Phosphor bronze and brass are two different metal alloys that have special qualities that make them useful for different purposes. Because of its remarkable strength, resistance to corrosion, and acoustic properties, phosphor bronze—an alloy of copper, tin, and phosphorus—is a highly favored material for use in musical instruments and electrical switches with sliding or moving parts. Conversely, brass—a combination of copper and zinc—has a brilliant, golden look and is ductile, making it a popular material for plumbing fixtures and decorative objects. Phosphor bronzes and brasses are alloy families with lots of variations. Comprehending the principal distinctions between these two metals is essential for making an informed choice between these materials.
This article will discuss the difference between phosphor bronze and brass in terms of composition, applications, advantages, and disadvantages.
What Is Phosphor Bronze?
Phosphor bronze, a copper alloy, incorporates tin and phosphorus to enhance its properties. The inclusion of tin contributes to heightened corrosion resistance and increased strength, while phosphorus imparts good wear resistance and stiffness. This alloy, known for its remarkable combination of strength and corrosion resistance, finds applications in several industries due to its unique set of characteristics. Phosphor bronzes have a narrower electrical conductivity range (11-20% IACS) than brasses (28-56% IACS). However, there are some exceptions displaying higher conductivity.
To learn more, see our full guide on Phosphor Bronze.
What Is Another Name for Phosphor Bronze?
Tin bronze is another term for phosphor bronze. This designation highlights the important part that tin plays in the composition of the alloy. Tin bronze is a popular option in many applications due to its well-known resistance to corrosion, strength, and wear.
What Is Phosphor Bronze Made Of?
Phosphor bronze is composed of copper (balance) with specific proportions of tin and phosphorus. Typically, it consists of 0.5–11% tin and 0.01–0.35% phosphorus. The manufacturing process involves melting and combining these elements, followed by shaping the alloy into various forms to meet specific application requirements.
What Does Phosphor Bronze Look Like?
Phosphor bronze, a reddish-brown alloy, is visually characterized by its warm and distinctive color, offering a rich and appealing aesthetic. This hue is a prominent feature of phosphor bronzes.
What Are the Different Types of Phosphor Bronze?
There are several varieties of phosphor bronze, each designed for a particular use. Table 1 highlights the composition, characteristics, and applications of different types of phosphor bronzes:
Alloy | Composition | Characteristics | Application |
---|---|---|---|
Alloy PB1 | Composition Cu 88–89.5%, Sn 10–11.5%, P ~0.02% | Characteristics Excellent corrosion resistance, good wear resistance, high mechanical strength, good conductivity, suitable for soldering and brazing | Application Washers, gears, bearings; best for medium to high loads |
Alloy PB2 | Composition Cu 85–87%, Sn 11–13%, Pb ~9%, P ~0.02% | Characteristics Higher corrosion resistance, more hard-wearing, better fatigue resistance | Application Similar applications to PB1 with higher wear resistance and loads |
Alloy PB102 | Composition Cu 95%, Sn 4.5–5.5%, P 0.2–0.4% | Characteristics Good corrosion resistance, improved wear resistance, stiffness, and mechanical strength; suitable for cold forming, good weldability, excellent for brazing and soldering | Application Marine and offshore hardware, electrical components, fasteners, decorative components |
Alloy SAE660 | Composition Cu 78–82%, Sn 6–8%, Pb 6–8%, P ~0.02% | Characteristics Good hardness, wear resistance, strength, excellent anti-friction properties, and machinability; does not suffer from dezincification; good resistance to brine and seawater | Application Pump and valve components, bearings, and bushings for medium loads |
What Are the Advantages of Phosphor Bronze?
The advantages of phosphor bronze include:
- Phosphor bronze is a good material for use in applications exposed to seawater, brine, and acids. Its resistance to seawater makes it an excellent choice for maritime applications.
- Phosphor bronze with added lead is suitable for machining applications due to its being easily shaped.
- It offers low friction and excellent sliding properties for applications such as bearings and sealing surfaces.
- Bars made of phosphor bronze have remarkable strength and can bear high tension in demanding applications.
- Despite a higher initial cost compared to brass, selecting phosphor bronze for an application may reduce maintenance needs, extending the life of a component in service.
- Phosphor bronze, with its fair electrical and thermal conductivity, proves invaluable for creating electrical connections in ultra-low-temperature environments. Its properties facilitate efficient energy transfer without introducing excessive heat.
What Are the Disadvantages of Phosphor Bronze?
The disadvantages of phosphor bronze include:
- The dust and fumes produced by phosphor bronze can be toxic when inhaled, posing a health risk. Although, the metal in solid form is not toxic.
- Phosphor bronze may cost more than some potential alternative materials for the same application.
- It is denser than some metals such as: aluminum, antimony, and barium, contributing to higher weight in certain applications.
- Depending on the specific alloy type, phosphor bronze may have limited availability compared to more common metals such as brass and stainless steel.
Is Phosphor Bronze Heavier Than Brass?
Yes, phosphor bronze is generally denser than brass, hence being heavier. Zinc is less dense than tin, so an alloy of copper and tin (bronze) will be denser than an alloy of copper and zinc (brass).
What Is Brass?
Brass is a metallic alloy primarily composed of copper and zinc. The alloy's characteristics can be affected by variations in the percentage of zinc. Brass looks like gold, is malleable, and is resistant to corrosion. It can be found in many different applications, such as: musical instruments, decorative items, plumbing fittings, and electrical components, due to its versatility.
To learn more, see our full guide on Brass Metal Composition.
What Is Another Name for Brass?
Another name for brass is "yellow copper," a historical reference acknowledging the characteristic golden hue derived from its copper-zinc composition.
Are Brass and Brass the Same?
No, brass and bronze are not the same. Bronze is mainly copper and tin, while brass is a copper-zinc alloy. Their varying compositions result in different properties, applications, and characteristics.
To learn more, see our full guide on Bronze Elements.
What Is Brass Made Of?
Brass is a copper and zinc alloy that can be formulated with a range of compositions to suit a variety of uses. Basic brass usually has a composition of 67% copper and 33% zinc, though there is a wide range of possible zinc content in this copper-based alloy. Lead is occasionally added to improve machinability. Brass is a versatile material that can be produced with qualities specifically designed for particular applications.
What Does Brass Look Like?
Brass has a distinctive gold-like appearance, characterized by a warm, yellowish color. This visual aspect, attributed to its copper-zinc composition, makes it easy to recognize in various applications.
What Are the Different Types of Brass?
Table 2 highlights the different types of brass, their composition, properties, and applications:
Brass Type | Composition | Properties | Applications |
---|---|---|---|
Brass Type Alpha Brass | Composition Cu 55–65%, Zn 35–45% | Properties Excellent cold workability, and good corrosion resistance. | Applications Forming, drawing, and decorative applications. |
Brass Type Alpha-Beta Brass | Composition Cu 60%, Zn 40% | Properties Good hot and cold workability, heat-treatable. | Applications Forging, pressing, gears, valves, and fittings that require strength and durability. |
Brass Type High-Zinc Beta Brass | Composition Cu 15%, Zn 85% | Properties Primarily used for die-casting, good wear resistance. | Applications Die-cast components like locks, hinges, and other applications that require wear resistance. |
Brass Type Leaded Brass | Composition Cu 63–66%, Zn 33–37%, Pb 1-3% | Properties Improved machinability, suitable for high-speed machining. | Applications Turned or milled components, plumbing fittings, and decorative hardware. |
Brass Type Naval Brass | Composition Cu 60%, Zn 39%, Sn 1% | Properties High corrosion resistance in seawater. | Applications Marine hardware, ship propellers, bushings, and bearings. |
Brass Type Yellow Brass | Composition Cu 67%, Zn 33% | Properties Bright yellow color, good cold working properties. | Applications Decorative purposes, ammunition casings, plumbing fittings, and musical instruments. |
Brass Type Red Brass | Composition Cu 85%, Zn 15% | Properties Reddish color, good corrosion resistance. | Applications Plumbing applications, casting, decorative hardware, and valves. |
What Are the Advantages of Brass?
Some of the advantages of brass include:
- It is ductile and malleable, allowing it to be drawn into wire or hammered into a sheet without breaking or cracking.
- Brass is a desirable option for a variety of decorative applications since it is affordable and can be aesthetically appealing
- Features a low coefficient of friction, ensuring smooth movement, and does not spark when in contact with other metals, enhancing safety.
- Brass fittings are a preferred material in the building sector because of their corrosion resistance.
- Brass has adequate strength allowing it to be used as material for manufacturing tools such as screwdrivers, pliers, and scrapers.
What Are the Disadvantages of Brass?
Some of the disadvantages of brass include:
- When exposed to ammonia, mercury, or some organic acids, brass can suffer from stress corrosion cracking, which compromises its structural integrity.
- Quickly tarnishes, developing a black or green patina, especially in the presence of oxygen and moisture, diminishing its aesthetic appeal.
- Regular maintenance is necessary to prevent tarnishing. Brass may need to be coated with a clear lacquer to inhibit oxidation and preserve its appearance, adding to the maintenance demands.
- Compared to other common metals like steel, brass is more expensive. The high copper content in brass contributes to its elevated cost.
Is Brass Stronger Than Phosphor Bronze?
No, brass is generally not stronger than phosphor bronze. Phosphor bronze, with the addition of tin and phosphorus, tends to have higher strength and wear resistance than brass, making it suitable for various heavy-duty applications.
How To Choose Between Phosphor Bronze and Brass?
When deciding between brass and phosphor bronze, take into account the particular needs of the application. Phosphor bronze is a good choice for heavy-duty components when increased strength, wear resistance, and design life are essential. When corrosion resistance, beauty, and ease of machining are important considerations, go for brass. Evaluating these factors will help you choose the alloy that is best suited for the purpose you have in mind.
What Are the Properties of Phosphor Bronze and Brass?
Table 3 highlights the properties of phosphor bronze vs. brass:
Property | Phosphor Bronze | Brass |
---|---|---|
Property Composition | Phosphor Bronze Copper alloy with tin and phosphorus | Brass Copper alloy with zinc |
Property Strength | Phosphor Bronze Higher strength, suitable for heavy loads | Brass Generally lower strength compared to bronze |
Property Wear Resistance | Phosphor Bronze Excellent wear resistance | Brass Moderate wear resistance |
Property Corrosion Resistance | Phosphor Bronze Good corrosion resistance | Brass Generally good, depending on the specific alloy |
Property Machinability | Phosphor Bronze Generally good | Brass Excellent, easy-to-machine |
Property Ductility and Malleability | Phosphor Bronze Good ductility and malleability | Brass Generally good, can be drawn into wires |
Property Color | Phosphor Bronze Typically reddish-brown | Brass Gold-like appearance |
How Malleable Are Phosphor Bronze and Brass?
Malleability refers to a material's ability to plastically deform without breaking, allowing it to be shaped or hammered into thin sheets. Phosphor bronze is generally less malleable than brass. While both exhibit good malleability, brass, with its copper-zinc composition, is often more easily worked and drawn into various forms than phosphor bronze.
Do Phosphor Bronze and Brass Rust?
No, neither phosphor bronze nor brass rust because they are not iron-based alloys, both are copper-based. Phosphor bronze alloys, in particular, are known for their tarnish and corrosion resistance, making them suitable for applications in caustic environments. Brass, being a copper-zinc alloy, does not rust either. Its inherent strength, though not as strong as bronze, along with ductility, and corrosion resistance make brass a favored choice, especially in marine applications where it can withstand harsh conditions.
Are Phosphor Bronze and Brass Brittle?
No, phosphor bronze and brass are not inherently brittle. The right amount of tin and phosphorus must be added with other elements to prevent brittleness. Adding elements such as tin strengthens metals. However, if you put enough tin, bronze becomes brittle independent of phosphorus content. Tin is added to copper to form bronze, and zinc is added to copper to form brass, both act as substitutional solutes in the copper matrix, strengthening it and making it less ductile. Copper can tolerate a wider range of zinc content than tin content before becoming brittle. Overall, these alloys display a useful balance between toughness and hardness.
To learn more, see our full guide on Brittleness Examples.
How Can Xometry Assist You With Your Phosphor Bronze or Brass Needs?
Xometry, a leader in the manufacturing-on-demand sector, offers comprehensive solutions for precision manufacturing across many industries. They offer 3D printing, injection molding, CNC machining, milling, turning, sheet metal fabrication, cutting, and finishing. For a wide range of manufacturing demands in materials such as brass and phosphor bronze, Xometry is a reliable partner because of its varied capabilities and dedication to high-quality production.
How To Identify Phosphor Bronze and Brass?
To distinguish between phosphor bronze and brass, observe their color. Phosphor bronze has a distinct reddish-brown hue, owing to its copper-tin makeup with added phosphorus. Brass, on the other hand, appears more yellow or golden due to its copper-zinc composition.
What Are the Applications of Phosphor Bronze and Brass?
The applications of phosphor bronze include:
- Springs: Springs can benefit from the strength, flexibility, and corrosion resistance that phosphor bronze offers. Utilized extensively in industrial and automotive operations, it provides effective energy storage and release.
- Bolts: Corrosion-resistant phosphor bronze bolts, with threaded shafts, find applications in construction, machinery, and marine structures. Known for durability, they provide robust and lasting fastening solutions.
- Bearings: Phosphor bronze is a great material for machinery bearings because of its wear resistance and self-lubricating qualities. These bearings ensure smooth relative motion, which increases system longevity and efficiency.
- Electrical Switches: Phosphor bronze's conductivity and corrosion resistance make it a preferred material for electrical switches. It plays a vital role in controlling electrical flow in various electronic devices and systems.
- Dental Bridges: Dental bridges—prosthetic constructions that replace lost teeth—use biocompatible phosphor bronze. The alloy's corrosion resistance ensures durability, contributing to the longevity and functionality of dental prosthetics.
- Organ Pipes: Phosphor bronze, prized for its acoustical properties, takes center stage in organ pipes. It contributes to the production of rich and resonant tones, enhancing the musical experience in diverse settings.
The applications of brass include:
- Gears: Gear manufacturing uses phosphor brass extensively because of its strength and resistance to wear. These toothed parts are vital to the effective transmission of motion.
- Ammunition Casings: Utilized in the production of ammunition casings, phosphor brass provides durability and corrosion resistance. Bullet shells benefit from the alloy's robust characteristics for containing gunpowder safely.
- Hose Couplings: Hose couplings use phosphor brass as a connection to unite hoses. Reliable and long-lasting connections in fluid conveyance systems are made possible by the alloy's resilience to corrosion and endurance.
- Zippers: In the realm of fastening devices, phosphor brass is employed in zippers. These devices, with interlocking metal teeth, benefit from the alloy's strength and corrosion resistance, ensuring reliable and durable fastening solutions.
- Plumbing: The corrosion resistance and longevity of phosphor brass make it a popular choice for plumbing systems. Long-lasting fluid conveyance systems are ensured by their construction-related contribution to the plumbing networks.
- Locks: Phosphor brass is a key material in the production of locks, providing strength and corrosion resistance. These devices, used for securing doors or containers, benefit from the alloy's robust properties.
- Home Ornaments: Phosphorus brass is used in home décor, such as ornaments. Its durability and aesthetic appeal make it a popular material for creating ornamental pieces that improve a home's ambiance.
- Musical instruments: Brass is a desirable material for building musical instruments because of its outstanding malleability, workability, and somewhat good corrosion resistance.
Each alloy's distinct qualities fill specific needs in diverse fields.
Is Brass a High-Quality Metal?
Yes, brass is considered a high-quality metal. It boasts corrosion resistance, ample strength, and ductility, making it versatile in various applications. With a proven track record spanning thousands of years in human use, brass has consistently demonstrated its reliability and durability, further solidifying its status as a high-quality material.
How Much Do Phosphor Bronze and Brass Cost?
The cost of phosphor bronze and brass varies, with phosphor bronze priced at $4,226.00–4,626.00 per ton, while brass ranges from $3200–5000 per ton.
Is Brass As Good as Gold?
It depends. In practical applications like plumbing fittings or locks, brass is preferred over gold due to its strength and cost-effectiveness. While gold holds unparalleled value in terms of rarity and historical significance, its practical use in certain industries might be limited by its properties and high cost.
Summary
This article presented phosphor bronze and brass, explained each of them, and discussed their various key differences. To learn more about phosphor bronze and brass, contact a Xometry representative.
Xometry provides a wide range of manufacturing capabilities and other value-added services for all of your prototyping and production needs. Visit our website to learn more or to request a free, no-obligation quote.
Disclaimer
The content appearing on this webpage is for informational purposes only. Xometry makes no representation or warranty of any kind, be it expressed or implied, as to the accuracy, completeness, or validity of the information. Any performance parameters, geometric tolerances, specific design features, quality and types of materials, or processes should not be inferred to represent what will be delivered by third-party suppliers or manufacturers through Xometry’s network. Buyers seeking quotes for parts are responsible for defining the specific requirements for those parts. Please refer to our terms and conditions for more information.
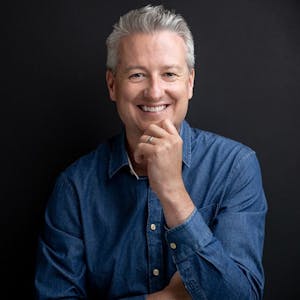