There are a few key equations you can’t escape in the world of manufacturing and engineering, and elongation at break is certainly one. Knowing what this valuable principle calculates can help you select the right materials—and be the difference between a successful and functional product. If you want to know all about this equation, how it works, and why it’s good to know it, keep on reading.
What is Elongation at Break?
This measurement is used to figure out how long a material can stretch before it snaps, breaks, or fractures (that’s why it’s also called the “fracture strain”). The value itself shows the change between a material’s starting length and just how much it has stretched. It’s also a great value for understanding how much materials (like plastics, metals, or textiles) can deform before they’re unsafe or unusable, which can affect things as simple as their looks and as important as their safety. It gives you a great idea of how much fatigue a material can handle, which in turn leads to better selections so that the products you make won’t break unexpectedly.
The Formula
There is a specific formula you can follow to find the elongation at break for a wide range of materials, and it’s normally expressed as a percentage. It’s pretty simple once you know how, but it involves a few different measurements:
Elongation at Break = (Final Length - Original Length) / Original Length x 100%
Here are the steps you can take to figure out a material’s elongation when it fractures:
- First, measure the original length of your material before you start testing it
- Using one of the standard methods out there, complete a tensile test
- When the material gets to its breaking point (or fracturing fracture), take the measurements for the final length
- With those measurements you can fill out your equation to get the exact percentage
An example equation using aluminum could look something like this:
- Measure the original length of your piece of aluminum (we’ll use 50 mm as an example)
- Then do your tensile test. Once the aluminum snaps, measure its length now (say it fractured at a length of 75 mm)
- To find the change in length, you would calculate 75 mm - 50 mm = 25 mm.
- You can then complete the elongation at break equation, which would look like this:
Elongation at break = (change in length / original length) x 100%
Elongation at break = (25 mm / 50 mm) x 100%
Elongation at break = 50%
The image below is a visual representation of the stress strain curve and how elongation at break would be deciphered on a graph:
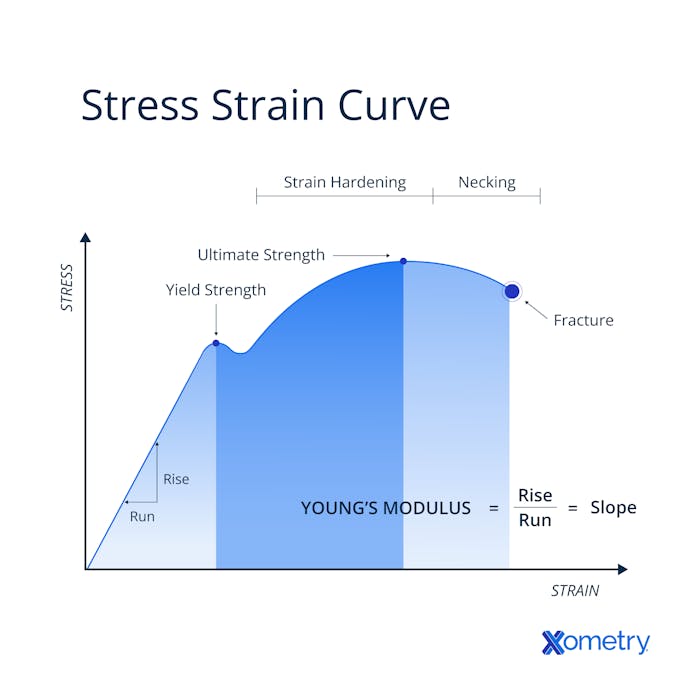
Example Values for Different 3D-Printed Materials
Elongation at break is used a lot for testing how 3D-printed materials hold up under stretching and tensile stress. The value ranges of the most common printer materials are as follows:
- PLA: 5–10%
- ABS: 5–50%
- PETG: 58–110%
- TPU: 400–700%
- Nylon: 5–120%
Materials You Can Test for Elongation at Break
There are numerous materials you can run through a tensile test and get their fracture strain values. These tend to be the most common:
1. Steel
Different steel types will have slightly different properties, which will also change their elongation at break point, but you’ll typically find it range between 10% and 20%.
2. Textiles
The measurement is important in textiles as it can let you know when the fabric of a car seat or industrial fabric will break. Textiles are vastly different, of course, but as a few examples, you’ll find cotton has a 4–8% range, wool is usually between 24% and 45%, and polyester has an impressive value of 50% or higher.
3. Metals and Metal Alloys
Depending on how a metal is made and processed, it can react in a completely different way to a similar metal that may not have been cold forged or that underwent a different process. That’s why it’s important to test metals for their elongation at break values, too. It would take a long time to go through all types, but for context, an aluminum alloy usually has a fracture strain of 17% whereas pure copper will have one of 60%.
4. Polymers
All kinds of polymers get tested in this way, from squeaky polystyrene to shiny PVC, and their ranges are about as varied as the types of plastic and polymers out there. Knowing their values gives a good idea of when these materials will deform and not be able to bounce back and when they’ll break and lose all function. As a few examples, PVC normally has a wide range of 25–58%, but an even wider range comes from polystyrene, which can be anywhere from 1% to 79%. Intrigued? Teflon can have a fracture strain between 40-650%, and polyethylene has one between 300-900%.
5. Rubbers
As one of the stretchier options, natural rubber in its purest form can stretch up to 700% before it breaks. Synthetic rubbers (or fluoroelastomers) reach their point at about 300%.
What Affects Fracture Strain
It’ll depend on the specific characteristics of material, but here are a few factors that take a toll on the elongation at break value of materials.
- Temperature: If the conditions feature warmer temperatures, you’ll tend to get higher readings of elongation at break percentages.
- Velocity during testing: If tensile strain is slowly introduced, you’ll find a material can sometimes stretch longer before breaking.
- Composite fillers: Composite materials with more fillers in them tend to have a lower value.
- Fiber orientation: Depending on how the fibers of a material are woven or aligned can also affect the point at which it snaps.
Common Testing Standards
There are a handful of standardized tests you can lean on for finding elongation values for multiple materials, which their names indicate:
- ISO 527-½ - Plastics: Determination of Tensile Properties
- ASTM D882 - Standard Test Method for the Tensile Properties of Thin Plastic Sheeting
- ISO 37:2017 - Rubber, Vulcanized, or Thermoplastic - Determination of Tensile Stress-Strain Properties
- ASTM D638 - Standard Test Method for Tensile Properties of Plastics
How Xometry Can Help
We work with many different materials here at Xometry and once you’ve selected the one that’s right for you, we have services that cater to various metals, plastics, and composites. If you’re interested in metal extrusion, plastic injection molding, prototyping injection molding, or tube bending, you can get a free quote today.
Check out our Technical Datasheet Glossary to learn more about different material properties.
Copyright and Trademark Notices
- Teflon™ is a registered trademark and a brand name (Teflon ®) owned by Chemours (formally DuPont)
Disclaimer
The content appearing on this webpage is for informational purposes only. Xometry makes no representation or warranty of any kind, be it expressed or implied, as to the accuracy, completeness, or validity of the information. Any performance parameters, geometric tolerances, specific design features, quality and types of materials, or processes should not be inferred to represent what will be delivered by third-party suppliers or manufacturers through Xometry’s network. Buyers seeking quotes for parts are responsible for defining the specific requirements for those parts. Please refer to our terms and conditions for more information.
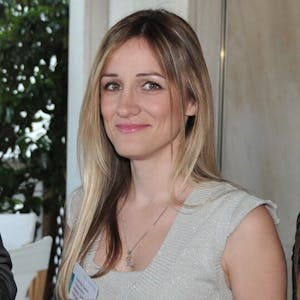