Engineering plastics are specially designed and formulated to have improved properties compared to commodity plastics. These properties may include better mechanical, electrical, and thermal properties; improved chemical and ultraviolet light resistance; and biocompatibility for food packaging applications. While not every engineering plastic exhibits all of these traits, they are distinct from commodity plastics due to their ability to be used in a broader range of technically demanding applications — from gears in power transmission applications to medical implants and prosthetics. Examples of various engineering plastics include: nylon, polyethylene terephthalate (PET), acrylonitrile butadiene styrene (ABS), polycarbonate (PC), and many more. The low density of engineering plastics compared to metals, coupled with their impressive material properties and economical price, make them a lighter-weight alternative to metals for a variety of applications. This article will review the subject of engineering plastics: their definition, their uses, their properties, and the many different types.
What Are Engineering Plastics?
Engineering plastics are a class of polymers that have been specially formulated to exhibit enhanced mechanical, electrical, thermal, and chemical properties compared to commodity plastics. These enhanced properties allow engineering plastics to be used in demanding industrial and engineering applications such as gears, bearings, bushings, and medical implants.
The main difference between engineering plastics and commodity plastics is that engineering plastics are used in more technically demanding environments. While commodity plastics are also popular, they are not suitable for the same applications as engineering plastics as they do not exhibit the same degree of material properties. Engineering plastic parts are typically manufactured by plastic injection molding or plastic extrusion, although 3D printing is also possible.
What Is the Importance of Engineering Plastics?
Engineering plastics play a pivotal role in many industries, such as: automotive, aerospace, electronics, medical, and consumer goods manufacturing. Engineering plastics are known for their ability to be used in applications where metals may be too heavy, expensive, or susceptible to corrosion, and where commodity plastics lack the strength and durability required. They are durable and versatile owing to their mechanical strength and impact resistance, coupled with their desirable thermal, electrical, and chemical properties. Engineering plastics offer manufacturers an ideal balance between strength, cost, weight, and durability.
What Are the Properties of Engineering Plastics?
The desirable properties of engineering plastics are listed and described below:
1. Abrasion Resistance
Abrasion resistance is a material’s ability to resist damage due to scratches, wearing, rubbing, marring, or any other friction-related phenomenon. Engineering plastics exhibit a high degree of abrasion resistance compared to commodity plastics due to their improved mechanical properties, specifically their hardness. Good abrasion resistance makes engineering plastics great for parts that are prone to wear, such as guide rollers, gears, and bushings.
2. Chemical Resistance
Chemical resistance is a material’s ability to resist reacting with various compounds, oils, solvents, gasses, and other elements in its operating environment. Engineering plastics generally exhibit good chemical resistance. This property makes them good for use in environments where exposure to chemicals is common, e.g., machinery of all kinds, medical applications, and consumer goods like kitchenware, cookware, and bathroom products.
3. Dimensional Stability
Dimensional stability refers to a material’s ability to retain its manufactured dimensions in the presence of high or low temperatures. Engineering plastics have varying levels of dimensional stability depending on the particular type of engineering plastic. The good dimensional stability of engineering plastics makes them useful for high-heat environments where thermal expansion is likely such as in the automotive, aerospace, and industrial industries.
4. Electrical Properties
Electrical properties are related to a material’s ability to conduct or insulate electrical currents. Electrical conductivity and resistivity are the two critical electrical properties of engineering plastics. Most engineering plastics are poor electrical conductors which makes them ideal for applications where electrical insulation is desired, such as in various electronic and wiring applications.
5. Flammability
Flammability is a material’s tendency to catch fire. Engineering plastics have varying levels of flammability depending on the particular type of engineering plastic. Some engineering plastics, such as PEEK or PPS, are specifically formulated for flame resistance and ignition prevention while other engineering plastics, like ABS, are flammable. Engineering plastics that are non-flammable are exceptional for use in applications where ignition is a concern such as in chemical processing.
6. Food Compatibility
Food compatibility refers to a material’s safety for use with food, specifically in packaging. Some engineering plastics, such as PET, POM, PMMA, and ABS, are safe for use with food due to their chemical structure and lack of additives, dyes, and other harmful products. Others, for example, polycarbonate, are not safe.
7. Impact Strength
Impact strength is a material’s ability to resist deformation due to a sudden or intense application of load, also known as a shock load. Impact strength is a critical property that characterizes how well a material can withstand sudden forces. Compared to commodity plastics, many engineering plastics exhibit high impact strength, which makes them good for load-bearing applications that are subjected to varying impact forces, such as machine guards and electronic housings.
8. Min/Max Operating Temperature (Thermal Resistance)
Thermal resistance is the property that characterizes a material’s ability to resist changes in its properties due to varying temperatures. Specifically, the low temperature at which materials become brittle and the high temperature at which materials become soft and even melt. Engineering plastics have varying degrees of thermal resistance depending on the type of plastic. For instance, PEEK is specially formulated for use in high-temperature environments (up to 250 °C). High-temperature environments where plastics are used include various machinery and industrial applications.
9. Sliding Properties
The sliding, or anti-friction, properties of engineering plastics make the materials more wear-resistant and abrasion-resistant compared to commodity plastics. Engineering plastics notably have a low coefficient of friction which enables these properties to be possible. The sliding properties of engineering plastics make them ideal for applications where repeated sliding, rubbing, or scraping are common such as in machinery components like wear pads, bearings, gears, pulleys, and rollers or medical applications like hip implants.
10. Ultraviolet (UV) Light Resistance
UV resistance refers to a material’s ability to resist degradation and discoloration due to exposure to ultraviolet rays from sunlight and other sources. UV rays can break down polymer chains and cause chemical changes within the material. UV resistance is important for engineering plastics because it enhances their ability to be used outside or in other UV exposure-intense environments. Many engineering plastics, particularly polyamides, PMMA, and Ultem®, exhibit outstanding UV resistance, which makes them able to be used in environments with constant UV exposure.
11. Water Absorption
Water absorption refers to a material’s affinity to absorb water. Engineering plastics are water-resistant and do not easily allow water to penetrate into the material. This makes engineering plastics ideal for applications where water contact is common.
What Are the Different Types of Engineering Plastics?
There are numerous types of engineering plastics which are listed and described below:
1. Nylon 6
Nylon 6 is a specific grade of nylon, or polyamide, material. Nylon 6 has good stiffness, toughness, electric and thermal insulation properties, and mechanical strength. Its properties can further be enhanced with glass fiber and other compounds. Nylon 6 is used for forming dies, insulators, washers, rollers, pulleys, valve seats, and more.
2. Polyethylene Terephthalate (PET)
PET is a popular type of engineering plastic known for its high strength, chemical resistance, and recyclability. A type of polyester, PET is used in applications like textiles, food and beverage containers, pill bottles, and more.
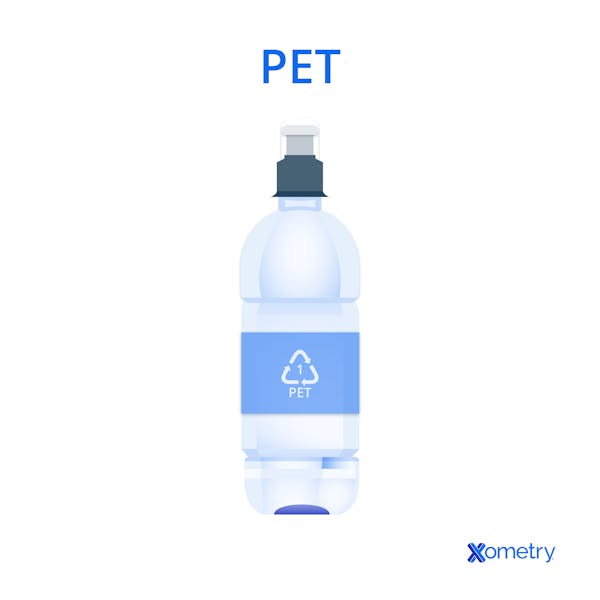
3. Acrylonitrile Butadiene Styrene (ABS)
ABS is another preferred type of engineering plastic that is valued for its chemical and thermal stability, strength, toughness, and glossy finish. Its host of desirable properties make it a versatile material. It is used in everything from consumer products like toys and bicycle helmets to automotive applications such as interior trim pieces, housings for electronics, and more.
To learn more, see our guide on Acrylonitrile Butadiene Styrene.
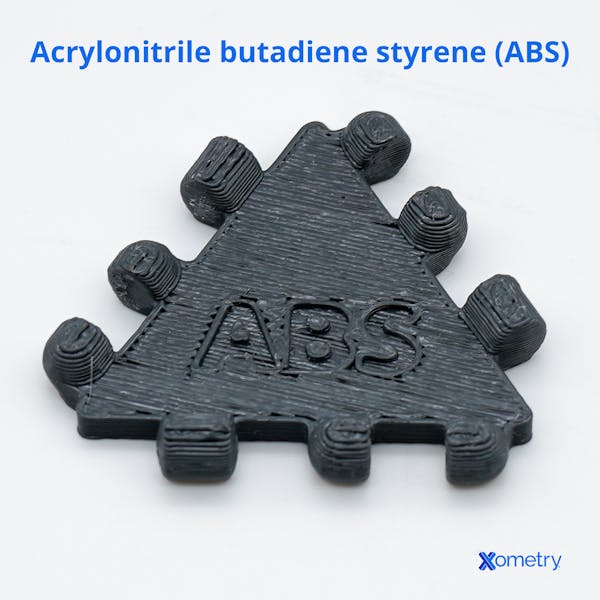
4. Nylon 6-6
Nylon 6-6 is another type of nylon (or polyamide) material. It has the same properties as nylon 6 but has a greater range of operating temperatures (up to 103 °C before deformation begins) and chemical resistance compared to Nylon 6. Nylon 6-6 is used in applications such as conveyor belts, clothing and other textiles, bearings, bushings, sprockets, electronic housings, and more.
5. Polyimides
Polyimides (PI) are formed by the combination of aromatic dianhydrides and aromatic diamines. This particular combination of chemicals yields a polyimide material with excellent thermal stability, high tensile strength, and good chemical resistance. These properties enable polyimides to be used in environments with temperature extremes up to 370 °C, in applications such as fuel cells, insulating coatings, structural adhesives, and more.
6. Polyether Ether Ketone (PEEK)
PEEK stands out from other engineering plastics due to its wide range of operating temperatures (up to 250 °C), outstanding chemical resistance, high strength, and stiffness. PEEK is used for pump and valve components; bearings, bushings, and seals in machinery; electrical connectors; and medical device components.
7. Polyphenylene Sulfide (PPS)
PPS is a high-performance, tough engineering plastic with great dimensional and thermal stability, as well as a wide operating temperature range of up to 260 °C and good chemical resistance. Moreover, PPS, like most other thermoplastics, is an electrical insulator. Its ability to be used at high temperatures coupled with its thermal stability makes PPS great for applications such as semiconductor components in machinery, bearings, and valve seats.
8. Poly(methyl methacrylate) (PMMA)
PMMA, also known as acrylic, is a common type of engineering plastic that is valued for its optical clarity, high strength, impact resistance, and light weight. For these reasons, PMMA is commonly used as a glass substitute. Applications of PMMA include windows, signage, display cases and fixtures, machine guards, and more.
9. Polybutylene Terephthalate (PBT)
PBT has properties similar to those of PET (polyethylene terephthalate). It is known for its dimensional stability, low moisture absorption, high strength, stiffness, and chemical, UV, and thermal resistance. It is commonly used in automotive fenders and interior trim pieces, power tool housings, and electrical enclosures.
10. Polyphenylene Oxide (PPO)
PPO, exhibits low moisture absorption, has excellent electrical and thermal insulating properties, great dimensional stability, and can be used in temperatures up to 155 °C. PPO is used for automotive fenders, electronics housings, and medical instruments.
11. Polyamides (PA)
Polyamides are a class of engineering plastic formed by chains of amide molecules. Nylons and aramids are both types of polyamides. Polyamides are known for their high strength, impact resistance, and dimensional stability, which makes them useful for a wide range of applications in various industries. From clothes and textiles to automotive trim pieces, to bushings and bearings in industrial machines, polyamides are a common type of engineering plastic.
12. Polycarbonates (PC)
Polycarbonates are known for their optical clarity, chemical resistance, tensile and impact strength, fire resistance, and recyclability. Polycarbonates are used in applications such as: machine guards, CDs, motorcycle face shields and windscreens, electronics housings, signage, streetlamps, safety glasses, and more.
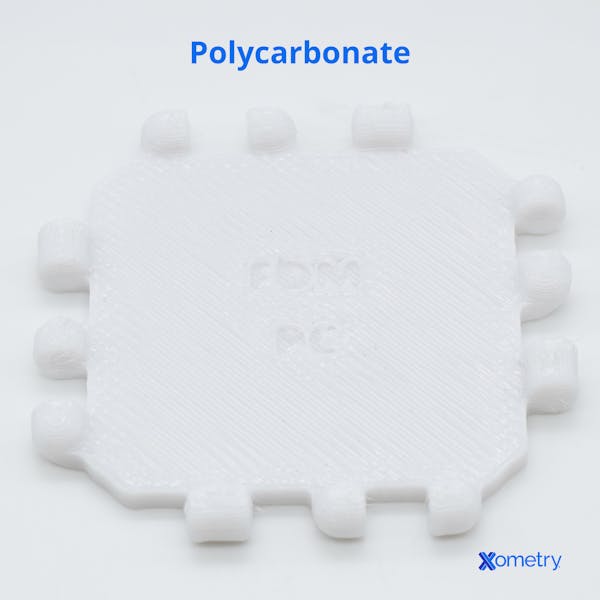
13. Polyetherimide (PEI) ULTEM®
PEI, also known by the popular brand name ULTEM®, is an engineering plastic valued for its mechanical strength, rigidity, creep resistance over a wide temperature range, and electrical insulation properties. PEI boasts the highest dielectric strength of any commercially available thermoplastic and is therefore commonly used in the electronics industry for fuses and coils. Additionally, it is used in the aerospace industry, where it is used for interior trim pieces.
14. Polyetherketoneketone (PEKK)
PEKK is an engineering plastic with characteristics similar to those of PEEK. This is because PEEK and PEKK are both part of a group of thermoplastics known as polyaryletherketones (PAEK). PEKK is characterized by good mechanical strength, thermal stability, and chemical resistance. Because of its mechanical strength and chemical resistance, PEKK is used in high-pressure pumps, gear wheels, propellers, orthopedic and dental implants, and more.
15. Polyetherketone (PEK)
PEK is a type of PAEK engineering plastic that is known for its low thermal expansion coefficient, creep resistance, chemical resistance, low flammability, and mechanical properties over a broad temperature range up to 260 °C. These properties make PEK useful for applications where loads are applied at high temperatures for an extended time such as in gears, bushings, bearings, shafts, and more. PEK is used in the aerospace, machinery, and automotive industries.
16. Polyketone (PK)
Polyketone is an engineering plastic that is a type of PAEK. PK has high impact strength — about two to three times higher than nylon or PBT — and has excellent wear and chemical resistance. Its wear and chemical resistance make PK often used in the automotive, oil and gas, and chemical industries.
17. Polyoxymethylene Plastic (POM / Acetal)
POM, also known as acetal or Delrin®, is one of the most popular engineering plastics due to its high strength, toughness, elasticity, dimensional stability, excellent machinability, impact strength, low friction coefficient, and chemical resistance. Acetal is used in everything from gears, pulleys, and rollers to snap fasteners like zippers and buckles due to its abrasion resistance and high strength.
18. Polysulfone (PSU)
PSU is a translucent engineering plastic that is known for its food compatibility, biocompatibility, wide service temperature range of up to 160 °C, and good mechanical properties. PSU is used in the medical and food preparation industries due to its bio-friendliness for applications like manifolds in food processing or medical trays.
19. Polytetrafluroethylene (PTFE / Teflon®)
PTFE is a popular engineering plastic known for its versatile properties. These properties include: broad temperature range from -240 °C to 260 °C and low moisture absorption, low coefficient of friction, flexibility, and chemical resistance. PTFE is used in many different applications, such as wiper blades, cookware, pipes for high-purity chemical processing, nail polish, and more.
What Are the Most Common Types of Engineering Plastics?
Different sources will list different engineering plastics as being the most common types. The list below was chosen based on which engineering plastics are most widely used across the largest variety of industries.
- PET: PET is a type of polyester with a broad range of uses such as: clothing, textiles, food and beverage containers, and pill bottles. PET is widely available, cheap to manufacture, easy to recycle, and has excellent mechanical properties. However, its low heat resistance, tendency to oxidize, and low biodegradability limit the applications where PET can be used.
- ABS: ABS is used in many different applications — from consumer components and automotive components to electronic devices of all kinds. ABS is inexpensive and plentiful, strong, lightweight, ductile, and thermally stable. However, ABS has poor resistance to fatigue, is flammable, and has a lower melting point compared to other engineering plastics.
- PC: Polycarbonate is used in applications such as machine guards, automotive headlamps, windows, safety glasses, and more. It is a fire-resistant material that is also lightweight, thermally insulating, strong, and fully recyclable. However, PC is sensitive to scratches and has a high coefficient of thermal expansion.
How Does Plastic Engineering Work?
Plastic engineering is a branch of engineering that focuses on the design and development of plastic materials and products. The boundaries of plastic engineering range from research and development in chemical laboratory settings to the plant floor where the process parameters for plastic machinery such as injection molding machines and plastic extruders are studied and optimized for a particular product. The purpose of plastic engineering is to create and optimize new plastic materials from organic polymers that are either petrochemical-based or naturally occurring. These plastic materials are synthesized via chemical reactions and are created to satisfy specific needs and applications.
What Are the Advantages of Engineering Plastics?
Engineering plastics have several advantages over commodity plastics, such as:
- Possess enhanced mechanical properties, such as improved tensile strength, impact strength, and toughness compared to commodity plastics’ properties
- Are lightweight and strong materials
- Exhibit a high degree of chemical resistance, making them great for applications where exposure to various oils, solvents, and chemicals is common
- Resist UV light damage (especially PMMA, ULTEM, and PTFE), making them reliable performers in outdoor environments
What Are the Applications of Engineering Plastics?
Listed below are some of the many applications of engineering plastics:
- Engineering plastics such as polycarbonate, ABS, nylon 6, and nylon 6-6 are widely used in the automotive industry for components like dashboards, interior trim pieces, electronic component housings, fuel caps, door handles, and more.
- PEEK, polyimides, PAI, and PTFE are engineering plastics commonly used in the aerospace industry. Examples are: pump gears, valve seats, electrical insulators and housings, and more.
- Food and beverage containers and disposable trays and plates are commonly made from engineering plastics. PET is the engineering plastic most frequently used in food and beverage applications due to its strength, chemical resistance, UV resistance, food compatibility, and recyclability.
- Electronic components such as housings, switches, end terminals, insulators, displays, and more can be made from engineering plastics. Such engineering plastics as nylon 6, nylon 6-6, PC, PBT, ABS, and PEI are often used in the electronics industry due to their mechanical properties such as: tensile strength and impact resistance, electrical insulation properties, wide operating temperature ranges, and chemical resistance.
- Consumer products range from toys and kitchenware to sporting goods and clothing. Engineering plastics such as PET, nylon, PMMA, and PTFE are used in a broad spectrum of consumer products due to their light weight, abrasion resistance, dimensional stability, chemical resistance, and UV resistance.
What Is the Hardest Engineering Plastic?
Which engineering plastic is judged to be the hardest depends on the measurement method used and the exact condition of the material. PMMA (acrylic) is the hardest engineering plastic as measured on the Shore D scale (Shore D 99) and on the Rockwell D hardness scale (105).
Are Engineering Plastics Strong?
Yes, engineering plastics are strong. They are specifically formulated to have high tensile strength and impact strength compared to standard commodity plastics such as polypropylene or polyethylene.
What Is the Difference Between Engineering Plastics and Commodity Plastics?
Engineering plastics are polymeric materials designed and formulated to have specific properties and to satisfy the requirements of various high-performance applications. They typically have enhanced mechanical, thermal, and chemical properties compared to commodity plastics.
Commodity plastics are general-purpose plastics that do not need to satisfy stringent technical requirements. Commodity plastics are used for everyday items from toys and packaging to disposable plates and cutlery. While both engineering plastics and commodity plastics are useful in their own right, they are intended to satisfy vastly different purposes.
Summary
This article presented engineering plastics, explained what they are, and discussed their importance and various applications. To learn more about engineering plastics, contact a Xometry representative.
Xometry provides a wide range of manufacturing capabilities and other value-added services for all of your prototyping and production needs. Visit our website to learn more or to request a free, no-obligation quote.
Copyright and Trademark Notices
- Ultem® is a registered trademark of SHPP GLOBAL TECHNOLOGIES B.V.
- Teflon™ is a registered trademark and a brand name (Teflon ®) owned by Chemours (formally DuPont)
Disclaimer
The content appearing on this webpage is for informational purposes only. Xometry makes no representation or warranty of any kind, be it expressed or implied, as to the accuracy, completeness, or validity of the information. Any performance parameters, geometric tolerances, specific design features, quality and types of materials, or processes should not be inferred to represent what will be delivered by third-party suppliers or manufacturers through Xometry’s network. Buyers seeking quotes for parts are responsible for defining the specific requirements for those parts. Please refer to our terms and conditions for more information.
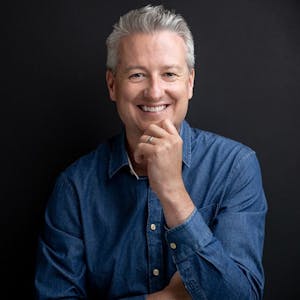