Polypropylene and polystyrene are important materials used in diverse industrial, commercial, and consumer applications. Both are used in pure form and as copolymer agents in a huge range of derivative materials. Polypropylene (PP) is a thermoplastic, consisting of long chains of propylene monomer in regular strands. It is very widely employed in single-use and long-life products from packaging to rope. PP is particularly well suited to roles requiring regular chemical/oil exposure, making it a favorite in the automotive sector.
Polystyrene (PS), on the other hand, is a brittle, clear thermoplastic that responds well to molding, extrusion, and calendering (hot rolling into sheet). It is a very widely utilized plastic, generally for short-life products because of its low cost, and single-use because of its brittleness. Polystyrene is used as a feedstock/component of Acrylonitrile Butadiene Styrene (ABS), as the primary constituent of high-impact polystyrene (HIPS), which is less brittle and usually clouded by the addition of acrylonitrile rubber particles which act to toughen the PS, as an insulating and shock absorbing material, and for floatation aids.
This article will further compare polypropylene vs. polystyrene in terms of applications, physical properties, recyclability, and costs.
What is Polypropylene?
PP is an “addition polymer,” and it can be manufactured in various forms (showing polymorphism), with significant resulting divergence in mechanical, chemical, and thermal properties. The forms are:
- Isotactic Polypropylene (iPP or PPi): This is the main commercially available form, and it demonstrates 30–60% crystallinity, a high melting point (in excess of 160°C), and wide commercial application.
- Polypropylene Fibers: These find wide application in textiles, ropes, etc. The fiber is drawn from a liquid mass, and in so doing experiences near-total alignment of the polymer chains in the line of the drawing, resulting in unique properties that are highly valued.
- Atactic Polypropylene (aPP or PPa): The atactic form possesses no regular structure and has no commercial uses as a sole component. Its disorder prevents any crystallinity from forming. It is a very soft elastic polymer that tears easily and crumbles in compression.
- Block Copolymer Polypropylene: This form is an experimental material that is not currently available commercially. But it has interesting properties as a synthetic elastomer and is made from alternating blocks of atactic and isotactic polymer, providing crystalline regions coupled by elastic, amorphous regions.
- Syndiotactic Polypropylene (sPP or PPs): This form possesses a regular structure, as the monomers alternate in orientation throughout the chains. It offers a much increased electrical breakdown voltage compared to other forms.
- Biaxially-Oriented Polypropylene (BOPP): This form is isotactic polypropylene that has experienced biaxial extension of up to 4.5:1 in the machine direction (MD) and up to 8:1 in the transverse or cross direction (CD). This results in high transparency and enhanced chemical, thermal, and mechanical properties.
These forms have identical chemical constituents, but the regular/irregular orientation of the monomer puts the methyl group (-CH3) to one side or the other, which significantly affects various properties. Mechanical modification then increases the alignment of chains significantly, producing another divergent group of polymorphic forms.
Polypropylene was first synthesized at Phillips Petroleum in 1951 by Paul Hogan and Robert Banks. The process was later scaled up to commercial practicality by Italian and German scientists Natta and Rehn, working in Spain, in 1954. By 1957 it was in widespread use throughout Europe and the US. For more information, see our guide on What is Polypropylene Plastic.
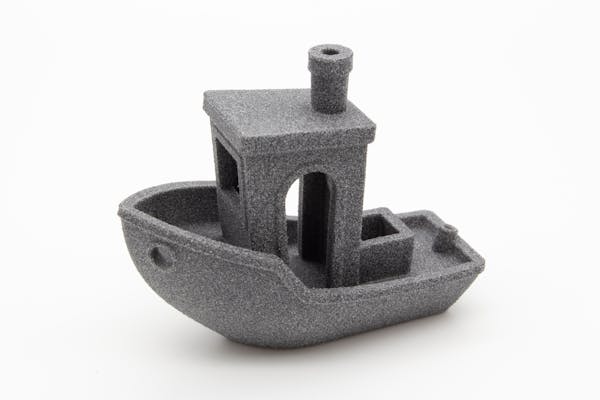
What is Polystyrene?
Polystyrene (PS) is a widely used polymer made by the polymerization of styrene, an aromatic hydrocarbon. PS is employed extensively as an expanded or foamed material, using hydrocarbons or HCFC gas, which dissolve readily in the polymer and can be pulled out of the solution suddenly, by relaxing the applied pressure. The unexpanded form is optically clear but takes opaque and translucent colorants well. It is a hard, brittle material and is a poor-quality barrier to oxygen and water vapor.
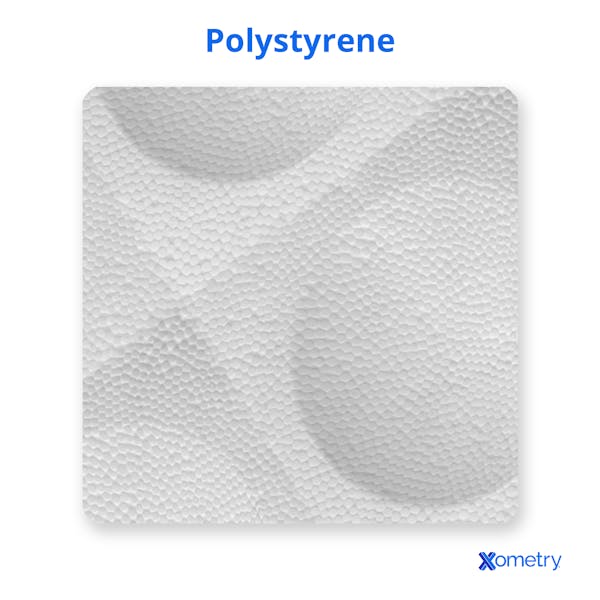
PS is a clear solid at room temperature but liquefies at 240 °C, solidifying again when cooled. This is typical thermoplastic behavior and allows easy manufacturing of complex components by molding and extrusion.
PS has perhaps the longest history of all thermoplastic polymers, having been accidentally discovered by Eduard Simon, a Berlin apothecary, in 1839. He refined a chemical he called styrol from Liquidambar Orientalis or storax. Overnight it thickened to a gel, which he incorrectly took to be the result of oxygenation. This was later understood to be the formation of macromolecules, i.e., partial sterilization. Various experimental discoveries lead to IG Farben manufacturing the polymer resin in 1931. Subsequently, expanded polystyrene was patented by Dow Chemicals in 1949.
Like PP, PS is an addition polymer and can be produced in three basic methods or forms:
- Atactic PS (PS-at): It possesses no order in the orientation of the monomer groups, so it is amorphous. This is the widely manufactured form.
- Syndiotactic PS (PS-st): It has alternating monomer orientations, the product of a Ziegler-Natta polymerization technique. It is made by a limited number of suppliers and is blended with nylon to make a low-weight, high-temperature-stable material used in the automotive sector for electrical components.
- Isotactic PS (PS-it): Its monomers are orientated in the same direction and are not manufactured.
Polypropylene vs. Polystyrene: Applications and Uses
Polypropylene and polystyrene are often considered substitutes for each other, particularly the toughened forms of HIPS and ABS, so it is common to find applications that use both materials.
Listed here are the main market sectors that utilize PP and its applications:
- Packaging (Products and Food): Liquid bottles (not caps), food containers, clear films, and heat-shrink films.
- Automotive: Air handling for engine and AC, interior parts, liners, mud shields, electrical insulators, and lead-acid-battery trays.
- Medical: Syringe barrels, medication containers, tubing, masks.
- Domestic/consumer Products: Household equipment for storage and liquid handling (water tanks, buckets, septic tanks), kettle and kitchen equipment bodies and handles, toothbrushes, baby equipment, pool and pond liners, garden equipment, suitcases.
- Chemical Industries: Pipelines and unstressed valve components for aggressive chemistries.
- Textiles and Carpets: Self-colored and resilient fibers for textiles, carpets, woven tarpaulins, astroturf, and non-woven fabrics for safety gear.
- Furniture: “Cast” resin garden and household furniture, decorative and low-stress cover panels in higher value furniture.
Listed here are the main market sectors that utilize PS (extruded/calendered sheet or molded items) and the applications:
- Packaging: Expanded PS is a very widely employed packaging material as: integral–hinge food containers, cut-block space fillers, and shock absorbers in boxes. HIPS is used for thicker-walled containers and bottles; yogurt pots are another common example of HIPS use.
- Food Packaging: Oriented HIPS offers fairly good clarity, once the monomer extension is significant, making this a good material for clear lids for food packs.
- Automotive: Rigid PS is widely used in interior fixtures and fender panels, in the high-impact and ABS forms.
- Home Appliances: HIPS is widely employed as refrigerator and freezer liners, washing machine and dishwasher parts, kitchen equipment covers, toilet seats, etc.
- Advertising: HIPS is used as a structural material in advertising displays and in bold-colored branding installations.
- Flotation: Expanded PS is widely used as a flotation aid in ships/boats and water toys.
Polypropylene vs. Polystyrene: Physical Properties
Table 1 list some of the physical properties, comparing polypropylene and polystyrene:
Property | Polypropylene | Polystyrene |
---|---|---|
Property Optical transmission | Polypropylene Can be high in some copolymers and in focused materials | Polystyrene Generally high clarity; some cloudiness may occur |
Property Hardness, Rockwell R | Polypropylene 20–118 | Polystyrene 121 |
Property Tensile Strength, Ultimate | Polypropylene 9–80 MPa | Polystyrene 35–59 MPa |
Property Tensile Strength, Yield | Polypropylene 4–1350 MPa | Polystyrene 34–55 MPa |
Property Elongation at break | Polypropylene 2.4–900% | Polystyrene 1–35% |
Property Modulus of Elasticity | Polypropylene 0.08–8.25 GPa | Polystyrene 2.59–4.71 GPa |
Property Flexural Yield Strength | Polypropylene .296–180 MPa | Polystyrene 7.35–106 MPa |
Property Flexural Modulus | Polypropylene 0.026–10 GPa | Polystyrene 1.58–3.45 GPa |
Property Coefficient of friction | Polypropylene 0.25 | Polystyrene 0.33 |
Property Coefficient of thermal expansion | Polypropylene 18.0–185 µm/m-°C | Polystyrene 71–80 µm/m-°C |
Property Melting point | Polypropylene 61–221 °C | Polystyrene 240 °C |
Property Max service temperature | Polypropylene 65–125 °C | Polystyrene 75–122 °C |
Polypropylene vs. Polystyrene: Recyclability and Sustainability
Polypropylene is manufactured from a hydrocarbon source material. No good bio-source alternative supply has been established. It is highly recyclable and, when clean and fully sorted, it is well suited for reuse. Typically, less than 1% of the PP made worldwide is recycled, however.
Polystyrene is manufactured from hydrocarbon sources and requires a moderately high-energy process to polymerize. In their unmodified form, HIPS and ABS forms are amenable to re-melting and production of “new” pellets, once sorted to exclude complicating contamination by incompatible polymers. Such material is considered second-grade, and some depolymerization will result from each melt cycle.
Expanded polystyrene (PS) poses serious environmental issues. Only a very small proportion of the manufactured material is even captured in disposal processes. Its particulate nature and the brittle fragility of PS make it the worst candidate for the inadvertent production of plastic nanoparticles that are an increasing burden in natural systems.
Polypropylene vs. Polystyrene: Cost
Polypropylene granules for molding, extrusion, or film/fiber manufacture typically cost around $1.30 per kg. Recycled material is generally 20 to 40% cheaper, depending on grade. Polystyrene is generally priced at around $1.05 per kg of granules, whereas HIPS costs around $1.20 per kg and ABS costs around $1.45 per kg.
Alternative Materials to Polypropylene and Polystyrene
Polypropylenes also have various alternatives, depending on the application.
- For single-use packaging, PP competes with expanded PS, high- and low-density polyethylene, and PVC.
- In films and heat-shrink wrapping, alternatives are polyethylene (PE) and to a lesser extent PVC.
- In piping and applications requiring chemical resilience, polypropylene competes directly with both HDPE and PVC.
- Finally, in automotive applications, polypropylene is a low-cost alternative to ABS and AES, where cosmetic considerations are outweighed by cost or the need for maximum impact resilience.
Polystyrene has various alternatives in all its commercially available forms including those listed below:
- In expanded packaging and shock-absorbing applications expanded PS can be substituted with a range of materials including: expanded/foamed polyethylene (PE), EVA foam, and expanded polypropylene.
- In sheet form, HIPS is a market leader but acrylic (PMMA) and polycarbonate are good alternatives.
- In single-use applications like disposable cutlery, various options exist, such as: molded plant starch, polypropylene, and polylactic acid (PLA).
- In clear films and semi-rigid sheets, various alternatives are widely used, including: polylactic acid (PLA), biaxially-oriented polypropylene (BOPP), polyethylene, PVC, and polyethylene terephthalate (PET).
- In the automotive sector, polystyrene (PS) can be substituted with the full range of higher-priced engineering polymers, but most commonly: nylons, ABS, polyether ether ketone (PEEK), acetal (POM), and polyethylene (PE).
Disclaimer
The content appearing on this webpage is for informational purposes only. Xometry makes no representation or warranty of any kind, be it expressed or implied, as to the accuracy, completeness, or validity of the information. Any performance parameters, geometric tolerances, specific design features, quality and types of materials, or processes should not be inferred to represent what will be delivered by third-party suppliers or manufacturers through Xometry’s network. Buyers seeking quotes for parts are responsible for defining the specific requirements for those parts. Please refer to our terms and conditions for more information.
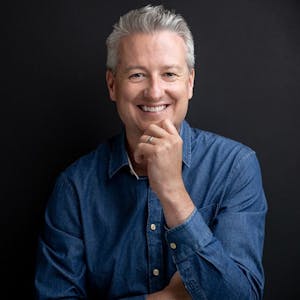