The yield point is the point on a material’s stress-strain graph at which it stops deforming elastically and starts deforming plastically. During elastic deformation, the material will return to its original dimensions, but plastic deformation changes its shape permanently.
In many cases, the yield point on a stress-vs-strain curve can be identified as the point where linear deformation stops and the curve dips down again before rising to the ultimate tensile strength point. Some yield points are not obvious to the eye on a stress-strain graph. Therefore, the point is chosen using an industry convention. First, a 0.2% offset is added to all strain values on the linear part of the graph. That shifts the line slightly to the right. The spot where the new line and old curve intersect is the yield point. The temperature and strain rate of the material can affect the yield point in opposing ways. Strain hardening can also influence the yield point of metals. This article will discuss yield point, its key characteristics, applications, and the factors that affect it.
What to Know About Yield Point
The yield point is a material property that describes the moment when a material stops deforming elastically and instead begins to permanently deform. Elastic behavior will see the material return to its original dimensions after a load is removed. The yield point of a material is usually determined using a tensile testing machine.
How the Yield Point Differs from the Elastic Limit in Materials
The yield point and the elastic limit are different characteristics but occupy very similar points on a stress-strain graph. Prior to its elastic limit, a material will not permanently deform. The yield point of a material is offset from that point by 0.2% in the strain (positive x) direction, meaning that usually, a material will have experienced a small amount of plastic deformation before reaching the yield point.
The Key Characteristics of the Yield Point in a Stress-Strain Curve
The stress-strain curve is a graphical representation of the amount of force applied per unit area against the extension of the material during a tensile test. The stress on the y-axis represents the force per cross-sectional area. The strain equates to the change in length divided by the original length. Most of the curve before the yield point is linear; this is the elastic region of deformation. After the yield point, the line will usually dip slightly and then continue upwards. From this point onwards, the material is plastically (permanently) deforming. For more information, see our guide on What is a Stress-Strain Curve?
Figure 1 below is an example of a stress-strain curve:
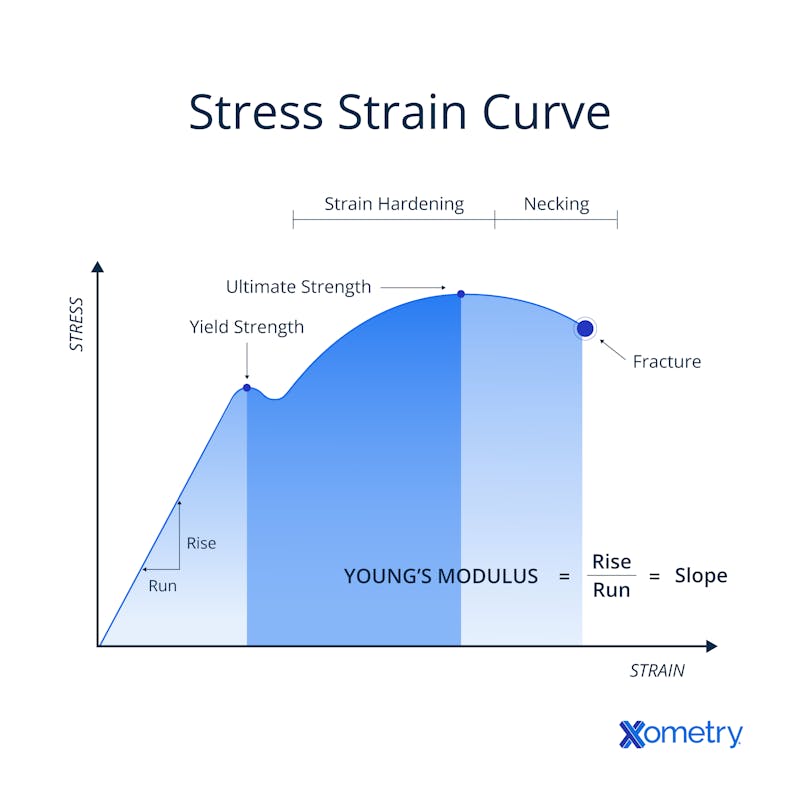
Factors Influencing Yield Points in Materials
The yield point for a given material is not always the same in all cases. It can be influenced by three main factors:
- Strain Hardening: The strain-hardening process loads the raw material beyond its yield point so that it plastically deforms. After the load is removed, the elastic strain will recover, but the material will remain slightly deformed. The yield point will henceforth occur at the maximum stress previously applied, increasing the total stress the material can take without further plastic deformation. This technique is limited to use with metals and must be performed prior to the material’s installation or machining into the end product.
- Strain Rate: As the strain rate from a load increases, so does the yield point. This is because faster strain rates impart more elastic deformation.
- Temperature: The higher the temperature of the material, the more energy it has. More energy means its atoms have an easier time breaking the bonds with their neighbors and beginning to flow. On the macroscopic level, this translates into the material becoming softer, so it’s easier to reach the plastic deformation stage.
When a Material Surpasses the Yield Point
When a material surpasses its yield point, it will permanently deform. The region after the yield point is referred to as the plastic region or region of plastic deformation. Shortly after that, the material will reach its peak stress and, if the stress is tensile, begin to neck. The point of peak stress is the ultimate strength and necking is the reduction in cross-sectional area at some point along the material. After this point, more applied force will only cause it to neck further until it fractures completely.
The value of the yield point determines when a material behaves elastically and when it behaves plastically. We call those that fail shortly after their yield point brittle materials, whereas materials that fail long after their yield point are ductile materials. A material's resilience is its ability to deform elastically and, therefore, absorb energy without permanent damage. Materials with a low yield point are not considered resilient while materials such as rubber have a high resilience.
Yield Points Observed in Different Materials
Every material type has its own yield point, and they vary as widely as any other mechanical property. Below are a few example materials and their yield strengths:
- A36 steel - 350 MPa
- Titanium 11 - 940 MPa
- Nylon - 45 MPa
- Diamond - 1600 MPa
- Polypropylene - 12-43 MPa
Practical Applications of Yield Points in Manufacturing
A material's yield point is critical for deciding the part's allowable mechanical load. The yield point can be used to:
- Choose an upper load limit so as to prevent failure.
- Determine a material's resilience.
- Predict the behavior of a material under load.
The Significance of the Yield Point in Structural Design
It is important to know the yield point of a material when designing a structure. Every material will behave differently after the yield point than it does before the yield point. The most notable difference is the permanent deformation of the material. If the yield point of a structure is exceeded, it will no longer have the same dimensions, even when the stress is released. Additionally, a brittle material (one that shows little deformation after the yield point) will fail with little or no warning after its yield point has been reached. Therefore, engineers typically prefer materials that can experience a large amount of strain after the yield point.
How the Yield Point Can Change Over Time
A material’s yield point can change, but not purely due to the passage of time. Other factors and influences on the material that parts may encounter during their useful lifetimes can alter the yield point. For example, as time passes, the temperature of the material can increase, which will decrease the yield point. Strain hardening can also occur, where a material exceeds its yield point by small amounts, creating a new higher yield point.
How Xometry Can Help
Xometry provides a wide range of manufacturing capabilities and other value-added services for all of your prototyping and production needs. Visit our website to learn more or to request a free, no-obligation quote.
Disclaimer
The content appearing on this webpage is for informational purposes only. Xometry makes no representation or warranty of any kind, be it expressed or implied, as to the accuracy, completeness, or validity of the information. Any performance parameters, geometric tolerances, specific design features, quality and types of materials, or processes should not be inferred to represent what will be delivered by third-party suppliers or manufacturers through Xometry’s network. Buyers seeking quotes for parts are responsible for defining the specific requirements for those parts. Please refer to our terms and conditions for more information
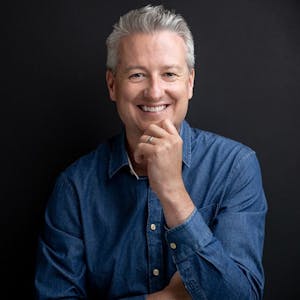