Silicone and latex are both rubbery thermosetting materials referred to as elastomers. Latex is a carbon-based compound that can either be obtained as a natural product extracted from rubber trees or a synthetic product derived from petroleum. Silicone, in contrast, is an inorganic polymer built on a silicon-oxygen backbone.
Latex can be processed using rubber injection molding, extrusion, calendering, and compression molding. It is valued for its excellent flexibility and abrasion resistance. Latex is used to make a range of products, such as gloves, abrasion-resistant liners, and adhesives.
Silicone is typically processed using open mold casting, compression molding, and blow molding. It has superior thermal and UV (ultraviolet) resistance, and an advantage over latex in biocompatibility. Silicone is used to fabricate products such as: seals, gaskets, gloves, and adhesives. This article will compare silicone vs latex in terms of properties, applications, and costs.
What is Silicone?
Silicone is a polymer made up of repeating molecular units that form long polymer chains. The monomers (the repeated chemical units) that make up the chains are alternating atoms of silicon and oxygen. They form a chain with bonding sites available for hydrocarbons or other chemical groups to branch from to make the complete silicone polymer molecule.
Silicone is a thermosetting inorganic polymer that is typically mixed in liquid form, with a base polymer and a catalyst. Upon mixing, it begins to cure in an exothermic chemical reaction.
Silicone is broken down into three subcategories: LSR (liquid silicone rubber), HCR (heat-cured rubber), and RTV (room temperature vulcanizing). RTV silicone is further broken down into RTV-1, which begins curing when exposed to air, and RTV-2, which is a mixture of a pre-polymer and a catalyst that cures at room temperature.
The different classes of silicones may be processed by different methods. RTV-1 is usually dispensed from a tube for immediate use and curing in the air. RTV-2’s two liquid components are mixed just before using them. Generally, silicone is processed via open mold casting, compression molding, or injection molding.
Silicones are available with a range of physical and mechanical properties. They run the gamut from the hardness of Shore A 10 to Shore A 90. Silicone has an excellent high temperature, UV (ultraviolet), and ozone resistance, but has poor cut and tear resistance, poor tensile strength, and poor abrasion resistance. Learn more in our guide on Silicone Plastic.
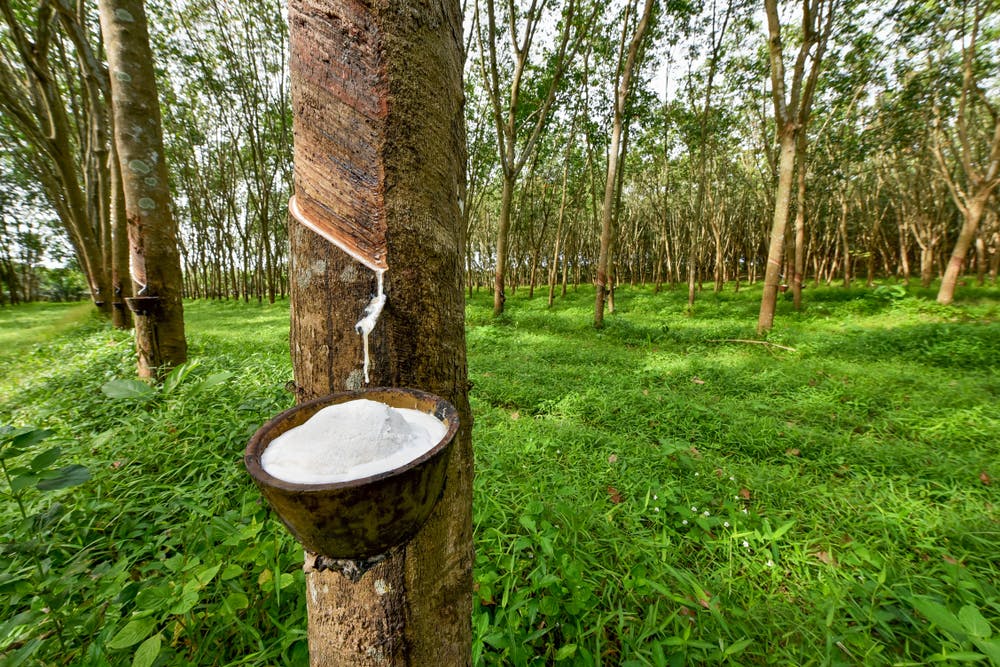
Hevea brasiliensis.
Image Credit: Shutterstock.com/Yatra4289
When the bark of this tree is cut, it exudes the milky, white fluid which is the raw material for natural latex rubber. This fluid is then converted into a rubber material using one of two methods, either the Dunlop™ or the Talalay method. Either process results in a material with excellent elongation, tear resistance, and moisture resistance. Natural latex can cause an allergic reaction for some people that can be rather severe.
Synthetic latex sometimes referred to as an emulsion polymer or engineered latex, is based on SBR (styrene butadiene) polymer chains and is manufactured from petroleum products. Synthetic latex does not cause an allergic reaction. Typical processing technologies for natural and synthetic latex include rubber injection molding, calendering, extrusion, immersion dipping, and compression molding.
Silicone vs. Latex: Applications and Uses
Silicone is available in three classifications with varying degrees of mechanical strength, thermal resistance, and biocompatibility. Some typical applications are listed below:
- High-temperature cookware such as utensils and bowls
- Molds
- Industrial sealing and bonding
- Catheters, hoses, implants
- Seals, gaskets, and caulk
Both natural and synthetic latex have a wide range of uses due to their flexibility, toughness, and wear resistance. Some typical applications are listed below:
- Gloves, swim caps, balloons, boots
- Catheters
- Rubber bands
- Cosmetics
- Open-cell foam mattresses
- Adhesives
Silicone vs. Latex: Physical Properties
Table 1 list some key physical and mechanical properties of latex and silicone:
Properties | Silicone (RTV-2) | Latex (Linatex ®) |
---|---|---|
Properties Hardness (Shore A) | Silicone (RTV-2) 27-35 A | Latex (Linatex ®) 38 A |
Properties Tensile Strength (MPa) | Silicone (RTV-2) 5.5 | Latex (Linatex ®) 25 |
Properties Flexibility (Elongation (%)) | Silicone (RTV-2) 450 | Latex (Linatex ®) 830 |
Properties Chemical Resistance | Silicone (RTV-2) Resistant to high-temperature water, salt water, brake fluid, chlorinated hydrocarbons | Latex (Linatex ®) Resistant to some household chemicals, solvents, such as acetone, and some weak acids; however, exhibits poor resistance to automotive chemicals like grease or fuel and strong acids like sulfuric acid |
Properties Maximum Operating Temperature (°C) | Silicone (RTV-2) 250 | Latex (Linatex ®) 70 |
Properties Heat Resistance | Silicone (RTV-2) Excellent thermal resistance | Latex (Linatex ®) Poor comparative heat resistance |
Data for castable silicone and natural latex was used for this comparison. Silicone has much higher thermal resistance than latex, while latex is generally considered to have better abrasion resistance.
Silicone vs. Latex: Recyclability and Sustainability
Natural latex can be considered a sustainable material since it is produced from trees, a renewable resource. Synthetic latex on the other hand is produced from petroleum and thus is not deemed sustainable. Neither natural nor synthetic latex can be recycled. However, natural latex is biodegradable. It is consumed by bacteria, albeit at a slow rate, requiring between six months and four years for a complete breakdown. It must, however, be noted that some natural latex products are treated with chemicals to prevent unwanted bacterial growth during normal use. These chemicals are not biodegradable making synthetic latex non-biodegradable.
Silicone is a thermosetting polymer. As such, it cannot be recycled like some thermoplastics, as it decomposes into harmful chemicals if heated past its maximum operating temperature. Silicone is also not produced from sustainable and renewable resources as it requires petroleum products during production.
Silicone vs. Latex: Cost
Silicone is an advanced engineering material, and as such, is generally costly. The cost of the material depends on the grade used and can vary wildly. For example, RTV-1 silicone can be purchased at any hardware store for approximately $135.00 per kg whereas RTV-2 silicone can cost approximately $4.790 to $8.80 per kilogram. Natural latex is typically more expensive than synthetic latex. Natural latex costs $1.48 per kilogram.
Alternative Materials to Silicone and Latex
Silicone and latex are elastomers. This means that suitable alternatives include (TPE) thermoplastic elastomers, (TPR) thermoplastic rubber, and (TPU) thermoplastic polyurethane. These materials can be processed using standard thermoforming techniques, such as injection molding, rotomolding, and blow molding. It must be noted that there is no natural alternative to natural latex.
Summary
This article presented silicone and latex, explained what they are, and discussed how to use each material for your manufacturing needs. To learn more about silicone and latex, contact a Xometry representative.
Xometry provides a wide range of manufacturing capabilities and other value-added services for all of your prototyping and production needs. Visit our website to learn more or to request a free, no-obligation quote.
Copyright and Trademark Notices
- Dunlop is a trademark of DNA Limited Private Company.
- Linatex is a trademark of linatex limited.
Disclaimer
The content appearing on this webpage is for informational purposes only. Xometry makes no representation or warranty of any kind, be it expressed or implied, as to the accuracy, completeness, or validity of the information. Any performance parameters, geometric tolerances, specific design features, quality and types of materials, or processes should not be inferred to represent what will be delivered by third-party suppliers or manufacturers through Xometry’s network. Buyers seeking quotes for parts are responsible for defining the specific requirements for those parts. Please refer to our terms and conditions for more information.
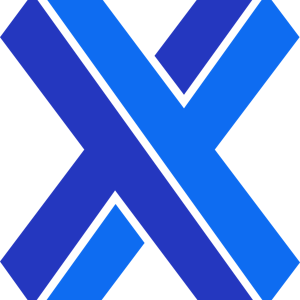