallinity, high yield strain, tough, temperature resistant, good fatigue strength |
Property Applications | Acetal Insulin pens, dry powder inhalers, electric toothbrushes, electrical connectors, kitchenware, gears, valves, pumps, fuel sender units, door locks, vehicle fuel tanks | Delrin Conveyor system parts, bearings, bushes, implants and prosthetics, rollers, safety restraints, door system parts, zip fasteners, linear guide rails |
Key Property Differences Between Acetal Copolymer vs. Delrin®
The common properties of both acetal copolymer and Delrin are:
- Very easy to machine (in the proper temperature range).
- Exhibits some centerline porosity. This is the process where the material becomes porous at the center of extruded profiles due to outer surfaces cooling first and reducing density at the center. It must be noted that acetal experiences less of this problem than Delrin, which is very prone to centreline porosity.
- Poor flame resistance with a UL94 rating of HB.
FAQs on Acetal and Delrin
How does a POM’s structure affect its overall strength?
POMs are made up of minuscule and tightly-packed crystalline structures that are a bit like mini blocks. These are pretty strong on their own, but the material’s overall strength depends on the bonds that connect and hold these blocks together. This is because bond strength within a crystalline block is much higher than between two blocks that are next to each other. When this material is pulled, bent, or otherwise put under stress, these connecting bonds can start to stretch. With too much force, they’ll eventually separate and weaken the material. There are ways to improve these bonds so that the material can handle more force without getting damaged.
How can POM be made even stronger?
As mentioned above, to make a POM stronger, the bonds between the crystalline blocks need to be reinforced. There are two main ways of doing this. The first is by adding reinforcing materials, like glass fibers, which works especially well for acetal (not so much for Delrin) because it can chemically bond with the glass. The second is by selective heat treatment, which could increase crystallinity and improve the bonds’ strength. Acetal reacts better to the additive method, while Delrin can sometimes benefit more from heat treatment.
How Xometry Can Help
Xometry offers injection molding services for all of your prototyping and production needs. Visit our website to learn more and to request a free, no-obligation quote using our Instant Quote Engine. You can get started today by uploading your designs to the Xometry Instant Quoting Engine®!
Copyright and Trademark Notice
- Delrin® is a registered trademark of E.I. Du Pont De Nemours and Company, Wilmington, DE.
Disclaimer
The content appearing on this webpage is for informational purposes only. Xometry makes no representation or warranty of any kind, be it expressed or implied, as to the accuracy, completeness, or validity of the information. Any performance parameters, geometric tolerances, specific design features, quality and types of materials, or processes should not be inferred to represent what will be delivered by third-party suppliers or manufacturers through Xometry’s network. Buyers seeking quotes for parts are responsible for defining the specific requirements for those parts. Please refer to our terms and conditions for more information.
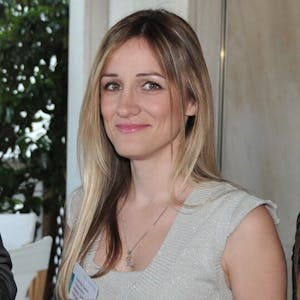