MJF, which is an abbreviation for multi-jet fusion, is a much-beloved type of 3D printing that comes packed with some pretty impressive benefits, like the fact its parts can be up to 98% isotropic, the powder is reusable (up to 80% of unused material), it’s fast, and its parts are very detailed. MJF printers also come with removable build volumes, allowing you to remove a completed part and cool it while you install another part and carry on with the printing process, making it excellent for high-volume production. Another bonus is that no support structures are required during printing. So, with all these benefits in mind, what exactly is MJF, and how does it work? Let’s see.
What is Multi Jet Fusion 3D Printing?
Multi-jet fusion creates 3D-printed parts using nylon, polypropylene, or TPU (thermoplastic polyurethane), all in powdered form. It was developed by HP Additive and commercially released in 2016. Compared to other more established methods of 3D printing, MJF is a relatively new kid on the block but has gained popularity because of how good it is.
It works by applying a fusing and detailing agent to a thin layer of powder that’s been placed in the shape of the part’s cross-section at a pre-set height. The fusing agent is good for absorbing heat and the detailing agent helps the edges be crisper and sharper, as well as prevents the molten plastic from bleeding past the edges of the part. An infrared heat source then bonds the powder into the final part by sintering the particles together wherever the fusing agent is applied, which is followed by the print bed moving down by the thickness of one layer (usually around 80 microns), and the process repeats itself. The following image shows a part made using this process:
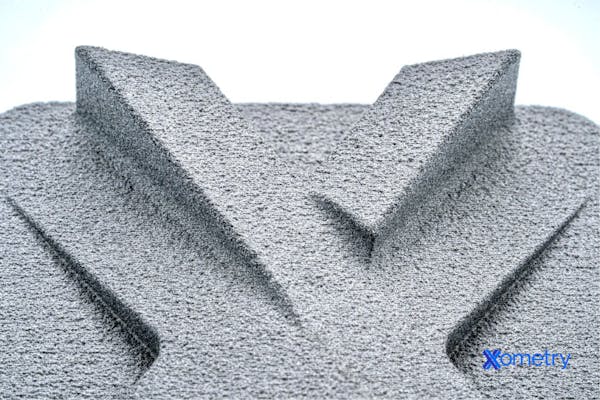
How Does MJF 3D Printing Work?
MJF 3D printing works by applying a thin layer of the material onto the print bed using a recoater. The powder is then heated to just beneath its sintering temperature. Next, a fusing agent is applied to the powder in the shape of the part cross-section. This is applied using multiple nozzles which jet the fusing and detailing agent onto the powder. The fusing agent helps absorb heat during a later process step. A detailing agent is applied to the edges of the part to help create crisper and sharper edges. The detailing agent prevents the molten plastic from bleeding past the part edges. An infrared heat source then passes over the material and sinters the plastic particles together wherever the fusing agent is applied.
Who Manufactures MJF Printers?
MJF printers are manufactured by HP (Hewlett Packard) Additive. HP is a well-known manufacturer of 2D inkjet and laser printers and copiers. This experience positioned HP to be able to leverage its hardware development knowledge in creating HP Multi Jet Fusion 3D printing technology.
How was MJF Created?
MJF 3D printers were first released in 2016. The technology leveraged existing precision inkjet technology developed by HP for use in standard 2D printers. This know-how was then combined with powder-based printing techniques. MJF printed parts are unique in their use of inkjet technology adapted to 3D printing of plastic powders, combined with shape and surface quality control provided by fusing and detailing agents.
What Materials Can MJF Print?
Lots of materials can work with MJF printing, the most common of which is probably PA12, which is a form of nylon. These types of printers can also print elastomeric parts. Here’s the full range of materials compatible with MJF:
- PA11 (nylon) is very flexible yet tough—even more so than PA12, which we’ll consider shortly. It’s a great material for end-use parts.
- PA12 (nylon) has very good resistance to cracking and has the lowest moisture absorption of all the polyamides. You can also find glass-filled variants. This material is good for making functional prototypes.
- PP (polypropylene) is perfect for prototypes that can imitate the performance of injection-molded polypropylene.
- TPU01 (thermoplastic polyurethane) is a material that has a great balance between flexibility and shock absorption. It can also make features with high resolutions.
- TPU M95A (thermoplastic polyurethane) has very good resistance to abrasion, as well as high elongation at its break strength. You can use this material to make a variety of things, like shoe insoles and seals, as well as functional prototypes.
- TPA (thermoplastic polyamide) is a lightweight, highly flexible elastomer. In low temperatures, it has impressively high elongation.
The image below shows a polypropylene part we made at Xometry using MJF:
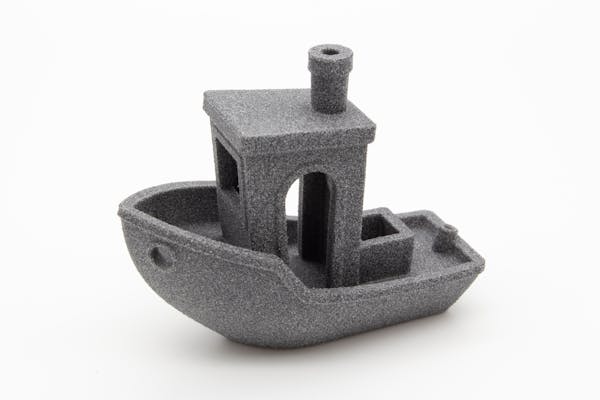
What are the Common Applications for MJF 3D Printing?
MJF printing can be used for functional prototypes as well as end-use parts. Some notable applications are listed below:
- Aircraft rudder trim systems
- Custom prosthetics
- Dental implant molds
- Robot end-arm tooling
- Drone frames
- Automotive door-support hinges
- Flexible lattice structures
Why Should You Use Multi Jet Fusion 3D Printing?
Use Multi Jet Fusion 3D printing when you need a technology that is fast and can produce highly detailed, dimensionally accurate features. Additionally, MJF is developed by HP, which has decades of experience in durable hardware development and end-user technical support.
Why is MJF Excellent for the Production of End-Use Parts?
MJF 3D printing is a high-volume additive manufacturing technology that was developed especially for the manufacture of end-use parts. MJF makes use of nylon and polypropylene powders as raw materials. Both are engineered thermoplastics used in a number of industrial applications. MJF parts also have isotropic properties which is not always the case with other printing technologies such as FDM (Fused Deposition Modeling) and SLS (Selective Laser Sintering). MJF is able to produce highly detailed small features. The use of a detailing agent also ensures a smooth, albeit matte, outer surface finish.
What are the Tiniest Details That MJF can Print?
MJF 3D printers can print parts with features as small as 0.1 mm in width. Table 1 below lists some additional minimum feature sizes possible with MJF printing:
Property | Minimum Size |
---|---|
Property Layer height | Minimum Size 80 μm |
Property Minimum slit between walls | Minimum Size 0.5 mm |
Property Minimum hole diameter (part thickness of 1mm) | Minimum Size 0.5 mm |
Property Minimum feature size | Minimum Size 0.1 mm |
Property Minimum font size for debossed or embossed text | Minimum Size 6 pt |
Table credit: HP MJF Handbook
What are the Advantages of MJF?
MJF is a highly capable 3D printing technology. Some of its key advantages are listed below:
- MJF parts are highly isotropic, with 98% isotropy achievable.
- MJF powder is reusable. Up to 80% of the unused material present in the build chamber during printing can be reused. The remaining 20% may consist of powder that has been oxidized and degraded due to the heat in the printing zone. The detailing agent evaporates during the printing process.
- MJF printers have removable build volumes. This means that the completed parts can be removed from the printer to allow for cooling while another build volume can be installed to maintain production continuity and to enable high volume production.
- No support structures are needed during printing, as the unsintered powder behaves as the part’s support structure.
Frequently Asked Questions on MJF
What is MJF's Dimensional Accuracy?
Multi-jet fusion can create parts that can potentially only veer off by ± 0.15 % from nominal dimensions with a lower limit of 0.3 mm. After that point, the dimensional accuracy is neither defined nor guaranteed by machine manufacturers.
Are MJF 3D Printed Parts Water Resistant?
They can be. It boils down to how well-designed they are. HP has tested the IP (Ingress Protection) rating of the raw materials it typically uses and has achieved IP66 and IP67 waterproof ratings with them. In case you’re not familiar with these numbers, the first digit in the IP rating means that the part is completely protected against the ingress of dust. The second number, especially if it’s a 6, means that the part resists water intrusion. If that number is a 7, it means the part won’t absorb water, even if submerged.
What is MJF's Maximum Construction Size?
The largest HP MJF printer at the moment is the Jet Fusion 5200 series. It has a usable build volume of 380 x 284 x 380 mm. MJF printers differ from other types in that they allow you to stack parts in the entire volume, which maximizes the entire available space. That’s mainly because you don’t need support structures—the powder itself supports the part. A side note: if you’re making large hollow parts, you might want to consider including permanent support inside it to increase its mechanical strength.
What are the Differences Between MJF and SLS 3D Printing?
They’re both powder bed fusion printing methods, but SLS, which stands for selective laser sintering, uses a laser to fuse the powder together, unlike the infrared energy source in MJF. It also requires support structures when printing. We have a whole guide on the difference between these two methods which you can check out.
Is Multi Jet Fusion Binder Jetting?
Multi jet fusion is not the same as binder jetting. The processes may appear similar, but multi-jet fusion uses heat to sinter powders together whereas binder jetting is room-temperature printing technology. Binder jetting produces parts with inferior mechanical properties compared to MJF.
How Xometry Can Help
If you have any other questions about MJF, SLS, or any other type of 3D printing, one of our representatives would be happy to help. Xometry also offers a plethora of other manufacturing services, including CNC machining, laser cutting, and powder coating. You can get started today by requesting a free, no-obligation quote from our website.
Disclaimer
The content appearing on this webpage is for informational purposes only. Xometry makes no representation or warranty of any kind, be it expressed or implied, as to the accuracy, completeness, or validity of the information. Any performance parameters, geometric tolerances, specific design features, quality and types of materials, or processes should not be inferred to represent what will be delivered by third-party suppliers or manufacturers through Xometry’s network. Buyers seeking quotes for parts are responsible for defining the specific requirements for those parts. Please refer to our terms and conditions for more information.
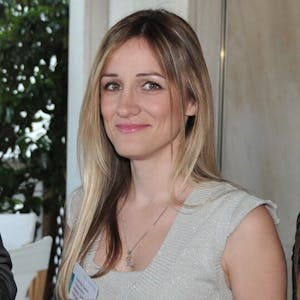