Ultimate Tensile Strength (UTS): Definition, How It Works, Calculation, and Example
Learn more about this measurement and how it is calculated by dividing the force required to break a material by its original cross-sectional area.
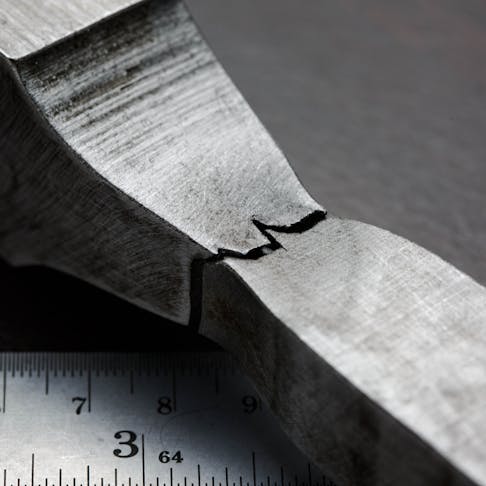
Ultimate tensile strength is a measure of the maximum stress a material can withstand before fracturing. The tensile strength of a material is measured using a tensile testing machine which applies a pulling load to a test specimen until it breaks. The rate of elongation and load of the force applied can be used to calculate the material properties. The ultimate tensile strength of a material can be found by dividing the force required to break a material by its original cross-sectional area. This article will define ultimate tensile strength, how it works, and its calculations, and it will give some examples.
What Is Ultimate Tensile Strength?
The ultimate tensile strength is the point at which a material fails. Strength is a measure of a material's ability to resist an applied load. However, the material will first deform elastically and then plastically before finally breaking into two or more pieces. The ultimate tensile strength is the maximum stress the material withstands before it breaks.
What Is the Other Term for Ultimate Tensile Strength?
The ultimate tensile strength is also known as the tensile strength. Sometimes ultimate tensile strength can be written as the acronym “UTS” or “TS.” All terms are used to describe the same property, which is the ultimate tensile stress experienced before the material completely fails.
How Does Ultimate Tensile Strength Work?
To calculate the ultimate tensile strength of a material, the cross-sectional area and force applied must be known. Both the stress experienced and the ultimate tensile strength of a material are calculated using the formula:
Stress (or) Strength = Force / Area
The only difference is strength is the maximum stress a material can withstand before fracturing, whereas stress is simply the ratio of the force to the cross-sectional area at any load level.
What Is the Significance of Ultimate Tensile Stress in Materials?
The tensile strength of a material is significant as it indicates a material's ability to withstand its maximum stress before fracturing. In applications such as suspension bridges and safety harnesses, the materials used must be able to withstand significant loads without failing. By determining the ultimate tensile stress of a material, appropriate materials can be chosen for a given design.
What Is the Formula for Calculating the Ultimate Tensile Strength?
The ultimate tensile strength formula is:
Strength = Force / Area
The force represents the load required to break the material, and the area is the cross-sectional area of the test sample before deformation. The ultimate tensile stress formula is the same as the tensile strength formula. However, stress is the amount of force experienced per area, and strength is the force experienced to break the sample per area.
How To Calculate Ultimate Tensile Strength?
A tensile test is performed to calculate the ultimate tensile strength. First, a test specimen is prepared into a “dumbbell” (also known as a “dogbone”) shape to ensure the part breaks in the middle. The specimen’s cross-section is then measured and recorded. After that, the part is loaded into the tensile test machine. The machine will apply a load until the test piece fails. Most modern tensile testers can record the force applied and use the cross-section to display the tensile strength automatically once the test is complete. If not, the force and cross-sectional area can be put in the formula:
Strength = Force / Area
What Is the Unit for Ultimate Tensile Strength?
The unit for tensile strength is in force per unit area, which is pounds per square inch (PSI) in the imperial system. In the metric system, newtons per square meter (N/m2) are used. However, newtons per square meter are substituted for Pascals (Pa); both have the same meaning, only differing in the name. The strength of some materials (especially polymers and metals) is relatively high, so megaPascals (MPa) are more commonly used for these materials.
What Are Examples of the Ultimate Tensile Stress of Different Metals?
A range of metals that are commonly tensile tested are listed below:
1. Steel
Steel is a mix of primarily iron and carbon (in varying amounts, typically below 2%), which adds strength and hardness to the basic iron metal. Steels have a tensile strength in the range of 200–2000 MPa, depending on composition and treatment. Steel is one of the most commonly used metals in the world and has mainly structural applications in civil engineering construction and structural parts of vehicles. To learn more, see our full guide on Steel.
2. Aluminum
Aluminum is also one of the most common metals due to its high strength-to-weight ratio and cheap cost. These properties lead to aluminum being used in many aeronautical and aerospace applications. Aluminum can achieve a strength of around 90–400 MPa, depending on the alloy.
3. Brass
Brass is a mixture of copper and zinc. Brass is very conductive; it is also malleable, which allows it to be easily shaped into complex profiles. These properties make brass suitable for use in plumbing and electrical applications. Brass has a tensile strength of around 200–550 MPa.
4. Titanium
Titanium is a naturally found silver metal. It has the highest strength-to-weight ratio of any metal, but it is very hard to process, which makes it expensive. Titanium is also biocompatible. This leads to the use of titanium in medical and aeronautical applications. Titanium has a tensile strength of 275–1100 MPa, depending on the grade.
What Are the Factors That May Affect the Ultimate Tensile Stress of a Material?
One of the major factors affecting the tensile strength of a material is the temperature of the material during testing. However, there are several more factors that affect the tensile strength:
- Microstructure
- Composition of material
- Testing conditions (including measurement accuracy and strain rate)
Does the Size and Shape of a Material Specimen Affect Ultimate Tensile Stress?
No, the size and shape of the test specimen do not significantly affect the ultimate tensile stress of the material if standardized test methods are followed. The size of the sample does not matter, as the cross-section used in the calculations of tensile strength accounts for differences in size. The use of the cross-section in the calculations of tensile strength negates any effect the shape of the test sample has on the outcome of the test.
How Does Ultimate Tensile Stress Differ From Tensile Strength?
The tensile stress is the force per unit area experienced by a material at any given time. The strength is the limit at which the force per unit area reaches the maximum, and the material fails. Both the tensile stress and strength are calculated using the formula force divided by area. However, tensile strength is specifically the limit of the force per unit area before the material fails.
How Does the Stress-Strain Curve Relate to Ultimate Tensile Strength?
The stress-strain curve is a plot of the force applied against the deformation experienced by a material during a tensile test. The point at which the curve decreases in stress is used to identify the ultimate tensile strength from the stress-strain curve, as shown in Figure 1 below: Ultimate tensile strength stress-strain curve.
The decrease in stress is due to the “necking” of the material. Necking occurs when the force applied in a tensile test is still applied but the material experiences a decrease in cross-sectional area.
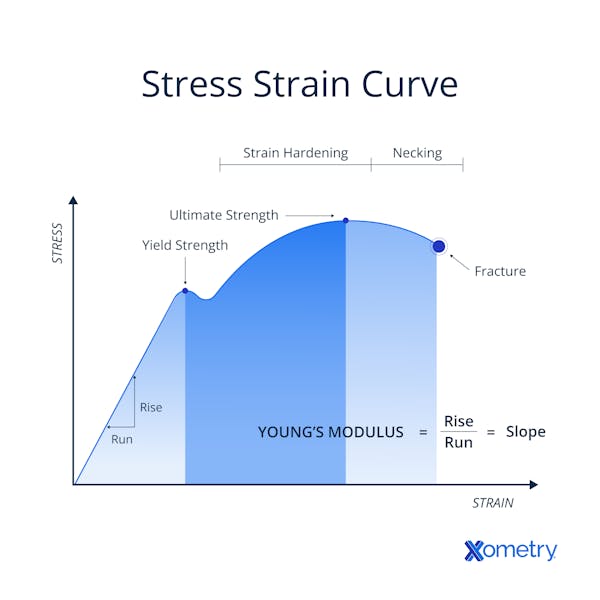
How Does Ultimate Tensile Stress Relate to 3D Printing?
The ultimate tensile stress of a material is a bigger consideration in 3D printing when compared to most other manufacturing methods, as the ultimate tensile stress varies more. This large variation is a result of 3D printers printing in layers, which makes the material anisotropic when using certain 3D printing processes. Other considerations that affect the ultimate tensile stress are the infill percentage and the wall thickness of a 3D-printed part.
How May the Ultimate Tensile Strength of 3D Printed Items Be Optimized for Particular Uses?
The main factor in optimizing the ultimate tensile stress of 3D-printed materials is the z-direction. The z-direction refers to the direction perpendicular to the layers being printed. The ultimate tensile strength of a material is weakest in the z-direction, so loads in this direction should be avoided. Other considerations when optimizing for tensile stress are the material choice, use of fiber reinforcement, infill percentage, and wall thickness. Orienting the part to be printed so that the real-life loads are running parallel to the printing z-axis will increase the strength of the part.
What Part Does Material Choice Play in a 3D Printed Object’s Ultimate Tensile Strength?
The material choice will greatly affect the tensile strength of the final part. Most parts are currently still printed in polymers. PLA is one of the most commonly 3D-printed materials as it is cheap and offers some strength. However, it is not suitable for most load-bearing applications. Therefore, polycarbonate, ULTEM 9085, or PEEK can be used instead, as they are much stronger materials.
Is a 3D Printed Object Stronger if the Ultimate Tensile Strength Value Is Higher?
Yes, when comparing two 3D printed parts of the same print orientation and structure, a higher ultimate tensile stress will result in a stronger part. When comparing a 3D-printed part and a conventionally manufactured part of the same material, the strength of the 3D-printed part is less than its non-printed equivalent.
Does the Printing Speed Impact the Ultimate Tensile Strength of a 3D Printed Part?
Yes, as the print speed of a 3D print increases, the strength of a part may decrease. The reason for this potential reduction in strength is that the print head does not have sufficient time to fully plasticize the polymer. This can create imperfections and result in poor adhesion between print layers.
Can a 3D Printed Parts Ultimate Tensile Strength Be Predicted Before It Is Printed?
Yes, the ultimate tensile stress of a 3D-printed part can be predicted before printing, although the results will vary depending on the 3D printing process and the prediction method. Finite Element Analysis (FEA) software can be used to calculate the stress of a part, as well as lots of other properties. FEA is better suited to predicting the strength of 3D printing processes resulting in fully dense, isotropic parts (such as metals printed with powder bed fusion processes). FEA results for FDM/FFF printed plastics can be less accurate.
However, 3D-printed parts will still require actual testing, and quality control is a big issue with them as printers are not as effective at repeatability as other manufacturing methods.
Summary
This article presented ultimate tensile strength, explained what it is, and discussed how to calculate it. To learn more about ultimate tensile strength, contact a Xometry representative.
Xometry provides a wide range of manufacturing capabilities, including casting and other value-added services for all of your prototyping and production needs. Visit our website to learn more or to request a free, no-obligation quote.
Disclaimer
The content appearing on this webpage is for informational purposes only. Xometry makes no representation or warranty of any kind, be it expressed or implied, as to the accuracy, completeness, or validity of the information. Any performance parameters, geometric tolerances, specific design features, quality and types of materials, or processes should not be inferred to represent what will be delivered by third-party suppliers or manufacturers through Xometry’s network. Buyers seeking quotes for parts are responsible for defining the specific requirements for those parts. Please refer to our terms and conditions for more information.
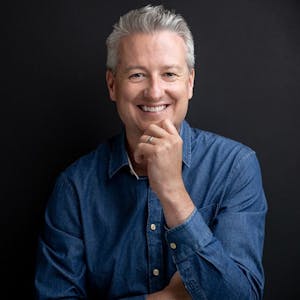