Low-pressure (LP) casting is the most common casting technology for aluminum alloys. This casting method exhibits impressive capabilities. It is particularly helpful in improving material strength and overall performance in, for example, aluminum alloy castings, compared to other casting methods, such as sand casting.
This article will discuss low-pressure casting as a metal manufacturing technology, exploring its definition, history, how it works, its pros and cons, and more.
What Is Low-Pressure Casting?
Low-pressure casting (LP casting) is a metal casting process that introduces molten metal into a mold under relatively low pressure (</=0.8 bar). This technique is particularly beneficial for creating high-quality castings with improved mechanical properties compared to other techniques, such as sand casting. Unlike gravity die casting, low-pressure die casting is performed with the mold positioned at or above the level of the molten metal.
Low-pressure casting produces stronger parts than conventional sand casting. This is because the slow, turbulence-free entry of liquid metal into the mold reduces porosity due to trapped gasses and solidification shrinkage. In addition to the benefits of pressurized mold filling, low-pressure casting dies contain integral cooling passages that aid in controlled cooling, further enhancing mechanical properties.
What Is the History of Low-Pressure Casting?
The origins of low-pressure casting trace back to the early 20th century. In the early 1900s, S.P. Wetherill and J.P. Wetherill Jr. in the U.S. pioneered the field by patenting low-pressure metal mold casting equipment for zinc-aluminum alloy parts in 1906. Concurrently, A.L.J. Queneau in West Germany explored the application of a resistance crucible furnace for casting aluminum bronze and manganese bronze in 1910. Meanwhile E.F. Lake in Britain patented equipment for lead and tin alloys around the same time.
In 1917, France introduced a groundbreaking low-pressure casting machine utilizing pressure generated through water evaporation. Despite these advancements, the technique experienced limited industrial utilization in subsequent decades. However, low-pressure casting emerged as a solution to address the wall thickness effect in heavy-section aluminum alloy castings post-World War II.
E.C. Lewis from British Alumasc furthered the research in the post-war era, achieving significant milestones like producing a light alloy beer barrel in 1950. Beyond the 1960s, low-pressure casting continued to evolve and expand its influence worldwide. Early adopters like Britain, the United States, Japan, and West Germany propelled the technique's popularity, particularly in producing aluminum alloy wheel hubs. Technological progress in machinery and processes further improved its capabilities.
What Is the Importance of Low-Pressure Casting in Manufacturing?
The significance of low-pressure casting in manufacturing is based on its ability to produce high-quality and intricate metal parts, particularly in aluminum alloys. The precisely controlled filling of the mold cavity reduces turbulence due to the smoother flow of the metal. This reduces gas entrapment and therefore makes the casted products less porous ensuring superior part quality. This controlled process also allows for the production of complex geometries, including relatively thin walls (about 3 mm) and intricate details. With reduced machining requirements, improved metallurgical properties, and compatibility with automation, low-pressure casting emerges as a versatile and valuable manufacturing technique.
How Does Low-Pressure Casting Work?
Low-pressure casting works by methodically introducing molten metal into a mold under controlled, low-pressure conditions.
The process begins with machining a mold from materials like steel or sand to replicate the intended part's shape and attributes. Permanent molds are more frequently employed than sand molds due to their greater productivity potential. This mold is carefully sealed to prevent any undesired air ingress. Before molten metal enters the mold, certain pre-casting processes may be performed. The mold might be preheated to prevent thermal shock, and fluxes could be employed to clean its surface and prevent oxidation. To eliminate trapped gasses, degassing procedures may also be carried out before casting. Once these preliminary steps are complete, the metal is elevated to a temperature surpassing its melting point within a furnace. Subsequently, the molten metal is conveyed to a holding furnace (crucible) responsible for sustaining the temperature and eliminating any impurities present in the metal. The furnace is then pressurized. The molten metal enters the mold cavity steadily. This controlled process is characterized by a lack of turbulence due to the low applied pressure. Before solidification begins, air within the mold is allowed to escape through strategically placed vents.
During the cooling phase, the molten metal gradually solidifies, conforming precisely to the shape of the mold cavity. Throughout this process, the applied pressure is maintained to fill any potential shrinkage pockets and guarantee that all intricate details of the mold are fully replicated by the solidifying metal. Once the metal has sufficiently cooled and solidified, the mold is opened, and the resulting casting is carefully removed. Depending on the complexity of the part, further processes such as trimming, machining, and finishing may be conducted to achieve the desired final product.
What Makes Low-Pressure Casting Stand Out Among Other Types of Casting?
Low-pressure casting excels at producing high-quality castings with low levels of porosity due to gas entrapment. This can be attributed to the low-turbulence, controlled mold-filling process combined with sustained pressure to fill voids from shrinkage during cooling. Furthermore, this casting method yields parts with smoother surface finishes than traditional sand casting techniques. The forte of low-pressure casting lies in its ability to reproduce intricate shapes with fine details and wall thicknesses as low as 3 mm. This casting technique is also gentle on molds and dies, extending their lifespan and minimizing maintenance costs. To learn more, see our guide on Types of Casting Methods.
What Is the Process of Low-Pressure Casting?
A detailed breakdown of each step involved in the low-pressure casting production cycle is discussed below:
1. Melt Metal Alloy in Furnace and Bring to Casting Temperature
The production cycle to make a low-pressure die casting part begins by melting the desired metal alloy in a furnace. Heating continues until it reaches the appropriate temperature for casting. Determining this casting temperature is a critical step and involves considering various factors to ensure the quality and integrity of the final part.
One key factor that influences the casting temperature is the melting point of the specific alloy composition being used. Different alloys have distinct melting points, and reaching this temperature ensures that the alloy is fully molten and ready for casting.
2. Transfer Molten Metal to Holding Furnace Below Mold
Once the liquid metal is brought to the right temperature, it's transferred to a holding furnace positioned beneath the mold. This holding furnace helps maintain the molten metal at the required temperature and ensures a continuous supply of material for the casting process.
3. Force Molten Metal Through Riser Tube into Mold by Applying Low Pressure
The molten metal is then forced through a refractory tube, or sprue, using low pressure. The pressure applied is usually significantly lower than in other casting methods, typically below 0.8 bars. The controlled low pressure in low-pressure casting and the slowness of the process facilitate a smooth and controlled flow upward through the riser and into the mold cavity via the mold's base. This pressure is typically sustained throughout the solidification stage to guarantee a thorough filling of the mold.
4. Let Metal Solidify Under Constant Pressure in Die Cavity
The molten metal begins to cool as it enters the mold but it only starts to solidify when it gets down to the liquidus temperature. The solidification process takes place under constant pressure, which ensures complete filling of the mold as the metal cools and contracts, or shrinks. This controlled solidification reduces the formation of defects and ensures a uniform structure within the cast component.
5. Release Pressure and Recycle Remaining Molten Metal
After the metal has solidified within the mold cavity, the pressure is released. Any remaining molten metal is then typically collected and recycled for future use, minimizing material waste.
6. Cool Mold for Easy Casting Removal
The mold, now containing the solidified cast component, is allowed to cool down. Cooling helps in the solidification process completion and enhances the overall integrity of the cast part. Once sufficiently cooled, the mold is opened, and the finished casting is removed.
What Are the Metals Used in Low-Pressure Casting?
The low-pressure casting process can be used to cast a variety of metals. Among the metals commonly cast using low-pressure casting are:
1. Magnesium
Magnesium alloys are often used in applications where light weight and high strength-to-weight ratios are crucial. These alloys find applications in industries such as: aerospace, automotive, and electronics. In the automotive industry, magnesium components are used to reduce the overall weight of vehicles, enhancing fuel efficiency and reducing emissions. For example, gearbox casings and steering components made from magnesium alloys contribute to lighter and more efficient automobiles.
2. Aluminum
Aluminum and its alloys are widely processed using the low-pressure casting method. In fact, they dominate all other metal choices in low-pressure casting. Aluminum's versatility, lightweight nature, and excellent corrosion resistance make it a popular choice for various industries, including: automotive, aerospace, and consumer goods. In consumer goods, such as laptops and smartphones, aluminum casings provide a balance between durability and aesthetic appeal
3. Copper
Copper is less common than other metals on the list because of its higher melting point which demands more energy and time to melt. Copper's high thermal conductivity, while advantageous in applications, can lead to mold cracking and thermal stress during rapid cooling, necessitating specialized mold designs. Oxidation susceptibility at elevated temperatures requires protective measures to maintain cast part quality. Additionally, copper alloys exhibit lower fluidity, potentially affecting mold filling in intricate designs.
Overall, copper alloys are valued for their electrical and thermal conductivity, making them suitable for applications in electronics and telecommunications. The electronics industry use it for heat sinks, connectors, and various electrical components that require efficient heat dissipation.
4. Zinc
Zinc alloys are often selected for die casting applications because their properties make them easy to work with: excellent fluidity, low melting point, and dimensional stability. These alloys are used in applications having intricate shapes, for decorative pieces, and for hardware. A notable application is in the production of door handles and hardware, where zinc alloys can be intricately cast into detailed designs while maintaining durability and corrosion resistance.
Can Steel Be Used as a Casting Metal for Low-Pressure Casting?
No. Steel is less frequently associated with low-pressure casting due to its notably high melting point and the distinctive challenges this characteristic presents within the low-pressure casting process. This divergence arises from the significant temperature disparities between steel and metals like aluminum, magnesium, and zinc, which are more commonly used in low-pressure casting. The elevated melting point of steel necessitates specialized equipment and techniques, including high-temperature molds and advanced temperature management systems, to address the complexities of the low-pressure casting process.
What Are the Applications of Low-Pressure Casting?
Low-pressure casting is mainly used for the manufacture of complex, high-quality components. These include: aluminum alloy engine blocks and suspension components for cars, cylinder heads, aluminum wheels, heat sinks for electronic components, pump housings, impellers, and even golf club heads. LP casting is suitable wherever complex geometry and intricate designs need to be produced.
What Industries Use Low-Pressure Casting Products?
Low-pressure (LP) casting stands as a favored manufacturing technique across various industries, notably automotive and aerospace. The adoption of this method is driven by its economic viability and the assurance of producing high-quality products. The automotive industry uses LP casting for components such as wheels and cylinder heads. Along with the aerospace industry, this is where LP casting is most widely used. Tennis rackets and bicycle frames can be made using LP casting. Certain components for washing machines, vacuum cleaners, and cooking equipment are also made using LP casting. Various components found in industrial machinery are made using LP casting, including: impellers, pump housings, and gearbox casings.
What Is the Quality of Low-Pressure Casting Products?
Low-pressure casting is known for its ability to yield superior castings with enhanced strength and dimensional accuracy (+/-0.005 inch for the first inch and then +/-0.003 for each additional inch). This is due to the precise control of the mold filling, which results in reduced porosity and oxide formation and consequently ensures a low defect rate and homogeneous mechanical properties throughout the cast product.
Are the Low-Pressure Cast Products Durable?
Yes, low-pressure casting products can be durable and exhibit good mechanical properties when the process is properly executed. The controlled nature and reduced turbulence of the low-pressure casting process routinely deliver high-quality castings with reduced levels of defects such as porosity caused by gas entrapment or shrinkage. Note that the durability of low-pressure casting products will also depend on factors such as: the choice of material, proper design and engineering, post-casting heat treatment (if required), and the specific conditions under which the products will be used. As with any manufacturing process, the quality of the casting and the attention to detail throughout the production process will play a significant role in determining the final durability of the product.
What Is the Accuracy of Low-Pressure Casting?
Low-pressure casting produces higher-quality castings in comparison to traditional gravity casting methods. The carefully regulated and uniform flow of metal, combined with reduced turbulence, results in enhanced dimensional accuracy. The standard tolerance for low-pressure casting products is set at +/-0.005 inch for the first inch and then +/-0.003 for each additional inch. A minimum draft of 0.5 degrees is recommended to ensure successful casting.
What Is the Lifespan of Low-Pressure Casting Products?
Die cast molds are expected to last between 80,000 and 100,000 casting cycles. When low-pressure casting is performed with proper techniques and attention to detail, the resulting products can have a long and reliable lifespan. The carefully regulated and uniform flow of metal, combined with reduced turbulence of the casting process often leads to parts with good mechanical properties and reduced porosity, contributing to their durability. However, the lifespan of low-pressure casting products can vary widely based on multiple factors. These include: the type of material used, the quality of the casting process, the design and engineering of the product, the specific application and conditions in which the product is used, and the level of maintenance and care provided throughout its service life.
What Are the Advantages of Low-Pressure Casting?
Low-pressure die casting (LPDC) offers a host of advantages, as listed below:
- Exhibits high accuracy as a result of maintaining low pressure during solidification.
- Minimizes inclusions from oxidation or trapped slag.
- Introduces molten metal to the mold without turbulence. Avoiding churning and splashing the liquid metal helps to avoid oxide formation, which, in turn, leads to a lower level of unwanted inclusions in the final casting.
- Produces castings with minimal porosity by employing low pressure.
- The regulated flow and solidification of metal enhance the mechanical attributes of the castings.
- Controlled mold filling results in fewer casting flaws and consequently, less material discarded as scrap.
- Can accommodate a diverse array of non-ferrous alloys, such as: magnesium, aluminum, and zinc.
What Are the Disadvantages of Low-Pressure Casting?
While the low-pressure die-casting process is renowned for its dimensional accuracy, it does also have some drawbacks:
- Takes longer to fill a given mold shape than other casting processes, such as high-pressure die casting.
- The potential for erosion within the aluminum casting form primarily emerges from the interaction between the molten metal and metal components of the equipment. This phenomenon of erosion typically affects components such as the crucible and riser. While erosion of the aluminum casting itself is not a common issue, localized erosion might occur in areas of high turbulence, such as near the entry point or other critical regions of the mold.
- Requires a minimum wall thickness of around 3 mm.
- Although low-pressure casting typically demands less energy than certain alternative casting methods, such as high-pressure die casting and sand casting, it does exceed the energy consumption of more straightforward techniques such as gravity casting.
- Substantial upfront financial commitment to procure specialized equipment and tooling. The expenses encompass the acquisition of the low-pressure casting machine, mold preparation, and additional ancillary equipment.
- The systems that control casting metal temperature and application of pressure for mold filling require skilled operators with appropriate training.
How Much Does Low-Pressure Casting Cost?
The cost of parts manufactured by low-pressure casting can vary significantly based on several factors, including: the size and complexity of the part being cast, the type of material used, the size of the production run, the quality requirements, and the specific equipment and facilities available.
Generally, low-pressure casting can be more cost-effective than some other casting methods, like high-pressure die casting, due to its reduced need for extensive tooling and its ability to produce high-quality castings with less porosity. While it still necessitates essential components like furnaces, liquid metal transfer systems, molds, and controls for temperature and pressure, LPDC does not need complex and costly die shot equipment and associated maintenance. The cost of low-pressure casting machines typically falls in the range of $30,000 to $50,000. Piece price of the cast products can range anywhere from as low as $1 to several thousand dollars. However, the exact cost would depend on the unique circumstances of each casting project. It's recommended to obtain quotes from casting service providers or manufacturers to get a more accurate estimate based on your specific requirements.
Is Low-Pressure Casting More Expensive Than High-Pressure Die Casting?
It depends. High-pressure die casting represents a significant investment, whereas opting for low-pressure die casting offers a more cost-effective alternative. Additionally, the high-pressure process is confined to smaller parts due to limitations imposed by the locking mechanism's capacity, which can only accommodate weights up to a certain threshold. High-pressure die casting is also cheaper for high-volume productions.
What Are the Alternatives for Low-Pressure Casting?
The main alternatives to low-pressure casting are listed below:
- Gravity Casting: In this approach, molten metal is poured into a mold using only the force of gravity. Gravity casting relies on the natural flow of metal due to gravity, which can result in slower filling times and may require thicker mold sections to counteract turbulence. Conversely, low-pressure casting, as its name suggests, employs controlled pressure to enhance mold filling speed and enable the production of parts with intricate features and thinner walls. What also sets gravity casting apart from low-pressure casting is its ability to accommodate a wider range of materials. While low-pressure casting primarily uses aluminum alloys, gravity casting supports various material choices.
- Investment Casting (Lost Wax Casting): This method involves creating a wax pattern that replicates the final product's shape and is then covered in a ceramic slurry to create a mold with controlled thickness. Investment casting offers greater precision than low-pressure casting, attributed to its use of precisely crafted wax patterns.
- Sand Casting: Traditional sand casting involves making a pattern, forming a mold from a mixture of sand, water, and a binder, usually clay, filling it with molten metal, and ultimately removing the mold. The choice between die casting and sand casting depends on the type of metal being used. Sand casting is notably preferred for its cost-effectiveness, particularly when dealing with materials like steel and cast iron. The process allows for the production of larger and more intricate parts with relatively lower tooling expenses. However, it's important to note that sand casting can yield rougher surface finishes and may necessitate thicker walls compared to die casting. Sand casting is also preferable over low-pressure casting when working with high-temperature metals.
What Is the Difference Between Low-Pressure Casting and High-Pressure Casting?
Low-pressure casting and high-pressure casting are two distinct methods employed in metal casting. The main difference is that low-pressure casting is generally conducted at pressures below 0.8 bar, ranging up to 1 bar in some cases. High-pressure casting, on the other hand, involves significantly elevated pressures, frequently exceeding 1000 bars.
The mechanical strength of the resulting cast parts is another point of difference. Components manufactured using low-pressure casting demonstrate elevated strength characteristics owing to their extended solidification duration accompanied by consistent pressure application. This combination of factors facilitates the formation of a more refined microstructure within the cast material, contributing to increased strength. On the other hand, components produced through high-pressure casting also possess commendable strength attributes; however, they encounter challenges in reaching the equivalent strength levels achieved by their low-pressure counterparts.
Desired part thickness plays a significant role in choosing between the two methods. Low-pressure casting excels in producing thick parts, yet is ill-suited for thin-walled components (less than 3 mm). On the other hand, high-pressure casting is useful for making thin-walled parts (down to 0.40 mm).
Summary
This article presented low-pressure casting, explained it, and discussed its importance and advantages. To learn more about low-pressure casting, contact a Xometry representative.
Xometry provides a wide range of manufacturing capabilities, including casting and other value-added services for all of your prototyping and production needs. Visit our website to learn more or to request a free, no-obligation quote.
Disclaimer
The content appearing on this webpage is for informational purposes only. Xometry makes no representation or warranty of any kind, be it expressed or implied, as to the accuracy, completeness, or validity of the information. Any performance parameters, geometric tolerances, specific design features, quality and types of materials, or processes should not be inferred to represent what will be delivered by third-party suppliers or manufacturers through Xometry’s network. Buyers seeking quotes for parts are responsible for defining the specific requirements for those parts. Please refer to our terms and conditions for more information.
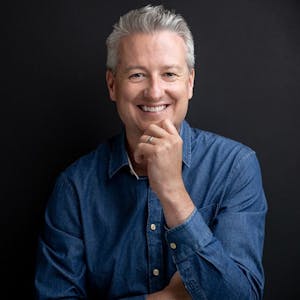