Since its invention in the 1930s, silicone rubber has been developed into hundreds of material grades and forms to fit applications not even dreamt of when it was first synthesized. Because of silicone’s superior temperature resistance, flexibility, and chemically inert nature, growth in silicone products shows no sign of abating. Silicones have exploded into almost every industrial, consumer, and medical-use market segment.
In this article, we will review the four main types of silicone rubber. We will also describe the other important silicone rubber types and their uses.
1. Room Temperature Vulcanized
Silicones that do not require heat to cure to their final form are called “room-temperature vulcanizing” (RTV) silicones. There are two kinds of RTV: one-component formulations (RTV-1), and two-component formulations (RTV-2).
RTV-1 is supplied ready to use. Once applied, a stabilizing agent in the silicone quickly begins to react with moisture in the air, curing the outside. Several different types of cross-linking agents are used. Some give off small amounts of acetic acid, amines, or alcohols while setting, while others are odorless. RTV-1 silicones are valued for their ease of use, good adhesion, and stability at high temperatures. Typical applications include use as sealants, bonding glues, and coatings. The image below shows RTV-1 used as a sealant:
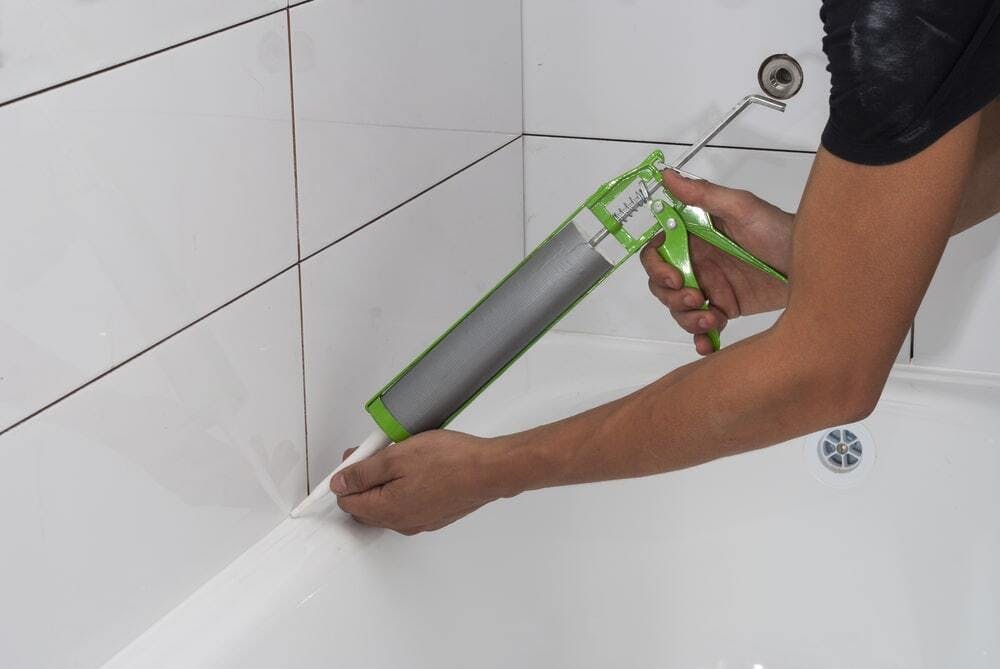
RTV-1 being used as sealant in a bathtub.
Image Credit: Shutterstock.com/Kuchina
RTV-2 comes in two parts that have to be mixed just before they are used. It cures faster than RTV-1 once mixed. RTV-2 comes in a broader range of products, with outstanding mechanical properties across a wide range of temperatures. Condensation-cured RTV-2 is less expensive than RTV-2 cured with a platinum catalyst. Platinum-cured silicone creates no byproducts, which is important for some applications. Some of RTV-2’s myriad applications include 3D printing, coatings, and molds.
2. Liquid Silicone
“Liquid silicone” refers mostly to the starting state of the incoming stock used to create silicone products. Earlier silicone grades were supplied in a semi-solid, gummy form that had to be compression molded. Liquid silicone rubber (LSR) is a two-part, platinum-cured raw material with good fluidity. This allows for capturing precise details in injection-molded components or conforming to any surface shape as a coating. The platinum-curing cross-linking system of LSR does not produce any byproducts while curing, making it a good material for food and medical-grade applications.
3. Fluorosilicone
Fluorosilicone is a variation of the polysiloxane (silicone) molecule. It has the same basic silicon-oxygen chain. Some of the methyl (CH3) groups found on the conventional silicone molecule, however, are replaced by trifluoropropyl groups. This change provides fluorosilicone with better resistance to several troublesome service environments including: fuel and oil, mineral spirits, toluene, and other organic solvents. Fluorosilicone achieves these gains in chemical resistance while maintaining nearly the same mechanical properties as conventional silicone. Fluorosilicone does not perform as well in hot air as silicone, and it is considerably more expensive. It is most suited to aerospace and automotive applications, where fuel and other chemical exposure is more likely to be a problem.
4.High-Consistency Rubber
High-consistency silicone rubber is also called “solid silicone” or “gum stock.” It is made up of high molecular weight polysiloxane chains. HCR can contain a variety of fillers to enhance special properties, such as hardness and heat resistance. HCR can be cured using either peroxide curing systems or platinum catalyst formulations. The latter creates no chemical byproducts during curing. The material is sold in bulk forms such as: bars, tubes, and cylinders for further processing. HCR is an outstanding material for long-term implantable medical devices, automotive engine components, and many consumer household products.
Forms of Silicone
Silicone can take many forms:
- Emulsion: Silicone emulsions consist of silicone molecules suspended in a stabilized water solution. Applications include: lubricants, release agents, and cleaning and polishing compounds to enhance spread and durability.
- Oil: Silicone oils are simple, linear polysiloxane chains that can slip past each other, providing a lubricating action. They may be used as hydraulic fluids and lubricating oils, and as raw materials for further processing.
- Liquid: Liquid silicone rubber is fluid enough to be used for precision injection molding. It is usually a two-part formulation that is mixed just before entering the mold. Applications for liquid silicone rubber include: gaskets, potting for electronics, formed parts, and medical devices.
- Caulk: Caulk is a viscous, room-temperature vulcanizing form of silicone. It has superior workability, adhesion, and durability.
- Resin: Silicone resins are usually thermosetting products with branching molecules that form densely cross-linked structures. They are used in adhesives, protective and water-repellent coatings, and heat-resistant paints.
- Grease: Silicone grease is made by adding fillers to silicone oil. The resulting thermally stable product lubricates the desired surfaces. It also conducts heat and protects against moisture and other chemicals. Mold release, glass joint seals, and electrical contact protection are some of the applications for silicone grease.
- Gel: Silicone gel is made from a two-part, platinum-catalyzed liquid formulation. It may contain additional oils or softeners to reach the right consistency for forming into thin sheets or packets. This form of silicone has been used in the medical field for scar reduction.
- Foam: Silicone foam is created by adding outgassing agents to liquid silicone. These agents are controlled to allow the manufacture of both open and closed-cell foams of varying densities. The foam may have a smooth skin – as for use in gaskets and spacers, or a rough surface, as may be acceptable in gap-fillers, pipe insulation, and other applications.
- Solid: Solid silicone rubber usually refers to a type of silicone that has long polymer chains and high molecular weight. It is also called “high-consistency rubber” (HCR). When cured, it is relatively dense and hard. It can be formed into final products such as tubing, engine mounts, seals, and gaskets.
For more information, see our guide on the properties of silicone.
Classification of Silicone
All forms of silicone can be classified as non-organic elastomeric polymers. As a group, they are flexible, non-chemically reactive, resist degradation by ultraviolet radiation, maintain their mechanical properties over a wide range of temperatures, and are considered non-toxic when used appropriately.
Silicones can be adapted into many different forms, and for thousands of end uses. They can be liquids, pastes, gels, foams, or solids. Silicones can be chemically tailored for extra strength, thermal stability, electrical conductivity, or chemical resistance.
Liquid Rubber vs Silicone
A liquid rubber sealant can be silicone-based, but it may also be based on other suitable materials, such as polyurethane. “Liquid Rubber” usually refers to thin sealants that can be applied to large areas such as driveways, roofs, and underground cement walls. The term “Liquid Silicone Rubber” (LSR) always means silicone. LSR is the raw material used for injection molding, joining/bonding surfaces, and sealing applications.
Summary
This article reviewed four of the most common types of silicone and how these differ from each other.
Contact a Xometry representative for help in deciding on the right composition and manufacturing techniques to produce high-quality silicone components or check our quoting tool.
Xometry provides a wide range of manufacturing capabilities and value-added services for all of your prototyping and production needs. Visit our website to learn more or to request a free, no-obligation quote.
Disclaimer
The content appearing on this webpage is for informational purposes only. Xometry makes no representation or warranty of any kind, be it expressed or implied, as to the accuracy, completeness, or validity of the information. Any performance parameters, geometric tolerances, specific design features, quality and types of materials, or processes should not be inferred to represent what will be delivered by third-party suppliers or manufacturers through Xometry’s network. Buyers seeking quotes for parts are responsible for defining the specific requirements for those parts. Please refer to our terms and conditions for more information.
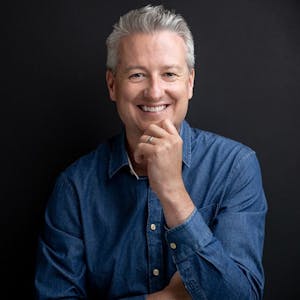