A direct extruder is a type of 3D printer extruder mechanism that directly feeds filament into the hot end assembly of an FDM® (fusion deposition modeling) or FFF (fused filament fabrication) machine, without the need for additional tubing or Bowden cables. It is commonly used in desktop FDM® direct-drive 3D printers. The direct extruder consists of: a stepper motor, a drive gear, and an idler arm mounted directly above the hot end. When the motor rotates, the drive gear grips the filament and pushes it downward into the hot end, at which it is melted and deposited onto the build platform layer by layer. Direct extruders are known for their precise filament control, which allows for better print quality, especially with flexible or soft materials. They are suitable for a wide range of filament materials, including: PLA, ABS, PETG, and TPU.
This article will discuss what a direct extruder is, including its use, how it works, and the materials suited for it.
What Is a Direct Extruder?
A direct extruder is a mechanical device that sits directly above the hot end of the printer and feeds filament to it, controlling the dispense rate and start/stop events by pushing the filament into the hot end or by withdrawing it to end the print operation.
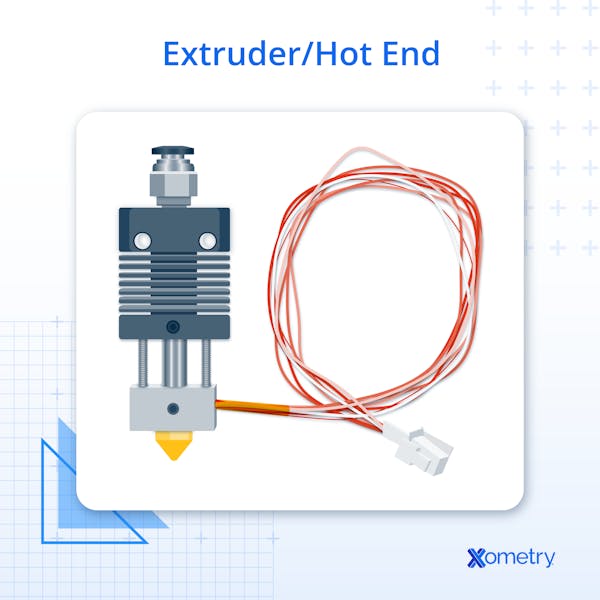
How Does a Direct Extruder Work?
A direct extruder is a filament-push motorized feed mechanism that sits directly above the hot end. The process is as follows:
- The primary function of the mechanism is to push the filament into the hot end. This results in the flow of molten build material as it is applied to the build table or previous model layers. The flow rate is precisely metered by the extruder motor. The filament is pushed into the heated zone and advances the already-molten polymer out of the nozzle as the build progresses.
- The secondary and highly critical action of the extruder is to retract the filament slightly. It severs the connection between the hot end and the built model cleanly when the hot end must be repositioned to recommence building. This aspect is critical to model quality, as the clean separation at the end of a build period must be effected without residual material forming a thread (stringing) attached to the completed section and without dribbling or smearing taking place during the subsequent move.
What Is the Use of a Direct Extruder?
Direct extruders bring benefits to the 3D printing process that are widely considered to be significant. As a result, it is common for machines to either be sold with or be converted to direct extruder setup as it offers the greatest flexibility in terms of: filament types and additives, build quality, and maintenance burdens.
What Are the Different Materials That Are Compatible With a Direct Extruder?
The different materials that are compatible with direct extruders are listed and discussed below:
1. ABS
ABS (acrylonitrile butadiene styrene) is a widely exploited filament, widely reported as optimally fed by direct extrusion in FDM® (fusion deposition modeling) and FFF (fused filament fabrication) printers. Direct extruders are simply better at handling ABS due to their precise filament control and consistent start/stop and steady extrusion.
ABS exhibits great flow properties, allowing it to be accurately deposited and well bonded in forming the desired object. ABS offers several benefits in 3D printing outcomes, including high strength, durability, and heat resilience, making it suitable for functional prototypes, moderately stressed parts, and end-use products.
These materials can be post-processed by sanding, painting, and solvent smoothing to deliver the best possible surface finish.
To learn more, see our full guide on ABS (Acrylonitrile Butadiene Styrene).
2. PLA
PLA (polylactic acid) is another extensively used filament that is compatible with direct extrusion FDM® and FFF printing. It offers the benefit of being bio-sourced and biodegradable. Direct extruders are well-suited for handling PLA due to more precise filament control and consistent start/stop and extrusion. This material also exhibits excellent flow properties when parameters are under good control, allowing it to be accurately deposited and well bonded to form the desired object.
PLA is known for its: ease of use, low warp, minimal odor during printing, and wide range of colors. It is commonly used for: prototyping, hobbyist projects, educational purposes, and consumer products due to its biodegradability and environmental friendliness. It is not among the higher-strength materials and is best used for shape/size confirmation rather than structural, functional, or field-evaluation prototyping.
To learn more, see our full guide on What is PLA Material.
3. Nylon
Nylon (polyamide) is a capable and engineering-useful filament material. It can be set up to work effectively in direct extrusion when specific considerations are made to accommodate its properties. Direct extruders with nylon filament deliver the same precise filament control through consistent start/stop and steady extrusion capabilities as with other filaments.
Nylon filament melts at higher extrusion temperatures, ranging from 230–260 °C, to achieve proper flow characteristics. This can result in difficulties in direct extrusion as there is a greater risk of heat buildup in the extruder when the cooling is insufficient or the build profile requires slow extrusion. This filament tends to absorb moisture from the environment, which can lead to printing issues as the water evaporates in the hot end and extruded material. Bubbling and poor adhesion will result if the filament is not newly dried before use.
Despite these challenges, nylon offers excellent mechanical strength, flexibility, and chemical resistance. This makes it very suitable for functional parts, engineering prototypes, and applications requiring stress resilience, wear durability, and impact tolerance.
To learn more, see our full guide on What is Nylon Filament.
4. HIPS
HIPS (high impact polystyrene) is a filament that is extensively used in direct extrusion 3D printing, again delivering precise filament start and retract control and consistent extrusion quality.
HIPS exhibits good flow properties when parameters are appropriately adjusted, allowing it to be well bonded and accurately deposited layer by layer. This material is appreciated in model building for its high impact strength, dimensional stability, and (particularly) its easy post-processing. Great cosmetic results are achieved by sanding and painting. Models can easily be solvent welded, making them suitable for a wide range of prototyping and modeling applications.
It is commonly used as a support material in more complex 3D printing applications, in which it can be dissolved using a D-limonene solution after printing. This leaves the primary material undamaged. Note that this does not apply to all primary build materials, so care is required.
To learn more, see our full guide on HIPS.
5. TPU
TPU (thermoplastic polyurethane) is a flexible and elastomeric filament that benefits from direct extrusion 3D printing. Remote extruders can struggle with material compression in the supply line, particularly with softer grades of this polymer.
TPU exhibits excellent elasticity and flexibility. However, in the liquid state, it can be accurately deposited and well bonded to form flexible parts like: gaskets, seals, clothing/branding components, and wearable technology. It is known for its durability, abrasion resistance, and ability to withstand bending, stretching, and washing without deforming. It is commonly used in applications requiring soft-touch surfaces, shock/vibration absorption, and impact resistance.
Effective printer setup, including filament path alignment and extruder tension adjustment, is important for successful results in a direct extruder setup.
6. PETG
PETG (polyethylene terephthalate glycol) is a particularly durable and very versatile filament that is widely utilized in direct extrusion FDM®/FFF printing. Direct extruders are suitable for handling PETG filament, although it is considered robust in indirect extruders. This is because the filament is quite rigid and accommodating of slight irregularity in feed.
It offers near-ideal flow properties, accurate deposition, and good bonding to form high-quality printed outcomes. It is appreciated for its high impact resistance, transparency, and chemical resistance. It also offers low shrinkage, minimal warping, and considerably easier printing compared to other common materials such as ABS.
PETG is commonly used whenever robust and visually appealing parts are required as stressed mechanical components and functional parts. Thoughtful printer setup, including bed-adhesion methods and temperature settings, is critical for successful 3D printing with PETG.
7. ASA
ASA (acrylonitrile styrene acrylate) is a durable thermoplastic filament that has chemical, thermal, and mechanical similarities with ABS. Additionally, it delivers improved weather resistance and UV stability, by comparison. This makes it more suitable for outdoor applications.
ASA exhibits beneficial flow properties such as low molten viscosity, allowing it to be accurately deposited and easily inter- and intra-layer bonded to form robust prints. ASA is appreciated for its good cosmetic capability and excellent mechanical properties, including: high impact resistance and dimensional stability, good chemical resistance, and thermal stability. This makes it suitable for an unusually wide range of applications, including: automotive parts, signage, and outdoor fixtures/fittings.
Good printer setup, including heated-bed temperature and enclosure for temperature stability (Note: FDM® is more effective than FFF with ASA), are important for successful 3D printing with ASA.
8. Specialty Filaments
Specialty filaments is a catch-all term that refers to a wide range of advanced materials and composites used in 3D printing. Each has characteristic properties, applications, and challenges. Direct extruders can handle virtually all specialty filaments effectively. These specialty filaments are:
- Flexible Filaments (e.g., TPU, TPE): These filaments are known for their elasticity and flexibility for printing soft-touch items like: phone cases, shoe insoles, and flexible seals/gaskets. Direct extruders can handle varying degrees of flexibility better than remote feeder solutions.
- High-Temperature Filaments (e.g., PEEK, PEI): These filaments can serve at elevated temperatures in demanding engineering applications. Direct extruders with all-metal hot ends and heated beds can handle high-temperature filaments effectively. However, extruder cooling and thermal isolation from the hot end offer a considerably lower risk of heat-creep or extruder overheating.
- Composite Filaments (e.g., carbon fiber, metal-filled): These contain additives such as: carbon fiber, metal particles, or wood fibers to improve mechanical properties and/or aesthetics. Direct extruders can process composite filaments with few difficulties.
- Conductive Filaments (e.g., graphene, carbon black, silver): These contain conductive additives that enable the printing of: circuits, sensors, and other electronic components. Direct extruders can accurately deliver conductive filaments in general.
- Color-Changing Filaments: These materials change color in response to temperature or UV light exposure, creating dynamic and visually striking printed objects. Direct extruders can handle such filaments without difficulty.
- Dissolvable Support Filaments (e.g., PVA, HIPS): These serve as secondary materials to support structures for complex prints and overhangs. They dissolve in water or limonene solution after printing and direct extruders can accurately deliver them to the build point.
9. PLA Composite
PLA composites combine PLA (polylactic acid) with a variety of additives that enhance their properties. Direct extruders can effectively handle PLA composite filaments, much the same as basic PLA filaments.
Some common types of PLA composite filaments, all of which work well with direct extruders, are:
- Wood-filled PLA, for a natural wood-like appearance and parts with a textured surface and wood-grain pattern.
- Metal-filled PLA with added bronze, copper, or aluminum powder added, to produce parts with a metallic sheen and weight.
- Carbon fiber PLA, with short carbon-fiber strands that enhance the mechanical properties for functional prototypes, mechanical parts, and engineering/stressed applications.
- Glow-in-the-dark PLA, with phosphorescent additives that absorb and emit light, causes them to glow in the dark for decorative applications.
- Marble-filled PLA, with finely ground marble powder, which gives printed objects a marble-like appearance and texture.
PLA composite filaments can all be extruded, generally with standard PLA printing settings on direct extrusion 3D printers. However, temperature settings may need adjustment and many additives increase the risk of hot-end clogging or material deposition and slipping in the extruder.
While direct extruders can reliably feed a broad spectrum of filament materials, certain materials may not be suitable for all such equipment. Some high-temperature filaments, such as PEEK and PEI, may require specialized direct extruders capable of tolerating extremely high temperatures beyond that which typical direct extruders can, and with aggressive thermal isolation of the extruder to reduce heat creep. Filaments containing abrasive additives, such as carbon fiber or metal particles, can wear down the extruder gears over time. Excessively soft or elastic filaments may cause feeding issues or inconsistent extrusion due to their inability to grip the drive gear effectively. This is not particularly a direct extruder issue, but the increased risk of heat creep in direct extruders can worsen this considerably. Filaments with unusual properties or compositions may not be compatible with standard direct extruders, as their specific requirements may demand specialized or unusual extrusion systems or modifications to the printer setup.
What Are the Advantages of a Direct Extruder?
Direct extruders offer a variety of advantages in most 3D printing applications such as:
- Provide greater precision and repeatability in filament feeding, resulting in consistent extrusion, crisper start/stop events, and overall better print quality.
- They can cope with a wider range of filament types, including flexible materials and exotics, without the need for additional modifications. They only require more regular maintenance checks for incipient clogging or wear in the extruder mechanism.
- Are typically more compact than Bowden extruders, making them attractive for desktop 3D printers with limited space.
- They are a simpler solution with less moving/wear exposed components and potential failure points. This reduces the burden of setup, maintenance, and troubleshooting.
- Facilitate faster retraction settings, reducing the risks of stringing and improving print speed/responsiveness.
What Are the Disadvantages of a Direct Extruder?
Despite their advantages, direct extruders also have some limitations that must be taken into account, including:
- Increased moving mass, as the direct mounting of the extruder mechanism adds weight to the moving printhead. This reduces the ability to accelerate and decelerate, marginally increasing print times.
- The proximity of the motor to the hot end can lead to a greatly increased risk of and consequences in heat creep, in which the filament softens prematurely and potentially clogs the nozzle. This can be very disruptive to prints.
What 3D Printing Applications Benefit From Direct Extruders?
Direct extruders are well-suited for virtually all 3D printing applications, given their generally better performance in precision and repeatability of filament extrusion control.
Is the Direct Extruder a part of the 3D Printer?
Yes, a direct extruder is a key component in any FDM®/FFF machine. The direct extruder is the most critical aspect of a 3D printer, as it has the largest influence on:
- Model strength, by controlling the feed of material to ensure good adhesion.
- Model cosmetics, by controlling the regularity and start-stop of the flow of build material to make consistent build resolution/layer thickness and facilitate the crisp start and stop points in the application of material to the model.
- Filament selection, as direct extruders present fewer limitations as to filament type and additives than do the less-direct Bowden-type extruders.
What Is the Difference Between Direct Drive vs. Bowden?
A direct extruder is placed directly above the hot end and feeds material into it with no intermediate components other than some degree of thermal isolation to reduce the heat-creep effect that can disrupt the filament within the extruder mechanism by softening it.
A Bowden extruder places a tube between the extruder and the hot end, as a guide for the delivery of filament under compression, pushed out by the extruder. The tube can be short, described as a direct drive Bowden extruder with the extruder placed a short distance above the hot end but physically separated from it. It can be much longer, placing the extruder on the chassis of the machine and connecting to the hot end via a long Bowden tube.
Summary
This article presented direct extruders, explained them, and discussed their various applications and how they work. To learn more about direct extruders, contact a Xometry representative.
Xometry provides a wide range of manufacturing capabilities, including 3D printing and other value-added services for all of your prototyping and production needs. Visit our website to learn more or to request a free, no-obligation quote.
Copyright and Trademark Notices
- FDM® is a registered trademark of Stratasys Inc.
Disclaimer
The content appearing on this webpage is for informational purposes only. Xometry makes no representation or warranty of any kind, be it expressed or implied, as to the accuracy, completeness, or validity of the information. Any performance parameters, geometric tolerances, specific design features, quality and types of materials, or processes should not be inferred to represent what will be delivered by third-party suppliers or manufacturers through Xometry’s network. Buyers seeking quotes for parts are responsible for defining the specific requirements for those parts. Please refer to our terms and conditions for more information.
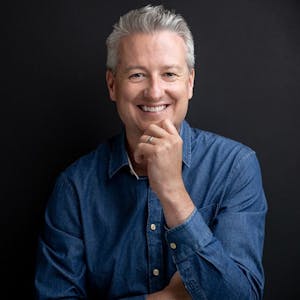