H13 tool steel stands as a versatile and widely employed material renowned for its exceptional attributes and applications across various industries. H13 is a preferred choice in scenarios demanding high-temperature stability, such as: hot forging, die casting, and extrusion. Its adaptability extends to injection mold and die-casting die production, in which its resistance to heat and wear proves invaluable. Despite its many advantages, including excellent thermal shock resistance and thermal fatigue resistance, H13 does have limitations, notably in terms of corrosion resistance and potential brittleness at elevated temperatures.
In this article, we’ll take a closer look at H13 tool steel. We’ll discuss its diverse applications, its composition, properties, advantages and disadvantages, and more.
What Is H13 Tool Steel?
“Tool steels” is an umbrella term used to describe a wide range of carbon and alloy steels that are well-suited for toolmaking. This is due to their distinctive hardness, ability to keep a cutting edge at high temperatures, and their resistance to deform. H13 stands out as a chromium molybdenum hot-work steel renowned for its remarkable resistance to both high temperatures and abrasion. This renders it exceptionally well-suited for a diverse array of applications involving high-temperature operations. The exceptional hot hardness exhibited by H13 serves as a defense against thermal fatigue cracking. H13 is the preferred choice for a multitude of hot-work tooling applications, surpassing the utilization of other tool steels.
How Is H13 Tool Steel Made?
H13 tool steel is made by melting iron along with carefully measured amounts of various alloying elements, including: chromium, molybdenum, and vanadium. These alloying elements are added to achieve the specific composition required for H13 tool steel. The melting process can occur in electric arc furnaces or other specialized furnaces designed for steel production. Alloying elements are then added to the molten metal to achieve the desired composition. This composition is crucial in determining the steel's final properties, such as hardness, toughness, and heat resistance. Once the molten steel has the appropriate composition, it is cast into molds to form ingots or semi-finished shapes.
The cast ingots or semi-finished shapes are then processed further through forging or rolling to shape them into more usable forms, such as bars, plates, or other tooling components. Heat treatment is a critical step in achieving the desired properties of H13 tool steel. The process involves controlled heating and cooling cycles to modify the steel's microstructure. The typical heat treatment processes for H13 include: preheating, austenitizing (high heat), quenching, tempering, and annealing. Once the heat treatment processing is complete, the H13 tool steel may undergo additional machining, grinding, or other finishing operations to achieve the final desired dimensions and surface finish.
How Does H13 Tool Steel Differ From Stainless Steel?
The key distinction between H13 tool steel and stainless steel lies in their compositions. Tool steel is enriched with carbon to achieve high hardness and wear resistance. In contrast, stainless steel's higher chromium content imparts exceptional corrosion resistance. To learn more, see our guide on Stainless Steel Metals.
How Much Does H13 Tool Steel Cost?
The cost of H13 tool steel can vary widely based on factors such as: the current market conditions, supplier, form (e.g., round bars, flat plates, custom shapes), size, quantity, and additional processing requirements. H13 tool steel prices could range anything from around $1,500 to $3,500 per metric ton, depending on these factors.
Is H13 Tool Steel a High-Alloy Steel?
Yes, H13 steel is considered a high-alloy steel. High-alloy steels are characterized by having a significant concentration of alloying elements beyond the basic elements of iron and carbon found in carbon steels. H13 tool steel contains a notable amount of alloying elements such as chromium, molybdenum, and vanadium, which contribute to its enhanced properties. To learn more, see our guide on Alloy Steel.
What Are the Uses of H13 Tool Steel?
H13 steel has the following applications:
- Used in the production of injection molds and die-casting dies due to its high toughness and resistance to heat and wear.
- The high thermal conductivity and resistance to thermal shock make AISI H13 a popular choice for extrusion dies. Additionally, this steel is employed for extrusion mandrels and cores due to its excellent heat resistance and toughness.
- Used in hot-forging applications due to its high resistance to thermal fatigue and excellent toughness. It is commonly used for manufacturing hot-forging dies, inserts, and various other components needed for hot-forging processes.
- Used in tooling for aluminum die casting. It's well-suited for various components like hot-gripper dies, hot-nut tools, and other components used in aluminum die casting.
- Used for the production of plastic molds due to its high toughness and resistance to wear and heat. This steel is also favored for applications such as die holder blocks, hot-press dies, and hot-work punches.
What Is the Chemical Composition of H13 Tool Steel?
The chemical composition of H13 tool steel is outlined in Table 1:
Fe | C | Cr | Mo | V | Si | Ni | Cu | Mn | P | S |
---|---|---|---|---|---|---|---|---|---|---|
Fe Balance | C 0.32–0.45 | Cr 4.75–5.50 | Mo 1.10–1.75 | V 0.80–1.20 | Si 0.80–1.20 | Ni 0.3 | Cu 0.25 | Mn 0.20–0.50 | P <= 0.03 | S <= 0.03 |
Table Credit: https://venturasteels.com/din-2344-aisi-h13-steel/#:~:text=SAE%2F%20AISI%20H13%20tool%20steel,high%20hardenability%20and%20great%20toughness.
What Is the Carbon Content of H13 Tool Steel?
The carbon content of H13 tool steels is approximately 0.4%. Steel H13 falls within the group known as the "H series" of tool steels. These steels are categorized as chromium-based hot-work steels and encompass a moderate carbon content, combined with a chromium content of roughly 5%.
What Are the Properties of H13 Tool Steel?
The physical and mechanical properties of H13 steel are given in Table 2 below:
Property | Metric |
---|---|
Property Density @ 20 °C | Metric 7.80 g/cm3 |
Property Melting temperature | Metric 1,427 °C |
Property Ultimate tensile strength @ 20 °C (varies with heat treatment) | Metric 1,200–1,590 MPa |
Property Tensile strength, yield @ 20 °C (varies with heat treatment) | Metric 1,000–1,380 MPa |
Property Reduction of area @ 20 °C | Metric 50% |
Property Modulus of elasticity @ 20 °C | Metric 215 GPa |
Property Poisson’s ratio | Metric 0.27–0.30 |
Property Machinability | Metric 55% |
Table Credit: https://www.azom.com/article.aspx?ArticleID=9107
The hardness values are also given in Table 3:
Tempering °C after quenching | HRC |
---|---|
Tempering °C after quenching 100 | HRC 54 |
Tempering °C after quenching 210 | HRC 53 |
Tempering °C after quenching 300 | HRC 53 |
Tempering °C after quenching 400 | HRC 55 |
Tempering °C after quenching 500 | HRC 56 |
Tempering °C after quenching 550 | HRC 54 |
Tempering °C after quenching 600 | HRC 51 |
Tempering °C after quenching 650 | HRC 43 |
Tempering °C after quenching 700 | HRC 34 |
Table Credit: https://venturasteels.com/din-2344-aisi-h13-steel/#:~:text=SAE%2F%20AISI%20H13%20tool%20steel,high%20hardenability%20and%20great%20toughness.
What Is the Machinability Rating of H13 Tool Steel?
The machinability rating of H13 tool steel is 55%. This tool steel belongs to the “H series” of tool steels which is classified as chromium hot-work steels with a medium carbon content (0.4%). H series tools steels (H10–H19) typically have machinability ratings of 50–60%. This group represents the most readily machinable category among tool steels and is employed when greater strength and/or hardenability are needed, surpassing what can be achieved with low-alloy steel.
What Are the Characteristics of H13 Tool Steel?
AISI H13 tool steel exhibits the following characteristics:
- Effective resistance to abrasion under both low- and high-temperature conditions.
- High toughness and ductility levels.
- Consistent and remarkable machinability and polishability.
- Strong high-temperature capabilities and resilience against thermal fatigue.
- Hot crack resistant.
- Thermal conductivity.
- Restricted water-cooling capabilities.
- Outstanding through-hardening characteristics.
- Minimal distortion during the hardening process.
Does H13 Tool Steel Rust?
Yes. H13 does not possess inherent resistance to the corrosive effects of chemically aggressive plastics, surface damage caused by moisture and humidity, and contamination from cooling water. These factors can diminish its overall effectiveness in these environments.
Can H13 Tool Steel Be Welded?
Yes, but it has limited weldability. Although it is technically possible to weld H13 steel, it necessitates a thorough understanding of the material's characteristics and careful execution of established welding practices to achieve successful results. The alloy's susceptibility to cracking during and after welding necessitates preheating the material before welding and maintaining suitable interpass temperatures during the process. A post-weld heat treatment (PWHT) is often recommended to relieve residual stresses and minimize the risk of cracking. Opting for gas metal arc welding presents a more favorable option when aiming for swift filling and the seamless joining of larger components. Normally, GTAW (gas tungsten arc welding) is best suited for tool steel due to its control over aim and feeding, and its amperage. Avoiding overheating during welding is also important to preserve the material's microstructure and properties.
Is H13 Tool Steel Corrosion-Resistant?
No, H13 tool steel is not typically considered highly corrosion-resistant compared to stainless steel or other specialized corrosion-resistant alloys. It is primarily used for applications in which its excellent combination of high-temperature strength, wear resistance, toughness, and ability to retain hardness at elevated temperatures are more important factors than corrosion resistance.
While H13 does contain some chromium (approximately 4.75–5.5%), it's not as corrosion-resistant as stainless steels with higher chromium content. H13 is more prone to corrosion than stainless steel, especially in aggressive environments in which exposure to moisture, chemicals, or corrosive gasses is prevalent.
What Are the Thermal Properties of H13 Tool Steel?
The thermal conductivity and coefficient of thermal expansion are given in Tables 4 and 5 below, respectively:
Temperature (°C) | W/m°C |
---|---|
Temperature (°C) 27 | W/m°C 17.6 |
Temperature (°C) 204 | W/m°C 23.4 |
Temperature (°C) 427 | W/m°C 25.1 |
Temperature (°C) 649 | W/m°C 26.8 |
Table Credit: https://hudsontoolsteel.com/technical-data/steelH3
Coefficient of Thermal Expansion (20°C) | 10-4 m/mK |
---|---|
Coefficient of Thermal Expansion (20°C) 20–100 | 10-4 m/mK 10.8 |
Coefficient of Thermal Expansion (20°C) 20–200 | 10-4 m/mK 12 |
Coefficient of Thermal Expansion (20°C) 20–300 | 10-4 m/mK 12.4 |
Coefficient of Thermal Expansion (20°C) 20–400 | 10-4 m/mK 12.7 |
Coefficient of Thermal Expansion (20°C) 20–500 | 10-4 m/mK 13.1 |
Coefficient of Thermal Expansion (20°C) 20–600 | 10-4 m/mK 13.3 |
Coefficient of Thermal Expansion (20°C) 20–700 | 10-4 m/mK 13.5 |
Table Credit: https://venturasteels.com/din-2344-aisi-h13-steel/#:~:text=SAE%2F%20AISI%20H13%20tool%20steel,high%20hardenability%20and%20great%20toughness.
The heat treatment properties are also given in Table 6:
Property | Value |
---|---|
Property Soft annealing °C | Value 760–810 |
Property Cooling | Value Furnace |
Property Hardness HB | Value Max. 240 |
Property Stress-relief annealing °C | Value Approximately 610–660 |
Property Hardening °C | Value 1030–1060 |
Property Quenching | Value Oil, Air, Salt Bath 500–550 °C |
Property Hardness after quenching HRC | Value 55 |
Table Credit: https://venturasteels.com/din-2344-aisi-h13-steel/#:~:text=SAE%2F%20AISI%20H13%20tool%20steel,high%20hardenability%20and%20great%20toughness.
What Are the Common Forms of H13 Tool Steel Material?
H13 tool steel is available in various forms to accommodate different manufacturing and machining needs. Some common forms of H13 tool steel include:
Round Bars and Rods
Round bars are cylindrical bars of H13 tool steel. They are commonly used for making various types of tools, dies, and components that require machining, forging, or shaping.
Flat Bars
Flat bars are rectangular bars with a flat surface. They are often used for applications in which a flat, broad surface is needed, such as: making inserts, punches, and larger tooling components.
Plates
H13 tool steel plates are flat sheets of steel with a uniform thickness. Plates are suitable for applications in which larger, flat surfaces are required, such as making larger molds or die inserts.
Sheets
Similar to plates, sheets are thinner flat pieces of H13 tool steel. They are used for various applications that require thinner sections, such as making intricate tooling components or smaller inserts.
Square Block
H13 tool steel in the form of square blocks is often used for manufacturing larger tooling components and dies. Square blocks can be further machined and shaped to create complex dies for processes like: forging, die casting, and extrusion. Their larger surface area provides ample room for machining and customization.
Hexagonal Steel Bar
Hexagonal steel bars, also known as hex bars, offer advantages in terms of machining and handling. The hexagonal shape provides multiple flat sides that can be easily gripped and rotated during machining operations, reducing the likelihood of slipping. These bars are commonly used to create tools, dies, and components that require precise shaping and machining.
What Are the Equivalents of H13 Tool Steel?
The equivalents for H13 tool steels are listed in Table 7.
USA | Europe | Germany | China | Japan | India | R. of Korea | Russia |
---|---|---|---|---|---|---|---|
USA AISI/SAE | Europe En | Germany DIN, WNr | China GB | Japan JIS | India IS | R. of Korea KS | Russia GOST |
USA H13 | Europe X40CrMoV5-1 | Germany X40CrMoV5-1 | China 4Cr5MoSiV1 | Japan SKD61 | India XT35Cr5MoV1 | R. of Korea STD 61 | Russia 4Ch4VMFS |
What Are the Advantages of Using H13 Tool Steel?
H13 tool steel has many advantages, including:
- Exhibits a good balance between hardness and toughness.
- Can withstand elevated temperatures without losing its hardness and strength.
- Its resistance to thermal fatigue is a significant advantage in applications that involve cyclic heating and cooling, like hot-working processes.
- Can be machined to create complex shapes and intricate details.
- Has good wear resistance due to its hardness.
- Widely used across various industries for different applications.
What Are the Disadvantages of Using H13 Tool Steel?
While there are some notable advantages associated with H13 steel, there are also some drawbacks to consider:
- Is not highly corrosion-resistant, which can be a concern in environments in which the tool or die is exposed to corrosive agents.
- Is relatively expensive compared to some other tool steel options.
- Achieving the desired properties in H13 requires specific and precise heat treatment processes.
- Has limited weldability, and special precautions need to be taken during welding to prevent cracking and preserve its properties.
Is H13 Tool Steel Better Than D2 Tool Steel?
It depends. The "better" selection between H13 and D2 hinges on the specific conditions of your application. Evaluating factors such as temperature conditions, wear attributes, mechanical stress levels, and desired tool longevity will guide your decision. Both H13 and D2 are widely used and versatile tool steels, but they possess distinct qualities that make them better suited for specific scenarios. The major difference between H13 and D2 steel is that H13 steel is a standard hot-work steel, whereas D2 is a cold-work steel.
H13 stands out with its remarkable resistance to high temperatures, thermal shock, and thermal fatigue, rendering it an optimal choice for applications like hot forging, extrusion, and die casting. Its toughness and wear resistance make it particularly fitting for environments in which elevated temperatures and mechanical stresses converge. Conversely, D2 tool steel excels in its exceptional wear resistance, positioning it favorably for tasks demanding an ability to withstand abrasive wear and retain sharp edges over extended use. Well-suited for cutting tools, punches, and dies, D2's high hardness and wear resistance cater to cold-working applications. Notably, D2's heat resistance is somewhat more limited compared to H13, and it may experience a reduction in hardness at elevated temperatures.
What Is the Difference Between H13 Tool Steel and M2 Tool Steel?
H13 tool steel and M2 tool steel are two prominent members of the tool steel family, each offering unique characteristics and suitability for specific applications. H13, classified as a chromium-based hot-work tool steel, boasts notable amounts of chromium, molybdenum, and vanadium in its composition. This blend provides exceptional toughness, making it an excellent choice for applications requiring durability in high-temperature environments such as die casting and forging.
On the other hand, M2, often referred to as high-speed steel, is a tungsten-molybdenum high-speed tool steel. With significant tungsten and molybdenum content, along with other elements like chromium and vanadium, M2 exhibits remarkable hardness and an ability to maintain its cutting edge even at elevated temperatures. This quality renders it ideal for cutting tools like: drills, taps, and milling cutters that demand endurance in high-speed cutting operations.
In its hardened state, H13 steel exhibits greater fracture toughness compared to M2 steel, while the latter possesses higher hardness.
Summary
This article presented H13 tool steel, explained it, and discussed its various uses and composition. To learn more about H13 tool steel, contact a Xometry representative.
Xometry provides a wide range of manufacturing capabilities and other value-added services for all of your prototyping and production needs. Visit our website to learn more or to request a free, no-obligation quote.
Disclaimer
The content appearing on this webpage is for informational purposes only. Xometry makes no representation or warranty of any kind, be it expressed or implied, as to the accuracy, completeness, or validity of the information. Any performance parameters, geometric tolerances, specific design features, quality and types of materials, or processes should not be inferred to represent what will be delivered by third-party suppliers or manufacturers through Xometry’s network. Buyers seeking quotes for parts are responsible for defining the specific requirements for those parts. Please refer to our terms and conditions for more information.
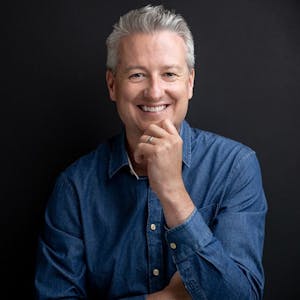