When analyzing the mechanical properties of materials, two important parameters often come into play: shear modulus and Young's modulus. These moduli provide valuable insights into a material's response to external forces and its overall stiffness. However, understanding when and how to employ each modulus correctly is crucial to selecting the right material for different applications. This article will compare shear modulus and Young's modulus, their similarities and differences, how each modulus is calculated, and what the values mean.
What Is the Shear Modulus?
The shear modulus, also known as the modulus of rigidity, is a material property that measures the stiffness of a solid material in response to shear stress. It describes a material's ability to resist deformation when subjected to forces acting parallel or tangentially to its surface.
When a solid material is subjected to shear stress, the material deforms by undergoing shear strain. The shear modulus is an important parameter in various fields of engineering, such as structural analysis, material science, and geotechnical engineering, as it influences the behavior of materials under shear loads and plays a role in determining their mechanical properties.
For information, see our guide on the Shear Modulus Equation.
What Is the Shear Modulus Formula?
The shear modulus formula is mathematically expressed as:
G = τ / γ
Where:
G = shear modulus
τ = shear stress
γ = shear strain
It is expressed in units of pressure, such as pascals (Pa) or pounds per square inch (psi).
What Does Shear Modulus Say About the Material?
The shear modulus is a measure of the material's stiffness in shear. It serves as a valuable indicator in determining the inherent resistance of a material to shear deformation. It quantifies the ratio of shear stress to shear strain within the material’s elastic limit. The shear modulus provides insights into a material's resistance to shearing or twisting deformation. A higher shear modulus implies that the material is more resistant to shear forces and is stiffer in shear. In contrast, a lower shear modulus indicates that the material is more susceptible to shear deformation and is less stiff in shear.
How Is Shear Modulus Calculated?
Determining the shear modulus of a material involves the use of various testing methods.
There are test methods that can determine the shear modulus directly, while other tests can determine the shear modulus indirectly, as long as the E (Young’s modulus) and ν (Poisson’s ratio) are known.
Tests that measure the shear modulus directly include:
ASTM D5379 / D5379M
- Title: Standard Test Method for Shear Properties of Composite Materials by the V-Notched Beam Method (Iosipescu Test)
- Direct shear modulus measurement.
- Commonly used for composites, especially carbon fibre laminates.
ASTM D7078 / D7078M
- Title: Standard Test Method for Shear Properties of Composite Materials by the V-Notched Rail Shear Method
- Improved version of D5379 for in-plane shear modulus in composite laminates.
- Higher load capacity and better alignment.
ASTM D4255 / D4255M
- Title: Standard Test Method for In-Plane Shear Properties of Polymer Matrix Composite Materials by the Rail Shear Method
- Also gives direct shear modulus, especially for polymer composites.
ASTM E143
- Title: Standard Test Method for Shear Modulus at Room Temperature
- Applies to structural metals, done with a torsion test, but it gives the true shear modulus value.
What Is an Example of a Shear Modulus?
An example of a shear modulus can be found in the structural steel used in the construction of large buildings. Structural steel is chosen for its high shear modulus, which allows it to resist deformation caused by shear forces. In the case of buildings, external forces such as wind loading can induce twisting stresses on the structure, resulting in shear stresses in the steel members. The high shear modulus of steel enables it to effectively withstand these shear stresses, ensuring the stability and integrity of the building even under challenging conditions.
The shear modulus of some other common materials is given below:
- Silicone Rubber: 0.0002 GPa (~0.03 × 10⁶ psi)
- Aluminum: 25 GPa (3.6 × 10⁶ psi)
- Steel: 75 GPa (10.9 × 10⁶ psi)
- Copper: 44 GPa (6.4 × 10⁶ psi)
- Iron: 77 GPa (1.12 × 10⁶ psi)
- Brass: 35 GPa (5.1 × 10⁶ psi)
- Lead: 5.6 GPa (0.81 × 10⁶ psi)
What Does a High Shear Modulus Value Mean?
A high shear modulus value indicates that a solid material is highly rigid. It requires a significant amount of force to cause deformation. A shear modulus exceeding 50 GPa is generally regarded as high, considering that many soft metals typically possess shear moduli of 40 GPa or lower.
What Does a Low Shear Modulus Value Mean?
A low shear modulus value suggests that a solid is soft or flexible, requiring only a small force to induce deformation. In general, a shear modulus below 10 GPa is considered low, often indicating materials such as plastics, rubbers, or soft metals. These can deform easily under modest shear forces.
What Material Has the Highest Shear Modulus?
The material with the highest shear modulus is diamond due to the covalent bonds within its carbon lattice. The carbon atoms arrange themselves in a precise diamond cubic crystal structure, resulting in a highly compact lattice that imparts exceptional hardness. A diamond’s shear modulus is typically in the range of 480-520 GPa. However, despite its hardness, diamond is susceptible to breakage along specific planes due to its cleavage properties.
Can Shear Modulus Have Zero Value?
Fluids are characterized by a shear modulus of zero. This means that when subjected to any force, the surface of a fluid will deform without resistance.
What Is Young's Modulus?
Young's modulus, also known as the elastic modulus or modulus of elasticity, is a mechanical property that describes the stiffness or elasticity of a material. It is named after the British scientist Thomas Young, who helped popularize the concept in the early 19th century, though the principle was first formulated by Leonhard Euler.
Young's modulus is defined as the ratio of stress to strain within the elastic limit of a material.
Young's modulus represents the slope of the stress-strain curve in the linear elastic region, in which the material behaves elastically and returns to its original shape after the applied force is removed.
Different materials have different Young's moduli, reflecting their varying stiffness. For example, materials like steel and concrete have high Young's moduli, indicating their relative rigidity and resistance to deformation. In contrast, materials like rubber and foam have low Young's moduli, indicating their greater flexibility and ease of deformation.
What Is the Young's Modulus Formula?
Mathematically, Young's modulus (E) is expressed as:
E = σ / ε
Where:
E = Young's modulus,
σ = stress applied to the material
ε = strain experienced by the material
Young's modulus is typically measured in units of pressure or stress, such as pascals (Pa) or newtons per square meter (N/m²).
What Does Young's Modulus Say About the Material?
Young's modulus is a fundamental material property that provides crucial information about its resistance to stretching and deformation. It characterizes the stiffness and elasticity of a material, shedding light on how it responds to applied forces and its ability to return to its original shape after deformation.
When a material is subjected to an external force or stress, it undergoes a certain amount of deformation or strain. Young's modulus quantifies the relationship between stress and strain, revealing how the material behaves under load. A lower Young's modulus indicates a higher degree of flexibility and ease of deformation in the material. Such materials are more compliant and can undergo larger strains under lower stress levels, though this does not necessarily mean they are more “elastic” in the technical sense. In contrast, a higher Young's modulus indicates that the material is stiffer and less prone to stretching or deforming under the same amount of stress.
How Is Young's Modulus Calculated?
Young’s modulus is determined using standardized mechanical testing procedures that measure the relationship between stress and strain in the elastic region of a material.
The most widely used method involves applying a uniaxial tensile or compressive force to a specimen and recording the resulting deformation.
Tensile Testing with a Universal Testing Machine (UTM)
This is the industry standard for measuring Young’s modulus in metals, polymers, and other structural materials.
- A specimen with standardized geometry (e.g., dogbone shape) is gripped at both ends.
- A gradually increasing load is applied along the specimen's axis.
- An extensometer or displacement sensor measures the elongation in the gauge section.
- Load and displacement data are converted into stress and strain, and the slope of the linear portion of the stress–strain curve yields Young’s modulus (E):
E = σ / ε
(where σ = stress, ε = strain in the elastic region)
Relevant Standards:
ASTM E111 (metals)
ASTM D638 (plastics)
ISO 527 (polymers)
What Are the Factors of Young's Modulus?
Young's modulus (E) is affected by several factors as listed below:
- Influence of Impurities: Impurities or the presence of foreign substances within a material can disrupt the atomic or molecular structure. This can alter the bonding forces and thereby influence the material's stiffness.
- Temperature: In some materials, as the temperature increases, the modulus decreases due to increased atomic vibrations and thermal expansion. However, other materials may exhibit more complex temperature-dependent behavior, with modulus variations that depend on factors such as phase transitions or changes in the crystal structure.
- Pressure: In some cases, particularly in materials that undergo significant compression, applying high pressure can lead to a reduction in the modulus, while in others, it may cause an increase.
- Porosity: Pores reduce effective cross-section and disrupt load transfer, lowering the modulus. This is why foams, sintered parts, and poorly consolidated composites have lower E.
- Chemical Degradation/Radiation: UV, oxidation, or radiation can break chains in polymers, resulting in reduced stiffness (or increased brittleness) over time.
What Is an Example of Young's Modulus?
Young's modulus finds practical application in determining the safe working limits of cables employed in cranes, cable cars, and ski lifts. It is crucial to have a thorough understanding of how loading affects these cables to ensure safe operations. A critical design and operational consideration are necessary to prevent the applied loads from surpassing the cables' elastic limit (i.e., staying within the elastic deformation region).
To account for uncertainties and potential risks, a Factor of Safety (FoS) is incorporated. The FoS is determined through rigorous engineering judgement and design codes and can range between 1.5 and 10, depending on the specific application. By applying an appropriate FoS, the design and operational parameters are established to maintain a sufficient margin of safety, ensuring that the cables can withstand anticipated loads without experiencing permanent deformation or failure.
Considering Young's modulus in the context of cable applications helps engineers and operators make informed decisions, ensuring the safety and reliability of these systems.
What Does a High Young's Modulus Value Mean?
A higher Young's modulus implies that the material is less prone to stretching and deformation under applied forces. As the modulus increases, the material becomes stiffer, meaning that it undergoes less elastic strain when subjected to a given stress. An idealized rigid body would have an infinite Young's modulus.
What Does a Low Young's Modulus Value Mean?
A lower Young's modulus suggests that the material is more flexible and easier to deform. It exhibits greater compliance, meaning it can undergo significant strain under relatively low stress levels.
However, low stiffness does not necessarily imply high elasticity, as elasticity refers to the ability to recover shape, not just deform.
What Material Has the Highest Young's Modulus?
Diamond is widely recognized as having the highest Young's modulus, estimated to be around 1,050–1,200 GPa. However, in certain meteorites, a carbon allotrope similar to diamond, known as Lonsdaleite, has been identified. Unlike diamond's cubic structure, Lonsdaleite is composed of a hexagonal carbon matrix. While direct modulus testing of Lonsdaleite is limited due to sample size and purity, simulations and indirect evidence suggest it may exceed diamond in hardness and potentially in stiffness.
Can Young's Modulus Have Zero Value?
No. When the modulus of elasticity is zero (E = 0), the slope of the stress-strain curve becomes a straight horizontal line. This indicates that for constant stress, the strain continues to increase indefinitely. This behavior more accurately describes an ideal fluid, not a perfectly plastic material, and Young’s modulus applies only to solids, not fluids.
In perfectly plastic materials, once the yield stress is reached, deformation continues without additional stress, but the material still has a non-zero Young’s modulus in the elastic region prior to yielding.
What Are the Differences Between Shear Modulus and Young's Modulus?
Young's modulus quantifies the ratio of stress (specifically tensile or compressive stress) to strain, serving as an indicator of a solid's stiffness. On the other hand, shear modulus measures the ratio of stress to strain under shear forces. While they evaluate different types of deformation, their values can differ significantly depending on the material’s structure and bonding.
Shear modulus is also referred to as the modulus of rigidity, emphasizing its role in assessing a material's resistance to shear stress. Unlike Young's modulus, which applies to compressive or tensile loading, shear modulus specifically addresses the response to shear forces. Figure 1 below illustrates the difference between Young's modulus vs. shear modulus:
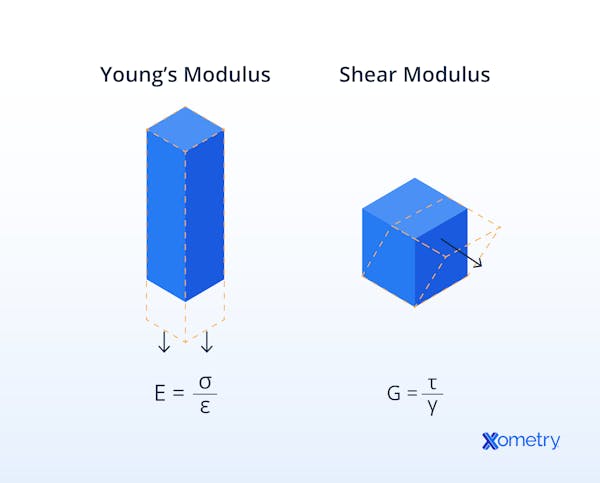
What Similarities Do Shear and Young's Modulus Have?
Shear modulus and Young's modulus are both mechanical properties that describe how materials behave under mechanical stress. Both measure the stiffness of a material, indicating its resistance to deformation. They quantify the material's ability to resist shape (shear modulus) or length (Young’s modulus) deformation under external forces. Both moduli relate to the elastic behavior of materials, which means they describe how materials respond to stress within their elastic limits.
Additionally, both shear modulus and Young's modulus are material-dependent properties. This means that different materials exhibit different stiffness characteristics, and these moduli provide a quantitative measure of that property. Lastly, shear modulus and Young's modulus share the same units of measurement, typically expressed in pascals (Pa) or gigapascals (GPa).
When To Use the Shear Modulus Equation?
The shear modulus equation finds practical use in various scenarios such as experiments and computational mechanics. For example, in experiments or tests involving shear or torsional forces, the shear stress and shear strain values can be measured using appropriate equipment. By applying these measurements to the shear modulus equation, the shear modulus of the material can be calculated. In computational mechanics, numerical methods such as finite element analysis (FEA) are utilized to simulate the behavior of materials and structures under diverse loading conditions. The shear modulus is one of the material properties required in FEA to model a material's response to shear forces accurately. In such cases, the shear modulus equation is employed to define the material's behavior within the simulation.
When To Use Young's Modulus Equation?
Young’s modulus equation has a few uses, including in tensile or compressive testing, structural analysis, and computational modeling. For example, in tensile or compressive testing, the stress and strain values can be measured using appropriate testing equipment. By utilizing these measurements in Young's modulus equation, Young's modulus of the material can be determined. Additionally, Young's modulus provides insights into how a material will deform under tensile or compressive loads and how it will perform in different structural applications. By knowing the stress and strain values, the equation can be employed to calculate Young's modulus, aiding in material selection and informing design considerations.
What Is an Elastic Modulus?
Elastic modulus is an umbrella term to describe a measure of the stiffness or rigidity of a material. Both Young’s modulus and shear modulus are examples of elastic moduli.
It generally quantifies the ability of a material to resist deformation under applied stress and recover its original shape when the stress is removed. Elastic modulus is particularly relevant in the study of solid materials, such as metals, polymers, and ceramics. Mathematically, the elastic modulus is defined as the ratio of stress to strain within the elastic limit of a material.
For more information, see our guide on What is an Elastic Modulus?
Summary
This article presented Shear Modulus vs. Young's Modulus, explained what it is, and discussed its various applications. To learn more about the differences between Shear and Young's Modulus, contact a Xometry representative.
Xometry provides a wide range of manufacturing capabilities and other value-added services for all of your prototyping and production needs. Visit our website to learn more or to request a free, no-obligation quote.
Disclaimer
The content appearing on this webpage is for informational purposes only. Xometry makes no representation or warranty of any kind, be it expressed or implied, as to the accuracy, completeness, or validity of the information. Any performance parameters, geometric tolerances, specific design features, quality and types of materials, or processes should not be inferred to represent what will be delivered by third-party suppliers or manufacturers through Xometry’s network. Buyers seeking quotes for parts are responsible for defining the specific requirements for those parts. Please refer to our terms and conditions for more information
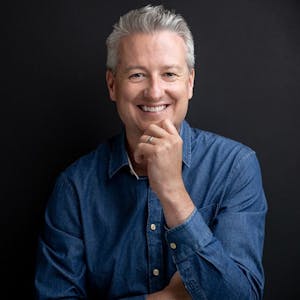