The purpose of hot-dip galvanizing is to protect the material from corrosion by creating a layer of zinc that acts as a protective coating. The process of hot dipping is to submerge the metal into a bath of molten zinc, which metallurgically bonds itself to the material (usually steel). This then protects the material against external elements such as: humidity, moisture, sodium chloride, and acid. The hot-dipped galvanized steel can be used across a wide range of industries, for things such as: roofing, structural beams, automotive bodies, rebar in cement, metal fences, and electrical pylons.
This article will discuss hot-dip galvanizing, how it works, its purpose, uses, advantages, and disadvantages.
What Is Hot-Dip Galvanizing?
The hot-dip process creates steel with a thin protective layer of zinc by dipping the steel into hot molten zinc. During the dipping, the zinc reacts with the steel to make a zinc-iron layer which can protect against corrosion. Hot-dip galvanizing is also referred to as galvanization and galvanizing.
What Is the Purpose of Hot-Dip Galvanizing?
The purpose of hot-dip galvanizing is to form a protective iron-zinc coating on the surface of the steel to protect against corrosion. The coating should cover both internal and external sections of products which are hollow or shelled. The galvanization coating is a sacrificial coating that reacts with the environment to protect the steel beneath it. Hot-dip galvanization also leads to an impact and abrasion-resistant surface when compared to other protective treatments.
What Is the Process of Hot-Dip Galvanizing?
With any parts to be galvanized, it is easier for any welding to be completed before galvanization, as galvanized steel is harder to weld than pre-treated steel. For the galvanization process, the first step is to degrease and clean the surface of the steel of any residues or particles on the surface. This allows the coating to react fully and adhere to the steel. The best method of cleaning is to submerge the part into an alkaline or acid solution and then rinse with cold water. After cleaning, a coating of flux is applied by dipping the part into a 30% zinc ammonium solution at 65–80 °C. This removes any remaining oxide from the surface to allow the molten zinc to react with the steel. The part is then dipped in the molten zinc at approximately 450 °C for approximately 4–5 minutes depending on the thermal inertia of the part. After the hot dip, the now galvanized steel can be air-cooled or quenched if required.
What Is the Right Temperature for Hot-Dip Galvanizing?
The temperature at which steel should be galvanized is 450 °C. The zinc needs to be at this temperature to allow a metallurgical reaction to occur between the zinc and the steel. Any colder and the wetting of the steel would not be optimal and a significant increase in temperature would begin to soften the steel. Additionally, hotter temperatures could cause the part to warp if there are significant internal stresses already in the steel before hot dipping.
Are Hot-Dip Galvanizing and Galvanizing Processes the Same?
No, hot-dip galvanizing and galvanizing processes are not the same. While both achieve the same result they both have different processes. The other processes for galvanizing are galvannealing and electro-galvanization. The galvannealing process is the same as the galvanization process, however after the hot dipping the part is heated up to over 1,050 °C and then air cooled. The annealing part of galvannealing encourages further reaction between the steel and zinc. In electro-galvanization, the steel is electroplated with zinc using zinc salt. This leaves behind a much thinner layer of zinc compared to regular galvanization.
What Is the Minimum Steel Thickness for Hot-Dip Galvanizing?
The thickness and silicon content of the steel being coated will dictate the minimum thickness of coating required. The ASTM A123 specification states that hot-dip galvanization should produce a coating between 1.4 to 3.9 mm thick for the best protection. The silicon content of the steel matters because an increase in silicon content makes the zinc more reactive and therefore a thicker coating will be required to maintain the longevity of the part. A thicker steel will also produce a thicker coating. As there is more iron available in a thicker steel part, more zinc will be required to react with the iron. This will produce a thicker protective layer.
Does Hot-Dip Galvanizing Warp Steel?
Yes, hot-dip galvanization can result in warping. When the steel is hot dipped it heats the steel which can allow the internal stresses in the steel to warp the part. To reduce the chances of this happening the steel can be stress relieved/tempered to reduce the internal stresses of the material.
What Is Hot-Dipped Galvanized Steel Used For?
Hot-dip galvanized steel is used where steel is being used in a corrosive environment. This could be in salt-laden air or marine applications, but could also apply when steel is embedded in soil, concrete, or water. Galvanized steel is a versatile metal that is used in car bodies, bikes, fasteners, structural beams in buildings, rebar in concrete, metal fencing, and electrical pylons.
What Industries Utilize the Use of Hot Dipped Galvanized Steel?
Hot-dipped galvanized steel is used in just about every industry. Hot-dipped galvanized steel is used in the automotive, construction, telecommunications, oil & gas, and aerospace industries, for any application in which steel is in a corrosive environment.
What Are the Properties of Hot-Dipped Galvanized Steel?
Table 1 below describes the properties and benefits of hot-dipped galvanized steel:
Property | Description | Benefit |
---|---|---|
Property Increased Corrosion resistance | Description The material's ability to withstand degradation from the environment | Benefit Increased part longevity and reduced maintenance |
Property Increased Hardness | Description Ability to withstand surface plastic deformation | Benefit Materials that have a high hardness benefit from increased strength and toughness |
Property Increased Abrasion resistance | Description Ability to resist being worn away | Benefit This benefits the steel by allowing it to retain a protective coating even in high-wear applications |
Property Self-healing | Description The self-healing property of galvanized steel comes about because the zinc layer sacrifices itself in a chemical reaction with an electrolyte and leaves behind a corrosion-resistant product to further protect the steel beneath | Benefit The self-healing property allows for a longer-lasting protective treatment |
Can Hot-Dipped Galvanized Steel Be Used in Form Milling?
No, hot-dipped galvanized steel is not typically used in form milling. Form milling tends to be used for cutting materials with irregular contours in a single cut. Form milling cutters tend to be made up of brazed carbide, solid carbide, HSS, and alloy steel rather than hot-dip galvanized steel.
Are Hot-Dipped Galvanized Steel Weldable?
Yes, it is possible to weld galvanized steel, however, it should only be conducted in a worst-case scenario. This is due to the lead exposure and welding fumes (which include vaporized zinc) that are associated with welding materials after they are galvanized which can present significant health risks. Additionally, welding causes potential weak spots in the material after being hot-dipped. To mitigate these risks, it is advisable to carry out welding the material before it is hot dipped and galvanized.
Are Hot-Dipped Galvanized Steels Better Than Galvannealed Steel?
No, hot-dipped galvanized steel is not better than galvannealed steel. While they share several similarities, there are a few differences between these types of steel which means galvanized steel tends to be inferior to galvannealed steel. Firstly, galvannealed steel offers a slightly higher degree of rust and corrosion resistance than hot-dipped galvanized steel due to its stronger coating. Secondly, galvannealed steel coating lends itself to being more weldable than hot-dipped galvanized steel, as well as demonstrating better electrical resistance, melting point, and hardness. Galvannealed steel also has high formability due to the annealing, which makes it highly ductile and strong.
Are Hot-Dipped Galvanized Steels Rustproof?
No, hot-dipped galvanized steels are not completely rustproof. Over time, they will be susceptible to rusting and corrosion from harmful external factors. This is dependent on the thickness of the galvanized zinc coating that protects the material. Even in the thickest coating, however, the steel will eventually succumb to rust. Humidity, sodium chloride (in the air or water), moisture, acids, industrial pollution, cement and plasters containing sulfates and chlorides, moss, and lichen are all factors that will contribute over time to the rusting of hot-dipped galvanized steel.
What Are the Advantages of Hot-Dip Galvanizing?
There are several advantages of hot-dip galvanizing, such as:
- Can last more than 50 years against corrosive elements.
- Hot-dip galvanized metal does not require maintenance after the initial dipping process has taken place.
- Has lower long-term costs as well as lower upfront capital expenditure for the process of galvanizing.
- Is often carried out following standards (such as AS 4680:2006) and is therefore required to have minimum coating thickness to ensure durability.
- Ensures that all parts of the material are dipped in molten zinc, thus providing it with a strong protective coat.
What Are the Disadvantages of Hot-Dip Galvanizing?
Some disadvantages of hot-dip galvanizing are listed below:
- Hot-dip galvanizing can only be executed in a galvanizing plant; the finished product is transported to its final destination.
- Zinc coating must be painted if a different color is required.
- There is potential for some items to warp, such as unsupported, flat sheets of metal or long, slender beams. This is due to the comparatively high temperatures of the molten zinc. This can be mitigated by zoned galvanizing procedures with good design to prevent any distortion from occurring.
- While it is possible to hot dip the vast majority of objects, on occasion it is not possible due to the limited size and dimensions of the zinc bath in which the material is dipped.
Is Hot-Dip Galvanizing Expensive?
No, hot-dip galvanizing is not particularly expensive. It can be a very cost-effective method of protecting material against corrosive elements for several reasons. Firstly, hot dipping the metal in molten zinc has lower initial costs than many other commonly specified protection methods from corrosion for steel. Secondly, the long-lasting life of galvanized steel also makes it a viable option for cutting costs over a long period. Finally, there are no expensive inspection fees or maintenance costs to have to pay for this material.
Is Hot-Dip Galvanizing Worth It?
Yes, hot-dip galvanizing is worth it for manufacturers. Firstly, it is extremely financially beneficial in terms of the process of dipping the material in zinc, which requires comparatively low capital expenditure and has very fast and efficient installation periods. Secondly, it is a long-lasting, reliable solution—it is very durable even in exposure to corrosive elements. Thirdly, it requires little maintenance and is extremely easy to inspect; usually, a simple visual inspection is sufficient. Overall, this makes hot-dip galvanizing an extremely attractive option for manufacturers to protect their material against corrosive elements.
Summary
This article presented hot-dip galvanizing, explained it, and discussed its purpose and process. To learn more about hot-dip galvanizing, contact a Xometry representative.
Xometry provides a wide range of manufacturing capabilities and other value-added services for all of your prototyping and production needs. Visit our website to learn more or to request a free, no-obligation quote.
Disclaimer
The content appearing on this webpage is for informational purposes only. Xometry makes no representation or warranty of any kind, be it expressed or implied, as to the accuracy, completeness, or validity of the information. Any performance parameters, geometric tolerances, specific design features, quality and types of materials, or processes should not be inferred to represent what will be delivered by third-party suppliers or manufacturers through Xometry’s network. Buyers seeking quotes for parts are responsible for defining the specific requirements for those parts. Please refer to our terms and conditions for more information.
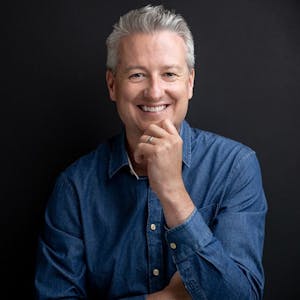