HDPE (high-density polyethylene) and UHMW (ultra-high molecular weight polyethylene) are both thermoplastic polymers made from ethylene monomers. The two plastics are indistinguishable based on appearance. The raw materials for both plastics are the reactive gases ethylene and hydrogen. These are polymerized in the presence of a catalyst, which differs depending on which plastic is being produced: a Ziegler-Natta catalyst for HDPE, or a metallocene catalyst for UHMW.
HDPE can be injection molded or blow molded, or formed into sheets and then further shaped using thermoforming, vacuum forming, or plastic welding techniques. It is a great option for manufactured chemical and water tanks. UHMW is a highly durable, affordable, and abrasion-resistant material used in a variety of wear applications. This article will compare the properties, applications, and costs of HDPE and UHMW.
What Is HDPE?
High-density polyethylene, or HDPE, is a type of thermoplastic polymer. Compared to other polyethylene types, it has a high density (0.95 g/cm3). The polymer chains can be closely packed in this substance because the degree of polymer chain branching is quite low. HDPE is fairly hard and offers good impact resistance. HDPE’s properties are unchanged by exposure to temperatures of up to 120°C and are autoclavable as a result. Some of HDPE's key characteristics are: high impact resistance, autoclavability, opaque/translucent appearance, high strength-to-weight ratio, low liquid permeability, and good chemical resistance.
To produce HDPE, ethylene monomers, a Ziegler-Natta catalyst, hydrogen, and a comonomer are polymerized with a solvent. The solvent's main role is to carry heat away from the reaction sites where polymerization occurs. An external circulation heat exchanger then removes excess heat from the reaction chamber. The separation/drying process receives the reacted slurry. Transferring the slurry to a high-speed centrifuge allows the separation and recycling of the inert solvent from the newly-formed HDPE particles. The HDPE particles are dried under an atmosphere of high-temperature nitrogen and steam, which removes any remaining solvent, and leaves a dry, uniform HDPE powder behind.
In the powder dryer, the solvent is evaporated using high-temperature nitrogen and steam, which dries the wet powders. The scrubber recovers the solvent that has evaporated. The dried HDPE powder is transferred to an extruder, which melts and pelletizes the powder into the final raw HDPE material. Typical applications of HDPE include: containers for liquids, plastic shopping bags, pipe fittings, trays, and cutting boards. For more information, see our guide on What is High Density Polyethylene.
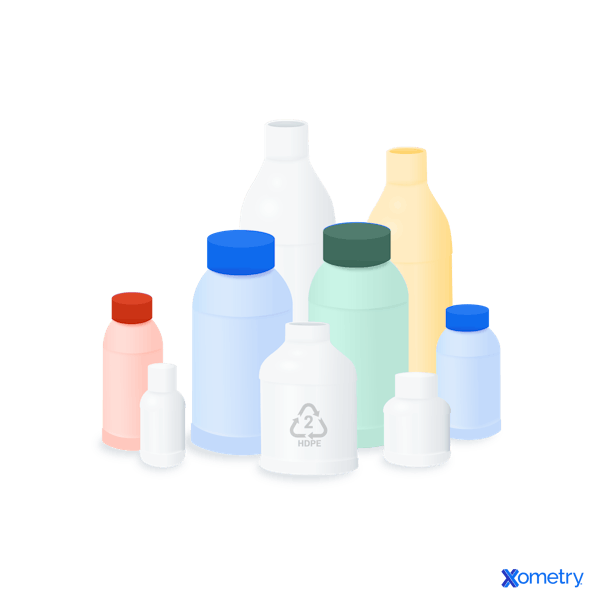
What is UHMW?
Ultra-high molecular weight polyethylene, also known as UHMW or UHMWPE, belongs to the thermoplastic polymer family. UHMW's ultra-high molecular weight (5-9 million AMU) is derived from its extraordinarily long polymer chains, all aligned in the same direction. Van der Waals forces bind each polymer chain to the others in its immediate vicinity. This increases the amount of energy it takes to separate the chains, which gives UHMW its superior toughness and impact resistance.
As with the somewhat lower-density member of the polyethylene family, HDPE, UHMW is produced by the polymerization of ethylene. Differences in the details of the chemical synthesis account for UHMW's greater density. Some of UHMW's key characteristics are: toughness, high impact resistance, crack resistance, non-adhesive properties, and non-toxic nature. Typical applications of UHMW include: star wheels, rollers, gears, screws, and sliding plates. Figure 1 are examples of UHMW plastic:
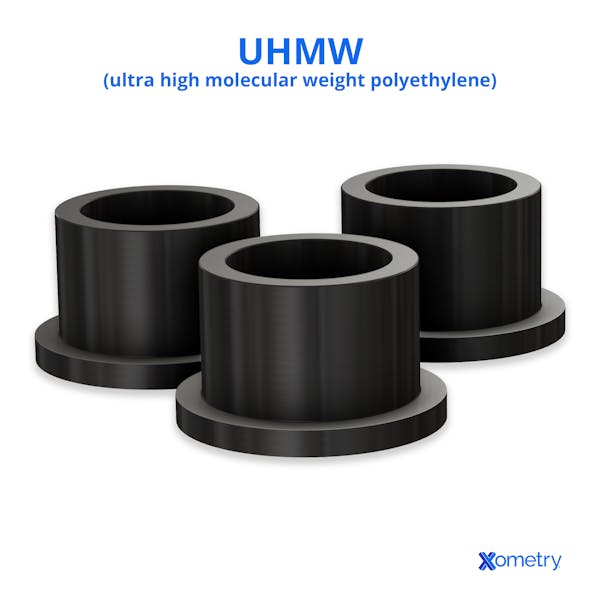
HDPE vs. UHMW: Applications and Uses
Both HDPE and UHMW have wide applications in many industries, due to their favorable properties. In some cases, these materials have shared applications, and for others, only one of the two materials is preferred due to its unique properties. The list below highlights some of the shared applications of HDPE vs. UHMW materials:
- Food and beverage processing and storage gear
- Kitchen gear: Cabinets, counters, and tables
UHMW is a very durable lightweight material that is also chemical and corrosion resistant. Listed below are the UHMW exclusive applications:
- Marine gear
- Assembly production lines
- Wear strips, bearings, star wheels, guide rails, and components of conveyor lines.
- Marine dock parts
- Body armor
- Electrical components
HDPE also has a variety of unique applications. Durability and weather resistance are two of HDPE plastic's most appealing qualities: the material is resistant to insects, rot, mold, and mildew. Additionally, it is easily moldable into virtually any shape, making it ideal for a wide range of products that may spend a lot of time outdoors, such as:
- Patio furniture
- Playground equipment
- Storage containers
- Bins for recycling and trash
- Compost containers
- Plastic wood
- Plastic vehicle components
It's also a common material for kitchen accessories. Cutting boards, cabinets, counters, tables, and small appliances can all be made of HDPE plastic, in addition to a variety of food and beverage container products.
HDPE vs. UHMW: Physical Properties
Both HDPE and UHMW have some impressive physical properties. Table 1 below compares the two materials:
Property | HDPE | UHMW |
---|---|---|
Property Melting Point (°C) | HDPE 118-137 | UHMW 133 |
Property Density (g/cm3) | HDPE 0.93-0.97 | UHMW 0.93-0.95 |
Property Hardness (Shore D) | HDPE 50-76 | UHMW > 63 |
Property Tensile Strength, Yield (MPa) | HDPE 11-43 | UHMW 20 |
Property Tensile Elongation (@ 73°F, %) | HDPE 600 | UHMW 350 |
Property Water Absorption (%) | HDPE 0.010-0.10 | UHMW 0.010 |
Property Chemical Resistance | HDPE Good | UHMW Good |
Property Heat Deflection Temperature at 0.46 MPa (66 psi) (°C) | HDPE 42.8-93.3 | UHMW 65 |
Property Abrasion and Wear Resistance | HDPE Good | UHMW Good |
HDPE vs. UHMW: Recyclability and Sustainability
Both HDPE and UHMW are recyclable, and are considered to be environmentally-friendly plastics. HDPE is one of the easiest plastic materials to recycle. It can be remelted and made into new parts at least 10 times before the quality of the plastic is affected.
UHMW plastic cannot be recycled quite as easily as HDPE. It can only be recycled less than 10 times while maintaining its original properties. Recycled UHMW can be mixed into raw UHMW to further extend its recyclability.
HDPE vs. UHMW: Cost
The cost of both HDPE and UHMW varies depending on the form you purchase it in. The average price for HDPE is roughly $1.2 /kg, and the cost for UHMW can be anything between $2– and –$6 /kg.
Alternative Materials to HDPE and UHMW
Alternative materials to HDPE and UHMW include:
- LDPE (Low-Density Polyethylene): Shopping bags, disposable packaging, clear food containers, and other items are made from LDPE due to its ductility.
- MDPE (Medium-Density Polyethylene): Since MDPE has more polymer chains and is denser, it is frequently used in gas pipes, carrier bags, shrink film, screw closures, and other products.
- ABS (Acrylonitrile-Butadiene-Styrene): Styrene, acrylonitrile, and polybutadiene are polymerized to produce ABS, which is strong, flexible, highly processable, glossy, and impact resistant. ABS is commonly used to fabricate decorative interior car parts, plastic face guards for wall sockets, and protective casings for power tools.
Summary
This article presented HDPE and UHMW, explained what they are, and discussed each are used in manufacturing. To learn more about HDPE and UHMW, contact a Xometry representative.
Xometry provides a wide range of manufacturing capabilities and other value-added services for all of your prototyping and production needs. Visit our website to learn more or to request a free, no-obligation quote.
Disclaimer
The content appearing on this webpage is for informational purposes only. Xometry makes no representation or warranty of any kind, be it expressed or implied, as to the accuracy, completeness, or validity of the information. Any performance parameters, geometric tolerances, specific design features, quality and types of materials, or processes should not be inferred to represent what will be delivered by third-party suppliers or manufacturers through Xometry’s network. Buyers seeking quotes for parts are responsible for defining the specific requirements for those parts. Please refer to our terms and conditions for more information.
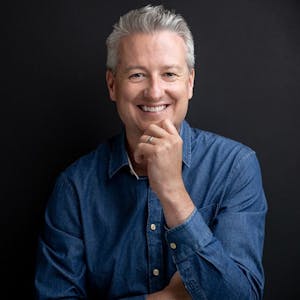