Modulus of resilience is an important characteristic that shows a material's capacity to store and release energy without permanent deformation. It is a measure of the amount of elastic strain energy that a material can absorb before it yields. To determine the modulus of resilience, the stress-strain curve’s area is calculated up until the elastic limit. However, because the elastic limit and yield point tend to be close together, it is possible to estimate the modulus of resilience by determining the area under the stress-strain curve up to the yield point. The higher the modulus of resilience, the better the material's ability to withstand shock loading and cyclic loading.
Choosing materials with appropriate values of modulus of resilience ensures that they can carry out their intended functions efficiently and safely. Modulus of resilience is an essential consideration in the design and production of those materials. This article delves deeper into the definition, determination, significance, applications, and benefits of the modulus of resilience.
What Is the Modulus of Resilience?
The modulus of resilience is the maximum amount of energy that a material can absorb per unit volume without permanently deforming. The term "resilience" describes a material's capacity to absorb and recover from deformation brought on by external forces without suffering long-term deformation or failure. By calculating the area or integral of the stress-strain curve up to the elastic limit, one can calculate the modulus of resilience. However, taking into account the area or integral of the stress-strain curve up until the yield point can provide an estimate of the modulus of resilience given the proximity of the elastic limit and yield point. It is a vital mechanical property for materials used in industries such as the aerospace and automotive sectors, where resistance to deformation and shock absorption are essential.
What Is the Other Term for Modulus of Resilience?
"Strain energy density" is another name for the modulus of resilience. It references the volume-based energy storage capacity of a particular material under conditions of elastic deformation. In materials science and engineering, this phrase is often employed to describe the elastic behavior of materials under stress.
How Does Modulus of Resilience Work?
When calculating a material's modulus of resilience, experts determine how much strain energy it can store per unit volume under conditions of elastic deformation, usually defined as over the range of stress from zero to the elastic limit (or the yield point). Modulus of resilience is a useful parameter for figuring out whether a material is suitable for uses where deformation and shock absorption are fundamental. A material with a high modulus of resilience is more likely to be appropriate for applications requiring deformation and shock absorption, such as the manufacture of automobile bumpers or sports equipment.
What Is the Importance of Modulus of Resilience?
When designing and analyzing structures under various mechanical stresses, the resilience modulus is critical. Not only does it take into account dynamic loading and impact forces, but also general mechanical behavior. It aids in evaluating a material’s capacity for energy absorption and deformation resistance under static loading. Additionally, it aids in the design of structures that can withstand repetitive loading by evaluating resistance to cyclic loading in fatigue scenarios. It also measures a material’s capacity to absorb energy, preventing excessive deformation or failure in situations involving vibration and dynamic oscillations.
For instance, when designing parts for automotive applications, aerospace components, or high-performance sporting goods, the modulus of resilience must be taken into account. For these structures to last for a long time and be safe, a material must be highly resilient so that impact forces can be applied without permanent deformation or damage.
What Is the Significance of Modulus of Resilience in 3D Printing?
The modulus of resilience is an important mechanical property in 3D printing because it helps to determine the material's ability to withstand stress and strain during the printing process. Better prints are produced when a material has a high modulus of resilience because it can withstand the forces of printing without breaking or deforming. When choosing materials for 3D printing applications, this property should be taken into consideration. It can be measured using different testing methods, such as tensile testing or compression testing. For more information, see our guide on how 3D printers work.
How Does the Modulus of Resilience Impact the Quality and Durability of 3D-Printed Parts?
The ability of 3D-printed parts to withstand stress and deformation is impacted by the modulus of resilience. Thus, modulus of resilience ultimately impacts the quality and longevity of 3D-printed products. A higher modulus of resistance can improve the quality and durability of 3D-printed parts by allowing them to accommodate more stress and strain without permanent deformation.
What Materials Are Utilized in 3D Printing With a High Modulus of Resilience?
Thermoplastics such as polycarbonate, nylon-based materials, and carbon fiber-reinforced composites are a few examples of materials that are used in 3D printing and have a relatively high modulus of resilience. Due to their high strength and stiffness, as well as their good impact and fatigue resistance these materials are preferred for certain applications. In high-performance applications like aerospace, automotive, and sporting goods, carbon fiber-reinforced composites, for example, have a resilience modulus that is several times higher than that of conventional plastics. The modulus of resilience of a thermoplastic material like polycarbonate or nylon can be determined using a tensile-testing machine. The machine applies a controlled force to a sample of the material and measures the resulting deformation. The modulus of resilience is then calculated as the area of the stress-strain curve up in the elastic region.
How Can Designers and Engineers Improve 3D-Printed Components' Modulus of Resilience?
Designers and engineers can improve the modulus of resilience in 3D-printed components by choosing materials with higher yield strength or Young’s modulus, optimizing component geometry, utilizing reinforcement techniques, and optimizing printing parameters. To improve mechanical properties, for instance, you might increase infill density and optimize the printing temperature and cooling rate, whereas to increase load-bearing capacity, you might add ribs or other reinforcement structures.
Do All 3D Printing Materials Exhibit the Same Modulus of Resilience Values?
No. Different 3D printing materials have different modulus of resilience values. This is caused by variations in the materials' molecular compositions and structures, which have an impact on their mechanical properties.
What Is the Formula for the Modulus of Resilience?
The modulus of resilience (Ur) is calculated using the formula:
Ur = (σy²) / (2E)
The modulus of resilience is defined as the strain energy per unit volume (U/V) up to the elastic limit. We can calculate this by integrating the area under the stress-strain curve.
Let’s consider a simple linear stress-strain relationship within the elastic range:
σ = Eε
Where:
σ = Stress
E = Modulus of elasticity (Young's modulus)
ε = Strain
The strain energy (U) per unit volume (V) can be calculated by integrating the stress-strain curve:
U/V = ∫₀^ε σ dε
Substituting σ = Eε:
U/V = ∫₀^ε Eε dε
Integrating, we get:
U/V = (1/2)Eε² | from 0 to ε
U/V = (1/2)Eε²
Now, let's relate the strain (ε) to the yield stress (σy) by considering the yield point. At the yield point, the material begins to deform plastically, and the stress remains constant. Therefore, we have:
σy = Eεy
Solving for εy:
εy = σy/E
Substituting εy back into the expression for U/V:
U/V = (1/2)E(σy/E)²
U/V = (1/2)σy²/E
Finally, since the modulus of resilience (Ur) is defined as U/V, we have:
Ur = (1/2)σy²/E
Ur = (σy²)/ (2E)
This equation represents the exact formula for the modulus of resilience, in terms of yield stress (σy) and modulus of elasticity (E).
Where:
- σy= yield strength of the material in megapascals (MPa), which is equivalent to 10^3 kJ/m^3
- E = modulus of elasticity of the material in (MPa), which is equivalent to 10^3 kJ/m^3
You must first ascertain the material's yield strength and modulus of elasticity to calculate the modulus of resilience using the formula above. These values can be obtained by using conventional tensile testing techniques.
How to Calculate the Modulus of Resilience?
The modulus of resilience can be calculated using the following steps:
- Identify the yield strength (σy) and elastic modulus (E) values for the target material. These are obtainable through standard tensile testing procedures.
- If the yield strength value is not already in the kJ/m^3 unit, convert it. Keep in mind that 1 MPa is equal to 10^3 kJ/m^3 and 1Gpa is the same as 10^6.
- Convert the modulus of elasticity value to kJ/m3 if it is not already in this unit.
- Fill in the values from steps 2 and 3 in the formula for the resilience modulus: Ur = (σy^2) / (2E).
- Calculate Ur using the equation.
- The resulting value of Ur will be expressed in terms of kJ/m3, which represents the amount of energy per unit volume that the material can store without permanently changing its shape.
As an illustration, consider a material with a 200 GPa elastic modulus and a 400 MPa yield strength.
First, convert the yield strength to kJ/m^3:
400 MPa = 400 × 103 kJ/m^3 = 4 × 10^5 kJ/m^3
Next, convert the elastic modulus to kJ/m^3:
200 GPa = 200 × 10^6 kJ/m^3 = 2 × 10^8 kJ/m^3
Now, substitute the values into the formula:
Ur = (σy²) / (2E).
Ur = (4 × 10^5 kJ/m^3)^2 / (2 × 10^8 kJ/m^3) = 16 × 10^10 kJ/m^3 / 2 × 10^8 kJ/m^3 = 8 × 10^2 kJ/m^3
Therefore, the modulus of resilience for this material is 800 kJ/m^3.
What Is the Unit Used for the Modulus of Resilience?
Kilojoules per cubic meter (kJ/m3) is the measurement unit for the resilient modulus (Ur). It represents the amount of strain energy per unit volume that a substance can absorb before permanently deforming or failing. This unit reflects the elasticity of the material and can be compared across different materials.
What Are the Different Methods to Measure Modulus of Resilience?
There are several ways to determine the modulus of resilience, including:
- Tensile Testing: Tensile testing is a common and practical technique for determining the modulus of resilience. It is a destructive test process, in which a material is stretched under controlled conditions until it breaks. The modulus of resilience is then determined using the region under the stress-strain curve up to the yield point.
- Compression Testing: Compression testing assesses a material's capacity to withstand crushing forces and regain its original shape following the application of a specific compressive force for a predetermined period. It can be used to calculate the modulus of resilience.
- Flexural Testing: A material is bent until it reaches its yield point during flexural testing. The modulus of resilience is then determined using the area under the stress-strain curve up to the yield point.
- Instrumented Impact Testing: The use of instrumented impact testing enables the direct measurement of several parameters, including: maximum force, yield point, and energy absorbed up to the point of brittle fracture. Additionally, the percentage of shear fracture and fracture toughness can both be calculated using this method.
What Are the Modulus of Resilience of Different Materials?
Here are the modulus of resilience values for some common materials:
1. Aluminum
Aluminum is used in the manufacture of aircraft because of its high strength-to-weight ratio and capacity to absorb significant amounts of energy without permanently deforming. Aluminum alloys have moduli of elasticity and yield strengths that range from 10,000 to 10300 MPa and 3.5 to 20 Mpa, respectively. Moreover, the strongest factor affecting the modulus of resilience is the chemical makeup of each aluminum alloy. One industry where the elastic springiness of aluminum is significant is the production of tennis rackets. Tennis players benefit from aluminum frames' flexibility and durability for more powerful and precise shots. For more information, see our guide on what is aluminum.
2. Copper
Copper is a popular material for electrical systems because it is a good conductor of electricity. However, repeated loads and impacts placed on electrical contacts can lead to deformation and failure over time. Designers can choose the appropriate thickness and shape of contacts to guarantee that they will withstand the anticipated loads without deforming or breaking by knowing the resilience modulus of copper. The modulus of elasticity and yield strength of copper is about 117,000 MPa and 83 MPa respectively. For more information, see our guide on what is copper.
3. Steel
Buildings and bridges are two examples of steel's practical use. Engineers must choose materials that can withstand the stresses and loads applied to the structures while keeping the component weight to a minimum. Steel typically has an elasticity modulus of 210000 MPa. While its yield strength ranges from 200 to 2100 MPa. For more information, see our guide on steel composition.
4. Titanium
Titanium’s resilience can be seen in aerospace applications, where it is used in the construction of aircraft components. Titanium alloys have elastic moduli that range from 55,000 to 114,000 MPa, and their yield strengths are between 240 and 1260 MPa. For more information, see our what type of metal is titanium guide.
5. Polycarbonate
Polycarbonate's remarkable ability to withstand impact makes it an ideal material for bulletproof windows. The modulus of resilience is a crucial factor in this application, as it determines whether the glass can absorb the energy of a bullet without shattering. By utilizing polycarbonate as the primary material for these windows, the impact resistance is significantly increased. Note that polycarbonate alone does not make up all of the material used to make bulletproof glass. To achieve the desired level of protection, it is usually constructed using layers of polycarbonate and other materials, such as tempered glass or acrylic. The result is an impressive thickness that can withstand even the strongest impact. The yield strength of acrylic/polycarbonate alloy ranges from 62.1 to 91.7 MPa, and its elastic modulus ranges from 1720 to 2600 MPa. While ABS/polycarbonate alloy has a modulus of elasticity of 1670 to 11100 MPa and yield strength of 8.2 to 900 MPa.
What Are the Benefits of Modulus Resilience?
Modulus of resilience benefits include:
- Predicting how a material will react to impact loading.
- Making it possible to choose materials that can withstand high stress and impact loading.
- Figure out how much energy a material can store and release, making it useful for applications that absorb energy.
- Providing insights into the design of materials with high durability and elasticity.
What Are the Limitations of Modulus Resilience?
The limitations of relying on the modulus of resilience for product design include:
- It only applies to materials within their elastic limit.
- It doesn't take into account environmental factors such as temperature, humidity, and chemical exposure.
- It doesn't consider the effects of surface conditions or material defects.
- It doesn't provide information on the material's behavior beyond the yield point.
- It can be influenced by the testing method used to determine the yield strength and modulus of elasticity.
Does Material Durability Always Increase With the Modulus of Resilience?
No, the modulus of resilience does not always correlate with an increase in material durability. The modulus of resilience is only one factor to take into account when figuring out a material's durability because it doesn't take other factors like exposure to the environment, fatigue, and wear resistance into account.
Is the Modulus of Resilience the Same as the Modulus of Elasticity?
No, the modulus of resilience is not the same as the modulus of elasticity. While the modulus of elasticity is the ratio of stress to strain in the elastic deformation region. The modulus of resilience, on the other hand, is the amount of energy per unit volume that a material can absorb before yielding.
Is the Modulus of Resilience a Fundamental Material Feature or a Testing Condition?
Yes, the modulus of resilience is a fundamental material feature. It shows how much energy a material can take in and release without experiencing plastic deformation. It is based on the material's elastic modulus and yield strength, two fundamental characteristics.
Can the Modulus of Resilience Predict Material Behavior Under Cyclic Loading?
No, the modulus of resilience cannot forecast how a material will behave when loaded cyclically. When a material is elastically deformed, it can absorb energy; however, cyclic loading and failure eventually involve plastic deformation, which is not taken into account by the modulus of resilience.
Summary
This article presented modulus of resilience, explained it, and discussed its importance and advantages. To learn more about modulus of resilience, contact a Xometry representative.
Xometry provides a wide range of manufacturing capabilities and other value-added services for all of your prototyping and production needs. Visit our website to learn more or to request a free, no-obligation quote.
Disclaimer
The content appearing on this webpage is for informational purposes only. Xometry makes no representation or warranty of any kind, be it expressed or implied, as to the accuracy, completeness, or validity of the information. Any performance parameters, geometric tolerances, specific design features, quality and types of materials, or processes should not be inferred to represent what will be delivered by third-party suppliers or manufacturers through Xometry’s network. Buyers seeking quotes for parts are responsible for defining the specific requirements for those parts. Please refer to our terms and conditions for more information.
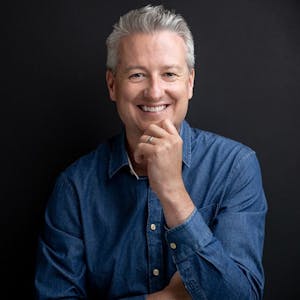