Overmolding is a manufacturing process in which one (polymer) material is molded or cast onto another material that may be composite, metal, or polymer in nature. The result is a single, integrated component of two materials which generally have distinct functions in the paired part. The process typically involves the use of a rigid substrate and often a softer or more flexible secondary process material (though overmolding can encompass more than two materials). This is to combine their differential properties and capabilities in a single part.
This article will discuss the process of overmolding, typical overmolding materials, their definition, importance, and how the process works.
What Do Overmolding Materials Achieve?
The overmolding of materials involves a plastic or metal part being placed in a second-stage molding tool in which additional cavity space is machined. This is filled with a second-stage molding material that can be rigid but is generally elastomeric in nature. The injected material flows around the tool-clamped first stage part and fills the additional cavity space. This will chemically couple to the substrate so that the process results in a single, integrated part. Virtually any polymer can be overmolded onto another part. For example, it is very common to overmold thermoplastic rubbers and thermoplastic elastomers (TPR and TPE) onto a range of engineering and consumer-grade plastics. These materials provide aesthetic, shock absorption, or grip benefits. Another example is the highly IP-rated products in marine and outdoor environments (constructed with ingress protection against water as a priority). These require very precise and high-pressure seal mechanisms that remain in place during the sliding and progressive engagement of casing parts. This is normally achieved by overmolding, as the placement and retention of O-ring-type seals are fraught with assembly challenges. These materials can be the more common TPR and TPE types, but they can also be liquid silicone rubber or even fluoroelastomer materials.
What Is the Other Term for the Process of Overmolding Materials?
There are various other terms for overmolding materials that are used as interchangeable or overlapping descriptors of closely related or derivative techniques. A few terms are: two-shot molding, co-injection molding, insert molding, hybrid molding, and soft overmolding. Two-shot molding refers to a process in which two materials are sequentially injected into a single but adaptive tool, to create a twin material, a single part. Multi-shot molding refers to cases in which more than two materials are used to create a part.
Co-injection molding (or co-molding), also known as sandwich molding or dual-durometer molding, uses two or more materials, injected simultaneously into a mold cavity. Insert molding involves placing required components into the mold cavity before injecting the overmold material to encapsulate them. Hybrid molding refers to the combination of different molding processes or techniques to produce a single part. It can involve a combination of overmolding, insert molding, thermoset, thermoplastic molding, or other methods to achieve specific design or performance requirements. Soft overmolding specifically describes the second-shot molding of a soft or flexible thermoplastic material onto a rigid and pre-existing element.
Some of these terms are interchangeable, but others have significant differences in their specific application or process details. Collectively, they describe variations of molding approaches that involve the combination of multiple materials to create integrated and functional composite parts.
Do Overmolding Materials Differ From Other Injection Molding Materials?
Overmolding and injection molding are essentially identical processes used to create (generally) plastic parts. They differ only in that the overmolding process is a secondary operation.
Any material that can be molded can potentially be overmolded. Where insert parts are placed in and retained in place in a tool before injection, the material that is injected is technically an overmold material. This process is commonly used in a huge array of both rigid and elastomeric thermoplastics and in thermoset silicone, synthetic, and natural rubber moldings. These insert parts can be molded components, machined or cast metal parts, electronics, and even natural materials.
Any molding material that is injected onto, into, or encompassing another part can be thought of as an overmold material. This can therefore include all moldable materials such as: a fluoroelastomer “window” for an infrared sensor to “count” turbine revolutions in a fuel flow sensor, Santoprene® seals on a marine instrument case to exclude salt water from the enclosed electronics when the case is screwed closed, and acrylic light guides for backlighting, overmolded into stainless steel injection-molded numeric keys for an outdoor payment terminal.
What Is the Importance of the Overmolding Materials?
Overmolding materials are important in that they are used to deliver complex and high-quality products across most consumer, industrial, military, and medical product sectors today. For example, overmolding helps by enhancing grip and ergonomics. This is most beneficial for handheld devices. Enhanced sealing and water resistance can also be achieved by bonding a soft and flexible gasket material onto a rigid component. This obviates the need for separate and manually placed gaskets, a stage that is fraught with potential for error that can go undetected in the assembled product.
Vibration damping and noise reduction can be integrated into products by overmolding materials. This technique is commonly employed in automotive parts, power tools, and machinery to improve user comfort and minimize noise pollution. Impact and shock absorption can also be similarly integrated with low labor and reduced part count. This protects sensitive components from damage due to drops, impacts, and shocks. Finally, overmolding allows for the creation of visually appealing products with varied colors, textures, and surface finishes, improving the apparent quality of a product.
What Is the Primary Purpose of the Overmolding Materials Process?
Overmolding has a variety of purposes. Its primary purpose, however, is to allow direct and precise manufacture of multi-material composite components that produce a single part to deliver multiple functions, with an optimal material for each function. This reduces either part count, or the need for functional compromise in material selection.
How Does the Overmolding Process Work?
A generic summary of the overmolding process typically involves these stages:
- A mold is first required, to retain the substrate and provide the forming cavity for the injected overmold material.
- Prepare the rigid substrate by cleaning, adding an adhesion modifier, or etching, to ensure good adhesion with the overmolded material.
- Place the rigid substrate into the desired position within the mold. Then introduce the overmold material into the unfilled parts of the cavity. This is achieved through injection molding, insert molding, transfer molding, casting, or compression molding, as appropriate.
- Allow the mold to cool—for the overmold material to solidify and bond with the substrate. In the case of thermoset materials, the mold is heated to induce cure and then cooled.
- Remove the overmolded part from the mold once it cools and solidifies. Trim the excess material and perform any necessary finishing operations, such as surface texturing or polishing.
What Are the Materials Used in Overmolding?
The materials used in overmolding are listed below:
1. Acrylonitrile Butadiene Styrene (ABS)
ABS is the most widely utilized molding material for consumer products, automotive parts, and many more applications. It has reasonable chemical compatibility with most of the soft, thermoplastic elastomeric materials that are used for grip and seal applications in these products. ABS is generally the substrate material in pairing with a soft material used for the overmolding. It is common to include mechanical engagement features, rather than relying excessively on the chemical coupling. Such features are through holes in the substrate that can serve as gallery connections to runners molded onto the inner surface of the rigid part. Reduced reliance on chemical coupling between substrate and overmold allows for some variation in the process, as the long-term durability of chemical coupling can be unreliable. Wisely applied mechanical coupling is insurance against later and catastrophic failure by peeling.
In the widespread use of ABS for functional and enclosure components, some parts/products can be expected to require service to some degree. Where parts are held together with thread-forming screws directly engaged with the plastic, multiple opening/closing cycles are very likely to result in screw force degradation. In such cases, it is common to use threaded brass or stainless steel inserts, with ridged and knurled outer faces. These are hand (or robot) placed onto pins in the tool and then the plastic encapsulates them as the part is molded. No chemical coupling occurs to metal parts, but the exterior features will suffice to retain the parts and resist normal forces applied to them by screwing (repeatedly).
2. Polypropylene (PP)
Polypropylene is a chemically stable and relatively soft polymer that is widely used for low-cost and disposable parts/applications and outside-environment tasks. It has become increasingly used for higher-grade consumer applications, as techniques for improved surface finish in molding have improved. It is the material of choice for electric toothbrushes, and this has accelerated as techniques to overmold grip/seal/aesthetic features have developed.
In particular, the chemical stability of PP is of benefit in hygiene applications, but the very low surface energy that creates this benefit makes normal overmolding impractical, as no chemical bond is possible with the PP in the as-molded state. Specialist TPEs have been developed to overcome this failure point.
To learn more, see our article on the Examples of PP.
3. Low-Density Polyethylene (LDPE)
LDPE is another example of a relatively soft engineering plastic that has very low surface energy, making it a traditionally unsuitable material for overmolding. The TPEs that are adapted to PP belong to families of modern polymers that are made up of variants that attach to these lower-surface-energy polymers, opening up new applications and opportunities for overmolding.
LDPE is widely used for water and gas pipes and large valve components, as well as food-grade processing equipment, storage vessels, and chemical plant components. Integrated, overmolded seal components would offer significant benefits in simplified assembly; such modifications can potentially offer improved reliability in this range of fluid and gas handling applications but have not yet become commonplace.
It is possible to overmold LDPE onto metal substrates, although only a mechanical connection is possible. This is rarely performed with small parts, as local stress around (for example) threaded inserts would challenge the resilience of this essentially soft material.
4. Thermoplastic Elastomers (TPE)
TPEs are a large family of adaptable and high-performing elastomers. They are particularly well adapted to overmolding applications, though they are also well suited to single material molding of parts. The class contains: Thermoplastic vulcanizates, TPV (TPE-v or TPV), Thermoplastic polyolefin elastomers, TPO (TPE-o), Thermoplastic polyurethanes, TPU (TPU), and Styrene block copolymers, TPS (TPE-s) among others.
Of note, various examples of the family have some long-term stability issues and can degrade under a variety of influences such as modest heating, UV, and oxidizers. In long-term contact with other components, there can also be adhesion issues that can damage over molds.
To learn more, see our article on TPE (Thermoplastic Elastomers).
5. High-Density Polyethylene (HDPE)
HDPE is generally considered unsuited for dual polymer overmolding, either as a substrate or as an overmold. This is because of the adhesion issues that result from its low surface energy. The benefit of using HDPE is its chemical resilience, which makes overmold adhesion difficult.
In extreme cases, it is possible to plasma or flame treat the surface of HDPE to promote adhesion. This practice is not used for overmolding but for affixing other parts. HDPE is a very practical engineering plastic and lends itself well to encapsulating metal parts such as: reinforcers, threaded inserts, etc, coupled by mechanical and structural means, rather than chemical adhesion.
To learn more, see our guide on What is HDPE.
6. Polyoxymethylene (POM)
Although chemically dissimilar to HDPE, POM shares many properties, and it is particularly ill-suited to dual polymer processes. This is because it has among the lowest surface energies of all engineering plastics. POM is, however, useful in overmolding metal parts such as threaded inserts. Its local hardness/toughness makes such couplings very robust.
7. Polyetherimide (PEI)
PEI is one of the higher-performing polymers employed in engineering applications. It has good thermal, mechanical, and chemical properties. PEI is a great option whenever high strength, high-temperature resistance, and wear resistance are required. It can be molded to very tight tolerances, with low thermal warpage, and is suited to high-value markets such as medical devices, and scientific equipment.
PEI is very well suited to insert molding, i.e., overmolding onto metallic substrates. This capability is widely employed for this material. There is no evidence of the use of PEI as a substrate for polymer overmolding, or in co-molding and dual injection applications, however.
Can EPDM Be Overmolded?
Yes, ethylene propylene diene monomer (EPDM) can be overmolded. EPDM is a versatile and widely utilized rubber with many useful properties. It offers great weather/UV resistance, high-temperature stability, and good electrical insulation properties.
EPDM can be overmolded onto almost any rigid substrate to combine its properties with those of the substrate, delivering enhanced functionality that the rubber alone does not offer. It is compatible with substrates made of most plastics, metals, and other rubber materials (for dual hardness purposes). Ensuring good adhesion between the EPDM and the substrate is achieved by material selection, mechanical coupling, and substrate surface preparation.
Can Silicone Be Overmolded?
Yes, liquid silicone rubbers (LSRs) can be overmolded. Much like EPDM, silicone rubber is known for its huge flexibility/elasticity, temperature resilience, and durability. Overmolding silicone rubber onto a substrate delivers enhanced functionality in a component or product. LSRs are compatible with a variety of substrates, including: plastics, metals, and other rubber materials. Material selection, smart adhesion design, and surface preparation can usually deliver good adhesion.
The overmolding of thermoset silicone rubbers is less common but possible. The widest use for this is in decorative applications such as text/character/artwork on silicone phone cases. This is achieved by the multi-stage casting of heat-cured rubbers, with intermediate and final compression molding stages to integrate and fully cure the resultant composite. Some thermoset (or acetic cure) silicones are used for encapsulation purposes in electrical and electronic equipment, but the cure condition compatibility with the substrate must be carefully considered.
To learn more, see our article on the Uses of Silicone.
How Long Does the Process of Overmolding Materials Take?
Molding processes are fast, with cycle times as short as 2–5 seconds of actual injection being common for small parts. Few parts require total injection process times, from tool closure to part ejection, of greater than 1–2 minutes. Setup in terms of potential cleaning and surface treatment of substrates can be more time-consuming, particularly if a chemical, additive, etc. stage is required.
Loading substrates into the tool before overmolding is a manual or robotic task and usually represents only a few seconds of process. This period can arise for large and complex moldings or assemblies in which many small substrates (such as threaded inserts) must be loaded into the tool.
How Strong Are Overmolding Materials?
The strength of overmolding materials varies. For example, where the overmolding material is a TPE, TPU, or TPR the materials are generally soft and relatively easy to tear. Where the overmold is an LSR or an EPDM (or other synthetic rubber), the polymers have higher elasticity and toughness and can be considered quite strong. Where the overmold is a rigid or engineering polymer, strengths approaching that of light metals are available, though polymer toughnesses are wide-ranging.
What Is the Minimum Thickness for Overmold Materials?
The minimum overmolded feature thickness is limited only by the quality of the tooling and the survivability of the eventual feature, once operational on the substrate. Few overmold features are thinner than 1 mm and a common minimum is 1.5 mm to achieve a reasonably substantial outcome. Much depends on the quality of the chemical coupling. If mechanical coupling is required for the majority of the adhesion, thicker features offer greater stability in the inter-coupling gaps.
What Is the Life Span of Overmolding Materials?
The durability and life expectancy of overmolded features depend on a range of factors such as material degradation and mechanical abrasion. If the material is exposed to conditions that are not compatible with its chemical stability, such as oxidizers, UV, and excess heat, then its life span will be unpredictably limited. Whenever soft materials suffer abrasion, they will spall, peel, and tear rendering operational life shorter. If mechanical coupling is relied upon, these outcomes will be worse.
What Are Examples of Overmold Materials Applications?
Overmolding is widely used, across many product sectors. Some overmold material applications are:
- EPDM valve seats in chemical plants and oilfield valves.
- TPE/TPR grip patterns on power-tool handles.
- Rigid and rubber handles on metal hand tools molded in TPE/TPR.
- Brass and stainless steel threaded inserts molded into Pelican hard cases, for equipment transport.
- Laparoscopic suture device, with PEI functional tip, overmolded onto guide cable.
What Are the Advantages of Overmolding Materials?
Overmolding offers various significant advantages in the manufacturing of plastic and plastic composite parts. These include:
- Facilitates the combination of multiple materials with divergent properties in a single part such as: improved grip, cushioning, sealing, and vibration damping.
- Enables flexibility in creating complex and intricate part designs and in simplified assemblies with multifunctional parts.
- Can lead to cost savings by reducing part count/assembly processes. In particular, the small and precise features required for vibration damping and sealing can pose assembly challenges that are better moved into the precise repeatability of a tooled/molded solution.
- Can enhance the durability and longevity of plastic parts by the ability to absorb shocks, and reduce impact forces.
- Can improve the overall quality of the final product, with stronger and more reliable small parts. It also reduces the risk of part failure, reducing the number of fixings and improving the dimensional accuracy of the placement of parts in an assembly.
What Are the Disadvantages of Overmolding Materials?
While overmolding offers many design, function, and aesthetic benefits, there are also some potential disadvantages to consider. These are:
- Requires expensive and highly specialized molds and tooling designs to accommodate multiple materials and complex part geometries.
- Requires experienced consideration of chemical compatibility between the base substrate and the overmold material, which can be challenging. Delamination or weak adhesion between layers is a common quality issue, as processes ramp up and setup/inspection requirements relax.
- Will often limit the choice of materials, in comparison with single material processes. Chemical compatibility, close (but not too close) melting points, proximal shrinkage rates, and other factors may impact the desired material properties or performance characteristics of the final part.
- Introduces additional complexities into the manufacturing process while simplifying assembly and reducing part count. The integration of multiple materials and the need for precise control of molding parameters will increase molding production complexity.
- Introduces additional quality-control challenges, in that ensuring consistent and uniform overmolded parts is harder than molding a single material. This necessitates stricter quality-control measures, including visual inspection, and peel testing.
Summary
This article presented overmolding materials, explained each material, and discussed why they are best for overmolding. To learn more about overmolding materials, contact a Xometry representative.
Xometry provides a wide range of manufacturing capabilities, including injection molding and other value-added services for all of your prototyping and production needs. Visit our website to learn more or to request a free, no-obligation quote.
Copyright and Trademark Notice
- Santoprene® is a registered trademark of the Celanese Corporation (Headquarters Dallas, US)
Disclaimer
The content appearing on this webpage is for informational purposes only. Xometry makes no representation or warranty of any kind, be it expressed or implied, as to the accuracy, completeness, or validity of the information. Any performance parameters, geometric tolerances, specific design features, quality and types of materials, or processes should not be inferred to represent what will be delivered by third-party suppliers or manufacturers through Xometry’s network. Buyers seeking quotes for parts are responsible for defining the specific requirements for those parts. Please refer to our terms and conditions for more information.
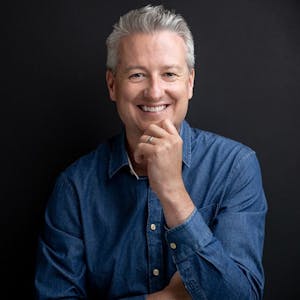