Polycarbonate (PC) is an amorphous thermoplastic with similar light transmission to glass. It is widely used as a glass substitute for its greater durability. The material is also favored for its impact and heat resistance. PC is used for light lenses in automotive applications, and for eyewear, lighting fixtures, greenhouses, medical devices, and protective gear.
PETG is a copolyester thermoplastic. It finds use in most product areas, because of its resistance to impact and most solvents. PETG is also widely used for product and food packaging across all sectors. The majority of PETG is used in making liquid containers for foods/water as it brings no contamination to the contents and remains stable in the long term, even under carbonation pressure-induced creep. This article will compare polycarbonate vs. PETG in terms of applications, properties, and costs.
What Is Polycarbonate?
Polycarbonate (PC) is an amorphous thermoplastic. It is generally considered interchangeable with polymethylmethacrylate (PMMA, or acrylic), although PMMA also has a lower refractive index (1.48), making it less effective for certain optical applications. Molded PC has higher light transmissivity than glass and is widely used as a substitute. Polycarbonate is widely used because of its durability and impact strength. Its scratch resistance is poor, but hard coats counter this. It is suitable for eyewear and lenses because of its relatively high refractive index of 1.58 (allowing thinner lenses for the same focal effect). Low molecular weight grades of PC offer poorer properties than higher weight, but easier processing. Choosing between cost and toughness drives selection; the higher weight grades are widely employed in the aerospace industry, for example.
The toughness of PC is valuable, and it is widely used in automotive applications. The UV stability of PC is relatively low, but the addition of coatings and antioxidants increases its life span. So vehicle light covers don’t yellow and embrittle, as they used to. PC is particularly useful for roofing applications, being tough, relatively low cost, highly transparent in the visible spectrum, and virtually opaque to UV. PC is also an important copolymer addition, adding strength and rigidity to other polymers. However, PC is extremely vulnerable to attacks by oils, solvents, and organic acids; these rapidly break down the polymer and destroy it. This property carries over into many of PC’s copolymer uses.
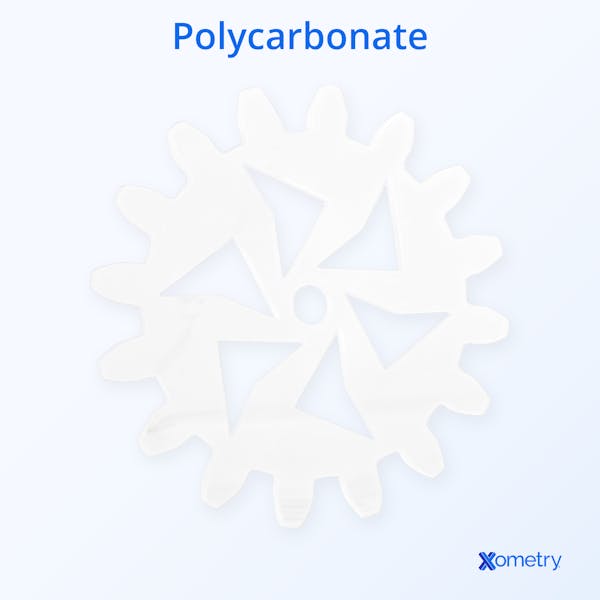
What Is PETG?
PETG (polyethylene terephthalate glycol) is a tough copolyester thermoplastic material. It is an enhanced version of PET (polyethylene terephthalate) in which the glycol component of the PET monomer is modified with the larger monomer molecule, cyclohexane dimethanol. This modification lowers the material’s crystallinity, slightly reduces its processing temperature, and increases its toughness, compared with the original PET. This corrects the tendency of PET to become cloudy due to crystallization at elevated temperatures.
PETG is used in a huge range of applications, because of its toughness, low price, and high degree of formability. It responds well to biaxial orientation—hot stretching in the two axes relative to a sheet handling machine, MD (machine direction), and TD or XD (transverse or cross direction).
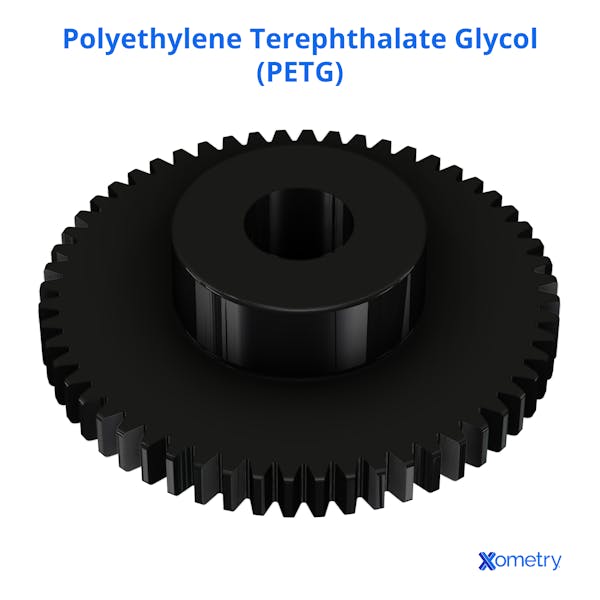
Polycarbonate vs. PETG: Applications and Uses
Listed here are the leading market sectors that utilize polycarbonate (extruded/calendered sheet, and molded items) and their applications:
- Medical Equipment: Cameras, lenses, medical aids.
- Protective Eyewear: Safety goggles, and face shields.
- Optical Components: Human vision corrective and instrument lenses, light guides.
- Automotive: Light covers and lenses.
- Media Discs: Blu-ray, DVDs, etc.
- Domestic and Commercial Paneling: Cupboards, kitchen paneling, handles.
- Display Stands/weatherproofing: Advertising displays, protective covers for advertising, weather shields, barriers in public spaces, and bus stops.
- Agriculture: Greenhouse roofing/windows.
- Lightweight Luggage: Bags and suitcases.
Applications for PETG are less diverse than for PC but are high volume. Examples are:
- Baby Products: Baby food containers and water bottles.
- Medical: Packaging applications, implants, and prosthetics.
- Signage: Strong color results and high UV stability make PETG a good choice in outdoor display and signage applications.
- Engineering: PETG is finding increasing use in machine component applications, because of its easy processing and high strength/durability.
Polycarbonate vs. PETG: Physical Properties
Table 1 below compares the physical properties of polycarbonate and PETG:
Property | PC value (metric) | PETG value (metric) |
---|---|---|
Property Optical transmission | PC value
(metric) Very high, better than glass | PETG value
(metric) Good, can be improved by biaxial orientation in the film |
Property Density | PC value
(metric) 1.2 g/cm3 | PETG value
(metric) 1.18–1.33 g/cm3 |
Property Hardness, Shore D | PC value
(metric) 90–95 | PETG value
(metric) 76 |
Property Tensile strength, ultimate | PC value
(metric) 28–75 MPa | PETG value
(metric) 20–68.9 MPa |
Property Tensile strength, yield | PC value
(metric) 39–70 MPa | PETG value
(metric) 28.3–58.6 MPa |
Property Elongation at break | PC value
(metric) 10–138% | PETG value
(metric) 5–360% |
Property Modulus of elasticity | PC value
(metric) 1.79–3.24 GPa | PETG value
(metric) 3–20.3 GPa |
Property Flexural yield strength | PC value
(metric) 36–103 MPa | PETG value
(metric) 39.2–88.9 MPa |
Property Flexural modulus | PC value
(metric) 0.971–3.1 GPa | PETG value
(metric) 1.17–2.76 GPa |
Property Dielectric constant | PC value
(metric) 2.85–3.17 | PETG value
(metric) 2.4–3.46 |
Property Melting point | PC value
(metric) 288–316 °C | PETG value
(metric) 260 °C |
Property Max service temperature | PC value
(metric) 115–135 °C | PETG value
(metric) 60–70 °C |
Polycarbonate vs. PETG: Recyclability and Sustainability
Polycarbonate (PC) is manufactured from hydrocarbon materials. It's a highly recyclable material that responds well to shredding and re-melt extrusion. This requires rigorous sorting to avoid impurities. PETG products bear the recycling mark ♹ for ease of separation from PET, which is marked ♳. Much of the PETG produced goes into single-use applications and then passes to incineration, or landfill, or is lost to the environment.
Polycarbonate vs. PETG: Cost
PC (polycarbonate) is a low-volume, specialist, and high-cost material, at around $2.80 per kg. Recycled PC material of near-top grade can sell for $1.60 per kg, where a supply chain exists. PETG, on the other hand, is widely used as a feedstock material in 3D printing applications, for which the filament costs between $20–55 per kg. As molded pellets of virgin material, its price ranges from around $1.10 for partially recycled, clear granules to $1.80 for virgin, clear material. Masterbatch color granules achieve up to $4.00 per kg.
Alternative Materials to Polycarbonate and PETG
Alternative material options for polycarbonate (PC) are highly dependent on the application. Examples of alternative materials are:
- Acrylic offers some advantages, such as better scratch resistance and lower temperature working, but it is considerably less strong. Acrylic offers good clarity, but a lower refractive index, making it suitable for windows but less so for lenses. In this case, urethane materials such as Trivex™ offer advantages.
- In lower-grade transparent applications, polystyrene (PS) offers an alternative to PC, but it is considerably weaker and very fracture prone. However, for applications such as light guides, PS can serve well.
- In many cases, ABS is a good alternative to PC, where ultimate strength and flexural resilience are less important.
PETG is an excellent solution to a wide range of packaging and product needs. Alternatives exist in all of the sectors in which it is employed. For example, in packaging films (generally biaxially oriented), alternatives are: BOPP (polypropylene), BOPE (polyethylene, both HDPE and LDPE), PET, and PVC (polyvinyl chloride). For molded and subsequently blow-molded bottles, alternatives are: PET, HDPE, LDPE, and ABS. For food handling/container applications, alternatives are: HDPE, PP (polypropylene), and ABS.
Summary
This article presented polycarbonate and PETG, explained each of them, and discussed their applications and differences. To learn more about polycarbonate and PETG, contact a Xometry representative.
Xometry provides a wide range of manufacturing capabilities and other value-added services for all of your prototyping and production needs. Visit our website to learn more or to request a free, no-obligation quote.
Copyright and Trademark Notice
- Trivex™ is a registered trademark of PPG Industries Ohio, Inc.
Disclaimer
The content appearing on this webpage is for informational purposes only. Xometry makes no representation or warranty of any kind, be it expressed or implied, as to the accuracy, completeness, or validity of the information. Any performance parameters, geometric tolerances, specific design features, quality and types of materials, or processes should not be inferred to represent what will be delivered by third-party suppliers or manufacturers through Xometry’s network. Buyers seeking quotes for parts are responsible for defining the specific requirements for those parts. Please refer to our terms and conditions for more information.
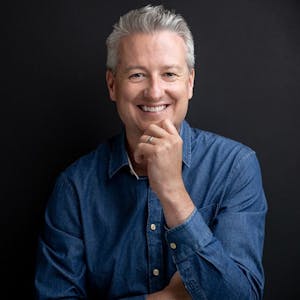