Industrial metal 3D printing has continued to penetrate the market at break-neck rates, thanks to evolutions in technology and outside factors like supply chain disruptions. We’ve covered the evolving ways metal 3D printing is being incorporated into industrial production before. However, due to the fast-moving nature of additive manufacturing development, we’re bringing you an update on how this technology is being increasingly adopted and how you can access it.
What is Metal 3D Printing?
First, the basics: there are multiple metal additive manufacturing methods, including the more widespread DMLS (direct metal laser sintering) as well as the more recently popular method of metal binder jetting. In DMLS, metal powder is directly melted (or sintered) by a laser layer by layer to create parts. However, metal binder jetting layers adhesive in a tray of metal powder, enabling printed pieces to be sifted out of the raw material when finished without having to remove support structures. From here parts can be baked and sintered or infused with a metal (like bronze) to reach their final form. This enables more mass production of metal parts once the initial design optimization is finished.
How Metal Additive Manufacturing is Evolving
Supply chain disruptions from the past couple of years have drastically increased the popularity of an already fast-growing field, especially for medical and aerospace companies. 2018 and 2019 predictions by Deloitte and PwC predicted 3D printing would continue to grow in popularity partly because metal and other non-plastic materials were becoming available for use in 3D printing. PwC specifically predicted the growth of an entire metal additive manufacturing supply chain, including companies that produce the printers and software themselves, printing material suppliers, and service companies. This has come into fruition in niche markets as more technology to complement 3d metal printing is being offered, a sign of the sector’s maturity.
While metal 3D printing was first limited to massive industrial DMLS printers, it has evolved into more complex and smaller machines that allow for a greater range of production. More small metal 3D printers, including metal binder jetting models, are coming onto the market. These take up less space on a factory floor and cost far less, breaking down the barrier for entry for companies that want to start metal additive manufacturing. At the same time, manufacturers of larger industrial printers are creating larger print beds to enable more parts created per print. They’re also continually adding more and more lasers to large DMLS printers, which increase the speed and consistency of a print, making it easier to predict.
Predicting the outcomes of metal additive manufacturing is getting easier too. While originally the user could only see how the part would turn out by printing it, newer printers have better software to predict design outcomes. Concepts like digital twins, which simulate how a 3D printed part will turn out before the print ever starts, will also help prevent errors creeping in as they continue to advance. Someday these twins will also be able to work across multiple programs and machines as a part goes through numerous manufacturing processes.
Metal material itself is becoming more available for additive manufacturing. Metal filament and powder costs have been predicted to drop. Additionally, some printers have come into the market that use polymer encapsulated metal injection molding material, which is less expensive than traditional 3D printing metals. At the same time, companies are already showing a growing interest in high-performance metals like refractory metals such as tungsten. In the future more high-performance metals will be available for industrial applications, including high entropy alloys. However, additive manufacturing plastics continue to evolve and may eventually replace metals for some properties as a cheaper alternative to expensive and rare alloys.
Metal 3D Printing Advantages
Why is metal additive manufacturing gaining so much ground? As you’ll see in the next section, different industries find different aspects of it valuable. In general, however, this newer production method allows for:
- efficient energy and material usage
- on-demand creation of a part at the point of use
- shortened supply chains
- more freedom in design
- less setup than for any other type of manufacturing (this includes increased flexibility and less expense than multiple sets of tooling.)
Metal Additive Manufacturing Applications
Metal 3D printing has become most popular in markets where short timelines are important, as well as where there are a lot of expensive metals used to make small parts. Aerospace and defense companies were some of the first to adopt 3D metal printing, followed closely by the medical and dental industries. These industries first adopted metal 3D printing because it addresses the factors that make standard parts for these sectors cost more than in other sectors.
Aerospace parts are historically expensive for several reasons, including the rare materials used, the necessity for short lead times, and the extra precision required to ensure they perform to specifications. They also need to be as lightweight as possible. Metal additive manufacturing addresses all of these factors in a less expensive way than more traditional manufacturing processes. A 3D printed metal part can weigh as much as 70% less than the identical part produced by other methods. Since a printer uses only the material it needs, the waste of expensive materials like titanium and nickel alloy is kept to a minimum compared to subtractive manufacturing processes. At the same time, already tight lead times for products like jet engine turbines are cut down and additional accuracy is possible with less effort (and therefore cost). Additionally, complex systems in aerospace can be more easily redesigned, simplified, and tested through 3D printing, as printing can reduce the number of components required and quicken the time to create a complex prototype system.
Medical and dental manufacturers also use 3D printing for its ability to create accurate, lightweight parts with short lead times. However, these fields also need to attain a high degree of customization at a lower cost, which is necessary for products like artificial hip joints and dental implants.
Additionally, automotive companies have been using metal additive manufacturing for high-end parts to a limited extent. Like in aerospace and defense, printing in metal offers automotive businesses easier redesign of systems to increase performance. It also allows for metal component weight reduction to improve fuel efficiency, and creation of specialized aftermarket parts. However, most automotive parts are less expensive than aerospace or medical parts, and additive manufacturing has yet to catch up to the speed of other processes, so 3D printing only fits in certain situations for these manufacturers.
In the future, industries like mining and oil and gas may also adopt metal 3D printing, as this process can help with the speed of delivery, an essential factor for these fields. According to one report, 83% of oil and gas firms are thinking about adopting 3D printing or on-demand manufacturing for spare parts.
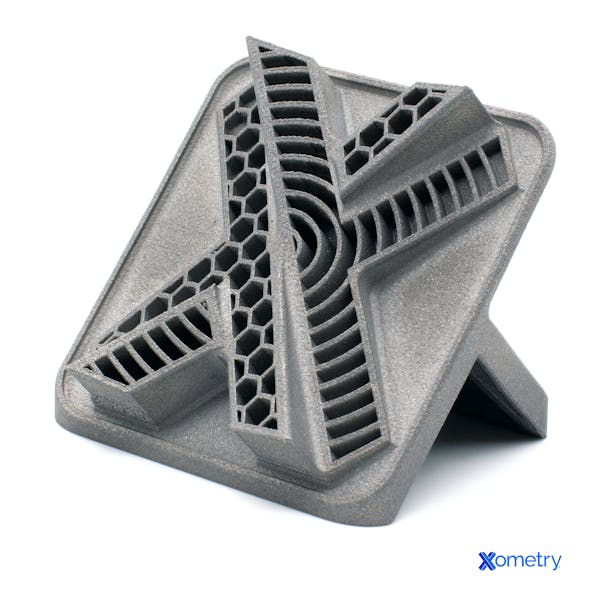
Metal Additive Manufacturing Examples
What does this look like in concrete terms? In aerospace, NASA and SpaceX have used metal additive manufacturing to make spaceship parts. NASA used the technique to create a rocket engine turbopump that contained 45% fewer parts. In SpaceX’s case, 3D printed parts went into its SuperDraco ship’s engine combustion chamber.
There are also metal additive manufacturing examples in the medical field. By 2016 the FDA had approved metal 3D printed implants for medical procedures, and they’ve been used since not only in hip implants, but for a custom artificial rib cage and a skull implant. Xometry has helped build new surgical robot prototypes through its 3D printing and other manufacturing services, creating medically validated parts.
There are some notable examples of other companies adopting this technology; Ford recently installed an autonomous robot to control printers creating end-use parts so it could scale up printing production. Meanwhile, Volkswagen has implemented binder jet printing in its headquarters plant in Germany. Multiple oil and gas suppliers are also experimenting with or implementing metal 3D printing, including PGV, which has been printing parts like tool slips and pistons on-demand enough to reduce lead times by 50-80% and physical inventory by 50%.
Metal Additive Manufacturing Disadvantages
To catch on in more industries, metal 3D printing will still need to overcome some hurdles. Both types of printing are limited in the amount of parts that can be printed simultaneously by the size of the build plate. For DMLS, the post-processing required to remove support structures is time-consuming and adds cost. Binder jetting doesn’t have support structures, allowing faster production in bigger batches. However, neither method has yet reached the speed and output of more traditional manufacturing processes like stamping or forging. Because of this, it’s essential to choose carefully which parts to produce using this method to ensure it provides an economic benefit.
Getting Into Metal 3D Printing
While metal 3D printing offers various benefits, it only makes sense to implement it in certain circumstances. It’s important to investigate whether your company will benefit from using this manufacturing process, and secondly, whether you should outsource the process or bring it in-house.
Any company can start using 3D printed parts, but those that aren’t able to make an upfront investment in the equipment and supporting processes will often use third party additive manufacturers to have parts made. Companies that want to create in-house additive manufacturing facilities will need to account for additional equipment and training for DMLS printers (such as support structure removal and DMLA safety procedures) and binder jet printers (such as baking and sintering or infusing the printed parts).
To determine if 3D printing is worth it, ask yourself:
- Which parts that you currently produce will benefit from being 3D printed?
- What will be the benefit in costs?
- What impact will 3D printing have on your business strategy?
- What impact will this process have on your supply chains?
- What regulatory considerations will you need to account for?
Any company that wants to start using additive manufacturing should first set up a team to talk to people in various departments so you know who the stakeholders are and which parts should be 3D printed first. If you’ve determined your company can go forward with incorporating 3D printing, there are further decisions to be made about whether to use a 3D printing manufacturer or set up this process in your own company.
Companies that invest in up-front costs for 3D printing will find they save money in the long run, and they’ll have more control over the process. Though a good additive manufacturer will provide intellectual property protection and cyber security, this additional control may appeal to companies that want to avoid sharing information. Companies that wish to manufacture in-house should consider whether their production will be centralized from one location or distributed from multiple locations. Many companies that decide to take 3D printing in-house will also start with third-party additive manufacturers to get advice about what’s possible and transfer knowledge to their own employees before setting up their own printers.
Companies that may benefit more from permanent outsourcing will include those without the budget for the upfront cost of buying and setting up all the necessary equipment and training. Additionally, companies who want low volume production or that simply want to experiment with short runs of products will also benefit. Finally, if parts must be tested or analyzed, it may be easier to work with an additive manufacturer who can do that for you. Any company that does want to outsource 3D printing should decide whether the 3D printed parts are coming from OEMs, tier 1 suppliers, or others.
How to Design for 3D Printing in Metal
Whether you’re designing new parts to be 3D printed, or creating parts you already produce with a manufacturing process, it’s vital to design parts specifically for the printing process instead of porting over designs from other processes. Otherwise printed parts will at best cost more, and at worst not perform as well as the same parts made using other processes.
We cover more details on designing for 3D printing in our in-depth guides to metal binder jetting design, DMLS design, and general 3D printing design. However, briefly, there are a few points it’s important to remember:
- Wall thickness should be at least .7 mm (.024 inches) on self-supporting features, and at least 1.2mm (.048 inches) on unsupported or load-bearing features. Wall thickness should also remain uniform.
- Keep at least a .5 mm (.020 inch) gap between part features.
- Get rid of confined hollows in the part design, as this is where trapped material or support structures can remain and block material that needs to leave during post-processing.
- Round corners to reduce stress points and increase the part’s performance over its lifetime.
- Be careful with cantilevers, as these are delicate on 3D printed parts, especially large, heavy ones.
Xometry's Metal 3D Printing Service
With developments in metal printing ranging from new printers to materials to software, this field offers exciting opportunities for production and supply chains, no matter the company's size. However, it’s essential to ensure this process is applied to pain points that other manufacturing methods cannot address. If you see metal additive manufacturing as a solution for your company, we can help. Check out our capabilities page on metal 3D printing to see how we can help you, or skip straight to our instant quote page to get AI-enhanced suggestions about the best way to create your products. Once you submit your file and requirements, you’ll get a quote and lead time within one minute.
Disclaimer
The content appearing on this webpage is for informational purposes only. Xometry makes no representation or warranty of any kind, be it expressed or implied, as to the accuracy, completeness, or validity of the information. Any performance parameters, geometric tolerances, specific design features, quality and types of materials, or processes should not be inferred to represent what will be delivered by third-party suppliers or manufacturers through Xometry’s network. Buyers seeking quotes for parts are responsible for defining the specific requirements for those parts. Please refer to our terms and conditions for more information.
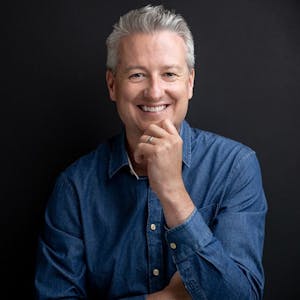