Coble creep is a deformation mechanism characterized by the diffusion of atoms along the grain boundaries of a material. It is one of several types of “creep,” or time-dependent permanent deformation, caused by constantly applied loads at elevated temperatures. Over time, under conditions of sustained loading at high temperatures, the diffusion of atoms causes materials to plastically deform and lose structural integrity. For this reason, coble creep tends to be the dominating form of creep at high temperatures 40-90% of the material’s melting point. It’s important for engineers and manufacturers to consider the potential of Coble creep in their designs and products to mitigate risks. This article will discuss Coble creep, describing how it occurs, and addressing how it can be controlled.
What Is Coble Creep?
Coble creep is a type of diffusion creep that involves the movement of atoms along the grain boundaries of a material’s microstructure. Like other forms of creep, Coble creep is time-dependent and occurs when high temperatures accompany a constantly applied stress. However, Coble creep, unlike dislocation creep, is labeled as a type of “boundary creep” rather than “lattice creep.” Coble creep occurs at high temperatures (but at temperatures lower than observed with dislocation creep or Nabaroo-Herring creep) and low stress relative to the yield point of a material. As temperatures increase to roughly 40-90% of the material’s melting point, atoms and vacancies on and near grain boundaries acquire sufficient energy to diffuse along grain boundaries. Over time, the diffusion of atoms and vacancies causes permanent deformation in the material and may eventually lead to rupture.
Compared to N-H creep, Coble creep occurs at lower temperatures since grain boundaries are areas of mismatched lattice and less energy is required to move atoms and vacancies along grain boundaries compared to grain interiors. For more information, see our guide on What is Creep.
How Does Coble Creep Occur?
Coble creep occurs when a material is subjected to high temperatures 40-90% of the material’s melting point and applied stress over the passage of time. At high temperatures, atoms and vacancies at grain boundaries become energized. Once activation energy is high enough, atoms and vacancies diffuse along the grain boundaries. Over time, an applied stress (which may be lower than the material’s yield point) can cause atoms to diffuse along grain boundaries under these conditions. The list below shows how Coble creep occurs:
- Material is Placed in High Operating Temperature: Coble creep begins when a material is placed in high operating temperatures (40-90% of a material’s melting point) High temperatures energize atoms and cause them to vibrate. When an energy level of an atom is high enough, atoms will diffuse into vacancies along the grain boundaries of the material.
- Applied Stress: In the first step, atoms are energized from high temperatures and diffuse into vacancies along grain boundaries. When stress is also involved, portions of the grain boundaries are in tension or compression. Atoms have a tendency to move from areas of higher density to areas of lower density. Therefore, when stress is applied at higher temperatures, atoms more quickly diffuse across grain boundaries.
- Time: When a material is subjected to stress at high temperatures 40-90% of its melting temperature for a long span of time, additional vacancies are generated in the material and atoms continue to diffuse towards them. If temperatures are further increased, more energy is available for this sequence of events to occur.
- Plastic Deformation Occurs: The longer a material is exposed to high temperatures and applied stresses, the more atoms will diffuse along the grain boundaries. As more atoms diffuse and vacancies become more common, the material plastically deforms as grain boundaries more easily slip against each other. If enough Coble creep occurs, the integrity of the part will be compromised which allows a new deformation mechanism such as dislocation creep or rapid tensile plastic deformation to occur.
What Are the Factors That Promote Coble Creep?
Coble creep occurs in response to the same main factors that drive other creep mechanisms. However, Coble creep often occurs at temperatures and stresses lower than those observed in other forms of creep. The factors of Coble creep are listed below:
- Temperature: Temperature is the factor with the strongest influence on the initiation of Coble creep. If a material has vacancies throughout its structure, atomic diffusion into these vacancies more rapidly occurs at higher temperatures since the atoms have more energy. Additionally, Coble creep can occur at lower temperatures than N-H creep because the activation energy for grain boundary diffusion is lower than the activation energy for trans-lattice diffusion. The grain boundary already consists of disrupted lattice elements that are at a higher energy level than the main lattice.
- Stress: Stress accelerates the diffusion of atoms and consequently the material’s deformation. Stress causes portions of the material’s grain boundaries to be in tension or compression. Atoms in the more densely packed compressed areas have a tendency to move to the less densely packed areas in tension.
- Time: The longer the material is subjected to high temperatures and applied stresses, the more deformation due to Coble creep accumulates.
- Grain Size: Materials with finer grain sizes are more susceptible to Coble creep while materials with larger grain sizes are more resistant to Coble Creep. Materials with finer grain sizes have more grain boundaries and thus more opportunities for atoms to diffuse. Single-crystal materials eliminate grain boundaries altogether, thus bypassing this particular creep mechanism.
- Grain boundary: Low-angle grain boundaries have lower energy and are therefore more resistant to Coble creep. High-angle grain boundaries have higher energy and are more susceptible to Coble creep.
- Chemical Composition: Chemical composition is a factor in Coble creep since atomic size can influence an atom’s diffusion capability. For instance, the right size substitutional solute atom can hinder the effects of Coble creep since it inhibits the ability for atoms to diffuse.
When Was Coble Creep Proposed?
The Coble creep mechanism was first proposed by American scientist Robert L. Coble in 1962. At that time, Coble was a professor at the Massachusetts Institute of Technology (MIT) and proposed that the influence of grain-boundary diffusion was more significant than the influence of the self-diffusion of atoms through the grains at temperatures between 40-90% of a material’s melting point. After numerous experiments and observations, he published his research findings on diffusion creep in the Journal of Applied Physics.
What Is the Importance of Coble Creep in Manufacturing Processes?
Coble creep has significant implications in both manufacturing and engineering. It’s important for both manufacturers and engineers to understand the phenomenon and adequately design structures and components to combat Coble creep’s effects. Creep-resistant alloys may be difficult to form in manufacturing due to the alloying elements present in the material. Therefore, creep directly affects the manufacturing methods needed to fabricate parts. Additionally, machinery and tools can be deformed by Coble creep which can harm manufacturing efficiency and product quality. Consequently, the proper design of tools necessitates the effects of creep be considered.
How Can Coble Creep Be Prevented?
Coble creep can be prevented or slowed by several methods, as listed below:
- Use a Material with a Higher Melting Temperature: Using a material with a higher melting temperature means that the service temperature will be a smaller fraction of the melting temperature.
- Reduce Operating Temperatures: Atoms have less energy and are less likely to diffuse throughout the material’s microstructure at lower operating temperatures. However, lowering operating temperatures is not always practical. The service environment is what it is. While directly reducing operating temperatures may be impractical, using a material with better conductive or convective cooling may achieve the same effects.
- Use a Material With a Larger Grain Size: Using a material with a larger grain size can help mitigate the effects of Coble creep since a larger grain size provides less easy grain boundary surface area for diffusion to occur. Larger grain sizes can be obtained by annealing.
- Use a Material with Columnar Grains or a Single-Crystal Material: Materials with columnar grains, or long, slender, and parallel grains help prevent Coble creep. Fewer transverse grain boundaries provide creep resistance. Using a single-crystal material, or a material with a single crystal and thus no grain boundaries, is also another way to prevent Coble creep.
- Use Specific Alloys: Using an alloy designed to inhibit creep through the presence of grain boundary precipitates can help to prevent Coble creep. These precipitates help prevent grain-boundary sliding due to atomic diffusion and also help limit dislocation glide and climb.
- Reduce Applied Stress: Reducing the stress applied to a material can help limit the effects of Coble creep. This is because stress promotes the diffusion of atoms. While directly reducing the loads experienced by a part is not always practical, increasing the material’s cross-section area can help reduce stress in the part.
How Does Coble Creep Compare to Diffusion Creep?
Coble creep is one type of diffusion creep. Diffusion creep is characterized by the movement of atoms within a material’s microstructure. In Coble creep, this movement is defined as the diffusion of atoms along grain boundaries. Nabarro-Herring creep, another form of diffusion creep, is characterized by the movement of atoms across the grains of material.
How Is the Coble Creep Rate Derived?
The Coble creep rate, like all other types of creep rate, is defined as the change in strain over time due to constant applied stress. However, in Coble creep, the diffusion of atoms is the main mechanism for deformation. The equation for the Coble creep rate is shown below:
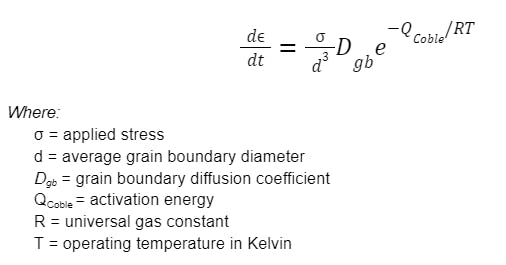
Coble creep equation.
From the creep equation, it can be seen that the rate of strain is directly proportional to the applied stress and inversely proportional to the grain boundary diameter. Therefore, both higher stress values and smaller grain boundary diameters lead to higher strain rates.
Does Coble Creep Occur in Ductile Metals?
Yes, Coble creep occurs in ductile but also brittle materials. Coble creep is more easily observed in ductile materials since they typically experience 3 stages of creep: primary, secondary, and tertiary creep. Primary creep is characterized by the initial decrease of the material’s strain rate, secondary creep is characterized by a steady-state strain rate and tertiary creep is characterized by accelerated strain rate and fracture. Brittle materials experience one stage of creep that is often directly proportional to time and leads to fracture. For more information, see our guide on the Most Ductile Metals.
Is Coble Creep Caused by High Temperature?
Yes, Coble creep is caused by high temperatures in conjunction with applied stress and the passage of time. Coble creep does not occur simply due to high temperatures. While high temperatures energize atoms and enable them to diffuse along grain boundaries, the application of stress and the passage of time hastens the Coble creep process. While high temperature is the largest influencing factor in Coble creep, grain size, crystal orientation, and chemical composition also have an impact on Coble creep rate.
Is Coble Creep Sensitive to Grain Size?
Yes, Coble creep is sensitive to grain size. Materials with finer grain sizes are more susceptible to Coble creep than materials with larger grain sizes since there is more grain boundary area for Coble creep to occur.
Does Coble Creep Help Relieve Strain?
No, Coble creep cannot help relieve strain caused by applied stresses. This is because Coble creep is a type of deformation, alongside elastic and plastic deformation. Therefore, Coble creep is actually a contributor to a material’s strain rather than a relief against strain.
What Is the Difference Between Coble Creep and Solute Drag Creep?
Coble creep is a type of diffusion creep that’s characterized by the diffusion of atoms along a material’s grain boundaries when subjected to high temperatures (40-90% of the material’s melting point) and low applied stress for an extended time. Solute drag creep is a type of dislocation climb creep and is defined as the dislocation of solute or substitutional atoms in a material’s microstructure. For more information, see our guide on Nabarro-Herring Creep.
Summary
This article presented coble creep, explained it, and discussed how it works. To learn more about coble creep, contact a Xometry representative.
Xometry provides a wide range of manufacturing capabilities and other value-added services for all of your prototyping and production needs. Visit our website to learn more or to request a free, no-obligation quote.
Disclaimer
The content appearing on this webpage is for informational purposes only. Xometry makes no representation or warranty of any kind, be it expressed or implied, as to the accuracy, completeness, or validity of the information. Any performance parameters, geometric tolerances, specific design features, quality and types of materials, or processes should not be inferred to represent what will be delivered by third-party suppliers or manufacturers through Xometry’s network. Buyers seeking quotes for parts are responsible for defining the specific requirements for those parts. Please refer to our terms and conditions for more information.
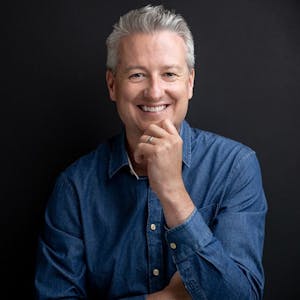