Ferritic stainless steels are a family of chromium-loaded alloys. This chromium content triggers the development of a distinctive crystalline microstructure. They can’t be hardened by heat treatment and are strongly magnetic, with excellent corrosion resistance, particularly in oxidizing environments. They typically have lower strength than austenitic stainless steel.
Ferritic stainless steel’s applications include: automotive exhaust systems due to their heat resistance and particularly strong corrosion resistance in elevated temperature environments; and household appliances, such as washing-machine drums and oven components. This article will further discuss ferritic stainless steel, its composition, types, properties, and applications.
What Is Ferritic Stainless Steel?
Ferritic stainless steel is a category of stainless steel alloy primarily known for its high chromium content, typically ranging from 10.5% to 30%. This composition imparts remarkable resistance to corrosion in oxidizing environments. Unlike austenitic stainless steel, ferritic stainless steel is magnetic due to its crystalline microstructure. It generally contains low carbon content and lacks the nickel that characterizes austenitic grades. This renders it less ductile and less prone to work hardening, limiting its formability.
Despite this, ferritic stainless steel offers advantages such as excellent corrosion resistance, good thermal conductivity, and relatively low thermal expansion. It finds applications in various industries, including: automotive (exhaust systems), appliances (oven components), architecture (decorative trims), and industrial equipment.
What Is the History of Ferritic Stainless Steel?
The history of ferritic stainless steel dates back to the early 20th century. It emerged as a distinct stainless steel category in the 1920s when metallurgists were experimenting with different alloy compositions. In 1924, an alloy containing 17% chromium and 0.3% carbon was developed, marking one of the first ferritic stainless steels. However, these early alloys lacked the corrosion resistance of austenitic stainless steels.
Advancements in the 1930s led to the development of improved ferritic stainless steel grades, containing higher chromium content and other alloying elements. These alloys began to find applications in specific niches, such as automotive exhaust systems and certain architectural components. Over the decades, further research and alloy refinement continued, expanding the range of ferritic stainless steel applications.
Today, ferritic stainless steel remains important in various industries due to its corrosion resistance, heat resistance, and magnetic properties. Its history reflects a continuous evolution driven by the quest to optimize its properties for specific applications while offering an alternative to other stainless steel categories.
What Is the Other Term for Ferritic Stainless Steel?
Ferritic stainless steels are sometimes referred to as chromium steels, or more generically as stainless steel. The specific alternative naming that differentiates ferritic stainless steels from the other stainless steel families is the “400 series” of steels.
What Is Ferritic Stainless Steel Made Of?
Ferritic stainless steel is primarily composed of bulk iron and chromium ranging from 10.5% to 30%; this composition facilitates the ferritic microstructure. These steels typically have a low carbon content, usually less than 0.10%.
Unlike austenitic stainless steel, ferritic stainless steel generally lacks significant amounts of nickel. Some variations might include small quanta of other elements like molybdenum or titanium (and in one case lithium) to enhance specific properties.
How Is Ferritic Stainless Steel Processed?
Ferritic stainless steel is manufactured through a process of smelting steel and alloying with the necessary elements. This smelt is followed by one of several forms of billet casting and then hot and/or cold rolling. The base metals, steel and chromium, are melted in an electric arc or induction furnace. It is generally under an inert atmosphere or a vacuum to maintain purity. Other alloying elements will be added as required for the target alloy. The molten alloy is either pour-cast or continuous-cast into various forms—slabs, billets, or blooms, depending on the intended downstream processes. The cast material is hot or cold rolled or forged into the required shapes. This shapes the material into plates, sheets, or other more finished forms. Annealing involves heating the material to a temperature that dissolves crystal boundaries and then gradually cooling it to relieve stresses and refine the microstructure. The material is then subjected to various final manufacturing processes.
What Are the Characteristics of Ferritic Stainless Steel?
Ferritic stainless steel possesses various distinctive characteristics that suit specific applications. These include:
- Offers good resistance to corrosion in oxidizing environments. This is lower than that of austenitic stainless steel due to the absence of nickel. Have lower ductility than some alloy grades. While they can be cold-worked, they are less ductile/malleable as the BCC microstructure is more resistant to the development of slip planes.
- Carries the tendency to form brittle structures upon cooling.
- Generally more resistant to stress corrosion cracking than austenitic grades.
- Often more cost-effective than austenitic stainless steel because nickel is a very high-cost constituent, absent from these alloys.
What Is the Color of Ferritic Stainless Steel?
Like all stainless steels, the ferritic alloys have a lustrous silver finish, which when flat and polished offers a true (not color distorted) reflection as a mirror finish.
What Does Ferritic Stainless Steel Look Like?
Ferritic stainless steel is silver in color and presents a surface whose reflectivity depends highly on its texture. In common use, ferritic components either have a matte/lightly textured surface or a highly polished and reflective finish.
What Are the Properties of Ferritic Stainless Steel?
Ferritic stainless steels have a wide range of highly beneficial properties that suit many industrial, infrastructure, transport, and consumer-product applications. Some of their properties are:
- They are magnetic.
- Can withstand moderately high temperatures.
- Have relatively good thermal conductivity.
- Offer good resistance to corrosion in oxidizing environments.
- Have lower ductility than some alloy grades.
What Are the Physical Properties of Ferritic Stainless Steel?
Table 1 lists the physical properties of two ferritic stainless steels:
Properties | Alloy 430 | Alloy 444 | Medium-carbon steel (for reference) |
---|---|---|---|
Properties Yield strength MPa | Alloy 430 205 | Alloy 444 275 | Medium-carbon steel (for reference) 300 |
Properties Tensile strength MPa | Alloy 430 450 | Alloy 444 415 | Medium-carbon steel (for reference) 650 |
Properties Elongation at fracture % | Alloy 430 22 | Alloy 444 22 | Medium-carbon steel (for reference) 25 |
Properties Hardness Rockwell B | Alloy 430 72 | Alloy 444 72 | Medium-carbon steel (for reference) 84 |
Properties Bulk modulus | Alloy 430 220 | Alloy 444 220 | Medium-carbon steel (for reference) 215 |
Properties Density kg/m3 | Alloy 430 7,700 | Alloy 444 7,700 | Medium-carbon steel (for reference) 7,800 |
Property | Typical for Ferritic Stainless Alloys |
---|---|
Property Chromium % | Typical for Ferritic Stainless Alloys 10.5–30 |
Property Carbon % | Typical for Ferritic Stainless Alloys 0.12 typical |
Property Chloride tolerance | Typical for Ferritic Stainless Alloys Low |
Property Acid tolerance | Typical for Ferritic Stainless Alloys Moderate |
Property Heat tolerance (oxygen atmosphere) | Typical for Ferritic Stainless Alloys Intermittent to 870°C, continuous to 815°C |
Property Nickel % | Typical for Ferritic Stainless Alloys 0–0.5 |
Property Manganese and Silicon % | Typical for Ferritic Stainless Alloys Max 1.0 |
What Are the Different Types of Ferritic Stainless Steel grades?
Listed and discussed below are the different types of ferritic stainless steel:
1. 439 Stainless Steel
439 stainless steel is a ferritic stainless steel alloy with a composition that includes: chromium, titanium, and niobium. It offers good corrosion resistance in mildly corrosive environments. This property makes it suitable for: automotive exhaust systems, catalytic converters, and applications in which heat resistance is required. With its lower carbon content compared with other ferritic stainless steels, 439 is less prone to sensitization and intergranular corrosion. Its magnetic properties and cost-effectiveness further contribute to its use in various industrial and architectural applications. Titanium and niobium enhance oxidation resistance and flaking at elevated temperatures.
2. 446 Stainless Steel
446 stainless steel possesses optimized resistance to oxidation at high operational temperatures. It includes elevated levels of chromium and additions of molybdenum and silicon. It is widely used for applications involving high temperatures, such as: industrial furnaces, chemical processing, and power generation equipment. Its unique combination of properties makes it suitable for specialized applications in which high-temperature performance is a specific need.
3. 430 Li Stainless Steel
430 Li stainless steel is a relatively new and specialized alloy with a structure that is referred to as 'Low Interstitials' (Li), meaning the lattice is formed mainly by alloy component displacements rather than alloy agents lying interstitial between matrix regions. This improves the material's formability and strength which allows the potential for weight reduction in weight-critical applications. The increased ductility and reduced work-hardening tendency, compared with traditional 430 stainless steel, make it suitable for deep drawing and forming applications. The low interstitial structure also induces reduced magnetic permeability, making the alloy suited to applications in which magnetic properties are required to be minimized. 430 Li stainless steel is an innovation aimed at addressing specific engineering challenges while maintaining the corrosion resistance and relative cost-effectiveness of traditional ferritic stainless steel.
4. 442 Stainless Steel
442 stainless steel is an alloy with relatively high chromium content (around 18–23%) and moderate carbon content. It includes small quanta of molybdenum and titanium, giving it improved high-temperature oxidation resistance. This alloy is designed for applications requiring resistance to elevated temperatures and oxidation scalings, such as: automotive exhaust systems, mufflers, and certain industrial environments such as flue ducts. However, its corrosion resistance is limited in aggressive environments.
5. 430 Stainless Steel
430 stainless steel is a widely used alloy formed using relatively high chromium content and providing only moderate corrosion resistance. It contains 16–18% chromium and low carbon content, making it susceptible to high sensitization. This limits its resistance to aggressive environments. It has good formability, making it suitable for applications like: kitchen appliances, automotive trim, and decorative architectural/product applications. It is recommended for highly corrosive or high-temperature environments. Its affordability and aesthetic appeal, however, make it a preferred choice for thermally and chemically less demanding roles.
6. 434 Stainless Steel
434 stainless steel is a ferritic stainless steel alloy of higher molybdenum content compared to some other ferritic grades. With around 16–18% chromium and 0.12–0.20% molybdenum, it has superior corrosion resistance, compared with standard ferritic steels like 430. The alloy is suitable for applications involving exposure to mildly corrosive environments. Its elevated molybdenum content, however, enhances its resistance to pitting and crevice corrosion. Its combination of strength, corrosion resistance, and affordability makes it useful in a wider spectrum of moderate chemical and mechanical stress applications.
7. 444 Stainless Steel
444 stainless steel is a high-chromium alloy with added molybdenum and niobium. With between 18 and 20% chromium, it possesses excellent corrosion resistance under moderately corrosive and mildly acidic conditions. The molybdenum and niobium content enhances its resistance to pitting and crevice corrosion. Because of this, the alloy is considered suitable for industrial and marine environments, as well as architectural applications. Its low carbon content contributes to its improved weldability, with a useful balance of strength, corrosion resistance, and cost-effectiveness. This is a versatile choice for a broad spectrum of applications and market sectors.
8. 409 Stainless Steel
409 stainless steel is a ferritic stainless steel alloy with good corrosion and heat resistance in moderate environments. It contains between 10.5 and 11.75% chromium and a small amount of nickel, which greatly improves its resistance to atmospheric corrosion and oxidation. Low carbon content contributes to its better weldability. It is commonly used in automotive exhaust systems, mufflers, and catalytic converters due to its ability to tolerate high temperatures and corrosive gases. While it delivers the required performance in applications involving heat and exhaust gases, its corrosion resistance may be limited in more aggressive environments such as exposure to sulfur-bearing flue gases.
Is 316 a Ferritic Stainless Steel?
No. 316 has a lower chromium content and contains nickel, giving it an austenitic crystalline structure.
What Are the Applications of Ferritic Stainless Steel?
Ferritic stainless steel has wide-ranging applications across most industries including:
- Automotive: Various ferritic stainless steel grades are widely used in automotive exhaust systems, mufflers, and catalytic converters.
- Appliances: Kitchen appliances such as: stoves, ovens, and refrigerator doors utilize ferritic stainless steel for aesthetic qualities, durability, and corrosion resistance.
- Architecture: These alloys are employed in architectural applications like: decorative trims, cladding, and interior design for good appearance, sufficient strength, and cost-effectiveness.
- Industrial Equipment: Is used extensively in industrial equipment exposed to moderately corrosive environments, such as: chemical processing equipment, heat exchangers, and structural components.
- Heat Exchangers: Ferritic stainless resistance to scaling and corrosion at elevated temperatures makes it suitable for heat exchanger tubing in various moderately aggressive and mild environment industrial processes.
- Energy Sector: It's used in power plants for components like boiler tubing and in-combustion steam generator tubes, in which heat resistance and oxidation resistance are crucial.
- Automotive Trim: Ferritic stainless steel's appearance and the good formability of some alloys make them suitable for automotive trim and decorative elements.
- Food Processing: In applications in which contact with food is involved, ferritic stainless steel's corrosion and stain resistance and easy cleaning properties are advantageous.
- Magnetic Applications: Ferritic stainless steel's magnetic properties are useful in certain electronic and electromagnetic applications.
- Welded Structural Roles: Some ferritic alloys are employed in welded structures in which good mechanical properties and cost-effectiveness are beneficial.
What Are the Benefits of Ferritic Stainless Steel?
Ferritic stainless steel offers several benefits that encourage its widespread use across most sectors, such as:
- Generally good corrosion resistance in moderately corrosive environments.
- Heat resistance enables its use in high-temperature applications.
- Formability and ease of fabrication contribute to its versatility in manufacturing processes.
- Magnetic properties are advantageous in specific electronic and electromagnetic applications.
- Cost-effectiveness is high in comparison with austenitic stainless steel.
What Are the Limitations of Ferritic Stainless Steel?
Ferritic stainless steel has distinct and marked limitations that must be considered when selecting it for specific applications, such as:
- Relatively low corrosion resistance compared to austenitic stainless steel.
- Susceptibility to sensitization and intergranular corrosion can be a concern.
- The mechanical strength and ductility are generally lower than those of austenitic grades.
- Formability is also somewhat restricted due to low ductility.
- Welding can be challenging due to the risk of brittleness and sensitization during the process.
How Does Ferritic Stainless Steel Differ From Regular Stainless Steel?
Ferritic stainless steel differs from most stainless steel categories like austenitic and martensitic steels in some significant regards. Ferritic stainless steel possesses moderate to good corrosion resistance in milder caustic/acidic environments, while austenitic stainless steel provides superior corrosion resistance. Minimized carbon levels and the absence of nickel significantly impact mechanical and thermal properties compared with many grades. The primary benefit they offer relative to other grades is a low cost, as the nickel and exotic metals content is lower than most other stainless steels.
To learn more, see our guide on the Composition of Stainless Steel.
Are Ferritic Stainless Steels Durable?
Yes, ferritic stainless steel is generally durable. This can, however, vary depending on the specific grade and its suitability for the application it's used in. Ferritic stainless steels generally offer good durability in moderately corrosive and acidic environments. Ferritic stainless steels are less environmentally/chemically durable than many other alloy categories such as austenitic or duplex stainless steels. This is particularly true in highly corrosive or aggressive environments.
Is Ferritic Stainless Steel Brittle?
No. Ferritic stainless steel is not inherently brittle, but it can be embrittled by factors such as: its composition, heat treatment, and processing conditions. Relative to some austenitic stainless steel, ferritic stainless steel tends to have lower toughness and ductility (i.e., greater risk of brittle fracture). There is an increased risk of embrittlement under certain conditions, particularly if parts are exposed to excess temperatures or specific environmental factors.
To learn more, see our guide on Brittle Metals.
Will Ferritic Stainless Steel Rust?
Yes, ferritic stainless steel can rust under some narrowly specific conditions that are not land-environment norms. Prolonged exposure to corrosive or acidic environments can lead to iron oxide staining on the surface of ferritic stainless steel, for example. In marine applications, or where chloride ions are otherwise present, moderate to heavy pitting corrosion and iron oxide leaching/staining will result.
Can Ferritic Stainless Steel Be Welded?
Yes, ferritic stainless steels can be welded, although it is not as straightforward a process as for many other alloys. The welding of these alloys is considerably more troublesome than working with austenitic alloys. This is due to the BCC crystalline structure and increased resultant risk of sensitization. Experienced techniques, alloy-appropriate filler rods, and careful post-weld heat treatment can ensure the weld's quality and the material's unaffected corrosion resistance.
Can You Harden Ferritic Stainless Steel?
Yes, although ferritic stainless steels are not hardenable through the traditional heat treatment methods that work well with martensitic alloys. Martensite is the phase responsible for increasing hardness by heating and quenching. However specific alloying additions or cold working of some ferritic alloys can contribute to increased strength to a limited degree.
What Is the Difference Between Ferritic Stainless Steel and Martensitic Stainless Steel?
Ferritic stainless steel has a body-centered cubic (BCC) crystal structure, offering good corrosion resistance in moderate environments. Martensitic alloys, on the other hand, are defined by a body-centered tetragonal (BCT) crystalline matrix. Both ferritic and martensitic stainless steels display varying degrees of high magnetic permeability. This depends on the alloy composition and work hardening and manufacturing processes. Martensitic stainless steels are generally responsive to heat/quench hardening and tempering, unlike ferritic alloys which are not heat-treatable. Ferritic stainless steels are also generally more corrosion-resistant than martensitic alloys, although this can depend on the particular alloys being compared. Finally, martensitic alloys offer greater strength and abrasion resistance than ferritics. Although, this again can depend on the particular alloys being compared and the manufacturing processes applied.
What Is the Difference Between Ferritic Stainless Steel and Austenitic Stainless Steel?
Ferritic stainless steel has a body-centered cubic (BCC) crystal structure. This offers good corrosion resistance in moderate environments. Austenitic alloys are defined by a face-centered cubic (FCC) crystalline matrix. Ferritic stainless steels display varying degrees of high magnetic permeability, depending on the alloy composition and work hardening and manufacturing processes. Austenitic steels, on the other hand, show virtually no magnetic response in their annealed state, with a slight level of permeability developing from work hardening. Ferritic and austenitic alloys are not heat-treatable, but austenitic stainless steels respond strongly to ductile and malleable work by hardening. Ferritic stainless steels are considerably less corrosion resistant than austenitic alloys, although this can depend to a limited degree on the particular alloys being compared. Austenitic alloys also offer greater strength and abrasion resistance than ferritics. However, this again can depend somewhat on the particular alloys being compared and the manufacturing processes applied. Austenitic alloys benefit considerably in strength and resilience terms from their intrinsic ductility.
To learn more, see our guide on Austenitic Stainless Steel.
Summary
This article presented ferritic stainless steel, explained it, and discussed its composition and types. To learn more about ferritic stainless steel, contact a Xometry representative.
Xometry provides a wide range of manufacturing capabilities and other value-added services for all of your prototyping and production needs. Visit our website to learn more or to request a free, no-obligation quote.
Disclaimer
The content appearing on this webpage is for informational purposes only. Xometry makes no representation or warranty of any kind, be it expressed or implied, as to the accuracy, completeness, or validity of the information. Any performance parameters, geometric tolerances, specific design features, quality and types of materials, or processes should not be inferred to represent what will be delivered by third-party suppliers or manufacturers through Xometry’s network. Buyers seeking quotes for parts are responsible for defining the specific requirements for those parts. Please refer to our terms and conditions for more information.
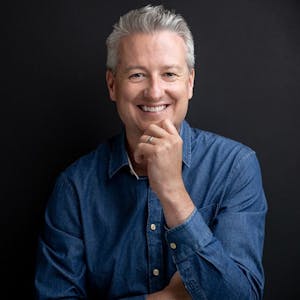