Polystyrene is a type of polymer that is transparent, rigid, brittle, and moderately strong in its unmodified state. It is a plastic made by polymerization, which combines the building block compound called styrene. Polystyrene is used in different forms, including as foam, film, and rigid plastic, for applications from food packaging to electronics protection. While polystyrene’s uses are flexible and it features a low shrink rate, it also flows slowly and can come out brittle. Polystyrene is food safe, though over time it can leach styrene. It’s commonly used in injection molding, and manufactured by companies such as Dow and Trinseo.
What is Polystyrene?
Polystyrene, also known as poly-phenylethene, is a polymer made up of repeating molecules called styrene. It is a thermoplastic polymer, meaning it softens and melts when heated and can be reused. It is an excellent electrical insulator and is resistant to chemicals such as acids and bases. Solid polystyrene is transparent due to the lack of crystalline arrangements of the styrene molecules. It is a brittle material with poor UV resistance. It also has a relatively low glass transition temperature of 100ºC, where the polymer begins to soften before melting. Polystyrene is designated with recycling code number 6, and it can be melted and reused in different shapes or forms.
Polystyrene is usually combined or co-polymerized with other compounds to form plastics with improved properties. For example, polystyrene is combined with methyl methacrylate to form Poly (styrene-co-methyl methacrylate) or PSMMA. The resulting material has higher clarity with enhanced UV and chemical resistance. Another popular plastic called Acrylonitrile Butadiene Styrene (ABS) results from the co-polymerization of acrylonitrile and butadiene with polystyrene. As a result, ABS possesses high tensile strength, weldability, moldability, and dimensional stability.
What Are the Uses of Polystyrene?
Polystyrene is used across all industries, from toys and parts of consumer goods to insulation and packaging materials. It is also the ingredient for the synthesis of new plastics. Polystyrene is used in its solid, film, and foam form, forms the polymer matrix in composites, and works as the basis for co-polymerized plastics.
- Solid or rigid form: this polystyrene type is transparent, rigid, brittle, and moderately strong in its unmodified state.
- Foam form: the most notable use of polystyrene is in a foam form, also known as Expanded Polystyrene (EPS).
- Film Form: films made from polystyrene are transparent, durable, and printable.
- Composites: Polystyrene is used as a base polymer matrix to fabricate fiber reinforced composites.
- Co-polymerized Polystyrene: polystyrene is usually combined with other compounds to synthesize plastics with unique properties. These include ABS, SBR, SAN, and HIPS.
Polystyrene is used in applications from appliances to medical products to automotive parts. Appliances use polystyrene foam as insulation, while its rigid form is used for housings and casings. Electronics also use this material’s rigid form for housings and casings. Polystyrene is also food safe, so it’s used in food service applications as rigid silverware and containers for food and drinks, as well as polystyrene film as part of meat and takeout packaging. The medical field also uses this material in test tubes and Petri dishes. Construction also benefits from this material as polystyrene foam is used as insulation. Another industry that uses polystyrene is the automotive sector, which uses pure polystyrene for children’s protective seats and composites of this material for automotive bodies and components.
Plates and cups can be made from polystyrene, as can sound dampening foam and protective lamination over posters and other products. Wind turbines and corrosion-resistant pipes can also be made of polystyrene. Its co polymerized forms of ABS, SBR, SAN, and HIPS can be used for applications from 3D printed prototypes to optical fibers rubber gaskets to automotive gas tanks.
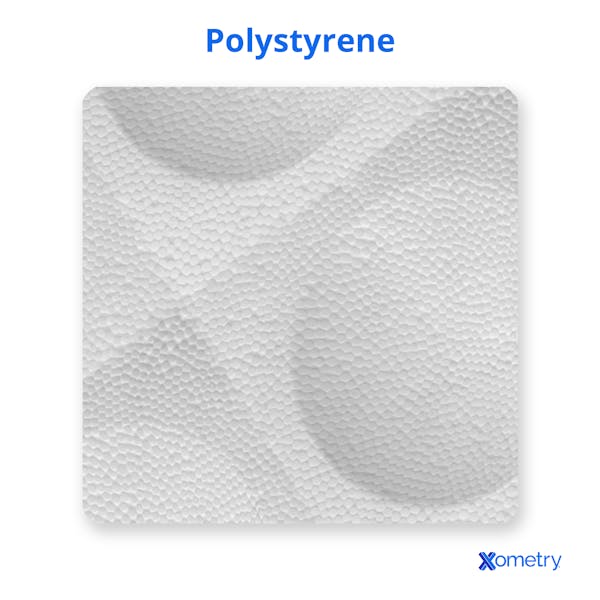
What Are the Advantages of the Plastic Injection Molding Process?
The advantages of polystyrene plastic injection molding are low shrinkage, moldability, and the flexibility to be used in blended and foam form. Polystyrene, like all thermoplastics, is reusable and easily molded. It also features low shrinkage during the plastic injection molding process. Usually, polystyrene shrinks less than 0.5%, which is low compared to other injection molded plastics. This property makes it possible to capture intricate design details of parts. Besides this, polystyrene features less warpage and produces uniform-shaped parts where designers can make accurate dimension predictions of finished parts.
Polystyrene foam can also be used in an injection molding process called structural foam molding to create rigid but light structures for different applications. Co-polymerized polystyrene is injection molded as well to produce parts with improved mechanical properties.
What Are the Disadvantages of the Plastic Injection Molding Process?
The disadvantages of the polystyrene plastic injection molding process are low melt flow index, high melting point, and a short temperature range. Polystyrene melts at a relatively high melting temperature of 210 ºC to 250 ºC, requiring higher energy demand to perform the injection molding process. Polystyrene also has a low melt flow index, with a typical value of 12 to 16 g/10min, which is the ease of flow of molten plastics during the injection molding process, measured in grams of plastic flow in 10 minutes.
The temperature range at which polystyrene begins to soften and melt is relatively short, and the process must be carefully monitored and designed accordingly. Unmodified polystyrene is also brittle, making parts prone to failure during the ejection of parts from the mold. There must be careful ejection pin design to ensure the parts can withstand the flexural stress endured during ejection. Polystyrene co-polymerization with compounds like rubber or butadiene is also often used to improve the material’s impact strength and make the plastic less brittle.
How Does Polystyrene Affect Human Health?
Polystyrene affects human health by releasing styrene when it starts leaching after long periods, which can affect the central nervous system. However, if accidentally ingested, the material will only cause someone to choke if the piece is big enough. Styrene, the main building block of polystyrene, is considered a potential carcinogen by the World Health Organization’s International Agency for Research on Cancer. In the 1980s, the US Environmental Protection Agency (EPA) was able to show that styrene was found in 100% of the samples of human fat taken from 48 states in the United States. Chronic exposure to styrene is dangerous to human health. It affects the central nervous system, causing headaches, fatigue, and confusion.
Is Polystyrene Toxic?
Polystyrene is not toxic, but the exposure of styrene molecules over a long period might create various health problems. Styrene molecules may leach out from polystyrene containers into food and be easily ingested by humans. Polystyrene is generally thought to be safe until it starts to shed, or the migration of styrene occurs in the form of micro or nanoparticles. Several research studies have linked styrene exposure with the risk of cancer. Styrene molecules leaching out of food and drink containers increase the chance of ingesting these molecules.
Is Polystyrene Used for Plastic Injection Molding?
Yes, Polystyrene is used for plastic injection molding; it is the most used plastic material for injection molded parts. Polystyrene can be injection molded in both solid and foam form. Solid polystyrene injection molding provides properties such as low shrinkage, which makes parts less prone to warpage. Added to that, it captures intricate design details of parts well. Due to its high molecular weight, it does have a low melt flow index, which can lengthen the production cycle. Polystyrene is also used in the process called structural foam molding. It is a modified injection molding process with a blowing or foaming process before the material is injected into the mold. This process produces parts that are rigid and lightweight. Polystyrene's brittleness and low melt index are usually improved by co-polymerizing or blending it with other materials to smooth the injection molding process. It also enables the maker to produce parts with high accuracy and good surface finish.
What is the Difference Between Polystyrene and Polypropylene?
The difference between polystyrene and polypropylene is their durability; unlike polystyrene, polypropylene is resistant to more forms of damage. Both polystyrene and polypropylene are polymers, i.e., large molecules with repeating smaller structural units or monomers. Styrene is the monomer for polystyrene, whereas propylene is for polypropylene. Polypropylene is one of the most used plastics in the production of households, food containers, electronics parts, packaging, automotive components, and other industries. Unlike polystyrene, polypropylene is more resistant to UV and organic solvents.
Even though both share similar economic benefits, their application differs according to their physical properties, form, and manufacturing process. Polypropylene is rugged and unbreakable plastic making it more versatile and durable than polystyrene. Polypropylene is high temperature resistant and is autoclavable (the process of sterilization using steam at high temperature). Polystyrene is not autoclavable, but other methods of sterilization such as gamma radiation are employed. Polypropylene is also usually reusable while polystyrene plastics, especially those used for packaging, are disposed of after single use. When injection molding is utilized, polypropylene has a higher melt-flow index and lower melting point than polystyrene. This makes the polypropylene injection molding process less energy-intensive, with a faster production cycle. A positive of using polystyrene compared to polypropylene is that it has a lower shrinkage rate which can affect final plastic product quality and precision. Both polypropylene and polystyrene can be foamed. However, unlike polystyrene, polypropylene in fiber form is used to make ropes with excellent strength and durability.
To learn more, see our guide on Polypropylene vs Polystyrene.
Conclusion
Polystyrene is a popular material in many applications, from parts of consumer goods to insulation and packaging solutions. Its moldability and low shrinkage make polystyrene suitable for injection molding. Moreover, polystyrene is the base material for various co-polymerization processes to produce better plastics with unique properties. It’s also used as polymer matrix for several composite materials.
Thinking about ordering polystyrene products? Engineers at Xometry are ready to help you choose which material and production technique will make your design project a success. Start your quote with Xometry today.
Disclaimer
The content appearing on this webpage is for informational purposes only. Xometry makes no representation or warranty of any kind, be it expressed or implied, as to the accuracy, completeness, or validity of the information. Any performance parameters, geometric tolerances, specific design features, quality and types of materials, or processes should not be inferred to represent what will be delivered by third-party suppliers or manufacturers through Xometry’s network. Buyers seeking quotes for parts are responsible for defining the specific requirements for those parts. Please refer to our terms and conditions for more information.
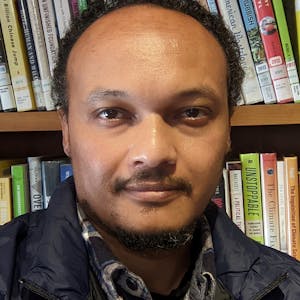